Aluminum alloys play a crucial role in the aerospace industry, known for their high strength-to-weight ratios, durability, and adaptability. Among the most prominent choices for structural components in aircraft are 7050 aluminum and 7075 aluminum alloys. Both alloys are widely used in the industry for producing essential stamped aluminum parts due to their unique properties and performance advantages. However, 7050 and 7075 differ significantly in chemical composition, mechanical properties, heat treatment requirements, and application-specific suitability. This article will explore both their similarities and differences to provide a comprehensive understanding of their ideal applications in aircraft structures.
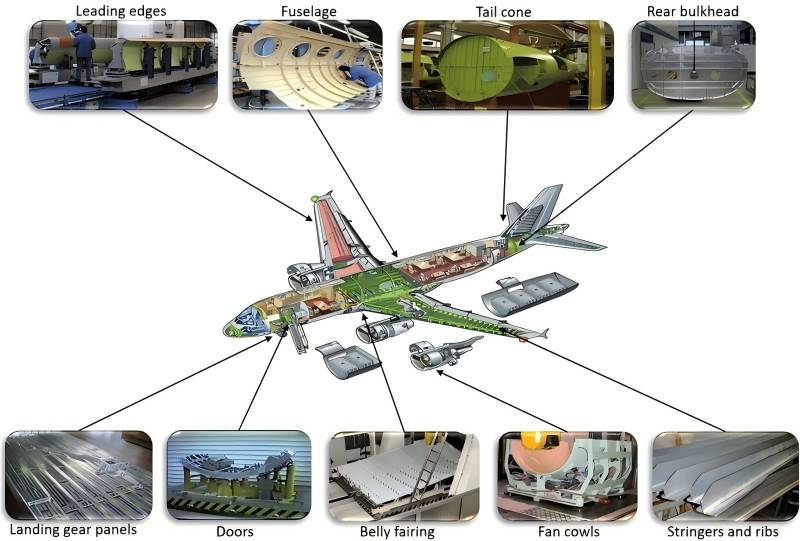
Similarities Between 7050 and 7075 Aluminum Alloys in Aircraft Applications
While 7050 and 7075 aluminum alloys may differ in certain aspects, they share fundamental similarities that make them invaluable to the aerospace industry:
- High Strength and Mechanical Properties: Both alloys are renowned for their exceptional strength and mechanical properties. They can withstand high stresses and complex loading conditions, ensuring the structural integrity of aircraft components.
- Wide Application in Aircraft Structures: Both alloys find extensive use in critical aircraft components, including wings, fuselage, and landing gear. Their combination of strength and lightweight properties contributes to improved aircraft performance and fuel efficiency.
- Excellent Fatigue Resistance: Fatigue resistance is crucial for aircraft components that are subjected to cyclic loading during flight. Both 7050 and 7075 alloys exhibit excellent fatigue performance, reducing the risk of failure.
- Heat Treatability: Heat treatment processes can further enhance the mechanical properties of both alloys. By carefully controlling the heating and cooling cycles, manufacturers can optimize the strength, hardness, and ductility of the material.
- Good Machinability: Both alloys are relatively easy to machine, allowing for the production of complex shapes and precise tolerances. This facilitates the manufacturing of intricate aircraft components.
Differences Between 7050 and 7075 Aluminum Alloys in Aircraft Applications
1. Chemical Composition and Alloying Elements
The primary difference between 7050 and 7075 aluminum alloys lies in their chemical composition, particularly the amounts of alloying elements like zinc, magnesium, copper, and zirconium, which significantly affect their performance and application suitability.
- 7050 Aluminum: The primary elements in 7050 aluminum include zinc (Zn), magnesium (Mg), copper (Cu), and zirconium (Zr). The typical range is 2.0-2.6% Cu, 1.9-2.6% Mg, 0.08-0.15% Zr, and 5.7-6.7% Zn. This combination provides 7050 aluminum with a balanced strength-to-weight ratio and excellent resistance to stress-corrosion cracking.
- 7075 Aluminum: For 7075 aluminum, the primary alloying elements are zinc (Zn), magnesium (Mg), and copper (Cu), typically 1.2-2.0% Cu, 2.1-2.9% Mg, and 5.1-6.1% Zn. The higher zinc content in 7075 enhances its strength but results in slightly lower resistance to stress-corrosion cracking compared to 7050.
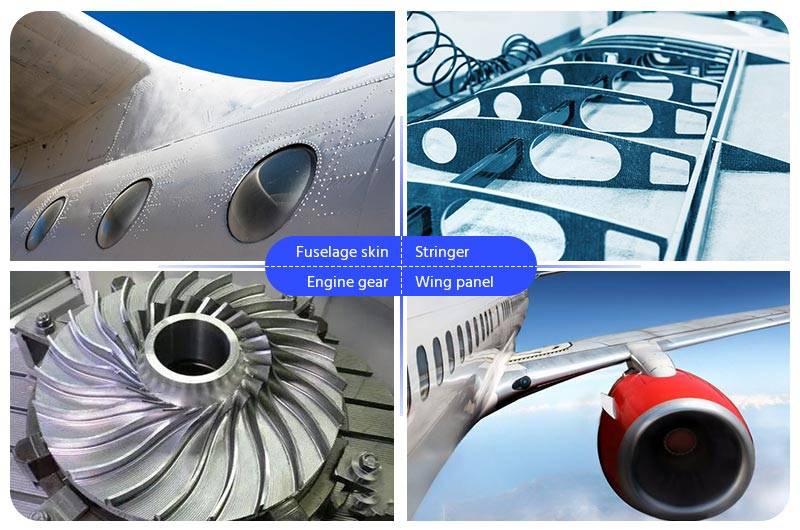
2. Strength and Toughness
Although both alloys are known for their high strength, the way they balance strength and toughness differs, making each suitable for specific applications.
