The metallographic structure of aluminum die casting is coarser than that of deformed aluminum alloy, so it is also different during heat treatment. The former has a long holding time, generally more than 2h, while the latter has a short holding time, only tens of minutes. Because of the metallographic structure of metal mold castings and low-pressure castings, the metallographic structure of aluminium die casting is coarser than that of deformed aluminum alloys, so it is also different during heat treatment.
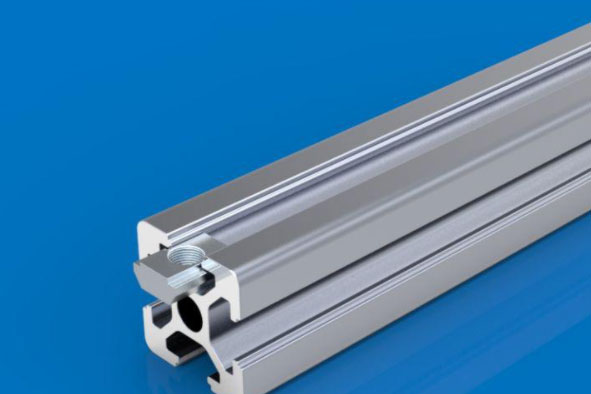
What is the Purpose of Heat Treatment?
The purpose of heat treatment of aluminum die castings is to improve mechanical properties and corrosion resistance, stabilize dimensions, and improve machining properties such as cutting and welding. Because the mechanical properties of many as-cast aluminium alloys cannot meet the requirements for use.
Methods of Heat Treatment
- Annealing
The function of annealing treatment is to eliminate the casting stress of the casting and the internal stress caused by machining, stabilize the shape and size of the workpiece, and spheroid part of the Si crystal of the Al-Si alloy, and improve the plasticity of the alloy.
- Quenching
Quenching is to heat the aluminum casting to a higher temperature and keep it for more than 2 hours to fully dissolve the soluble phase in the alloy. Then, it is rapidly quenched into water at 60-100°C to rapidly cool the casting, so that the strengthening components can be dissolved in the alloy to the maximum extent and stored at room temperature.
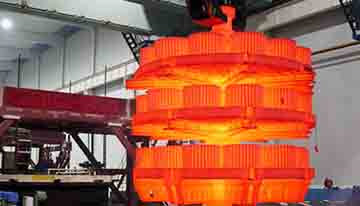
- Aging treatment
Aging treatment, also known as low-temperature tempering, is a process in which the quenched aluminium castings are heated to a certain temperature, held for a certain period of time, and air-cooled until room temperature, so that the supersaturated solid solution is decomposed and the alloy matrix is stabilized.
- Loop processing
Cool the aluminum casting to a certain temperature below zero (such as -50°C, -70°C, -195°C) and keep it for a certain period of time, and then heat the casting to below 350°C, so that the medium solid solution lattice of the alloy shrinks and expands repeatedly. And make the crystal grains of each phase shift a little, so that the atomic segregation zone and the particles of the intermetallic compound in the solid solution crystal lattice are in a more stable state, and the purpose of improving the size and volume of the product parts is achieved.
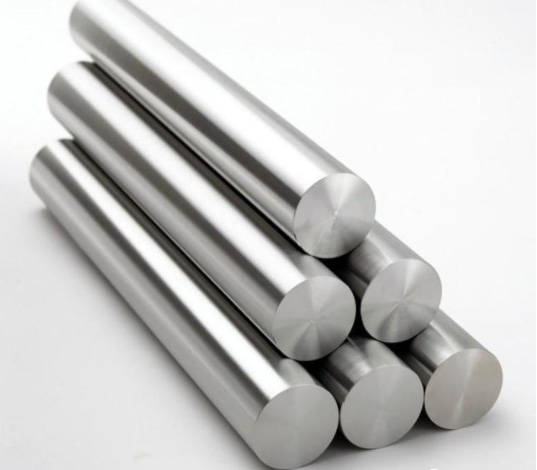
Heat Treatment Equipment and Materials
1. Main technical requirements of heat treatment equipment
(1) Since the temperature difference between quenching and aging of aluminum alloy is not large (because the quenching temperature is close to the melting point of the low-melting eutectic component in the alloy), the temperature difference in the furnace should be controlled within ±5°C;
(2) The temperature measurement and temperature control instruments are required to be sensitive and accurate to ensure that the temperature is within the above error range.
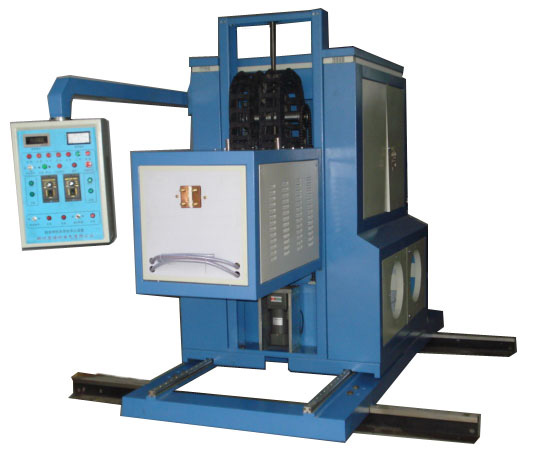
(3) The temperature of each zone in the furnace should be uniform, and the difference should be within the range of 1-2°C.
(4) The quenching tank has a heating device and a circulation device to ensure that the heating and temperature of the water are uniforms.
(5) Contaminated cooling water should be checked and replaced regularly.
2. Quenching medium
Quenching medium is an important factor to ensure the realization of various heat treatment purposes or functions. The higher the cooling rate of the quenching medium, the more intense (fast) the cooling of the casting, the higher the degree of supersaturation of the α solid solution in the metal structure, and the better the mechanical properties of the casting, because a large number of strengthening phases such as intermetallic compounds are solid-dissolved into the α solid solution of Al.
3. Temperature measurement, temperature control instruments and materials
The accuracy of temperature measurement and temperature control instruments should not be lower than 0.5. The heat treatment furnace should be equipped with automatic recording, automatic alarm, automatic power-off, and power-recovery devices and instruments that can automatically measure and control the temperature to ensure the temperature in the furnace. Accurate display and control and uniform temperature.