Aluminium finned tube heat exchangers are widely used in industries such as HVAC, refrigeration, and power generation due to their excellent heat transfer properties and lightweight design. However, their efficiency can be affected by a variety of factors, ranging from material properties to operational conditions. A deep understanding of the factors that affect their heat transfer efficiency can help optimize the design, improve performance, and reduce costs.
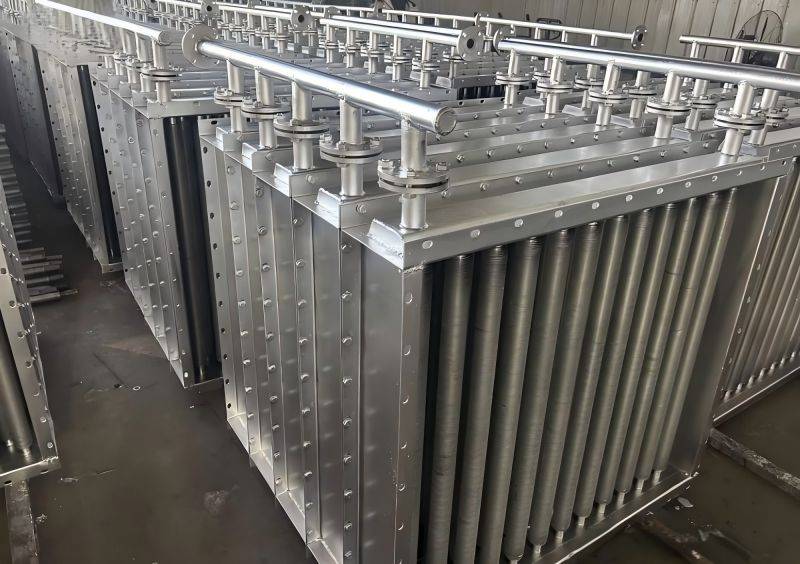
Factor 1: Material Properties
The material properties of aluminium and its alloys are fundamental to the heat transfer efficiency of finned tube heat exchangers. These properties determine how effectively heat is conducted and dissipated throughout the exchanger.
- Thermal Conductivity: Aluminium is known for its high thermal conductivity, typically around 205 W/m·K, which allows for rapid heat transfer. However, impurities or coatings added during manufacturing can reduce this property, impacting efficiency.
- Corrosion Resistance: Aluminium’s natural oxide layer offers some corrosion resistance. However, prolonged exposure to moisture or harsh chemicals can degrade this layer, creating insulating deposits that hinder heat transfer.
Selecting high-quality aluminium with minimal impurities and ensuring proper surface treatments can help maintain optimal thermal conductivity and corrosion resistance, maximizing heat transfer efficiency.
Factor 2: Aluminium Fin Design
The design and configuration of fins play a critical role in enhancing the heat exchange process. Fins increase the surface area available for heat dissipation, but their design must strike a balance between performance and practicality.
- Fin Spacing: A closer fin space translates to a larger surface area for heat exchange, potentially leading to improved performance. However, too closer fin space can obstruct airflow, increasing pressure drop and hindering overall heat transfer. The optimal fin density requires careful consideration of the specific application and operating conditions.
- Fin Thickness: While thicker fins offer a larger conduction path for heat transfer within the fin itself, they can also increase the thermal resistance within the fin material. This is because thicker fins have a greater distance for heat to travel from the base to the tip. An appropriate fin thickness must be chosen to balance these competing factors.
- Fin Shape: The shape of the fins significantly influences airflow patterns and heat transfer rates. Louvered fins, for instance, create turbulence in the airflow, enhancing heat transfer. Plate fins, on the other hand, offer a simpler geometry but may have lower heat transfer coefficients compared to more complex shapes.
By optimizing fin design for specific applications and environments, heat exchangers can achieve improved performance while minimizing maintenance challenges.
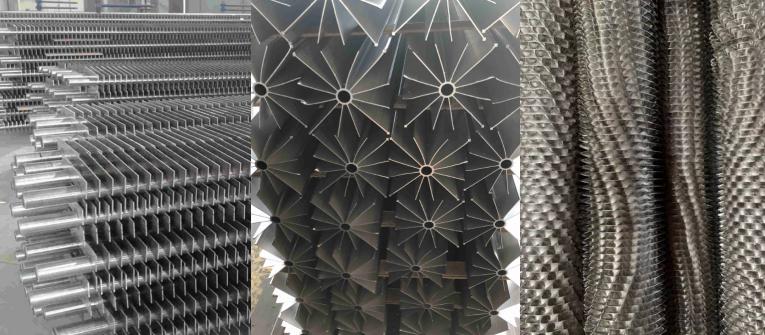
Factor 3: Aluminium Tube Characteristics
The choice of tube material and its dimensions significantly influence heat transfer performance.
- Tube Material: Aluminium tubes are preferred for their lightweight and high thermal conductivity. Variations in alloy composition can also affect performance.
- Tube Diameter and Wall Thickness: The tube diameter and wall thickness affect the internal fluid flow and the available heat transfer area. Smaller tube diameters can enhance heat transfer by increasing the surface area per unit volume. However, excessively small diameters can increase pressure drop and make cleaning more difficult. The tube wall thickness also plays a role, with thinner walls generally offering lower thermal resistance.
Careful consideration of tube dimensions and materials ensures efficient heat conduction while maintaining the structural integrity of the heat exchanger.
Factor 4: Fluid Flow Characteristics
The characteristics of the fluid flowing through the heat exchanger exert a significant influence on heat transfer efficiency.
