Seamless aluminum tubes are primarily produced through two methods: the drawn and extruded process. This article delves into a detailed comparison of these two manufacturing methods, exploring their respective manufacturing processes, dimensional accuracy, surface quality, corrosion resistance, and application fields.
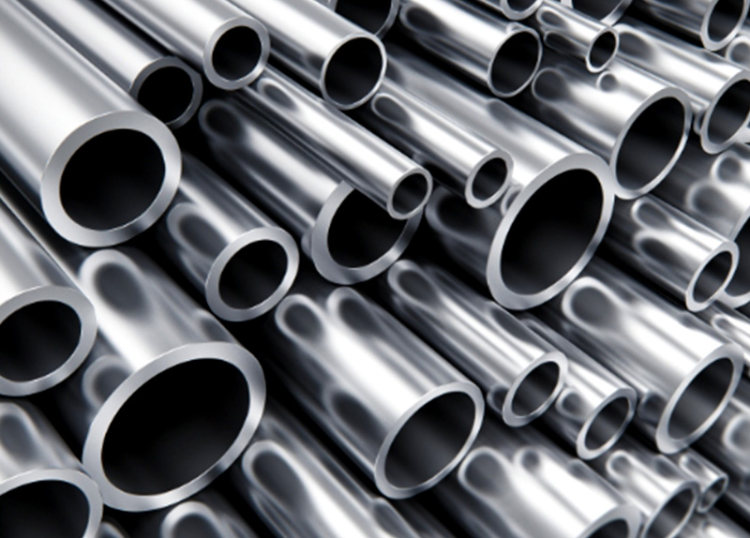
1. Manufacturing Process Comparison
Drawn Seamless Aluminum Tube
The manufacturing process of drawn seamless aluminum tubes involves several critical steps:
Casting: Aluminum ingots are cast to create the initial material.
Heat Treatment: The cast ingots undergo heat treatment to enhance their mechanical properties.
Piercing: The heat-treated ingots are pierced to form a hollow billet, creating the basic structure of the seamless tube.
Cold Drawing:
- The hollow billet is drawn through a series of dies. Each pass through the die gradually reduces the tube’s diameter and wall thickness, refining its dimensions closer to the desired specifications.
- This process requires precision equipment, ensuring the tube’s final dimensional accuracy and surface quality.
Straightening: The tube is straightened to meet the required straightness standards.
Advantages and Limitations:
- Precision: The multiple drawing passes allow for tight control over the tube’s dimensions, resulting in excellent dimensional accuracy and surface finish.
- Limitations: The process introduces significant stress, potentially leading to microcracks in the tube wall, which can affect the tube’s overall quality and durability.
Seamless Extruded Aluminum Tube
The manufacturing process of seamless extruded aluminum tubes is more streamlined and involves the following steps:
Casting and Heating: Similar to the drawn process, aluminum ingots are cast and then heated.
Extrusion:
- The heated ingots are placed into an extrusion press.
- The aluminum is forced through a die, forming the desired tube shape in a single, continuous motion.
This process shapes the tube in one pass, eliminating the need for subsequent cold drawing operations.
Advantages and Limitations:
- Production Efficiency: The seamless extruded process is faster, reducing overall manufacturing time.
- Versatility: The extrusion process allows for the production of tubes with varying cross-sectional profiles, including complex geometries.
- Limitations: The dimensional accuracy and surface quality depend heavily on the design of the extrusion die and process parameters. While advances in technology have improved precision, the overall accuracy and finish are generally lower than those achieved with the drawn process.
