Pharmaceutical blister packaging is a critical component of drug delivery, ensuring the safety, efficacy, and convenience of medications. One of the essential materials used in blister packaging is aluminum foil. This article will delve into the significance of aluminum foil thickness in pharmaceutical blister packaging, exploring its role, common grades and thicknesses, and the impact it has on packaging performance.
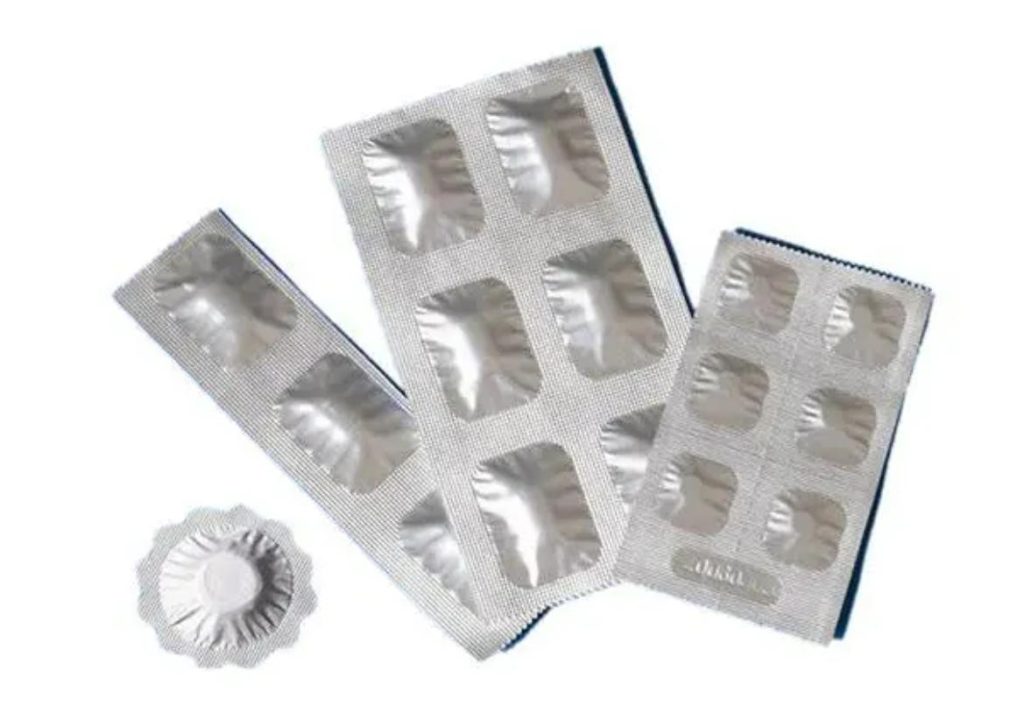
Aluminum Foil in Blister Packaging
Aluminum foil is a popular choice for pharmaceutical blister packaging due to its several advantages:
It offers exceptional barrier properties, which are critical for protecting sensitive pharmaceutical products from moisture, oxygen, and light. These properties help in maintaining the stability and potency of medications throughout their shelf life. Additionally, aluminum foil is flexible, durable, and capable of being easily laminated with other materials, making it ideal for creating secure and effective blister packs.
Common Aluminum Foil Grades in Pharmaceutical Packaging
Aluminum foil used in pharmaceutical packaging typically comes in several grades, including:
- Pharmaceutical Grade Foil: Specifically designed for direct contact with pharmaceutical products, this foil ensures minimal risk of contamination.
- Laminated Foil: This involves aluminum foil being combined with other layers, such as polymer films, to enhance barrier properties and sealability. 8011 aluminum foil is commonly used in blister packs for added protection.
Common Thicknesses Used in Pharmaceutical Packaging
The thickness of aluminum foil used in blister packaging can vary depending on the required performance characteristics. Common thicknesses include:
- 20-25 microns: Often used for standard blister packs, providing adequate barrier protection for many products.
- 30-40 microns: Used for more demanding applications where enhanced barrier properties and mechanical strength are needed.
- 50 microns and above: Typically employed for specialized packaging requiring superior durability and barrier performance.
