In the realm of engineering and construction, the selection of materials plays a pivotal role in determining the success and longevity of a project. Among the plethora of options available, extruded aluminum tubes and extruded steel tubes stand out as two of the most widely used and versatile materials. While both offer unique properties and advantages, their distinct characteristics make them suitable for different applications. This article delves into the intricacies of extruded aluminum tubes and extruded steel tubes, providing a comprehensive comparison to guide you in selecting the right material for your specific needs.
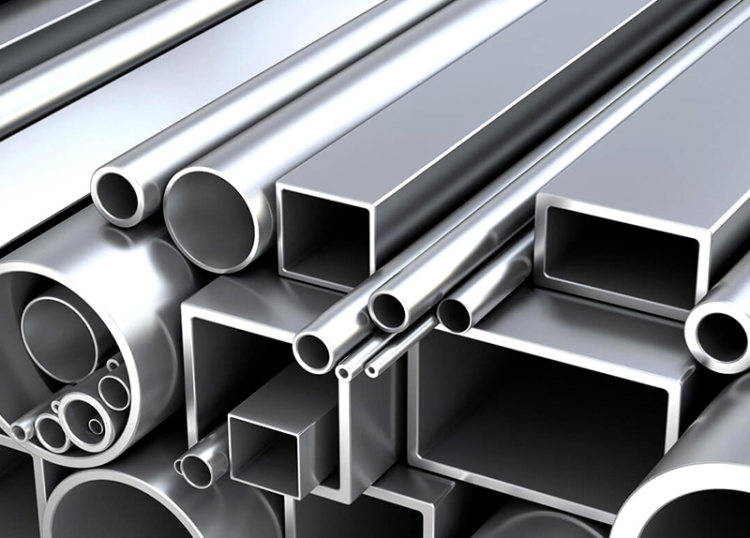
Properties and Characteristics of Extruded Aluminum Tubes
Extruded aluminum tubes are formed by forcing heated aluminum billets through a shaped die, resulting in a variety of hollow cross-sections. Aluminum, as a material, possesses several inherent qualities that make its extruded form particularly advantageous for many applications.
- Lightweight and High Strength-to-Weight Ratio: Aluminum is significantly lighter than steel, making it an ideal choice for weight-sensitive applications such as aerospace and automotive components. Despite its lightness, aluminum offers remarkable strength, boasting a strength-to-weight ratio that exceeds that of many other metals.
- Excellent Corrosion Resistance: Aluminum forms a naturally protective oxide layer that shields it from corrosion. This inherent resistance to rust and other forms of corrosion makes aluminum a suitable material for outdoor applications, marine environments, and chemically reactive environments.
- Good Electrical and Thermal Conductivity: Aluminum’s excellent electrical conductivity makes it a preferred choice for electrical wiring and components. It also exhibits good thermal conductivity, enabling efficient heat transfer in applications such as heat sinks and radiators.
- Easily Machinable and Formable: Aluminum is highly machinable, allowing for precise cutting, drilling, and milling operations. It is also relatively formable, making it suitable for bending, rolling, and drawing into various shapes.
- Environmentally Friendly and Recyclable: Aluminum is one of the most recyclable metals, with over 70% of all aluminum ever produced still in use today. Its recycling process consumes significantly less energy than primary production, making it an environmentally friendly choice.
Properties and Characteristics of Extruded Steel Tubes
Extruded steel tubes are produced using a similar extrusion process as aluminum tubes, but with heated steel billets instead. Steel, as a material, brings its own set of distinct properties that contribute to its widespread use in various industries.
- Exceptionally High Strength and Toughness: Steel is renowned for its exceptional strength and toughness, making it the material of choice for applications requiring high load-bearing capacity and resistance to impact and deformation.
- Good Weldability: Steel offers excellent weldability, allowing for strong and reliable joints that can withstand significant stress. This property is crucial in structural applications and in the fabrication of complex assemblies.
- Affordable Cost: Compared to aluminum, steel generally has a lower production cost, making it a more economical option for certain applications where cost is a primary consideration.
