Today, the word “lightweight” has developed from a term in the automotive industry to a high-frequency word in media news. In simple terms, lightweight is to reduce the vehicle’s weight as much as possible on the premise of ensuring the strength and safety of the vehicle, thereby improving the power of the vehicle, reducing fuel consumption, and reducing exhaust pollution. As for the advantages and disadvantages of the all-aluminum body structure, you can refer to this article “Is all-aluminum car structure good or bad?“.
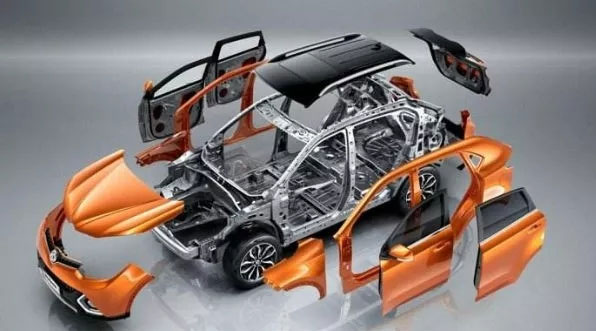
In recent years, due to the increasingly strict requirements for environmental protection and energy-saving, the lightweight of automobiles has become an unstoppable trend in the development of automobiles in the world.
According to the report of the European Aluminum Association, every 100kg reduction in vehicle mass can save 0.6L of fuel per 100 kilometers and reduce CO2800-900g. The density of aluminum is only 1/3 of that of steel, and it has good plasticity and recyclability, making it an ideal lightweight material for automobiles.
During the first and second oil crises in the 1970s, in the face of rising oil prices, automakers around the world tried to use aluminum alloys to make previously steel radiators, cylinder heads, and bumpers. Improve fuel efficiency.
Since then, the proportion of aluminum alloys in automobiles has continued to increase. According to research data released by the famous consulting firm Ducker Worldwide, the average amount of aluminum used in European cars has tripled since 1990, from 50kg to the current 151kg, and will increase to 196kg in 2025.
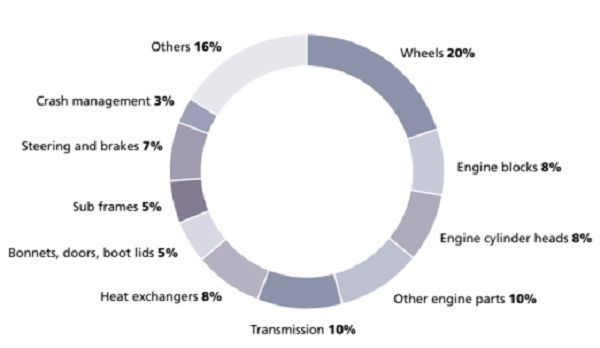
At present, the trend for automobile lightweight is more and more fierce, and aluminum alloys are widely used in wheel hubs, engines, radiators, oil pipes, etc.
The mass of the car body accounts for about 40% of the total mass of the car. For the lightweight of the whole vehicle, the lightweight of the car body plays a pivotal role. According to the data of EuroCarBody 2016, the application rate of aluminum alloy has reached more than half of the quality of the body-in-white (that is, the body that has been welded but not painted) of some high-end models.
For example, the Aston Martin DB11 aluminum alloy application rate is as high as 86.1%, the second-generation Honda NSX (Acura NSX) reaches 79.0%, and the fifth-generation Land Rover Discovery (Land Rover Discovery) reaches 62.9%.
However, the application of aluminum alloys in the body of ordinary models is still relatively small. According to data from the well-known consulting firm Ducker Worldwide, the penetration rate of aluminum alloy sheets in automobile bodies was only 4% in 2015.
Today, all-aluminum body manufacturing is still a technology at the top of the pyramid, which is only applied to some high-end models. Body weight reduction is an important research topic in the lightweight development of automobile manufacturers.
Main types of aluminum alloys for vehicles
At present, aluminum alloys for automobiles can be divided into die-casting aluminum alloys and deformed aluminum alloys, among which die-casting aluminum alloys are the main ones, accounting for about 66%. Deformed aluminum alloys can be divided into rolled sheets (18%), extruded profiles (11%), and a small number of forgings (5%).
It is worth noting that although cast aluminum alloy is still the main form of aluminum alloy for vehicles in 2016, its share has dropped by 8 percentage points compared with 2012.
On the contrary, the share of rolled sheet material increased significantly from 13% in 2012 to 18% in 2016 due to the development of the lightweight body. At the same time, the share of extruded profiles and forgings did not change much.
