In today’s visually-driven world, surface aesthetics play a pivotal role in capturing attention and making a lasting impression. Whether it’s the sleek exterior of a car, the modern facade of a building, or the luxurious finish of a consumer product, the appearance of surfaces matters. One key ingredient that has been revolutionizing the way surfaces are transformed is aluminum pigment paste. In this article, we delve into the world of aluminum pigment paste, exploring its properties, applications, and transformative potential in turning dull surfaces into dazzling ones.
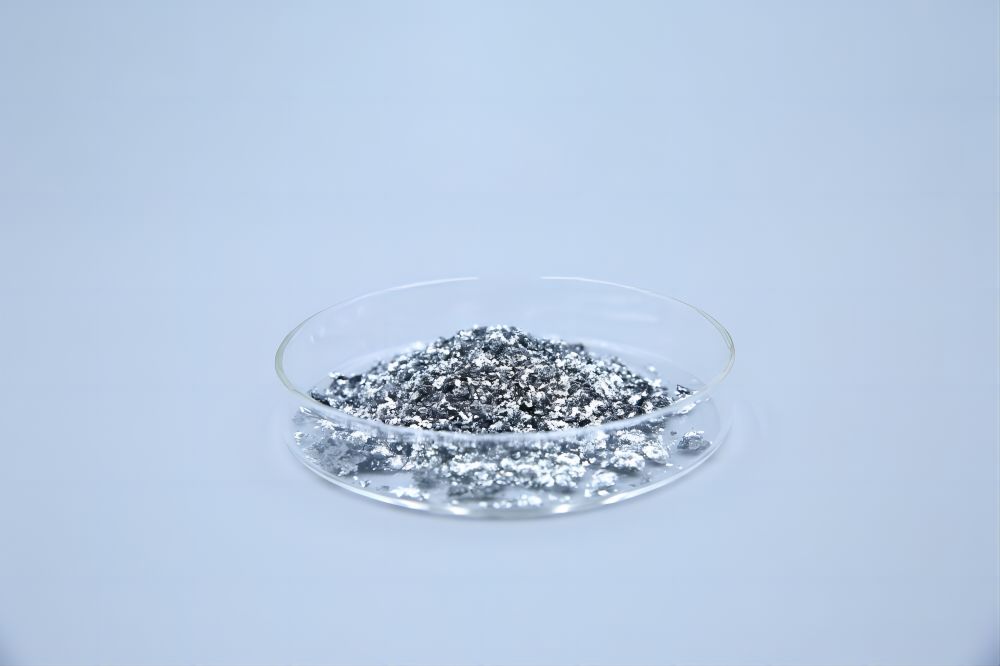
What is Aluminum Pigment Paste?
Aluminum pigment paste is a specialized material used in various industries for imparting metallic effects to surfaces. It consists of finely ground aluminum particles suspended in a binder or carrier fluid, forming a paste-like consistency. The unique properties of aluminum pigment paste make it a versatile and effective choice for achieving a wide range of visual effects on different substrates.
Composition:
The primary component of aluminum pigment paste is aluminum powder, which is typically derived from high-purity aluminum sources. The aluminum particles are finely milled to achieve specific particle sizes and shapes, which play a crucial role in determining the appearance and performance of the final coating. The size and shape of the aluminum particles can vary, with common shapes including flakes, granules, or spherical particles.
The aluminum particles are suspended in a binder or carrier fluid, which helps to stabilize the pigment and facilitate its application onto various surfaces. The choice of binder can vary depending on the intended application and desired properties of the final coating. Common binders used in aluminum pigment paste include acrylic resins, epoxy resins, polyurethanes, and solvent-based carriers.
Types of Aluminum Pigment Paste
Aluminum pigment paste can be classified based on several factors including particle shape, size, and application. Here are the primary classifications:
Particle Shape:
- Flake Aluminum Pigment Paste: Flake aluminum pigment paste contains flat, platelet-shaped aluminum particles. These flakes create a reflective surface when applied, resulting in a bold metallic effect with high brilliance and reflectivity. Flake aluminum pigment paste is commonly used in applications where a striking metallic appearance is desired, such as automotive coatings, architectural finishes, and consumer products.
- Spherical Aluminum Pigment Paste: Spherical aluminum pigment paste contains aluminum particles with a spherical or rounded shape. These spherical particles produce a smoother, more uniform appearance compared to flake pigments. Spherical aluminum pigment paste is often used in applications where a subtle metallic effect is desired, such as in industrial coatings and printing inks.
Particle Size:
Aluminum pigment paste can also be classified based on the particle size distribution of the aluminum particles. Particle size influences the visual appearance and performance of the final coating. Smaller particle sizes typically result in smoother finishes with better coverage, while larger particles may produce a more textured or sparkly effect.
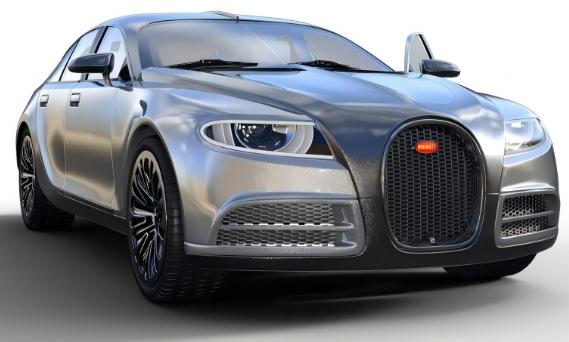
Application:
Aluminum pigment paste can be classified based on its intended application or industry use. Common applications include:
- Automotive Coatings: Aluminum pigment paste is widely used in automotive coatings to create metallic finishes on car exteriors and parts. These coatings enhance the visual appeal of vehicles and provide protection against corrosion and abrasion.
