Aluminum wire plays a crucial role in electrical power transmission due to its lightweight nature, cost-effectiveness, and conductivity. As a widely used conductor, aluminum wire is found in residential, commercial, and industrial applications. However, choosing the right aluminum wire requires understanding its specifications, which are typically represented by numerical designations.
This article aims to explain the meaning behind aluminum wire specifications, providing insights into the numbering system and its implications. We will explore the American Wire Gauge (AWG) system, compare common aluminum wire specifications, and discuss their applications and installation considerations.
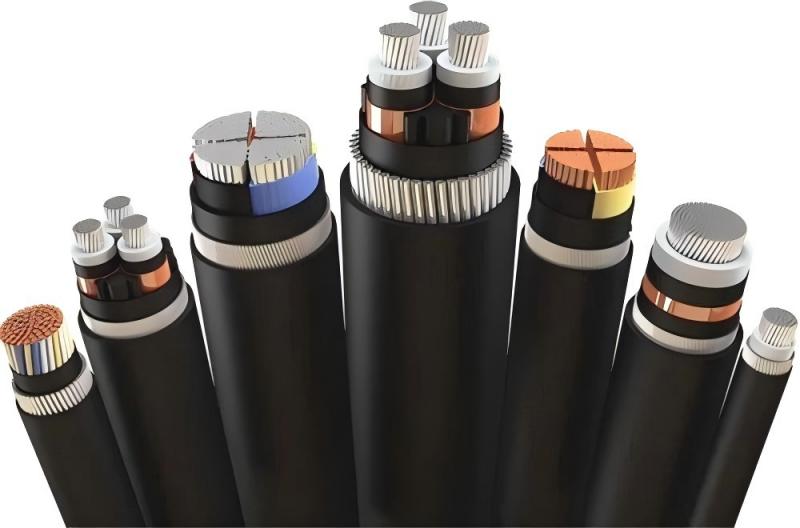
Understanding the Numbers in Aluminum Wire Specifications
1. American Wire Gauge (AWG)
The American Wire Gauge (AWG) is a standardized system used to measure the diameter of electrical conductors. In this system, a lower AWG number corresponds to a thicker wire, which generally has a higher current-carrying capacity. For aluminum wire, the ampacity (current-carrying capacity) is typically lower than that of copper wire of the same AWG size due to the differences in electrical conductivity.
2. Deciphering the Numbers in Aluminum Wire Specifications
Aluminum wire specifications often contain a series of numbers, such as “2-2-2-4” or “4-4-4-6.” These numbers indicate the size and number of conductors within the cable.
- The first set of numbers represents the size (AWG) of the phase conductors.
- The last number refers to the size of the neutral conductor, which may be the same as or smaller than the phase conductors.
For instance, in a “2-2-2-4 aluminum wire,” the three “2” conductors are the phase wires, while the “4” conductor serves as the neutral.
3. Examples of Different Number Combinations
- 2 2 2 4 Aluminum Wire: This specification is commonly used in residential wiring for circuits that require a higher current capacity. The AWG 2 phase conductors can handle more current, while the AWG 4 neutral conductor is sufficient for balancing the load.
- 4 4 4 6 Aluminum Wire: This configuration is often used in commercial buildings where the electrical load is moderate. The AWG 4 phase conductors provide adequate current capacity, and the AWG 6 neutral conductor is suitable for the expected load.
- 1 1 1 3 Aluminum Wire: This specification is used in industrial settings or for heavy-duty applications. The AWG 1 phase conductors can carry a significant amount of current, while the AWG 3 neutral conductor ensures proper load balancing.
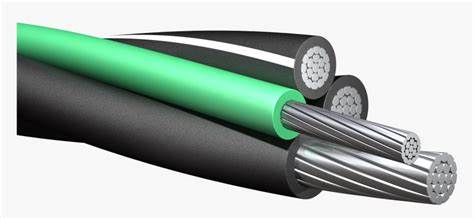
Comparison of Common Aluminum Wire Specifications
Different aluminum wire sizes have varying ampacities and are suitable for different applications. Here’s a comparison of some commonly used sizes:
Specification | Conductor Count | Neutral Size | Ampacity (Approx.) | Typical Applications |
2-2-2-4 | 3 conductors + neutral | 4 AWG | ~100A | Residential subpanels, URD |
4-4-4-6 | 3 conductors + neutral | 6 AWG | ~65A | Small subpanels, secondary distribution |
1-1-1-3 | 3 conductors + neutral | 3 AWG | ~130A | Large residential/commercial feeders |
6-6-6-6 | 4 equal conductors | 6 AWG | ~55A | Small circuits, mobile homes |
2-2-2-2 | 4 equal conductors | 2 AWG | ~90-100A | Residential and light commercial feeders |
4-4-4-4 | 4 equal conductors | 4 AWG | ~75A | Secondary distribution, small panel feeders |
4-4-4-2 | 3 conductors + neutral | 2 AWG | ~85A | Medium-sized subpanels |
The difference in neutral wire sizing affects the overall efficiency and voltage drop, making it crucial to select the appropriate configuration for the intended application.