Cast aluminum alloy
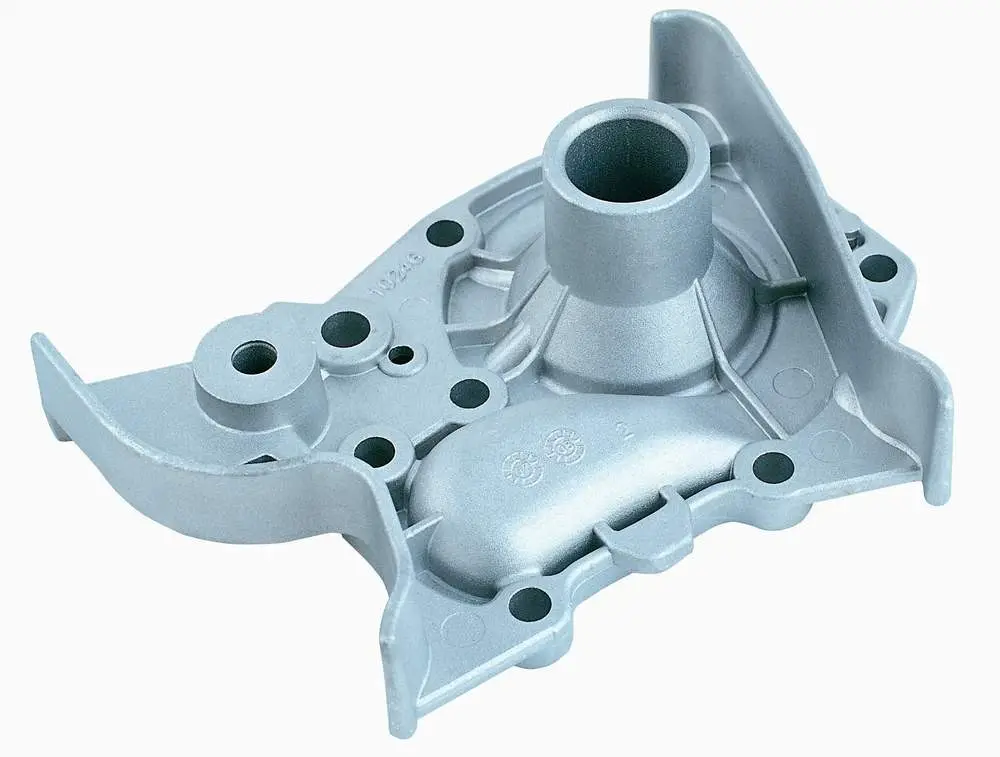
Cast aluminum alloys are the most widely used types of aluminum alloys in most automobiles, and are widely used in structural parts such as wheels, engine parts, underframes, shock absorber brackets, and space frames. In the automotive industry, cast aluminum alloy wheels are the most popular parts with a high aluminization rate.
At present, the vast majority of aluminum alloy wheels are made of A356 alloy by low-pressure casting, and some high-end wheels are made by squeeze casting (industrial die forging), forging, or spinning technology.
Both the cylinder block and the cylinder head of the engine require materials with good thermal conductivity and strong corrosion resistance, which are the advantages of aluminum alloys. At present, a large number of automobiles use aluminum cylinder blocks and cylinder heads, but cast iron is still used on some occasions that require high strength and high resistance.
In recent years, the development of new Al-Si-Cu-Mg-Fe alloys and the development of corresponding casting technologies have enabled aluminum alloy castings to achieve higher performance, further promoting the application of aluminum alloys in engine components (including diesel engines).
There are also various casting methods for the cylinder block and head, such as gravity casting and low-pressure casting. In addition, cast aluminum alloys are widely used in shock absorber brackets, electric vehicle battery packs, structural boxes, and other structural parts. Since these parts are mostly thin-walled parts with complex shapes, Al-Si alloys are mostly produced by high-pressure casting.
Deformed aluminum alloy
Compared with cast aluminum alloys, the average application share of wrought aluminum alloys in automobiles is still small. According to a survey by Ducker Worldwide, wrought aluminum alloys accounted for only 34% of automotive aluminum alloys in 2016 (18% for rolled sheets, 11% for extruded profiles, and 5% for forgings).
