Aluminium wires play a crucial role in various industries, ranging from electrical power distribution to construction and automotive applications. Its lightweight, high conductivity and excellent corrosion resistance make it an ideal choice for numerous applications. But how exactly are these wires made? This article takes you through the journey of aluminium wires, from raw material sourcing and preparation to the finished product.

Raw Material Sourcing and Preparation
The journey of aluminum wire begins with bauxite, the primary ore of aluminum. This reddish-brown mineral, rich in aluminum oxide, is mined from the earth’s crust. The subsequent steps need to undergo significant processing to transform into the pure and versatile form used in wire manufacturing.
Common Aluminum Alloys for Making Aluminum Wire
While pure aluminum can be used, most aluminum wires are produced from alloys. These alloys enhance specific properties such as strength, conductivity, and corrosion resistance. Common alloys include:
- Aluminum-Copper Alloys (e.g., 1xxx, 2xxx series): Known for their high strength and good conductivity, these alloys are widely used in electrical transmission lines and construction applications.
- Aluminum-Silicon Alloys (e.g., 4xxx series): These alloys exhibit excellent castability and weldability, making them suitable for applications requiring complex shapes.
- Aluminum-Magnesium Alloys (e.g., 5xxx series): These alloys offer a good balance of strength, corrosion resistance, and weldability, making them suitable for marine applications and architectural structures.
Sourcing and preparing aluminium is a foundational step in the wire manufacturing process. The choice of alloy depends on the intended application, ensuring the final product meets specific requirements for performance and durability.
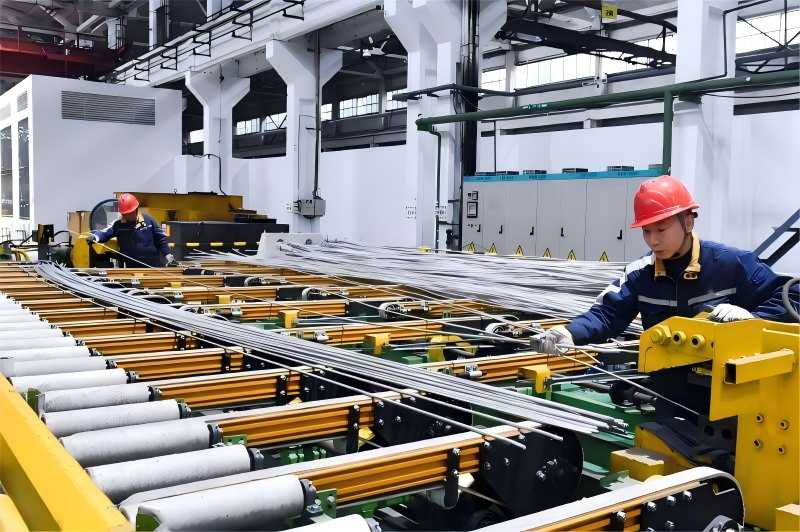
Aluminum Wire Manufacturing Processes
Once the aluminum alloy is produced, it undergoes a series of processes to transform it into the desired wire form. These processes involve shaping, reducing the cross-section, and enhancing the mechanical properties of the aluminum.
Melting and Casting
Melting: Refined aluminium or alloyed materials are melted in high-temperature furnaces. Solid aluminium ingots are heated to convert them into molten aluminium. During this process, precise temperature control is essential to ensure the quality of the molten metal. If alloy aluminium wires are being produced, specific alloying elements are added at this stage to modify properties such as strength and corrosion resistance.
Casting: The molten aluminium is poured into specific molds or continuous casting systems to create billets or rods. This step ensures the aluminium billet’s shape and size conform to requirements and that the internal structure is uniform, and free from defects like air pockets.
Hot Rolling and Wire Drawing
Hot Rolling: The aluminium billets are heated and passed through rolling mills to reduce their thickness and create rods. This process is ideal for creating larger sections like strips or rods.
Wire Drawing: To achieve finer diameters, aluminium rods are subjected to a drawing process. The rods are pulled through dies of decreasing sizes using a wire-drawing machine. This process applies tensile forces to gradually reduce the diameter while maintaining uniformity. Proper lubrication minimizes friction and ensures a smooth surface finish.
Annealing and Heat Treatment
Annealing is used to improve the ductility and flexibility of aluminium wires. By heating the wires to a specific temperature and cooling them gradually, manufacturers achieve the required mechanical and electrical properties.
The manufacturing process of aluminum wire involves a combination of mechanical and thermal treatments. Precision engineering and rigorous quality control are essential at each stage to ensure the production of high-quality, consistent wire that meets the stringent demands of various applications.
