Al-Al composite tubes (composite aluminum tubes) are a unique class of materials gaining significant traction across various industries. These tubes are formed by combining two or more aluminum alloys through specialized processes, resulting in a composite with properties exceeding those of individual alloys. One crucial application of composite aluminum tubes lies in condenser header pipes, which play a vital role in heat exchange systems. Since these pipes are subjected to repeated cycles of pressure and temperature changes during operation, fatigue performance becomes a critical factor in ensuring their long-term durability and reliability.
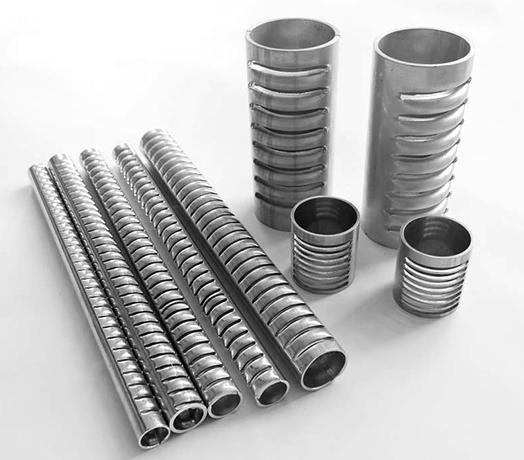
Fatigue Performance Research of Composite Aluminum Tubes
The fatigue properties of composite aluminum tubes have been extensively studied to ensure that they are suitable for applications such as condenser header pipes that need to undergo repeated stress cycles. The following is a breakdown of the main research areas:
- Fatigue Life Testing: This method involves subjecting the composite aluminum tube to repeated cyclic loading in a laboratory setting until it fractures. The number of cycles endured before failure determines the fatigue life of the tube. This data is crucial for predicting the lifespan of condenser header pipes under real-world operating conditions.
- Fatigue Strength Testing: This test measures the maximum stress a composite aluminum tube can withstand when subjected to an infinite number of loading cycles. The fatigue strength value helps engineers understand the material’s reliability in condenser header pipes enduring sustained pressure fluctuations.
- Fatigue Crack Propagation Behavior: Researchers investigate how cracks develop and propagate within the composite aluminum tube material during fatigue loading. Understanding this behavior allows for the development of strategies to prevent and manage crack growth, enhancing the overall lifespan of condenser header pipes.
- Analysis of Influencing Factors: Various factors can influence the fatigue performance of composite aluminum tubes. Researchers analyze the impact of factors such as the specific alloy combination used in the composite, the manufacturing process, the thickness of the individual layers, and the presence of any surface imperfections. This analysis helps optimize the design and production of composite aluminum tubes for condenser header applications, maximizing their fatigue resistance.
- Fatigue Life Prediction Models: Developing accurate fatigue life prediction models is a crucial area of research. These models often leverage concepts like Continuum Damage Mechanics (CDM) theory and machine learning algorithms like Support Vector Machines (SVM). By incorporating data from fatigue life and fatigue strength testing, these models can predict the lifespan of composite aluminum tubes in condenser header pipes with greater accuracy, enabling proactive maintenance strategies.
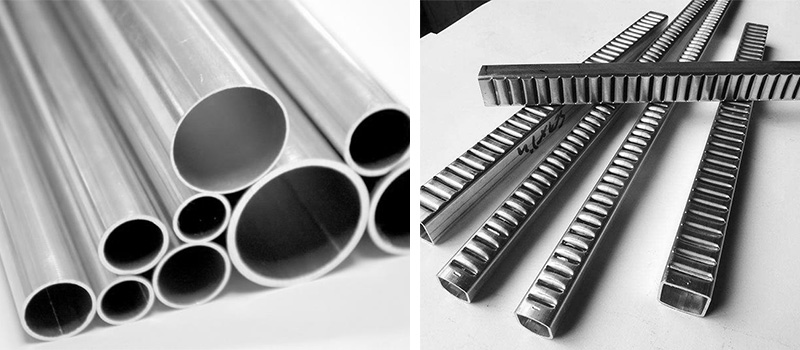
Latest Research Findings
The field of fatigue performance of composite aluminum pipes is constantly developing, and new research results are constantly emerging. Here are some noteworthy latest developments:
- Digital Image Processing and Corrosion Analysis: Researchers have employed digital image processing techniques to analyze the corrosion morphology of pre-corroded aluminum alloy specimens. This analysis has led to the development of prediction models linking corrosion time and fatigue life. This information is particularly valuable for condenser header pipes operating in environments prone to corrosion.