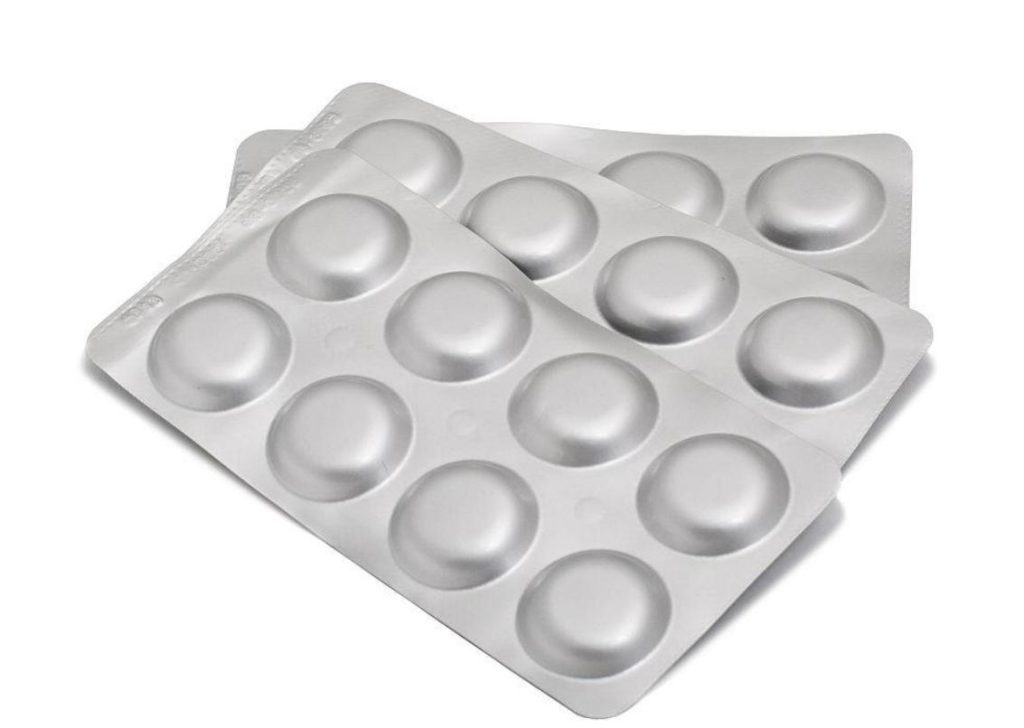
Impact of Aluminum Foil Thickness on Packaging Performance
The thickness of aluminum foil can significantly influence the performance of pharmaceutical blister packaging. Key areas affected include:
Barrier Properties
The thickness of aluminum foil plays a crucial role in its ability to act as a barrier against external elements such as moisture, oxygen, and light. Thicker foils generally provide enhanced barrier protection, which is essential for preserving the stability and potency of pharmaceutical products. For instance, a 30-micron foil offers superior resistance to moisture and oxygen compared to a 20-micron foil, thereby extending the shelf life of sensitive medications. In contrast, thinner foils may not offer the same level of protection, potentially leading to reduced effectiveness of the product over time.
Seal Integrity
Aluminum foil thickness also significantly impacts the integrity of seals in blister packaging. Thicker foils tend to have greater resistance to tearing and punctures during the sealing process, resulting in stronger and more reliable seals. This is vital for ensuring that the blister pack remains intact and that the medication is protected from contamination. On the other hand, thinner foils may be more prone to seal failures, which can compromise the protection of the product and increase the risk of contamination.
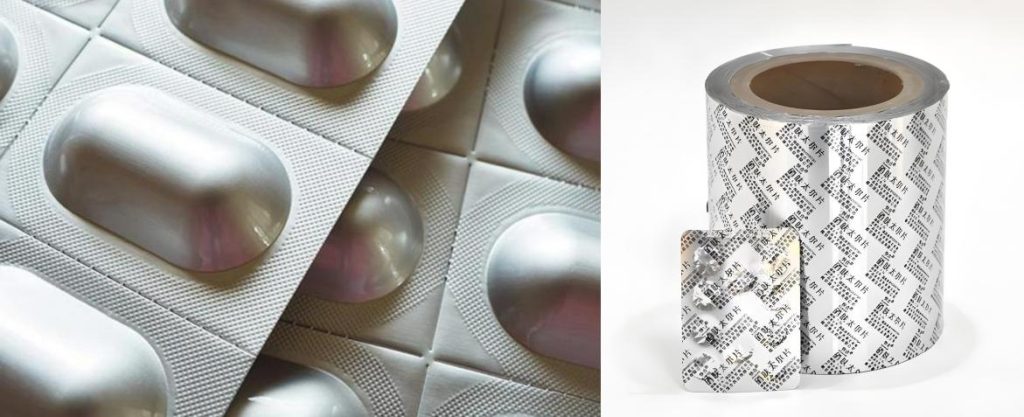
Mechanical Strength
The mechanical strength of the foil, which includes its resistance to physical damage such as punctures and abrasions, is influenced by its thickness. Thicker aluminum foils provide greater durability and resistance to damage, making them more suitable for handling and transportation. This added strength helps prevent the blister packs from being compromised during distribution and storage. Conversely, thinner foils may be more vulnerable to physical damage, potentially leading to compromised packaging performance and product integrity.
Cost and Efficiency
While thicker aluminum foils offer improved performance in terms of barrier properties, seal integrity, and mechanical strength, they also come with higher material costs. Therefore, selecting the right thickness involves balancing the performance benefits with the associated costs. For many applications, a standard 20-25 micron foil provides sufficient protection at a lower cost. However, for more demanding applications where enhanced performance is required, investing in thicker foils may be justified despite the increased expense. Careful consideration of both performance requirements and budget constraints is essential for optimizing packaging effectiveness.
The thickness of aluminum foil used in pharmaceutical blister packaging is a critical factor influencing the overall performance of the packaging. Thicker foils offer superior barrier properties, enhanced seal integrity, and greater mechanical strength, which are essential for protecting sensitive medications. However, these benefits come at a higher cost, necessitating a careful evaluation of performance needs versus budget constraints. By understanding the impact of foil thickness, pharmaceutical manufacturers can make informed decisions to optimize packaging effectiveness and ensure the safety and efficacy of their products.