Heat sealing aluminum foil is a critical process across numerous industries, from food packaging to pharmaceuticals. Achieving a perfect seal ensures product integrity, extends shelf life, and maintains critical barriers against contaminants. This article delves into the expert techniques required to master this process. Mastering heat sealing is not just about applying heat; it’s about precision, consistency, and a deep understanding of the materials involved.
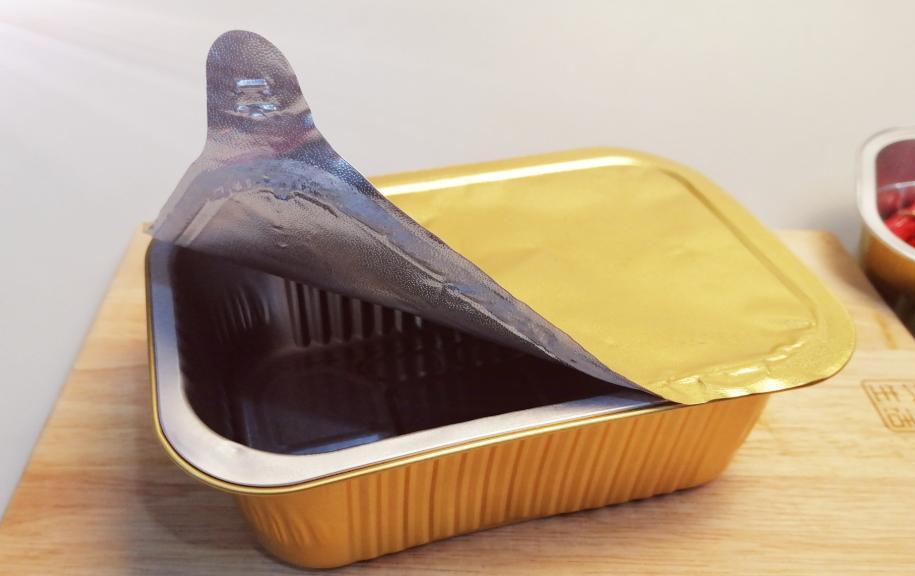
Why Use Heat Sealing for Aluminum Foil
Heat sealing provides a reliable, airtight, and tamper-proof solution for packaging. Aluminum foil is an ideal material for this process because of its excellent barrier properties, flexibility, and durability. It prevents moisture, light, and oxygen from penetrating, ensuring product integrity. This makes it indispensable for sensitive items such as food, medicine, and electronics.
Applications of Heat-Sealed Aluminum Foil
- Food Packaging: Extends shelf life by creating an airtight seal for snacks, beverages, and frozen foods.
- Pharmaceuticals: Protects medicines and medical devices from contamination and environmental exposure.
- Industrial Products: Used for sealing chemicals or sensitive electronic components to prevent damage during transportation.
- Cosmetics: Provides a hygienic and secure packaging solution for creams, serums, and powders.
In conclusion, heat sealing aluminum foil is a versatile and efficient packaging method with widespread applications, making it a go-to choice for many industries.
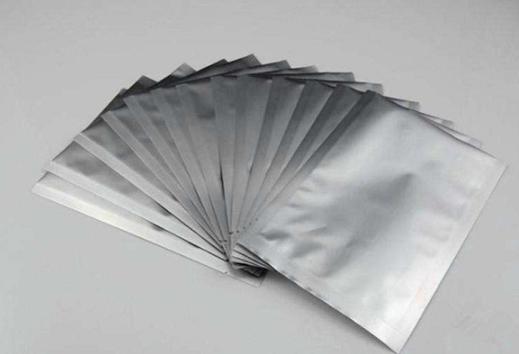
How to Heat Seal Aluminum Foil
Achieving a flawless heat seal on aluminum foil hinges on precise control over several critical factors. Beyond the basic parameters of heat and pressure, meticulous attention to coating uniformity and pinhole prevention is paramount. These advanced techniques ensure a robust, reliable seal, especially in sensitive applications.
Step-by-Step Introduction:
1. Material Selection and Inspection:
Begin with high-quality aluminum foil, ensuring it meets the required specifications for thickness and purity. Critically inspect the foil for any pre-existing defects, such as scratches or tears, which can compromise the seal.
Verify the integrity and uniformity of the sealing layer coating. This is done by using quality control equipment that measures the thickness of the coating, and checks for any unevenness.