Key Applications of Aluminum Wire
Aluminum wire’s versatility and cost-effectiveness have led to its widespread adoption in various electrical applications. Its lighter weight compared to copper, coupled with its adequate conductivity, makes it a practical choice for numerous power distribution and transmission scenarios.
1. Underground Residential Distribution (URD)
Underground Residential Distribution (URD) systems are a cornerstone of modern power delivery, particularly in residential and commercial areas where aesthetic considerations and weather-related vulnerabilities of overhead lines are concerns. Aluminum URD cables, such as those with 4-4-4-4 or 2-2-2-4 configurations, are specifically designed for this purpose.
- Direct Burial Capability: URD cables are engineered for direct burial in the ground, eliminating the need for extensive conduit systems in many cases. This significantly reduces installation costs and minimizes disruption to the surrounding environment.
- Moisture and Corrosion Resistance: These cables are typically insulated with cross-linked polyethylene (XLPE), a robust material that provides excellent electrical insulation and exceptional resistance to moisture and chemical corrosion. This is critical for underground applications where exposure to damp soil and varying environmental conditions is inevitable.
- Transformer to Building Connection: URD cables facilitate the crucial connection between pad-mounted transformers and the service entrance of residential and commercial buildings. They carry the secondary voltage from the transformer, delivering power to the building’s electrical system.
- Subdivisions and Urban Planning: URD systems are vital for modern subdivisions and urban planning, enhancing the visual appeal of neighborhoods by eliminating unsightly overhead wires. They also improve reliability by reducing the risk of weather-related outages.
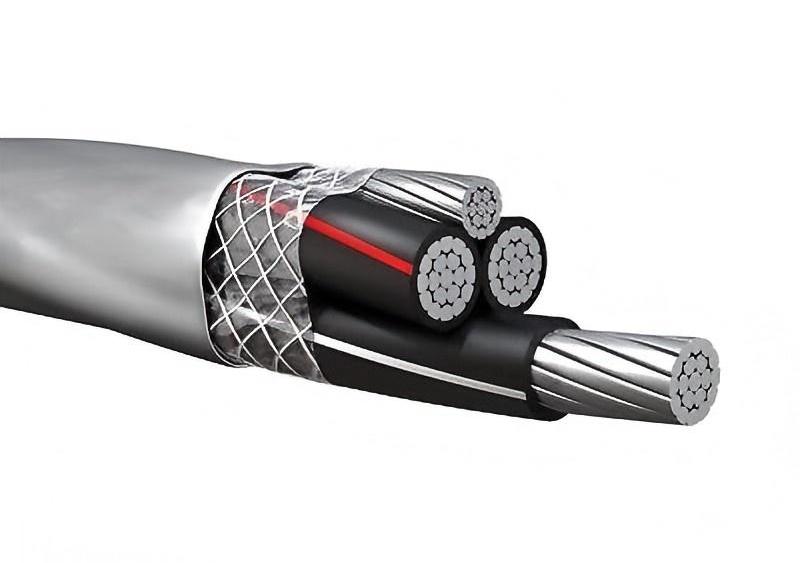
2. Residential and Commercial Wiring
Although historically there have been issues with early aluminum wiring installations in homes, modern aluminum wiring, when installed correctly, is a viable option.
- Service Entrances: Aluminum conductors are commonly used for service entrance cables, which connect the building’s electrical panel to the utility meter. These cables often carry substantial current loads, making aluminum’s cost-effectiveness advantageous.
- Branch Circuits (with Proper Installation): When using aluminum wire for branch circuits, strict adherence to modern installation practices is essential. This includes using appropriately rated connectors, and anti-oxidant compounds, and ensuring proper torque on connections. Older style aluminum wiring has had problems, and it is crucial to use modern methods.
- Large Commercial and Industrial Buildings: In large commercial and industrial settings, aluminum wiring is frequently used for feeders and branch circuits due to its cost advantages, especially in larger wire sizes. These buildings often require extensive wiring systems, making the economic benefits of aluminum significant.
3. Power Transmission
Aluminum’s lightweight nature and good conductivity make it ideal for long-distance power transmission.