- Pre-corrosion and Multiaxial Fatigue Behavior: Studies have shown that pre-corrosion and alternating corrosion have a significant impact on the multiaxial fatigue behavior of 7075 aluminum alloy (a commonly used material in composite aluminum pipes). This discovery provides valuable insights into optimizing the fatigue resistance of condenser headers exposed to corrosive environments and complex stress conditions.
These advances highlight the continuous efforts to improve the understanding and prediction of the fatigue performance of composite aluminum tubes, paving the way for more efficient and reliable utilization of them in condenser header pipe applications.
Applications of Al-Al Composite Tubes in Various Fields
The exceptional combination of properties offered by composite aluminum tubes makes them highly attractive for a wide range of applications across diverse industries:
- Aerospace: Composite aluminum tubes are lightweight and high-strength, making them an ideal choice for aircraft and rocket structural components. They are used in fuel pipelines and hydraulic systems, where reducing weight and withstanding harsh operating conditions are crucial.
- Construction engineering: Composite aluminum pipes provide a feasible alternative to traditional piping systems in buildings. Due to their corrosion resistance, strength, and compatibility with various building materials, they are used in water pipes, air conditioning systems, and gas delivery.
- Automotive manufacturing: The automotive industry uses composite aluminum tubes in key components such as radiators, air conditioning systems, and fuel delivery systems. Their lightweight construction helps improve fuel efficiency, while their excellent thermal conductivity helps heat sinks efficiently dissipate heat, which improves overall engine performance. In addition, their corrosion resistance ensures extended service life in harsh automotive environments.
- Industrial applications: Composite aluminum tubes are used for conveying liquids and gases in various industrial environments. Applications include seawater desalination plants, whose corrosion resistance is crucial for resisting harsh saline environments. In addition, due to their light weight and ability to withstand high voltage, they are also used in communication equipment and rail transit systems.
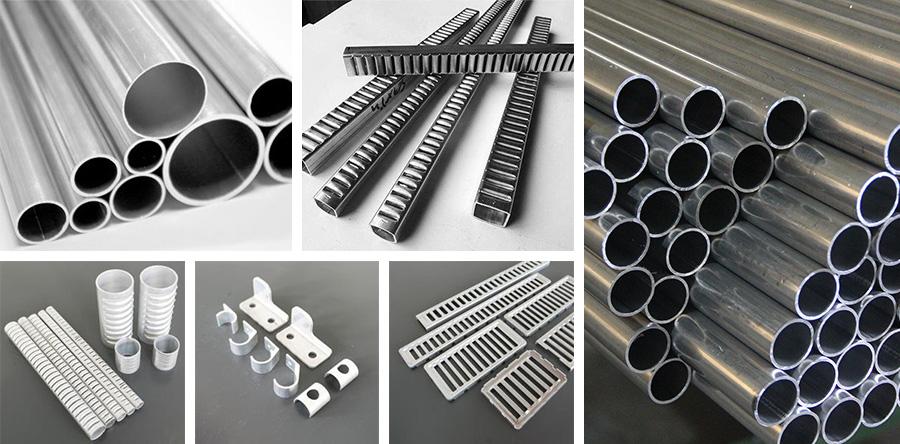
Conclusion
Al-Al composite tubes represent a promising material solution for various applications due to their unique combination of properties and performance advantages. Extensive research efforts are continuously improving the understanding of their fatigue performance, paving the way for further optimization and broader application. Their lightweight construction, high strength, excellent corrosion resistance, and efficient thermal conductivity make them ideal candidates for demanding applications across industries, including critical components like condenser header pipes in power plants. As research and development progress, composite aluminum tubes are poised to play an increasingly significant role in the construction of lighter, more durable, and energy-efficient structures and systems.