Aluminum stamping, a high-speed, high-volume manufacturing process, involves transforming flat aluminum sheets into intricate three-dimensional shapes using specialized tooling and immense force. This process is integral to various industries, from automotive and aerospace to electronics and construction, due to aluminum’s desirable properties like lightweight, corrosion resistance, and excellent formability. However, the success of aluminum stamping hinges critically on the selection of the appropriate aluminum alloy. This article delves into the nuances of choosing suitable aluminum alloys for stamping, examining their influence on the stamping process, and exploring the mechanical properties of the resulting stamped parts.

What Types of Aluminum Alloys are Suitable for Stamping
Aluminum alloys are classified based on their primary alloying elements, which significantly influence their properties.
1. Overview of Aluminum Alloys
Wrought aluminum alloys are designed for shaping processes like aluminum stamping. They are further categorized based on their primary alloying elements:
- Copper Alloys (2xxx Series): Known for their high strength, but they can be challenging to weld and may exhibit limited formability.
- Magnesium-Silicon Alloys (6xxx Series): Offer a good balance of strength, formability, and weldability, making them popular choices for aluminum stamping applications.
- Magnesium Alloys (5xxx Series): Renowned for their high strength-to-weight ratio and excellent corrosion resistance.
- Manganese Alloys (3xxx Series): Provide good workability and moderate strength, often used in applications where cost-effectiveness is crucial.
- Zinc Alloys (7xxx Series): Exhibit exceptional strength but can be more susceptible to cracking during forming operations.
- Silicon Alloys (4xxx Series): Primarily used for welding purposes due to their low melting point.
2. Commonly Used Stamping Alloys
6xxx Series (Aluminum-Magnesium-Silicon): This series is a workhorse in the aluminum stamping industry.
- 6061: A versatile alloy known for its excellent formability, moderate strength, and good weldability. It finds applications in automotive components, aerospace structures, and architectural products.
- 6063: Offers high formability and good corrosion resistance. It’s commonly used in extrusion processes but can also be stamped into various shapes, including those found in construction and consumer electronics.
5xxx Series (Aluminum-Magnesium): These alloys are prized for their high strength-to-weight ratio, making them suitable for applications where weight reduction is critical.
- 5052: Provides a good balance of strength, formability, and corrosion resistance. It’s often used in marine applications, transportation, and pressure vessels.
- 5083: Exhibits high strength and excellent weldability, making it suitable for demanding applications like shipbuilding and military vehicles.
3xxx Series (Aluminum-Manganese): These alloys offer a good combination of workability and cost-effectiveness.
- 3003: Known for its high formability and good corrosion resistance. It’s widely used in food and beverage packaging, as well as general sheet metal fabrication.
- 3004: Offers higher strength than 3003 while maintaining good formability. It’s commonly used in transportation applications and architectural products.
3. Other Suitable Alloys
- 7xxx Series (Aluminum-Zinc-Magnesium-Copper): These alloys offer exceptional strength but can be more challenging to form due to their susceptibility to cracking. They are often used in aerospace applications where high strength is paramount.
- 2xxx Series (Aluminum-Copper): These alloys provide high strength but can be more difficult to form and weld. They are typically used in applications where high strength and corrosion resistance are critical, such as aircraft components.
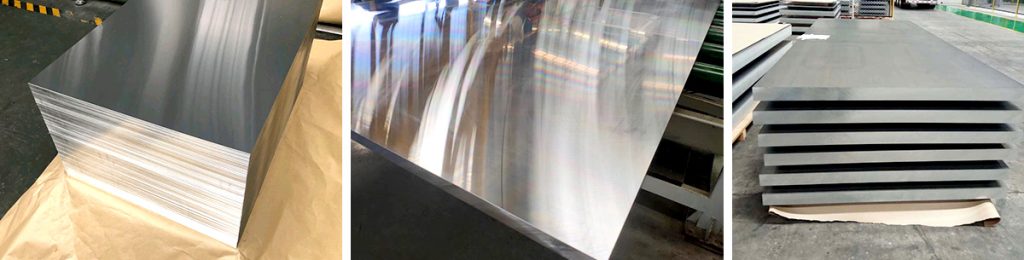
How Do Different Aluminum Alloys Affect the Stamping Process?