- Fire Resistance: Steel exhibits superior fire resistance, making it a preferred choice for structural components and safety equipment in fire-prone environments.
- Wide Range of Available Sizes and Shapes: Extruded steel tubes are available in a vast array of sizes and shapes, catering to a wide range of application requirements.
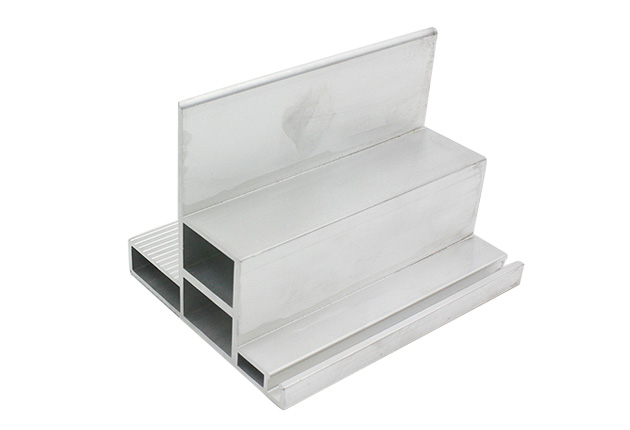
Detailed Comparison of Extruded Aluminum Tubes and Extruded Steel Tubes
Property | Extruded Aluminum Tubes | Extruded Steel Tubes |
Strength | High strength-to-weight ratio, suitable for applications requiring high strength while minimizing weight | Exceptionally high strength, ideal for applications demanding exceptional load-bearing capacity and resistance to impact and deformation |
Weight | Lightweight, making it an excellent choice for weight-sensitive applications where reducing weight is crucial | Heavier than aluminum, but still offers a favorable strength-to-weight ratio in many applications |
Corrosion resistance | Excellent corrosion resistance, making it suitable for outdoor applications, marine environments, and chemically reactive environments | Good corrosion resistance, but may require additional protective measures in highly corrosive environments |
Machinability | Excellent machinability, allowing for precise cutting, drilling, and milling operations, making it easy to fabricate and modify | Good machinability, but slightly less machinable than aluminum, requiring more effort for precise machining |
Cost | Generally higher cost than extruded steel tubes due to the higher production cost of aluminum | Generally lower cost than extruded aluminum tubes, making it a more economical option for cost-sensitive applications |
Environmental impact | Environmentally friendly and recyclable, with over 70% of all aluminum ever produced still in use today, reducing the environmental footprint | Less environmentally friendly than aluminum, with a higher energy requirement for production and a larger carbon footprint |
Detailed Applications of Extruded Aluminum Tubes
Extruded aluminum tubes find applications in a diverse range of industries, including:
Aerospace industry
- Aircraft structural components: Aluminum’s lightweight and high strength-to-weight ratio make it an ideal material for aircraft structural components, including fuselage frames, wing spars, and landing gear struts.
- Wing skins: Aluminum’s smooth surface and corrosion resistance make it suitable for wing skins, contributing to aerodynamic efficiency and durability.
- Landing gear: Aluminum’s lightweight and strength make it a preferred choice for landing gear components, ensuring safe and reliable landings.
- Fuel lines: Aluminum’s corrosion resistance and lightweight properties make it suitable for fuel lines, ensuring the safe transfer of fuel throughout the aircraft.
- Heat sinks: Aluminum’s excellent thermal conductivity makes it an effective material for heat sinks, efficiently dissipating heat generated by electronic components.
Automotive industry
- Automotive frames: Aluminum’s lightweight and high strength-to-weight ratio make it an ideal material for automotive frames, contributing to fuel efficiency and improved performance.
- Body panels: Aluminum’s lightweight, corrosion resistance, and formability make it suitable for body panels, enhancing vehicle aesthetics and weight reduction.
- Bumpers: Aluminum’s impact-absorbing properties and lightweight nature make it a preferred choice for bumpers, providing protection while minimizing weight.
- Wheels: Aluminum’s lightweight and strength make it an excellent material for wheels, enhancing vehicle performance and reducing unsprung weight.
