When aluminum alloys are welded, some cracks often occur at the joints. This will affect the quality of aluminum tubes, aluminum profiles, etc. Therefore, this paper will conduct an in-depth analysis of the causes of serious cracks.
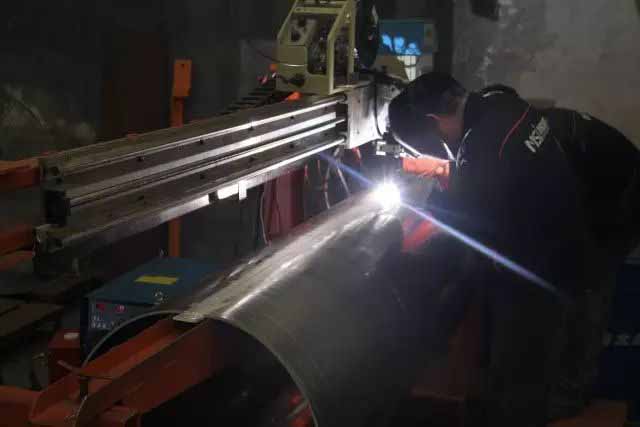
Cracks in Aluminum Alloy Welded Joints and Their Characteristics
In the process of aluminum alloy welding, due to the different types, properties, and welding structures of materials, various cracks can appear in the welded joints, and the shape and distribution characteristics of the cracks are very complex. According to their generated parts, they can be divided into the following two types of cracks form.
(1) Weld metal cracks: longitudinal cracks, transverse cracks, crescent cracks, hairy cracks or arc cracks, root cracks, micro cracks (especially multi-layer welding).
(2) Cracks in the heat-affected zone: weld toe cracks, layered cracks, and microscopic thermal cracks near the fusion line. The temperature range of crack generation is divided into hot cracks and cold cracks. Hot cracks occur at high temperatures during welding, mainly due to the segregation of alloying elements at grain boundaries or the presence of low-melting substances.
Depending on the material of the metal to be welded, the shape, temperature range, and main reasons for the occurrence of hot cracks are also different. Hot cracks can be divided into 3 categories: crystallization cracks, liquefaction cracks, and polygonal cracks. Crystallization cracks are mainly produced in hot cracks. During the crystallization process of the weld, near the solidus line, due to the shrinkage of the solidified metal, the residual liquid metal cannot be filled in time.
Intergranular cracking occurs under the action of solidification shrinkage stress or external force, which mainly occurs in carbon steel, low-alloy steel welds, and some aluminum alloys with more impurities; liquefaction cracks are heated in the heat-affected zone to Produced under the action of shrinkage stress during high-temperature grain boundary solidification.
During the test, it was found that when the surface of the filler material was not sufficiently cleaned, there were still many inclusions and a small number of pores in the weld after welding. In the three sets of tests, since the welding filler material is a cast structure, and the inclusions are high melting point substances, it will still exist in the weld after welding;
In addition, the casting structure is relatively sparse, and there are many holes, which are easy to absorb the components containing crystal water and oil quality, which will become the factors that generate pores during the welding process. When the weld is under tensile stress, these inclusions and pores often become the key sites for inducing microcracks.
Further observation by microscopy revealed that there was a clear tendency for these inclusions and pore-induced microcracks to intersect with each other. However, it is still difficult to judge whether the harmful effect of the inclusions is mainly manifested as a stress concentration source to induce cracks, or is mainly manifested as a brittle phase to induce cracks.
In addition, it is generally believed that pores in aluminum-magnesium alloy welds do not have a significant impact on the tensile strength of the weld metal. the phenomenon of cracks.
Whether the phenomenon of micro-cracks induced by pores is only a secondary phenomenon or one of the main factors causing the sharp decrease in the tensile strength of welds, also needs further research.