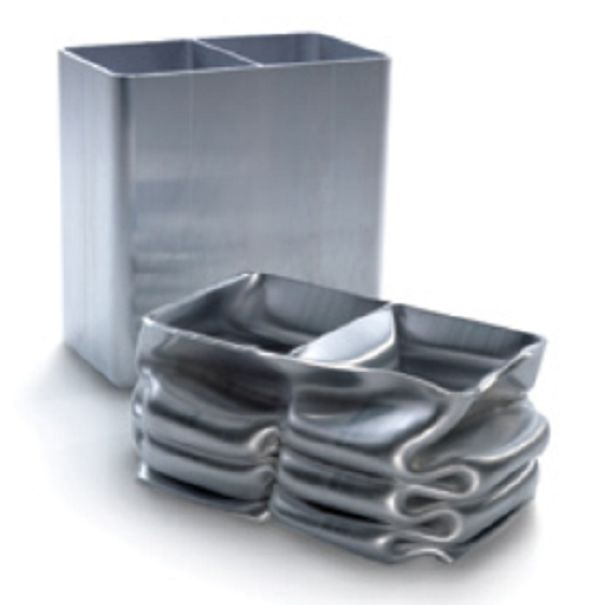
However, in some high-end models with all-aluminum bodies, the share of deformed aluminum alloys is much higher than that of cast aluminum alloys. At present, the industry has invested a lot in the research and development and application technology of deformed aluminum alloys including all-aluminum body technology, and its proportion has increased rapidly.
Ducker Worldwide predicts that due to the rapid development of aluminum alloy body technology, the application of wrought aluminum alloys (especially rolled sheets) in automobiles will usher in rapid growth.
Deformed aluminum alloys for vehicles mainly include the 5xxx series (Al-Mg series), 6xxx series (Al-Mg-Si series), and a small amount of 2xxx series (Al-C series) and 7xxx series (Al-Zn-Mg series). Among them, 5xxx series alloys cannot be strengthened by heat treatment and have excellent formability. However, after forming, the yield point is likely to be extended and the surface will wrinkle, which affects the appearance quality of the product. Therefore, it is mainly used for parts with complex shapes such as inner plates.
6xxx series alloys can be strengthened by heat treatment through the solid solution of Mg and Si and the aging precipitation of the Mg2Si phase. After coating and drying, the strength is improved, and they have high dent resistance, which is suitable for outer panels, body frames, and other requirements. strength and rigidity.
In addition to rolled sheets, extruded profiles are also important deformed aluminum alloys for vehicles, which are generally suitable for structural parts of the equal section, such as bumpers, energy-absorbing boxes, and front sections of front longitudinal beams, door sills, and rear sections of rear longitudinal beams.
Medium-strength 6xxx is the main material for extruded profiles due to its high extrusion rate and surface quality, as well as its age-hardening properties during extrusion. On some occasions with higher strength requirements, high-strength 7xxx series aluminum alloys are also used to produce extruded profiles.
How will the automotive aluminum alloy develop?
Aluminum alloys have played an important role in the wave of automotive lightweight, but they also face important challenges. Lightweighting does not only require weight reduction but also requires a balance between the performance, safety, cost, and weight of the vehicle.
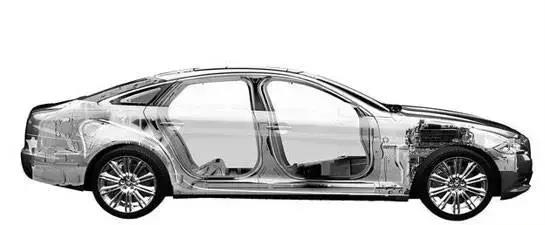
At present, the core resistance faced by aluminum alloys for vehicles is still high cost, which makes the application of all-aluminum bodies only limited to high-end models and cannot be expanded to a large number of economic models for the time being. The performance limitation of aluminum alloy is also an important factor restricting its development. It still can’t replace steel in some parts.
At the same time, the connection technology of aluminum alloys, especially multi-material connection technologies such as cast iron-aluminum, steel-aluminum, magnesium-aluminum, etc., is also a major factor hindering the application of aluminum alloys in automobiles. Audi’s new A8 D5 “abandoned” the all-aluminum body that has persisted for more than 20 years, and adopted a considerable weight of high-strength steel.
Affected by this, the D5 model is 51KG heavier than the previous generation model, but the torsional rigidity of the body is greatly increased by 24%, the safety is greatly enhanced, and the cost is also greatly reduced.
Under the Sixth Framework Plan, the European Union organized 38 units from 9 countries and regions to cooperate and implement the SuperLight-Car joint research and development project (SuperLight-Car) from 2004 to 2009.
The experience of this project shows that the further development of aluminum alloys for vehicles should be devoted to the research and development of new high-performance alloys and new production technologies at the same time. The research and development work also needs to integrate resources, led by automobile manufacturers, and cooperate with raw material, parts suppliers, and relevant scientific research institutions to jointly explore advanced lightweight technologies and promote the establishment of a lightweight body-related industry chain.