- Architectural Finishes: Aluminum pigment paste is used in architectural coatings to add decorative metallic effects to building facades, window frames, and interior surfaces. These coatings can range from subtle pearlescent finishes to bold metallic accents, depending on the design aesthetic.
- Consumer Products: Aluminum pigment paste is incorporated into various consumer products such as cosmetics, packaging materials, and electronics to enhance their visual appearance. Metallic finishes add a touch of luxury and sophistication to these products, making them more attractive to consumers.
- Industrial Coatings: Aluminum pigment paste is utilized in industrial coatings for applications such as metal furniture, machinery, and appliances. These coatings provide both decorative appeal and functional benefits such as corrosion resistance and durability.
By understanding these classifications, you can select the most suitable type of aluminum pigment paste for their specific application requirements, ensuring optimal performance and aesthetic results.
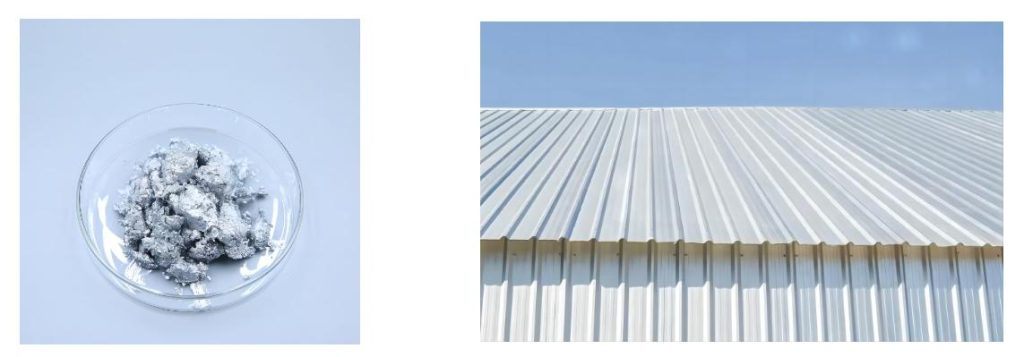
How to Transforming Surfaces with Aluminum Pigment Paste?
Transforming surfaces with aluminum pigment paste involves several key steps to ensure optimal adhesion, coverage, and visual impact. Here’s a detailed guide on how to effectively use aluminum pigment paste to achieve stunning surface transformations:
1. Surface Preparation:
Before applying aluminum pigment paste, proper surface preparation is essential to ensure adhesion and durability of the coating. Follow these steps to prepare the surface:
- Clean the Surface: Remove any dirt, dust, grease, or other contaminants from the surface using a suitable cleaner or solvent. Ensure that the surface is completely clean and free from residues.
- Sand or Prime (if necessary): Depending on the substrate material and condition, sanding or priming may be necessary to promote adhesion. Use sandpaper or a suitable primer to create a smooth, uniform surface for the pigment paste application.
2. Methods of Application:
Aluminum pigment paste can be applied using various methods, each offering distinct advantages depending on the surface area, desired finish, and application environment. Common application methods include:
- Brushing: Use a brush to apply the aluminum pigment paste onto the surface in smooth, even strokes. This method is suitable for small to medium-sized areas and allows for precise control over the thickness of the coating.
- Spraying: Utilize a spray gun or airbrush to apply the aluminum pigment paste onto the surface. Spraying is ideal for covering large surface areas quickly and evenly, and it provides a uniform coating thickness. Adjust the spray pattern and pressure to achieve the desired coverage and finish.
- Roller Coating: Apply the aluminum pigment paste with a paint roller for fast and efficient coverage of large surfaces. Use a high-quality roller suitable for the type of substrate and ensure that the paste is applied evenly to avoid streaks or unevenness.
3. Tips for Achieving Desired Effects:
To maximize the visual impact of aluminum pigment paste and achieve the desired surface transformation, consider the following tips:
- Adjust Pigment Concentration: Experiment with different concentrations of aluminum pigment paste to achieve the desired level of brilliance, reflectivity, and color intensity. Higher concentrations will result in a more pronounced metallic effect.
- Control Application Thickness: Pay attention to the thickness of the coating during application to achieve uniform coverage and avoid runs or drips. Apply multiple thin coats rather than a single thick coat for better adhesion and durability.
- Ensure Proper Drying: Allow sufficient drying time between coats and after the final application to ensure proper curing and adhesion of the aluminum pigment paste. Follow the manufacturer’s recommendations for drying times and environmental conditions (temperature, humidity, etc.).
By following these steps and tips, you can effectively transform surfaces with aluminum pigment paste, creating stunning metallic finishes that enhance the visual appeal of various products and structures. Experiment with different application methods and techniques to achieve the desired aesthetic effects and bring your creative vision to life.
Conclusion
Overall, aluminum pigment paste offers a versatile and effective solution for enhancing surface aesthetics in various applications. Its ability to impart metallic effects, combined with its ease of application and compatibility with different substrates, makes it a popular choice for designers, manufacturers, and coating applicators seeking to transform surfaces from dull to dazzling.