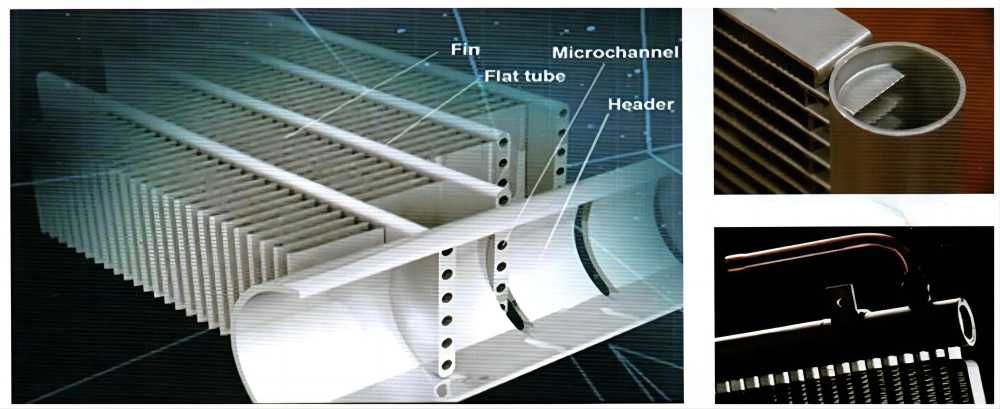
2. Dimensional Accuracy and Surface Quality Comparison
Drawn Seamless Aluminum Tube
The drawn seamless aluminum tube manufacturing process is highly regarded for its precision, delivering exceptional dimensional accuracy and surface quality. Here’s a closer look at why this process excels:
Dimensional Accuracy:
- Multiple Reductions: The cold drawing process involves multiple reductions in both diameter and wall thickness, with each pass through the die incrementally refining the tube’s dimensions. This step-by-step reduction ensures that the final product meets very tight tolerances, which is crucial in applications where precision is paramount.
- Precision Control: The controlled nature of each drawing pass allows for meticulous adjustment of the tube’s dimensions, resulting in a product that is precisely tailored to meet specific requirements. This is particularly advantageous in industries such as aerospace and medical devices, where even slight deviations can be unacceptable.
Surface Quality:
- High-Quality Finish: As the tube is drawn through the dies, friction and tension between the tube and die surfaces naturally smooth out any irregularities on the tube’s exterior. The result is a smooth, polished surface that is aesthetically pleasing and functionally superior, particularly in applications where surface integrity is critical.
- Polishing Effect: The cold drawing process essentially acts as a continuous polishing operation, eliminating surface defects and producing a finish that often requires little to no further treatment.
Seamless Extruded Aluminum Tube
The seamless extruded aluminum tube process, while different, has its own set of strengths and challenges related to dimensional accuracy and surface quality:
Dimensional Accuracy:
- Single-Pass Formation: In the extrusion process, aluminum is forced through a die in a single pass, forming the tube in one continuous operation. This means that the final dimensions are primarily determined by the die’s design and the parameters set during extrusion.
- Less Precision: While modern extrusion technology allows for relatively high precision, the overall dimensional accuracy of extruded tubes typically does not match that of drawn tubes. Minor variations in die design or extrusion conditions can lead to inconsistencies in tube dimensions, which might not be acceptable in applications requiring the highest precision.
Surface Quality:
- Die and Process Dependence: The surface quality of extruded tubes is heavily dependent on the condition of the extrusion die and the specific parameters used during extrusion. Issues such as poor die design or suboptimal extrusion conditions can lead to surface defects, including roughness, pitting, or other irregularities.
- Lower Surface Finish: Compared to drawn tubes, extruded tubes generally have a lower surface finish quality, which might require additional processing if a smoother finish is needed for the application.
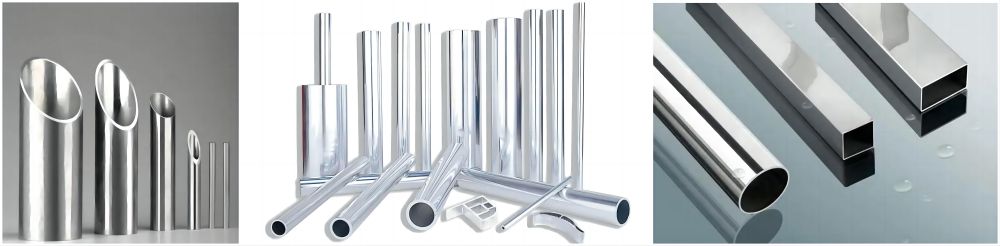
3. Corrosion Resistance Performance Comparison
When comparing the corrosion resistance of drawn seamless aluminum tubes and seamless extruded aluminum tubes under identical chemical composition and heat treatment conditions, the following points emerge:
Drawn Seamless Aluminum Tube:
Microcrack Susceptibility: The stress introduced during the cold drawing process can create microcracks, which may act as pathways for corrosive agents to penetrate the material. Over time, these microcracks can propagate, leading to a reduction in the tube’s corrosion resistance, especially in harsh environments.
