The world around us is built and shaped by an array of materials, each with its unique properties and applications. Among these, 7075 aluminum tubes stand out for their remarkable combination of strength, weight, and versatility. This article delves into the diverse applications of these tubes across various industries, highlighting their impact and the exciting potential they hold for the future.
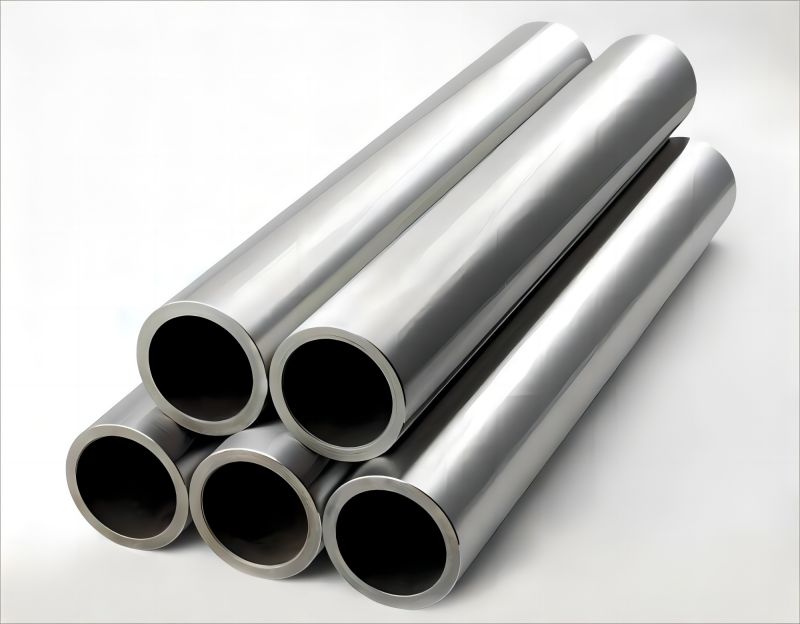
Why 7075 Aluminum Tubes Are Indispensable?
7075 aluminum tubes are not merely hollow metal pipes; they are the unsung heroes of modern engineering. Crafted from an alloy renowned for its exceptional strength-to-weight ratio, these tubes, particularly in the 7075 T6 tempering form, offer a unique combination of properties that make them indispensable across various industries.
The “T6” designation signifies a specific heat treatment process that further enhances the material’s strength, making it ideal for demanding applications. This translates to several key advantages that set 7075 aluminum tubes apart:
- Lightweight: Compared to traditional materials like steel, 7075 aluminum tubes offer significant weight reduction. This translates to improved fuel efficiency in vehicles, enhanced performance in aircraft, and greater maneuverability in sporting goods.
- Exceptional Strength: Despite their lightness, 7075 tubes possess remarkable strength, allowing them to withstand significant loads and stresses. This makes them suitable for applications like aircraft structures, high-pressure gas cylinders, and components in industrial machinery.
- Corrosion Resistance: 7075 aluminum exhibits inherent corrosion resistance, ensuring the longevity of the finished products and minimizing maintenance requirements.
- Weldability: These tubes are readily weldable, facilitating efficient and robust construction of various components.
These combined properties elevate 7075 aluminum tubes beyond just a material choice; they make them a crucial enabler for advancements and optimization across various sectors. From high-performance vehicles and sophisticated machinery to lightweight sporting equipment and durable marine structures, 7075 aluminum tubes play a vital role in shaping our world. Their versatility, strength, and cost-effectiveness solidify their position as an indispensable material for the future.
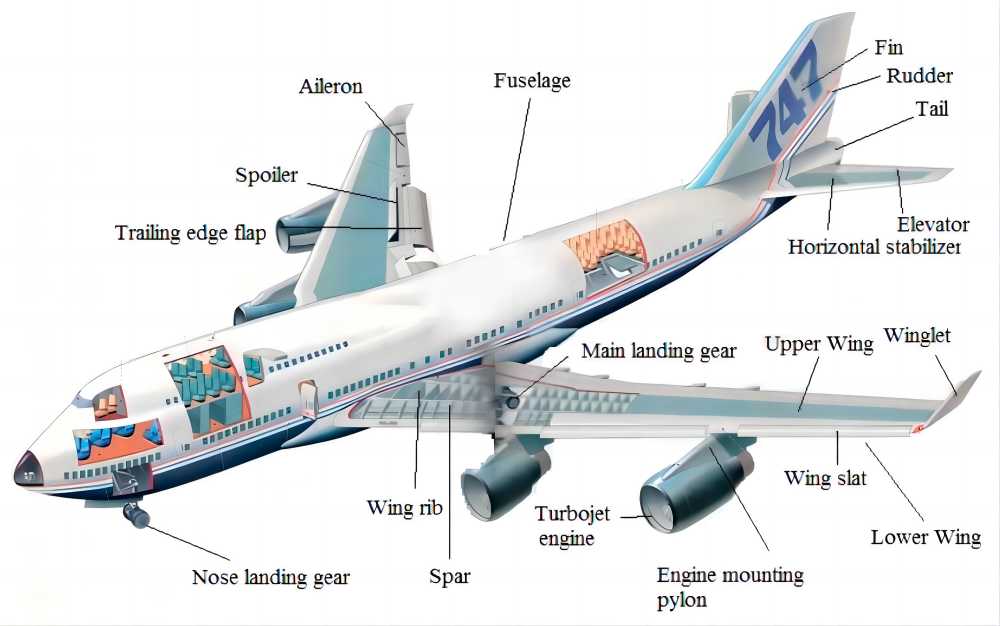
1. Aerospace Applications
The aerospace industry is perhaps the most prominent user of 7075 aluminum tubes. These tubes are extensively used in:
- Aircraft Fuselage and Structural Components: The exceptional strength-to-weight ratio of 7075 tubes makes them ideal for constructing the fuselage, the backbone of an aircraft. These tubes provide the necessary structural integrity while minimizing weight, crucial for maximizing fuel efficiency and flight performance.