- Engine components: Aluminum’s heat dissipation properties and lightweight make it suitable for engine components, such as cylinder heads, intake manifolds, and pistons.
Construction industry
- Curtain walls: Aluminum’s lightweight, corrosion resistance, and aesthetic appeal make it a preferred choice for curtain walls, providing a modern and durable exterior for buildings.
- Window frames: Aluminum’s lightweight, corrosion resistance, and formability make it suitable for window frames, offering energy efficiency and aesthetic design flexibility.
- Handrails: Aluminum’s lightweight, corrosion resistance, and aesthetic appearance make it an excellent material for handrails, providing safety and visual appeal.
- Scaffolding: Aluminum’s lightweight and strength make it a suitable material for scaffolding, providing a safe and portable work platform for construction activities.
- Architectural elements: Aluminum’s versatility and aesthetic appeal make it a popular choice for architectural elements, such as cladding panels, decorative accents, and roofing systems.
Electrical and electronics industry
- Electrical enclosures: Aluminum’s lightweight, corrosion resistance, and electromagnetic shielding properties make it suitable for electrical enclosures, protecting sensitive electronic components.
- Heat sinks: Aluminum’s excellent thermal conductivity makes it an effective material for heat sinks, efficiently dissipating heat generated by electronic components.
- Busbars: Aluminum’s lightweight and high conductivity make it a preferred choice for busbars, ensuring efficient power distribution in electrical systems.
- Wiring conduits: Aluminum’s lightweight, corrosion resistance, and ease of installation make it suitable for wiring conduits, providing a safe and efficient way to route electrical cables.
Medical industry
- Medical devices: Aluminum’s lightweight, biocompatibility, and strength make it suitable for medical devices, such as wheelchairs, crutches, and prosthetics.
- Surgical instruments: Aluminum’s lightweight, precision machining capabilities, and sterilizability make it an excellent material for surgical instruments, ensuring accuracy and sterility.
- Packaging: Aluminum’s versatility and barrier properties make it suitable for medical packaging, providing protection for sterile products and preventing contamination.
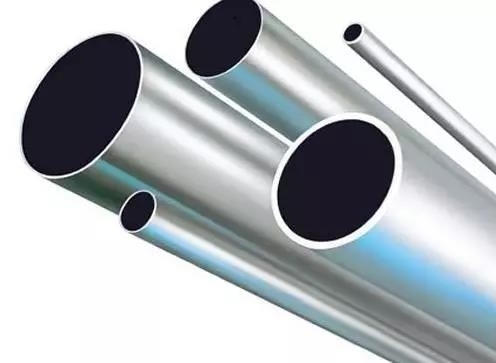
Detailed Applications of Extruded Steel Tubes
Extruded steel tubes are widely used in various applications, including:
Structural components
- Building frames: Steel’s exceptional strength and fire resistance make it an ideal material for building frames, providing support for skyscrapers, bridges, and other large structures.
- Towers: Steel’s high strength-to-weight ratio and ability to withstand heavy loads make it suitable for towers, such as communication towers, wind turbines, and transmission towers.
- Machinery supports: Steel’s exceptional strength and durability make it an excellent material for machinery supports, ensuring the stability and load-bearing capacity of heavy machinery.
Pressure vessels
- Chemical storage tanks: Steel’s high strength and resistance to corrosion make it suitable for chemical storage tanks, ensuring safe containment and protection against hazardous chemicals.
- Hydraulic cylinders: Steel’s high strength and ability to withstand high pressures make it an essential material for hydraulic cylinders, providing the power for hydraulic machinery.
- Pressure pipes: Steel’s strength, durability, and ability to withstand high pressures make it suitable for pressure pipes, conveying fluids in various industrial and commercial applications.
Piping and tubing systems
- Plumbing systems: Steel’s durability and corrosion resistance make it a reliable choice for plumbing systems, ensuring the safe conveyance of water and wastewater.
- HVAC ducts: Steel’s strength and ability to withstand pressure make it suitable for HVAC ducts, transporting air for heating, ventilation, and air conditioning systems.