2. Coating Precision:
The sealing layer, typically a polymer, must be applied with extreme precision. Variations in coating thickness can lead to inconsistent seals.
Utilize advanced coating technologies, such as gravure or extrusion coating, to ensure uniform application. Implement inline monitoring systems track coating thickness in real-time, allowing for immediate adjustments. A coating thickness variation of more than 2 microns can cause a weak seal.
3. Pinhole Control Techniques:
Pinhole formation, tiny holes in the foil, can compromise barrier properties and seal integrity.
Pinhole control techniques are implemented to minimize breaches in the foil’s barrier properties. Specialized handling and processing methods reduce mechanical stress, and cleanroom environments minimize particulate contamination. Pinhole detection systems, using light or electrical current, identify any imperfections. In pharmaceutical applications, even a single pinhole can render a package unusable, emphasizing the critical nature of these controls.
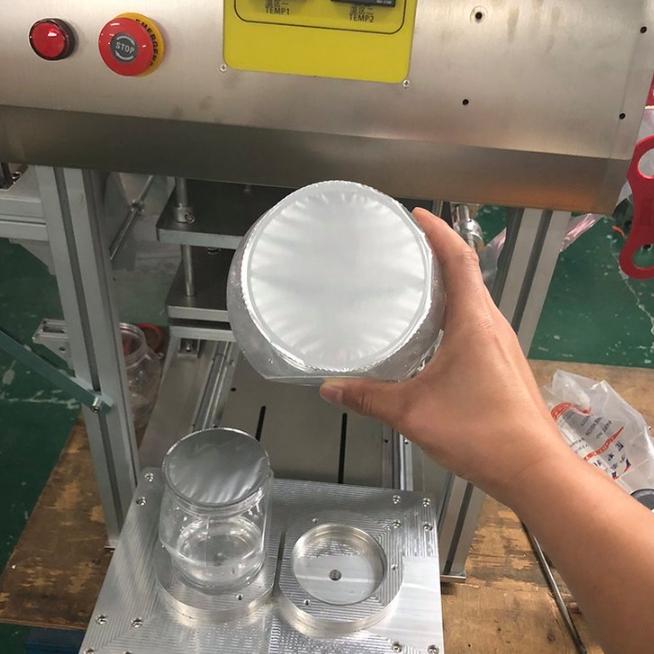
4. Equipment Setup and Calibration:
Select a heat sealing machine capable of precise temperature and pressure control. Calibrate the machine meticulously, considering the specific foil thickness and sealing layer composition. Ensure the sealing jaws are clean and free from any contaminants that could interfere with the seal.
5. Alignment and Sealing Process:
Accurate alignment of the foil between the jaws is crucial for a uniform seal. During the sealing process, consistent pressure and heat are applied for a precise dwell time. In some instances, modified atmosphere packaging (MAP) is used to extend shelf life.
6. Seal Inspection and Testing:
Finally, each seal undergoes a thorough inspection and testing phase. Visual inspections are conducted for uniformity, and seal strength tests, like peel or burst tests, verify the bond’s robustness. Leak detection equipment is used to identify any breaches, especially vital in medical and pharmaceutical applications.
By focusing on coating precision and pinhole control, manufacturers can elevate the quality and reliability of their heat-sealed aluminum foil products, ensuring optimal performance in demanding applications.
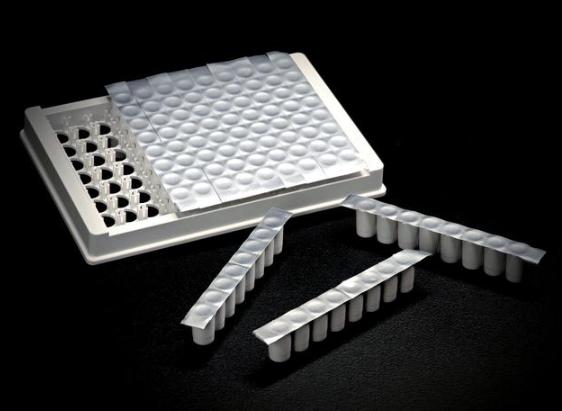
Key Factors for Achieving a Perfect Seal
Achieving a flawless heat seal involves controlling several key parameters that directly affect the quality, durability, and effectiveness of the seal. Below is a detailed explanation of these critical factors:
Temperature Control:
Temperature is one of the most critical variables in heat sealing. An optimal range must be maintained to activate the heat-sealable coating without damaging the aluminum foil or underlying materials. For instance:
- Heat-sealable lacquer-coated foil typically requires temperatures between 180°C and 250°C.