- Wing Structures: Wing structures are subjected to immense aerodynamic forces during flight. 7075 t6 aluminum tubes offer the perfect balance of strength and weight, allowing for the construction of lightweight yet robust wings that can withstand demanding flight conditions.
- Landing Gear Components: Landing gear components require high strength to handle the impact of landing and taxiing. 7075 aluminum tubes, due to their exceptional strength and fatigue resistance, are widely used in landing gear struts and other critical components.
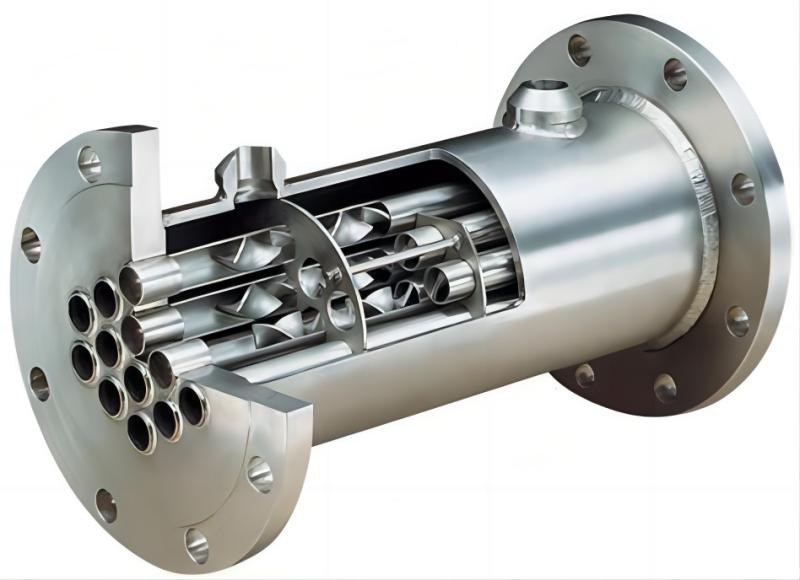
2. Automotive Applications
The automotive industry has also embraced the benefits of 7075 aluminum tubes. These tubes find application in:
- Lightweight Chassis and Frames: Utilizing 7075 aluminum tubes in chassis and frame construction allows car manufacturers to achieve significant weight reduction without compromising on strength. This contributes to improved fuel efficiency and overall performance.
- Heat Exchangers: 7075 aluminum tubes find application in automotive heat exchangers due to their excellent thermal conductivity. This property allows for efficient heat transfer, vital for maintaining optimal engine temperature and performance.
- Engine Components: Due to their strength-to-weight ratio and machinability, 7075 aluminum tubes can be found in various engine components, such as pistons and connecting rods. Their use helps reduce engine weight without sacrificing the required strength and durability.