The choice of aluminum alloy significantly impacts the aluminum stamping process and the final product’s properties.
1. Formability
- Strain Hardening: During stamping, the metal undergoes plastic deformation, leading to strain hardening, where the material becomes stronger and less ductile. The rate of strain hardening varies among alloys. Alloys with higher strain hardening rates may require more force to deform and can be more susceptible to cracking.
- Ductility: Ductility is the ability of a material to undergo plastic deformation without fracturing. Highly ductile alloys can be formed into complex shapes with minimal risk of failure. Alloys with lower ductility may require more gradual deformation steps to avoid cracking.
2. Strength
- Stamping Pressure: The strength of the aluminum alloy directly influences the required stamping pressure. Higher-strength alloys necessitate higher forces to achieve the desired deformation.
- Springback: Springback is the tendency of the metal to partially recover its original shape after being formed. Stronger alloys exhibit higher springback tendencies, requiring careful consideration in die design to compensate for this effect.
3. Work Hardening
Work hardening can be beneficial in some cases, as it can increase the strength and stiffness of the final part. However, excessive work hardening can lead to localized strain and potential cracking. The rate of work hardening varies among alloys, influencing the overall formability and the final mechanical properties of the stamped part.
4. Heat Treatment
Some aluminum alloys, such as the 6000 and 7000 series, can be heat treated to further enhance their strength and other mechanical properties. Heat treatment processes, such as solution heat treatment and artificial aging, can significantly affect the alloy’s formability and its suitability for stamping.
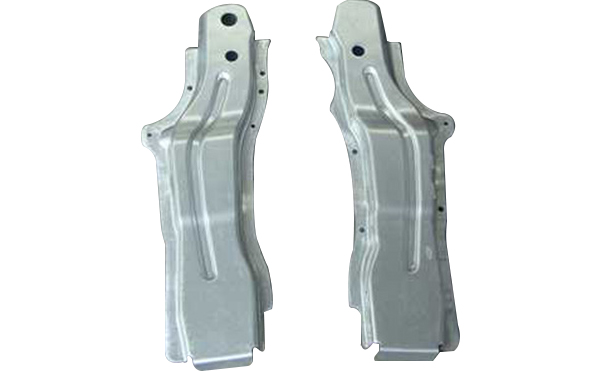
What are the Mechanical Properties of Aluminum Stamped Parts?
The mechanical properties of aluminum stamped parts are critical for ensuring their performance in service.
1. Strength
- Tensile Strength: Measures the maximum stress an alloy can withstand before fracturing under tension.
- Yield Strength: Indicates the stress level at which the alloy begins to deform plastically.
- Fatigue Strength: Represents the ability of the alloy to withstand repeated cyclic loading without fracturing.
The strength properties of stamped parts are influenced by the alloy’s composition, the stamping process parameters, and any subsequent heat treatment.
2. Ductility
Ductility is a measure of an alloy’s ability to deform plastically without fracturing. It’s typically measured in terms of:
- Elongation: The percentage increase in length of a specimen before it fractures under tensile loading.
- Reduction in Area: The percentage decrease in cross-sectional area of a specimen at the point of fracture.
Ductility is essential for ensuring that the stamped part can accommodate the complex shapes required in many applications.
3. Hardness
Hardness is a measure of an alloy’s resistance to indentation or scratching. It’s often measured using the Rockwell or Brinell hardness scales. Higher hardness generally improves the wear resistance and dimensional stability of the stamped part.
4. Other Properties
- Corrosion Resistance: Aluminum and its alloys are naturally resistant to corrosion due to the formation of a protective oxide layer on their surface. However, the corrosion resistance of different alloys can vary.
- Fatigue Life: The number of cycles of loading that a part can withstand before fracturing under cyclic stress. Fatigue life is crucial for components subjected to repeated loading, such as those found in automotive and aerospace applications.
Aluminum stamping offers a versatile and efficient solution for modern manufacturing needs. By understanding the properties of various aluminum alloys and their impact on the stamping process, manufacturers can optimize performance and cost-effectiveness. With advancements in alloy development and stamping techniques, aluminum stamped parts will continue to play a pivotal role in industries seeking lightweight, durable, and sustainable solutions.