Aluminum plates are essential components in numerous industrial applications, valued for their versatility, strength, and lightweight. Two notable types of aluminum plates are the MIC-6 aluminum plate and the aluminum cast plate. This article delves into the key characteristics, manufacturing processes, and application areas of both materials, equipping readers to make informed choices for their specific needs.
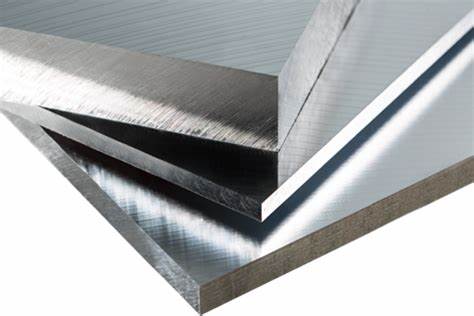
Understanding MIC-6 Aluminum Plate: Characteristics and Process
MIC-6 aluminum plate is a high-precision cast aluminum plate renowned for its exceptional dimensional accuracy and thermal stability. It is a meticulously formulated aluminum alloy specifically designed to meet the stringent demands of modern industrial applications where precise tolerances are paramount.
The production of MIC-6 aluminum plate utilizes a unique continuous casting process that guarantees uniformity and consistency throughout the material. This process involves several key steps:
- Chemical Composition: The precise balance of elements within the MIC-6 alloy, including aluminum (Al), silicon (Si), copper (Cu), magnesium (Mg), zinc (Zn), manganese (Mn), and chromium (Cr), is meticulously controlled. This ensures consistent material properties throughout the plate.
- Continuous Casting: Unlike traditional casting methods that involve pouring molten metal into molds in batches, MIC-6 utilizes a continuous casting technique. This method casts plates of specific thicknesses individually, resulting in exceptional uniformity and consistency across each plate.
- Continuous Feeding: During the casting process, molten metal is continuously fed into the mold. This eliminates the formation of defects often associated with intervals and seams that occur in traditional batch casting methods, leading to a more complete and uniform aluminum alloy plate.
- Stable Heat Dissipation: The design of the casting process ensures controlled and stable heat dissipation on both surfaces of the MIC-6 aluminum plate. This minimizes the formation of thermal gradients within the material, preventing warping and cracking due to thermal stress.
- Excellent Heat Stability: MIC-6 aluminum plate exhibits remarkable heat stability, maintaining its dimensional accuracy even in high-temperature environments. This characteristic makes it ideal for applications where thermal expansion can be a significant concern.
The meticulous manufacturing process of MIC-6 aluminum plate translates into several key advantages:
- Superior Dimensional Accuracy: Due to the controlled casting process and minimal internal stress, MIC-6 plates boast exceptional dimensional accuracy. Tolerances can be maintained within a remarkable range of 0.1mm (0.004 inches), making them ideal for precision machining applications.
- Minimal Machining Distortion: The fine grain structure of MIC-6 combined with its stress-relieved nature minimizes deformation during high-speed machining operations. This allows for the creation of intricate components with tight tolerances without compromising on precision.
- Excellent Machinability: MIC-6 is a free-cutting aluminum alloy, meaning it produces small, uniform chips during machining. This reduces tool wear and tear, leading to cleaner cuts and improved machining efficiency.
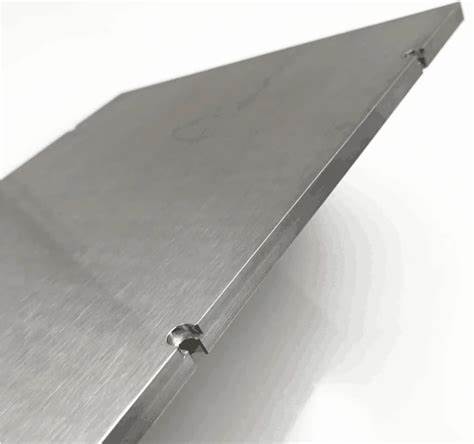
Understanding Aluminum Cast Plate: Characteristics and Process
Aluminum cast plate, in general terms, refers to any aluminum plate directly formed through a casting process. Compared to traditional rolled aluminum plates, cast plates offer specific advantages, such as:
- High Production Efficiency: The casting process for aluminum cast plates is typically faster than rolling, leading to higher production rates and potentially lower costs.