- Variations outside this range can result in weak seals (underheating) or damage (overheating).
Use calibrated sensors and automated systems to maintain consistent temperatures during the process.
Pressure Optimization:
Pressure ensures the foil adheres uniformly to the sealing surface. Insufficient pressure can lead to gaps or uneven seals, while excessive pressure may distort the foil. Key considerations include:
- Adjusting pressure according to foil thickness and coating type.
- Use evenly distributed pressure across the sealing area to avoid wrinkles or stress points.
Regularly calibrate equipment to ensure optimal pressure settings.
Dwell Time:
Dwell time refers to the duration the sealing surfaces are in contact under heat and pressure. This time must be sufficient for the heat to transfer through the foil and activate the adhesive layer.
- Typical dwell times range from 0.5 to 2 seconds, depending on foil properties and application requirements.
- Prolonged dwell times can cause scorching, while shorter durations may lead to incomplete seals.
Experimentation and fine-tuning are essential to identify the ideal dwell time for each application.
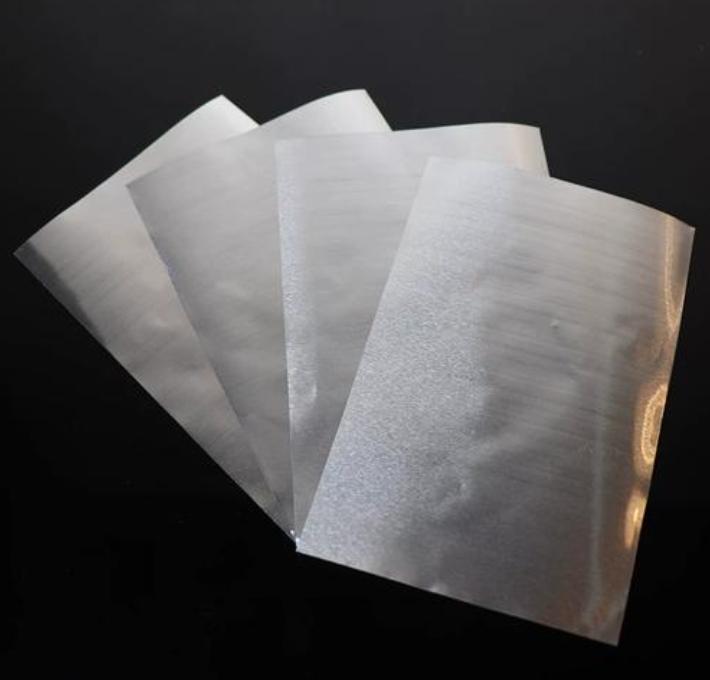
Foil Quality and Integrity:
The quality of the aluminum foil itself significantly impacts the sealing process. Factors to monitor include:
- Thickness uniformity: Variations can cause uneven heat transfer.
- Pinhole occurrence: Defects can compromise the seal’s integrity.
- Coating consistency: Uneven coatings can lead to weak adhesion.
Perform thorough inspections and source high-quality foil to minimize issues.
Environmental Factors:
External conditions, such as humidity and ambient temperature, can influence the heat sealing process. For example:
- High humidity can affect the adhesion of certain coatings.
- Cold environments may require longer dwell times or higher temperatures to achieve proper sealing.
Maintain a controlled environment for consistent results.
Equipment Maintenance:
Properly maintained equipment ensures reliable performance and prevents defects during sealing. Best practices include:
- Regular cleaning of sealing surfaces to remove residue or contaminants.
- Inspecting and replacing worn components, such as heating elements or pressure pads.
- Periodic calibration of temperature, pressure, and timing systems.
Schedule routine maintenance checks to avoid unexpected downtime and ensure consistent seal quality.
Heat sealing aluminum foil to perfection requires a combination of quality materials, precise equipment settings, and attention to detail. By understanding why aluminum foil is a preferred choice, following step-by-step sealing methods, and considering critical factors like temperature, pressure, and foil quality, manufacturers can enhance their packaging efficiency and product safety. Whether in food, pharmaceuticals, or industrial applications, mastering these techniques ensures a reliable seal that meets industry standards.