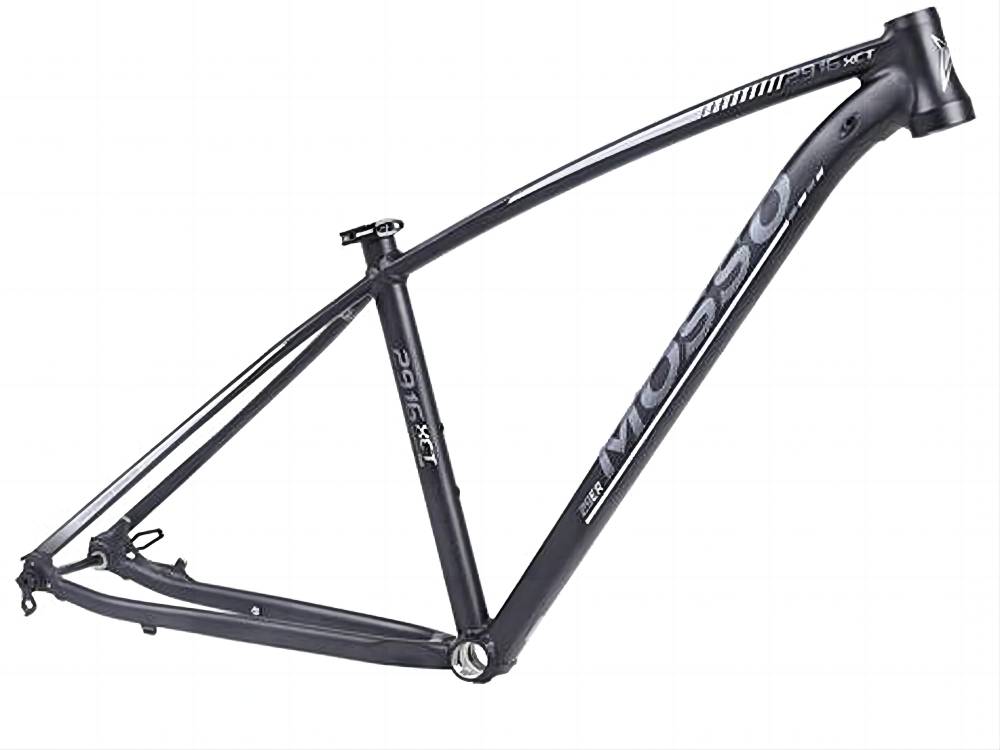
3. Applications in Sporting Goods
The world of sporting goods also utilizes the versatility of 7075 aluminum tubes:
- Bicycle Frames: High-performance bicycles often utilize 7075 aluminum tubes for their frames due to the superior strength-to-weight ratio, allowing for lightweight and responsive bikes without compromising on durability.
- Archery Equipment: The exceptional strength and stiffness of 7075 aluminum tubes make them ideal for constructing arrow shafts and certain bow components, ensuring accuracy and consistency in archery applications.
- Ski Poles: Lightweight and robust, 7075 aluminum tubes are commonly used in high-end ski poles, providing skiers with the necessary support and control while minimizing weight for improved maneuverability.
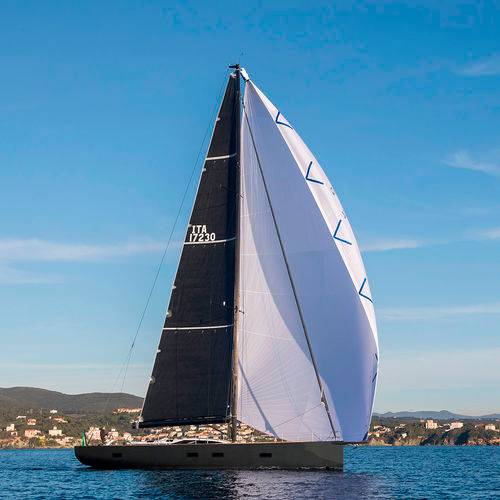
4. Marine Applications
The marine industry also leverages the unique properties of 7075 aluminum tubes in various applications:
- Boat Masts and Rigging: The masts and rigging of sailboats require exceptional strength and resistance to corrosion. 7075 aluminum tubes, boasting both attributes, are widely utilized in these components, ensuring safe and efficient sail operation.
- Hull Construction: In some boat designs, particularly high-performance vessels, 7075 aluminum tubes may be used in specific sections of the hull. Their lightweight nature contributes to improved speed and maneuverability.
- Marine Engine Parts: Similar to the automotive industry, certain marine engine components benefit from the use of 7075 aluminum tubes. Their strength and machinability allow for the creation of lightweight yet robust components, contributing to improved engine performance and efficiency.

5. High-Performance Equipment
Beyond the industries mentioned above, 7075 aluminum tubes find application in various high-performance scenarios:
- Firearms Components: Specific components of firearms, such as receivers, barrels, and handguards, can be manufactured using 7075 T6 aluminum tubes. This temper designation offers even greater strength and durability compared to the standard 7075 alloys, making it suitable for these demanding applications. However, it is crucial to note that the use of 7075 aluminum tubes in firearms is subject to various regulations and legal restrictions depending on the firearm type and local laws.
- High-Pressure Gas Cylinders: Due to their exceptional strength and resistance to corrosion, 7075 T6 aluminum tubes are utilized in the construction of high-pressure gas cylinders used for various industrial and recreational purposes. These cylinders can safely store and transport compressed gases like oxygen, nitrogen, and helium.
- Industrial Machinery: 7075 aluminum tubes contribute to the construction of various components in high-performance industrial machinery. Their strength-to-weight ratio allows for lightweight yet robust machine parts, improving overall efficiency and performance.
In conclusion, the mighty 7075 aluminum tube stands as a testament to the power of material science and its impact on various sectors. As technology continues to evolve, these versatile tubes are poised to play an even more significant role in shaping the future, pushing the boundaries of design and performance across various industries.