- Industrial piping systems: Steel’s strength, durability, and availability in various sizes and shapes make it a versatile choice for industrial piping systems, transporting fluids in various industrial processes.
Automotive frames
- Chassis components: Steel’s exceptional strength and ability to withstand impact make it an ideal material for chassis components, providing the structural integrity of cars, trucks, and other vehicles.
- Roll cages: Steel’s high strength and ability to protect occupants in case of rollovers make it an essential component of roll cages in racing cars and other vehicles.
- Suspension components: Steel’s strength and durability make it suitable for suspension components, ensuring smooth and safe handling of vehicles.
Construction machinery
- Bulldozer frames: Steel’s exceptional strength and ability to withstand heavy loads make it an ideal material for bulldozer frames, providing the structural support for earth-moving equipment.
- Excavator booms: Steel’s high strength and durability make it suitable for excavator booms, ensuring the power and stability needed for digging and lifting tasks.
- Crane structures: Steel’s exceptional strength and ability to withstand heavy loads make it an essential material for crane structures, providing the support for lifting heavy objects.
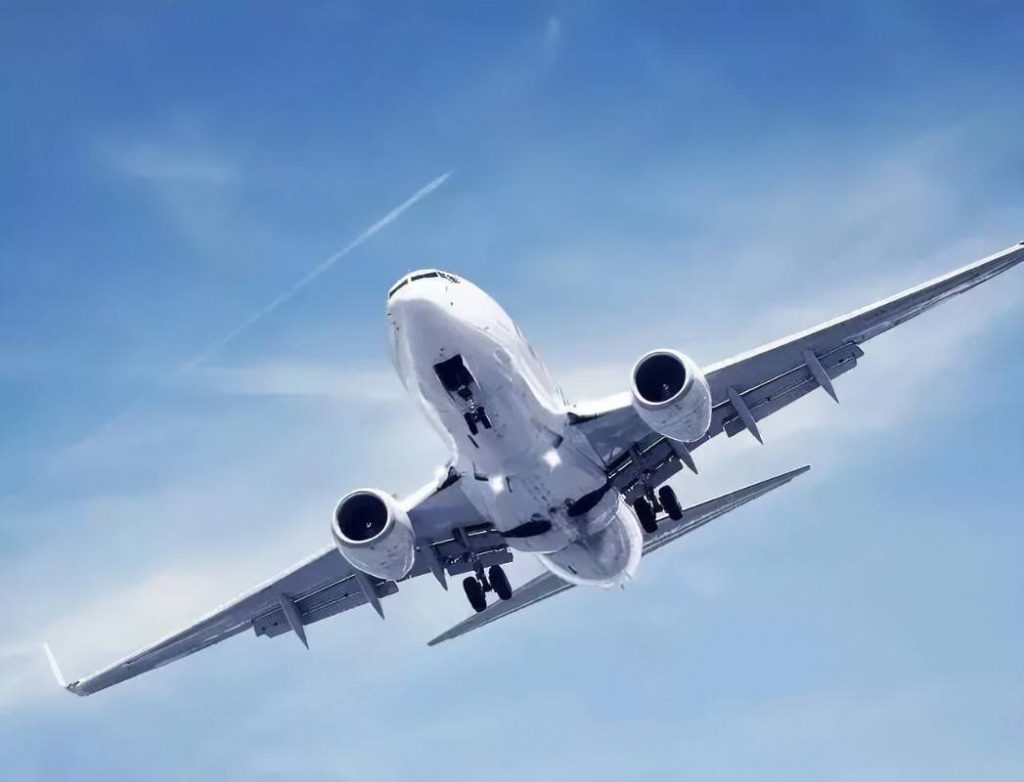
In conclusion, extruded aluminum tubes and extruded steel tubes offer unique advantages and disadvantages that make them suitable for specific applications. Extruded aluminum tubes excel in applications requiring lightweight, corrosion resistance, and machinability, while extruded steel tubes are preferred in applications demanding exceptional strength, weldability, and affordability. By carefully considering the specific requirements of each application, engineers and designers can make informed decisions to select the most appropriate material for their projects.