- 7050 Aluminum: Known for its well-rounded strength and toughness, 7050 aluminum is particularly effective in applications that require resistance to stress-corrosion cracking and high fracture toughness. Its properties make it suitable for thicker parts that may be exposed to stress concentrations, such as fuselage frames and bulkheads.
- 7075 Aluminum: While 7075 aluminum achieves extremely high strength, it has relatively lower toughness and stress-corrosion resistance than 7050. This makes it ideal for components where strength is paramount, and thinner sections are preferable. Common applications include thin aircraft skins, wings, and other high-stress regions that benefit from the alloy’s lightweight, high-strength profile.
3. Heat Treatment Performance
The response to heat treatment also varies significantly between the two alloys, especially regarding temperature control and susceptibility to stress-corrosion cracking.
- 7050 Aluminum: The alloy responds well to heat treatment conditions such as T7451 and T7651, maintaining its strength in thicker sections and improving its resistance to stress-corrosion cracking. Its heat treatment process is comparatively less demanding, allowing it to retain consistent properties across various dimensions.
- 7075 Aluminum: With higher zinc content, 7075 aluminum requires more precise control during heat treatment, especially in the T6 and T73 tempers. These conditions enhance its strength but also increase the alloy’s susceptibility to stress-corrosion cracking if not properly managed. As such, 7075 aluminum parts may require additional precautions or alternative processing methods for certain applications.
4. Application Scope
The differences in composition and properties also affect the specific applications where each alloy performs best in aircraft structures.
- 7050 Aluminum: Primarily used in middle-thick plates, extrusions, free forgings, and mold forgings, 7050 aluminum is ideal for structural components requiring high stress and corrosion resistance. These include components such as fuselage frames, bulkheads, and wing skins, where enhanced fracture toughness and stress-corrosion resistance are critical.
- 7075 Aluminum: Known for its extremely high strength and lightweight nature, 7075 aluminum is used in thin sheets and components with complex shapes, such as wing surfaces, landing gear, and engine mounts. These parts benefit from the alloy’s strength but are less susceptible to stress-corrosion cracking due to their smaller cross-sections.
5. Cost and Availability
The cost and availability of each alloy vary due to differences in their production processes and market demand.
- 7050 Aluminum: Due to its complex production requirements and higher resistance to corrosion, 7050 aluminum generally costs more and is less readily available. Its production requires stringent quality control, limiting its use to specific high-stress applications in aerospace.
- 7075 Aluminum: With more mature production processes and broader market demand, 7075 aluminum is relatively affordable and widely available. It is produced on a large scale, making it more accessible for industries that require high-strength aluminum in significant quantities.
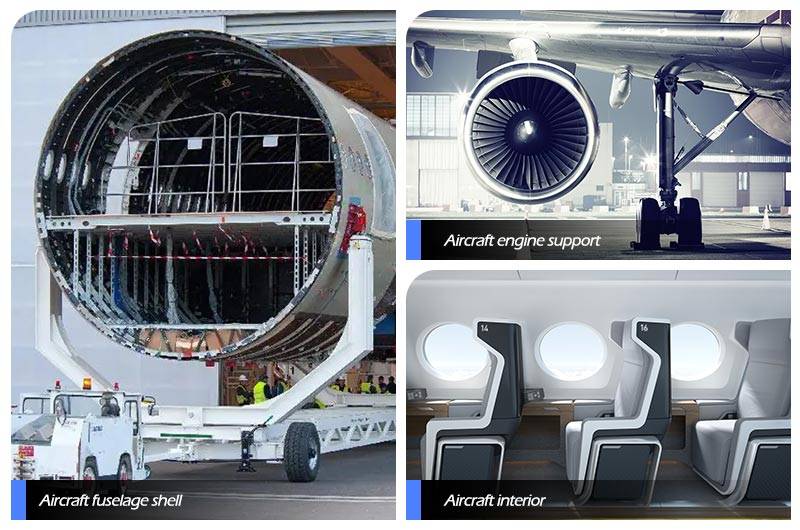
In summary, 7050 and 7075 stamped aluminum parts have many similarities in the application of aircraft structure, such as high strength, good mechanical properties and a wide range of applications. However, they differ significantly in terms of chemical composition, strength and toughness, heat treatability, range of applications, and cost and availability. When choosing which aluminum alloy to use, comprehensive considerations need to be made based on specific application needs and environmental conditions.