Are forged aluminum alloys and die cast aluminum alloys the same thing? The answer is no, forged aluminum alloys are aluminum alloys that are mainly used for forging processing. Die-cast aluminum alloy belongs to cast aluminum alloy, but it mainly uses pressure-cast aluminum alloy. What is the natural difference between them? Keep reading this article you will find out the answer.
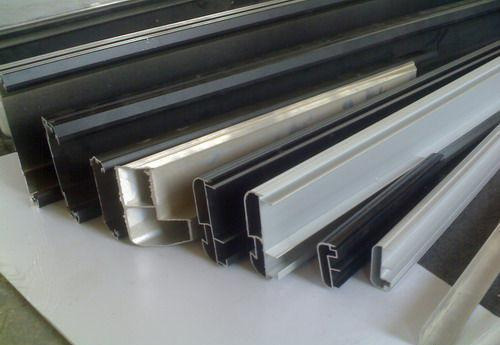
Different Chemical Contains Forged and Casting Aluminum Alloy
- Chemical Contain of Forged Aluminium Alloys
Forged aluminum alloys include A1-Si-Mg-Cu alloy and A1-Cu-Ni-Fe alloy. Commonly used forged aluminum alloys are LD2, LD5, LDl0, etc. They contain many kinds of alloying elements, but the content is small. They have excellent thermoplastic properties, so their forging properties are very good, and their mechanical properties are also good. This type of alloy is mainly used for die forgings under load and some forgings with complex shapes.
- Chemical Contain of Casting Aluminium Alloys
There are four types of cast aluminum alloys: A1-Si series, A1-Cu series, Al-Mg series and Al-Zn series. For cast aluminum alloys, in addition to the necessary mechanical properties and corrosion resistance, they should also have good casting properties. performance. Among the cast aluminum alloys, the best combination of casting properties and mechanical properties is A1-Si alloy, also known as silicon aluminum alloy.
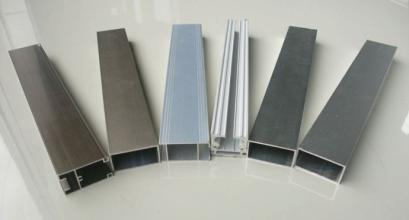
Cast aluminum alloy has good casting performance, low density, excellent corrosion resistance, heat resistance and weldability. It is used to manufacture castings with complex shapes but low strength requirements, such as aircraft, instrument housings, etc.; Strong and complex castings, such as motor housings, cylinder blocks, fan blades, engine pistons, etc.
An Introduction to 2 Different Machining Methods
- Casting
Casting is a metal thermal processing technology that human beings mastered relatively early, with a history of about 6,000 years. China entered the heyday of bronze castings from about 1700 BC to 1000 BC, and craftsmanship has reached a very high level. Casting is a method of casting liquid metal into a casting cavity suitable for the shape of the part, and after it cools and solidifies, the part or blank is obtained. The material to be cast is mostly a metal that is originally solid but heated to a liquid state (for example: copper, iron, aluminum, tin, lead, etc.), and the material of the mold can be sand, metal or even ceramic. In response to different requirements, the methods used will be different.
- Forging
Forging is a processing method that uses a forging machine to apply pressure to a metal blank to plastically deform it to obtain a forging with certain mechanical properties, certain shape and size. Forging (forging and stamping) is one of the two major components. Through forging, defects such as as-cast looseness generated in the metal smelting process can be eliminated, and the microstructure can be optimized. At the same time, due to the preservation of the complete metal streamline, the mechanical properties of forgings are generally better than those of castings of the same material. For important parts with high load and severe working conditions in related machinery, forgings are mostly used in addition to rolling plates, profiles or welded parts with simple shapes.
Which is Better Forging or Casting Aluminum Alloy?
Forging: Generally, it is the solid deformation of metal materials at high temperatures to achieve the shape you want;
Casting: After the metal material is melted, the liquid is poured into the cavity to get the shape you want;
Die casting: The hydraulic metal is quickly injected into the mold through the die casting machine to obtain the corresponding casting, which is generally only used for non-ferrous alloys (mainly aluminum and zinc alloys, but also copper alloys)
The strength first depends on the material, and then the process. The forged material has the best internal fiber structure and the best comprehensive strength. Die casting is only a type of casting. Since general die castings cannot be heat treated, the strength is lower than that of similar castings after heat treatment. However, the strength before heat treatment is higher than that of castings without heat treatment.