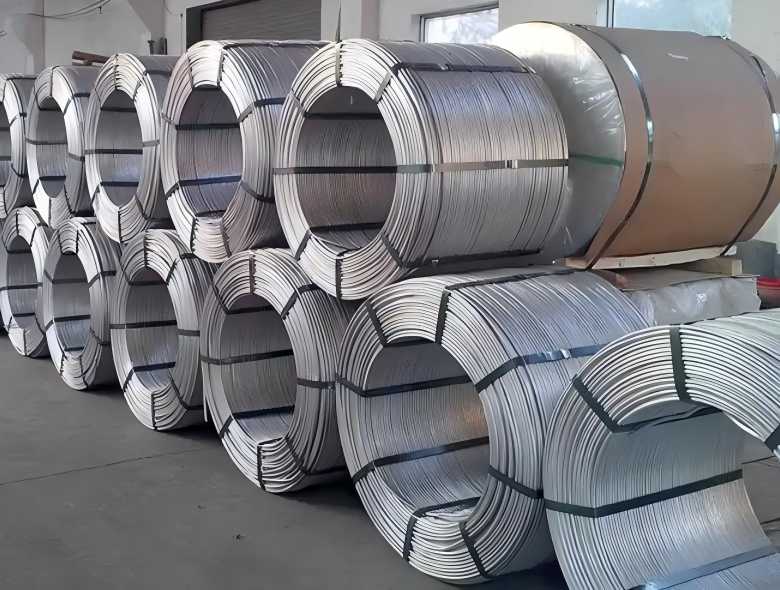
Finishing and Quality Control
After the wire is drawn, it may undergo additional finishing processes to enhance its properties or appearance. Rigorous quality control measures are implemented throughout the manufacturing process to ensure that the final product meets the required specifications.
Finishing Processes:
- Anodizing: An electrochemical process that creates a protective oxide layer on the surface of the aluminum wire, improving its corrosion resistance and aesthetics.
- Electroplating: A process where a thin layer of another metal (e.g., copper, nickel) is deposited on the wire’s surface, enhancing its conductivity or appearance.
- Powder Coating: A process where a dry powder coating is applied to the wire’s surface, providing insulation, protection, and a decorative finish.
Quality Control:
- Dimensional Checks: Regular measurements are taken to ensure that the wire diameter and other dimensions conform to the specified tolerances.
- Mechanical Testing: Tests such as tensile strength, elongation, and hardness are conducted to evaluate the mechanical properties of the wire.
- Electrical Conductivity Tests: Measurements are taken to ensure that the wire exhibits the required electrical conductivity.
- Corrosion Resistance Tests: Tests are performed to assess the wire’s resistance to various corrosive environments.
The finishing and quality control stages are critical in ensuring that the aluminum wire meets the highest standards of performance and reliability. Through meticulous attention to detail and the implementation of rigorous testing procedures, CHAL can deliver high-quality products that meet the diverse needs of our customers.
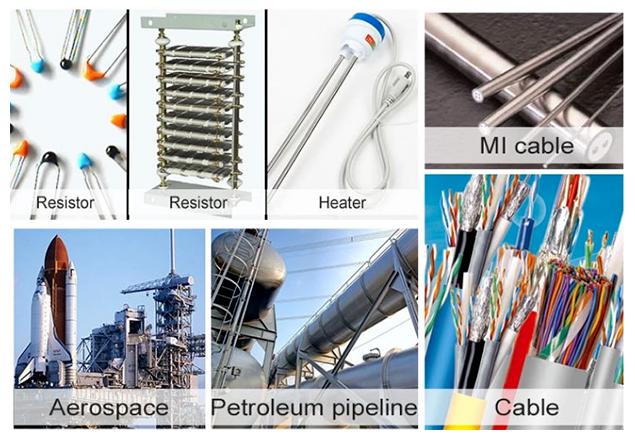
Applications of Aluminum Wire
Aluminum wire finds widespread applications across various industries due to its unique combination of properties. Key applications are:
- Electrical Transmission and Distribution: Aluminum conductors are extensively used in overhead power lines and underground cables due to their high conductivity and lightweight, which reduces the weight and cost of transmission towers.
- Construction: Aluminum wires are widely used in building wiring, electrical appliances, and construction materials.
- Transportation: Aluminum wires are used in automotive wiring, aircraft wiring, and other transportation applications due to their lightweight and excellent corrosion resistance.
- Electronics: Aluminium wiring is employed in various electronic devices and components, offering a balance of performance and cost.
The production of aluminum wire is a complex process that involves a series of sophisticated steps, from the mining of bauxite to the final finishing and quality control measures. Their applications in energy, construction, automotive, and electronics highlight their indispensability in our daily lives and technological progress. Through continuous innovation, CHAL will provide high-quality, reliable products that meet the ever-growing demands of the modern world.