Seamless Extruded Aluminum Tube:
Higher Wall Density: The extrusion process generally results in tubes with a higher wall density and fewer internal defects. The absence of microcracks means that extruded tubes may offer better resistance to corrosion in certain aggressive environments, making them more durable over time.
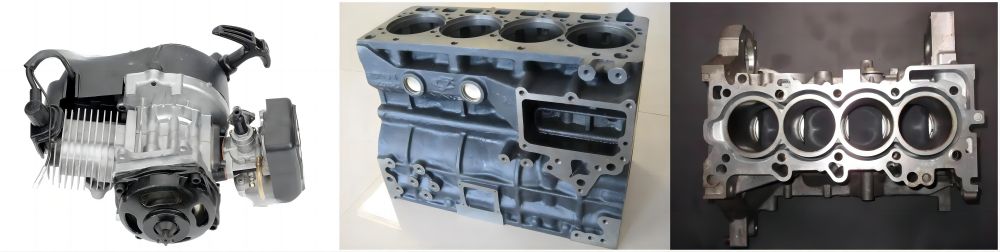
4. Application Field Comparison
Drawn Seamless Aluminum Tube
Due to their high dimensional accuracy and superior surface quality, drawn seamless aluminum tubes are widely used in applications requiring tight tolerances and a pristine surface finish. Key application areas include:
- Aerospace Industry: The high precision and strength-to-weight ratio of drawn seamless tubes make them ideal for critical structural components in aircraft, where performance and reliability are paramount.
- Precision Instruments: In the manufacturing of precision instruments, the dimensional accuracy of drawn tubes ensures consistent performance, which is essential for maintaining the integrity of sensitive equipment.
- Medical Equipment: The smooth, polished surface finish of drawn tubes is crucial in medical applications, where surface integrity can directly impact the functionality and safety of medical devices.
Seamless Extruded Aluminum Tube
On the other hand, seamless extruded aluminum tubes are often favored in applications where production efficiency and the ability to create complex shapes are more important than achieving the highest levels of dimensional accuracy. Notable applications include:
- Automotive Industry: The extrusion process’s versatility allows for the production of tubes with intricate cross-sectional profiles, which are essential in vehicle frames, chassis components, and other structural parts. The ability to produce complex shapes in a single pass significantly reduces manufacturing time and costs.
- Construction Industry: In construction, the durability and strength of extruded tubes make them suitable for structural applications, where the focus is on strength and longevity rather than precision.
- Electronics Industry: The electronics industry benefits from the cost-effectiveness and versatility of extruded aluminum tubes, which are used in various components, including heat sinks and structural supports.
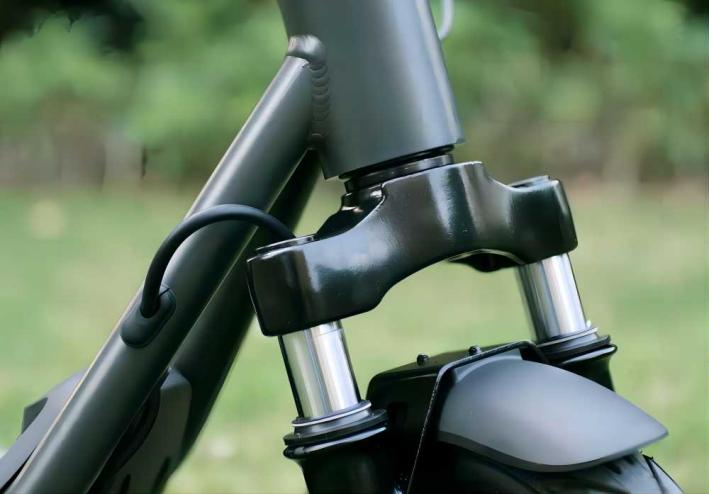
To sum up, the choice between drawn seamless aluminum tubes and seamless extruded aluminum tubes depends largely on the specific requirements of the application. Drawn tubes excel in precision and surface quality, making them ideal for high-performance applications, while extruded tubes offer versatility and efficiency, making them suitable for a broader range of uses.