Aluminum is a versatile material that is commonly used in the manufacturing industry due to its lightweight, corrosion-resistant, and easy-to-machine properties. However, designing aluminum machining parts can be challenging, and requires consideration for the machining process. In this article, we’ll explore some of the design considerations that are important when machining aluminum parts.
Which features should be take into consideration?
Material Selection
The first consideration when designing aluminum machining parts is material selection. There are many different types of aluminum alloys available, each with their own unique properties. Some of the most common aluminum alloys used in machining include 6061, 2024, and 7075.
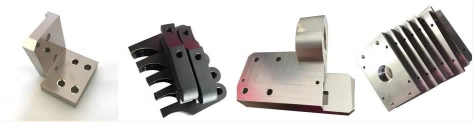
When selecting an aluminum alloy for machining, it’s important to consider factors such as strength, machinability, and cost. 6061 aluminum is a commonly used alloy due to its high strength and good machinability. However, it can be more expensive than other aluminum alloys. 2024 aluminum is another commonly used alloy due to its high strength-to-weight ratio, but it can be more difficult to machine. 7075 aluminum is a high-strength alloy that is often used in aerospace and military applications, but it can be more expensive than other aluminum alloys.
Part Geometry
The next consideration when designing aluminum machining parts is part geometry. Aluminum parts can be manufactured in a variety of shapes, including cylindrical, prismatic, and complex shapes. When designing part geometry for machining, it’s important to consider the need for fixturing and the ability to access difficult-to-reach areas.
For example, when machining a cylindrical part, it’s important to consider the length-to-diameter ratio of the part. Parts with a high length-to-diameter ratio may require additional support or specialized fixturing to prevent deflection during machining. Prismatic parts may require additional consideration for clamping and fixturing to ensure that they remain stable during machining. Complex shapes may require multi-axis machining or specialized fixturing to ensure that all areas of the part can be reached during machining.
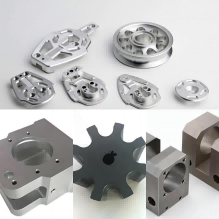
Tolerances
Tolerances are an important consideration when designing aluminum machining parts. Tolerances refer to the allowable deviation from the desired dimensions of a part. When setting tolerances for aluminum parts, it’s important to consider the machining process used and the requirements of the final product.
For example, some machining processes, such as milling, may be able to achieve tighter tolerances than others, such as turning. Additionally, the requirements of the final product may dictate the tolerances that are necessary. For example, a part that will be used in a high-precision application, such as a medical device, may require tighter tolerances than a part that will be used in a less critical application, such as a consumer product.
Surface Finish
Surface finish is another important consideration when designing aluminum machining parts. Surface finish refers to the texture or appearance of the surface of a part. There are many different surface finishes that can be applied to aluminum parts, including anodizing, polishing, and powder coating.
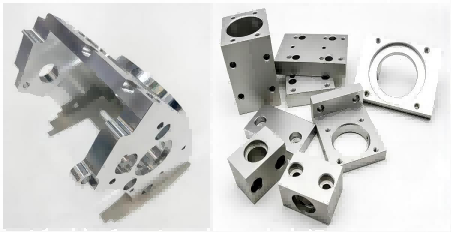
When selecting a surface finish for aluminum parts, it’s important to consider the requirements of the final product and the desired aesthetic appearance. Anodizing can be used to improve the corrosion resistance of aluminum parts, while polishing can be used to create a smooth, reflective surface. Powder coating can be used to create a durable, long-lasting finish that is resistant to scratches and chips.
Machining Parameters
The final consideration when designing aluminum machining parts is machining parameters. Machining parameters refer to the cutting speed, feed rate, and depth of cut used during the machining process. When selecting machining parameters for aluminum parts, it’s important to consider the material being machined, the desired surface finish, and the available machining equipment.
For example, different aluminum alloys may require different machining parameters due to their unique properties. Additionally, the desired surface finish of the part may dictate the use of specific machining parameters. Finally, the available machining equipment may limit the range of machining parameters that can be used.
It’s also important to note that optimizing machining parameters for aluminum parts can help to reduce machining time, increase tool life, and improve surface finish. For example, increasing the cutting speed may help to reduce machining time, while decreasing the feed rate may help to improve surface finish.
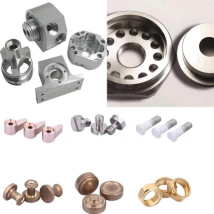
Conclusion
Designing aluminum machining parts requires careful consideration for the machining process. Material selection, part geometry, tolerances, surface finish, and machining parameters are all important considerations that can impact the performance and efficiency of aluminum parts.
By taking the time to carefully consider these factors, manufacturers can optimize the design and manufacturing process for aluminum parts, resulting in high-quality, efficient, and cost-effective products.
Ultimately, designing aluminum machining parts requires a balance of practical considerations, such as cost and machining efficiency, and the requirements of the final product, such as strength and aesthetic appearance. By balancing these factors, no matter it is CNC aluminum parts or customized aluminum parts, manufacturers can meet the needs of their customers while also achieving optimal manufacturing efficiency.
Related Products
Related Articles