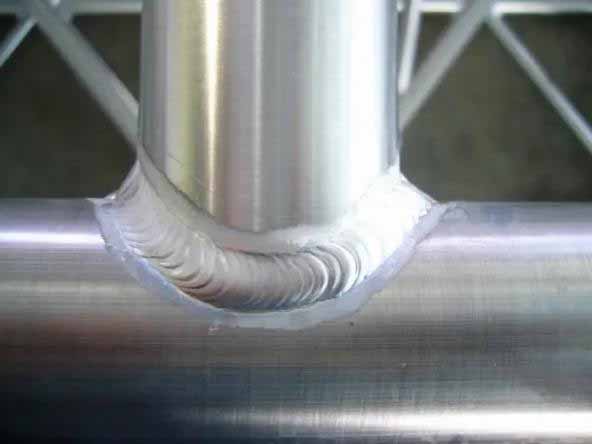
Preventive measures for aluminum alloy welding cracks
According to the mechanism of hot cracks during the welding of aluminum alloys, improvements can be made from two aspects of metallurgical factors and process factors to reduce the probability of hot cracks in aluminum alloy welding.
In terms of metallurgical factors, to prevent intergranular thermal cracks during welding, it is mainly by adjusting the welding seam metal system or adding a modifier to the filler metal. The focus of adjusting the welding suture system, from the perspective of crack resistance, is to control an appropriate amount of fusible eutectic and narrow the crystallization temperature range.
Since aluminum alloys are typical eutectic alloys, the maximum crack tendency corresponds to the “maximum” solidification temperature range of the alloy, and the presence of a small amount of eutectic always increases the solidification crack tendency. The element content exceeds the alloy composition where the crack tendency is greatest so that a “healing” effect can occur.
As modifiers, trace elements such as Ti, Zr, V, and B were added to the filler metal in an attempt to improve the plasticity and toughness by refining the grains and preventing welding hot cracks. , and achieved results. Figure 3 shows the crack resistance test results of Al-4.5%Mg welding wire with modifier added under the condition of rigid lap fillet weld.
The Zr added in the test was 0.15%, and the Ti+B was 0.1%. It can be seen that adding Ti and B at the same time can significantly improve the crack resistance.
The common feature of elements such as Ti, Zr, V, B, and Ta is that they can form a series of peritectic reactions with aluminum to form refractory metal compounds (Al3Ti, Al3Zr, Al7V, AlB2, Al3Ta, etc.). Such small refractory particles can become non-spontaneous solidification nuclei when the liquid metal solidifies, thereby producing the effect of grain refinement.
In terms of process factors, mainly welding specifications, preheating, joint form, and welding sequence, these methods are all based on welding stress to solve welding cracks. The welding process parameters affect the unbalance of the solidification process and the microstructure state of the solidification process, and also affect the strain growth rate during the solidification process, thus affecting the generation of cracks.
The welding method with concentrated heat energy is conducive to the rapid welding process, which can prevent the formation of coarse columnar crystals with a strong directionality, thereby improving crack resistance. Using a small welding current and slowing down the welding speed can reduce the overheating of the molten pool and improve the crack resistance.
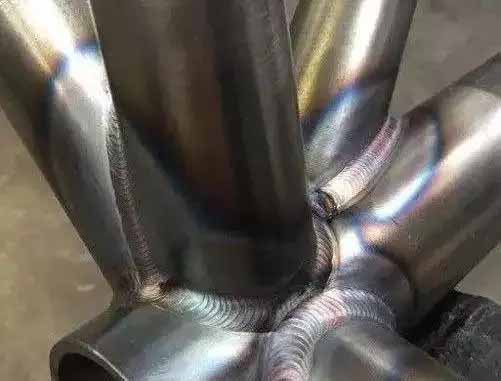
The increase in the welding speed promotes the increase of the strain rate of the welded joint, which increases the tendency of hot cracking. It can be seen that increasing the welding speed and welding current promotes the increase of the crack tendency. During the assembly and welding of the aluminum structure, the welding seam is not subjected to great rigidity, and measures such as segmented welding, preheating, or appropriate reduction of the welding speed can be adopted in the process.
Through preheating, the relative expansion of the test piece can be made smaller, the welding stress can be reduced accordingly, and the stress in the brittle temperature range can be reduced; try to use butt welding with open grooves and small gaps, and avoid the use of cruciform joints and Improper positioning, welding sequence.
When welding is finished or interrupted, the crater should be filled in time, and then the heat source should be removed, otherwise, it will easily cause crater cracks. For the welded joints of 5000 series alloy multi-layer welding, microcracks are often generated due to local melting of the intergranular, so the heat input of the next layer of weld bead must be controlled.
According to the test in this paper, for the welding of aluminum alloy, the surface cleaning of the base metal and the filler material is also very important. The inclusion of material in the weld will become the source of cracks and the main reason for the decline of weld performance.