- Lower Cost: Due to the streamlined production process, aluminum cast plates can be more cost-effective than MIC-6 plates, making them a suitable choice for applications where budget constraints are a factor.
However, there are some trade-offs with this efficiency:
- Varied Mechanical Properties: The internal structure of aluminum cast plates can exhibit some inconsistencies compared to MIC-6 plates. This can lead to slight variations in mechanical properties across different parts of the same plate.
- Limited Alloy Variety: The casting process for aluminum cast plates is generally limited to a smaller range of aluminum alloys compared to rolled plates. This may restrict material selection for specific applications.
The production of aluminum cast plates typically involves the following steps:
- Melting: Aluminum ingots are introduced into a melting furnace and heated until they transform into a molten liquid.
- Casting: The molten aluminum is treated and then poured into a casting machine, forming an aluminum slab or ingot.
- Rolling: The cast aluminum ingot is then passed through a series of rollers to achieve the desired plate thickness and dimensions. In some cases, multiple rolling passes might be required.
- Cooling Treatment: After rolling, the aluminum plate undergoes a cooling process to stabilize its temperature and achieve a workable state.
- Surface Treatment: The surface of the plate might be subjected to cleaning and other treatments to ensure a smooth, blemish-free finish.
- Cutting: The final step involves cutting the aluminum plate into desired lengths and sizes to meet customer requirements.
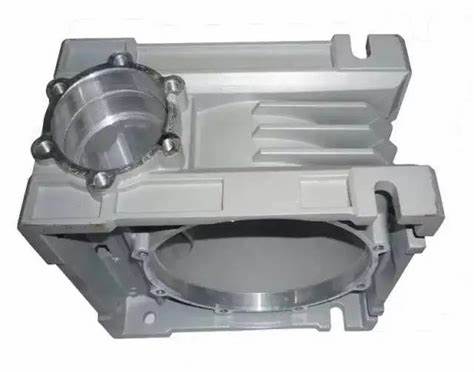
Applications for MIC-6 Aluminum Plate and Aluminum Cast Plate
The exceptional dimensional accuracy, thermal stability, and superior machinability of MIC-6 aluminum plate make it a prime candidate for applications in various industries where precision and performance are critical. Here are some prominent examples:
- Aerospace: Due to its lightweight nature, high strength-to-weight ratio, and resistance to corrosion, MIC-6 aluminum plate is extensively used in the aerospace industry for manufacturing aircraft structural components, including:
- Aircraft skin (body panels)
- Fuselage frames
- Stringers (longitudinal support beams)
- Wing components
- Landing gear components
- Engine components requiring high dimensional stability
- Automotive: The automotive industry utilizes MIC-6 aluminum plate for its lightweight properties and excellent machinability in the production of various car body parts, such as:
- Doors and hoods
- Engine components like cylinder heads and intake manifolds
- High-performance brake calipers requiring precise tolerances
- Heat sinks for efficient heat dissipation
- Electronics: In the electronics industry, the MIC-6 aluminum plate is valued for its ability to conduct heat effectively while maintaining dimensional stability. Applications include:
- Circuit board substrates for electronic devices
- Heat sinks for managing thermal loads in electronic components
- Precision housings for electronic equipment
- Construction and Decoration: While not as common as in other industries, MIC-6 aluminum plate can be employed in construction and decoration projects where high dimensional accuracy and a sleek aesthetic are desired. Examples include:
- Architectural cladding panels
- Building structural components requiring tight tolerances
- High-end window and door frames