- Overhead Transmission Lines: Aluminum conductors are the primary choice for overhead transmission lines, which carry high-voltage electricity over vast distances. These conductors are often reinforced with a steel core (aluminum conductor steel reinforced, or ACSR) to provide the necessary tensile strength for long spans.
- High-Voltage Transmission: Aluminum’s lower weight allows for longer spans between transmission towers, reducing the number of towers required and minimizing installation costs.
- Reduced Sag: While aluminum expands more than copper, the light weight of the aluminum reduces sag in the lines, especially over long distances.
- Substations: Aluminum bus bars and conductors are also used within substations, providing efficient and reliable connections for high-voltage equipment.
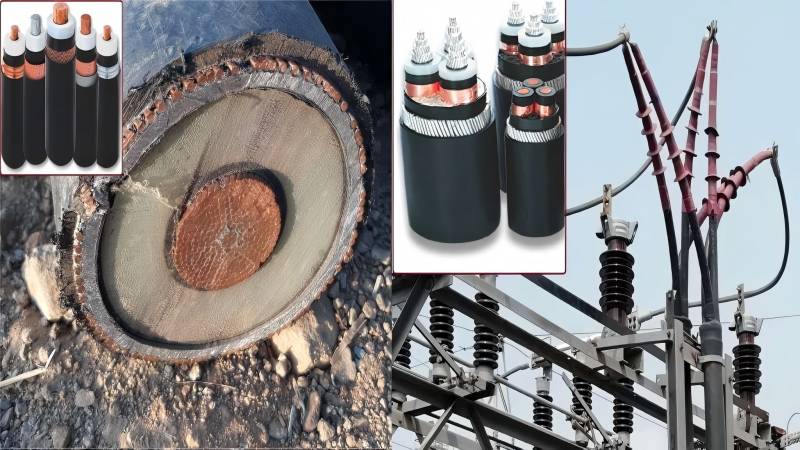
Installation and Safety Considerations
Proper installation of aluminum wire is critical to ensuring safety, reliability, and long-term performance in electrical systems. Below are key considerations for safe aluminum wire installation and maintenance.
1. Proper Installation Practices
Ensure that aluminum wire is installed following the National Electrical Code (NEC) regulations.
Use appropriate connectors rated for aluminum conductors to prevent overheating and connection failure.
2. Connecting Aluminum to Copper Wire
When connecting aluminum and copper wires, use copper-aluminum transition connectors to avoid galvanic corrosion.
Apply an anti-oxidation compound to aluminum terminations to prevent oxidation and ensure a reliable connection.
3. Preventing Oxidation and Corrosion
Aluminum wire is more susceptible to oxidation than copper, which can increase resistance and lead to overheating. Protective measures include:
- Using anti-oxidation compounds on all exposed aluminum conductors.
- Ensuring proper torque settings when securing aluminum conductors to terminals.
- Regular inspection and maintenance of aluminum wiring systems.
4. Choosing the Right Wire for Different Applications
The selection of aluminum wire specifications is not arbitrary. It is driven by specific application requirements:
- Current Load: The amperage requirements of the application dictate the necessary conductor size. Higher current loads necessitate larger gauge wires.
- Voltage Drop: Longer cable runs result in increased voltage drop. Selecting the appropriate conductor size minimizes voltage drop, ensuring efficient power delivery.
- Environmental Conditions: Environmental factors such as moisture, temperature, and chemical exposure must be considered. In harsh environments, cables with robust insulation and corrosion protection are essential.
- Electrical Codes and Standards: All installations must comply with local and national electrical codes, such as the National Electrical Code (NEC), to ensure safety and reliability.
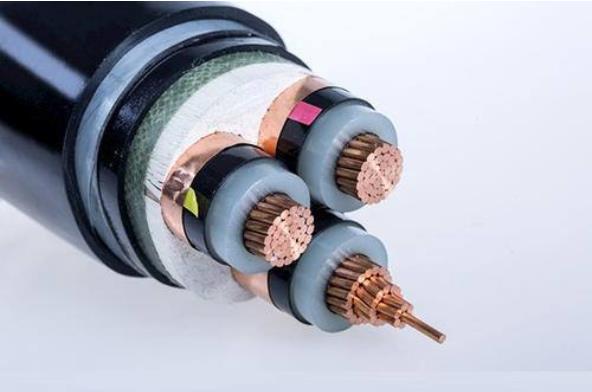
Understanding aluminum wire specifications is paramount for ensuring safe and efficient electrical installations. The numerical designations provide valuable information about conductor sizes and current-carrying capacities. By carefully considering the application’s requirements and adhering to proper installation practices, professionals can harness the benefits of aluminum wire in various electrical systems.