- Flow Rate: Increasing the fluid flow rate generally enhances heat transfer. Higher flow rates reduce the boundary layer thickness, which is the region near the heat transfer surface where fluid velocity is significantly reduced due to viscous forces. A thinner boundary layer allows for more efficient heat transfer between the fluid and the heat exchanger surface.
- Fluid Properties: The physical properties of the fluid, such as viscosity, thermal conductivity, and specific heat, directly impact heat transfer. Fluids with higher thermal conductivity and lower viscosity generally exhibit better heat transfer performance.
- Flow Distribution: Even fluid distribution across the heat exchanger is essential for maximizing heat transfer efficiency. Uneven flow can lead to localized hot spots or cold spots, reducing the overall heat transfer effectiveness. Proper baffling and flow distribution techniques are crucial for ensuring uniform flow across the heat exchanger surface.
Optimizing flow rate, fluid properties, and flow distribution helps achieve better heat transfer rates while maintaining energy efficiency and operational stability.
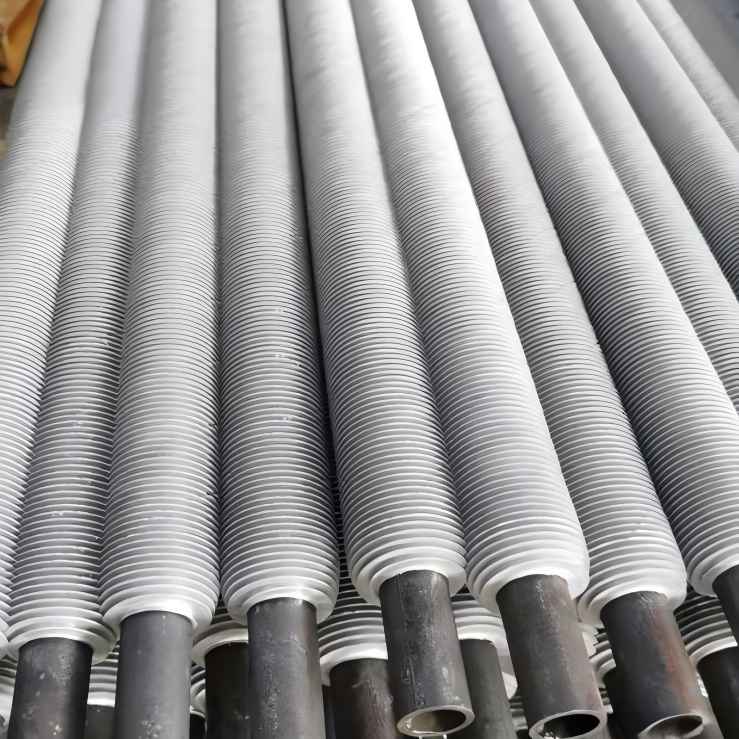
Factor 5: Operating Conditions
Operating conditions, such as temperature differences and pressure, have a significant impact on heat transfer performance.
- Temperature Difference: The greater the temperature gradient between the working fluid and the air, the more efficient the heat transfer. However, excessive gradients can lead to thermal stresses.
- Pressure: Higher pressures can improve fluid velocity within the tubes, enhancing heat transfer. However, extreme pressures may risk structural damage.
Maintaining optimal temperature and pressure conditions ensures consistent performance and prevents unnecessary wear and tear on the system.
Factor 6: Environmental Factors
The environment in which the heat exchanger operates can significantly influence its efficiency by affecting both airflow and material integrity.
- Fouling and Dust Accumulation: Fouling occurs when impurities in the fluid, such as dust, particles, or scale, adhere to the heat transfer surfaces. This buildup creates an insulating layer that increases thermal resistance, hindering heat transfer. Regular cleaning and filtration systems can mitigate this issue.
- Humidity: High humidity levels may cause condensation on the fins, leading to corrosion or the formation of frost in cold environments.
Regular maintenance and environmental control measures are essential for preserving the efficiency and lifespan of aluminium finned tube heat exchangers.
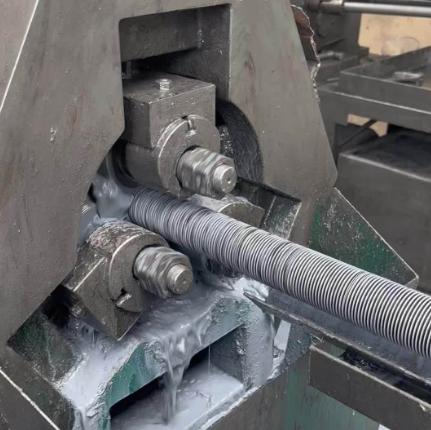
Factor 7: Manufacturing Quality
The quality of manufacturing processes directly affects the performance and durability of heat exchangers.
- Joint Integrity: Proper bonding between fins and tubes ensures effective thermal conduction. Poorly soldered or mechanically bonded joints create thermal resistance.
- Surface Smoothness: Smooth surfaces inside the tubes and on the fins minimize resistance to heat flow and fluid dynamics.
- Manufacturing Tolerances: Inconsistent fin dimensions and spacing can disrupt airflow patterns and reduce heat transfer effectiveness. Precise manufacturing tolerances are crucial for ensuring consistent and reliable performance.
Investing in high-quality manufacturing processes ensures reliable performance and reduces the likelihood of efficiency losses over time.
Final Thoughts
Heat transfer efficiency in aluminium finned tube heat exchangers is influenced by a combination of material properties, design considerations, operating conditions, and maintenance practices. When designing, manufacturing, and using aluminum finned tube heat exchangers, these factors need to be fully considered. By optimizing the design, improving the manufacturing quality, reasonably controlling the operating conditions, and doing a good job of maintenance, the heat transfer efficiency of the heat exchanger can be improved, thereby achieving better performance, and reducing energy consumption and operating costs.