Aluminum cast plates, on the other hand, are a more cost-effective option for applications where precise tolerances are less critical. Their advantages lie in their faster production times and lower costs. Here are some common applications:
- Machinery and Equipment: Due to their affordability and reasonable strength, aluminum cast plates are used in the fabrication of various machine parts, including:
- Machine bases and housings
- Frames and brackets
- Non-critical structural components
- Automotive: While not ideal for high-performance components, aluminum cast plates can be used for some automotive applications where cost is a significant factor, such as:
- Engine blocks for non-performance vehicles
- Cylinder heads in less demanding engines
- Brake calipers for everyday vehicles
- Construction and Decoration: In construction and decoration applications, aluminum cast plates can be a suitable choice for:
- Building components with less stringent dimensional requirements
- Decorative elements like railings and fences
- Lighting fixtures where precise tolerances are not crucial
- Furniture components that prioritize aesthetics over structural rigidity
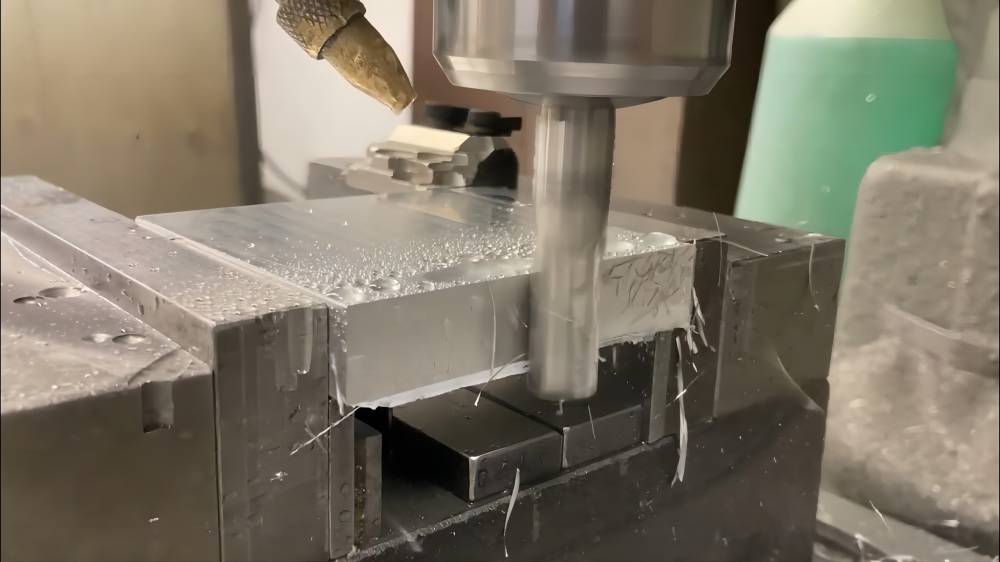
Tips for Selecting the Right Cast Aluminum Plate
Choosing between MIC-6 aluminum plate and aluminum cast plate hinges on the specific project requirements. Here’s a breakdown to aid your decision:
1. When to Choose MIC-6 Aluminum Plate
- Dimensional Accuracy is Paramount: If your project demands exceptional dimensional accuracy and minimal distortion during machining, MIC-6 is the clear winner. Its superior dimensional stability allows for the creation of highly precise components.
- Thermal Stability is Crucial: Applications involving high temperatures where maintaining precise dimensions is critical necessitate MIC-6. Its excellent thermal stability ensures minimal dimensional changes even in hot environments.
- Machinability is a Priority: For projects requiring intricate machining operations with tight tolerances, MIC-6’s free-cutting nature and minimal deformation during machining make it the preferred choice.
2. When to Choose Aluminum Cast Plate
- Cost is a Major Factor: If budget constraints are a primary concern, aluminum cast plates offer a more cost-effective solution compared to MIC-6.
- Dimensional Accuracy is Less Critical: When precise tolerances are not essential for the application, and slight variations in plate dimensions are acceptable, aluminum cast plates can be a suitable option.
- Production Speed is Important: For projects with tight deadlines, the faster production process of aluminum cast plates can be advantageous.
Conclusion
Both MIC-6 aluminum plate and aluminum cast plate are valuable materials in the metalworking industry, each with its own strengths and weaknesses. Understanding the distinct characteristics and manufacturing processes of each material empowers you to make informed decisions when selecting the optimal material for your specific application. When prioritizing dimensional accuracy, thermal stability, and superior machinability, the MIC-6 aluminum plate reigns supreme. However, if cost is a major factor and precise tolerances are less critical, aluminum cast plates offer a compelling alternative. By carefully considering the project requirements and weighing the advantages of each material, you can select the most appropriate option to ensure the success of your project.