In the realm of metals, aluminum stands out for its lightweight, corrosion resistance, and malleability, making it a versatile material for diverse applications. Among the numerous alloys available, 1060 and 6061 are two commonly utilized aluminum sheets. Understanding the compositional distinctions and application areas of these alloys is crucial for informed decision-making in material selection.
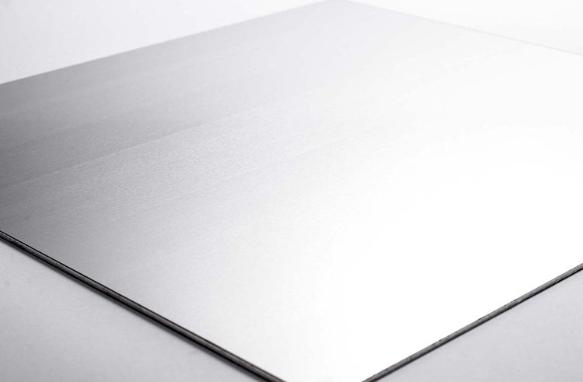
Composition Insights of 1060 Aluminum vs 6061
The fundamental difference between 1060 and 6061 aluminum sheets lies in their chemical compositions.
1060 aluminum, also known as commercially pure aluminum, boasts a minimal alloying content of 99.6% or higher. This makes it one of the softest and most ductile aluminum alloys. The absence of other significant alloying elements gives 1060 excellent corrosion resistance and high thermal and electrical conductivity. However, its low strength makes it less suitable for applications requiring structural integrity under heavy loads.
In contrast, 6061 aluminum incorporates additional alloying elements, primarily magnesium and silicon, to enhance its mechanical properties. This combination imparts excellent strength, corrosion resistance, and weldability to 6061. It can be easily machined and formed, making it a popular choice for structural components and high-stress applications. However, the increased alloying content slightly reduces its formability compared to 1060 aluminum.
Mechanical Properties of 1060 Aluminum vs 6061
The compositional variations between 1060 and 6061 aluminum translate into distinct physical and mechanical properties.
1060 Aluminum Sheet:
Due to its pure aluminum composition, 1060 is relatively soft with low tensile strength, typically ranging from 12 to 18 ksi (kilopounds per square inch). However, this alloy excels in ductility, allowing it to undergo significant deformation without fracturing. It is well-suited for applications where flexibility and formability are essential, such as in the manufacturing of kitchen utensils, reflectors, and decorative elements. However, it may not be suitable for applications requiring high strength or hardness.
6061 Aluminum Sheet:
6061 aluminum’s alloying elements bolster its tensile strength, reaching values between 25 and 35 ksi. It offers a balanced combination of strength and machinability. Its mechanical properties can be significantly enhanced through heat treatment, making it ideal for aerospace components, marine fittings, and structural parts in various industries. Its versatility and strength make it a go-to choice for applications demanding durability. Additionally, 6061 aluminum exhibits improved hardness and wear resistance compared to 1060 aluminum.
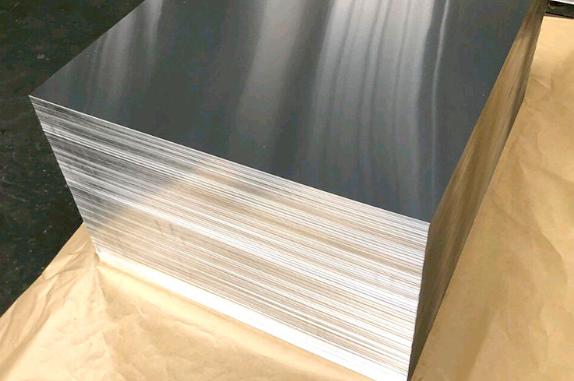
Applications of 1060 Aluminum vs 6061
The distinct properties of 1060 and 6061 aluminum sheets dictate their suitability for specific applications.
1060 Aluminum Sheet Applications:
1060 aluminum’s exceptional formability and low strength make it ideal for applications that require intricate shapes and minimal structural loads, such as decorative elements, food packaging, and electrical components. Such as:
- Reflectors and lighting fixtures
- Insulation jackets
- Kitchen utensils
- Decorative elements
- Chemical process equipment
6061 Aluminum Sheet Applications:
6061 aluminum’s superior strength and hardness broaden its application range to include structural components, automotive parts, aerospace components, and marine structures. Its ability to withstand higher stresses and maintain dimensional stability under demanding conditions makes it a preferred choice in these applications. Such as:
- Aircraft parts
- Marine fittings
- Bicycle frames
- Automotive components
- Structural components in construction
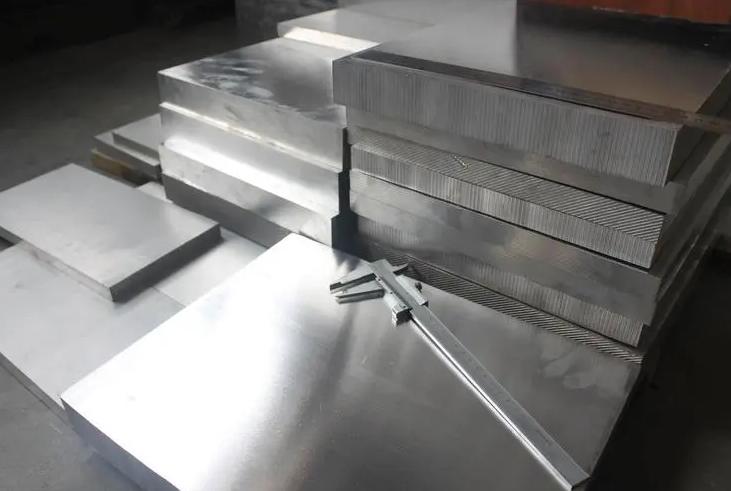
Conclusion
In decoding the differences between 1060 and 6061 aluminum sheets, it becomes clear that each alloy has distinct advantages based on its composition and mechanical properties. While the 1060 is prized for its formability and corrosion resistance, the 6061 stands out for its strength and versatility in demanding applications.
Choosing between 1060 and 6061 aluminum sheets ultimately depends on the specific requirements of the intended application. Whether it’s a decorative element, a structural component, or a high-stress aerospace part, understanding the nuances of these alloys empowers engineers and manufacturers to select the most suitable material for their projects, ensuring optimal performance and longevity.