Additive manufacturing(AM), commonly known as 3D printing, is transitioning from prototyping to industrial production, driven by the revolutionary adoption of aluminum powder. With its low density, high strength-to-weight ratio, and excellent thermal conductivity, aluminum has become a strategic material in aerospace, automotive, and medical industries. Market research indicates that the aluminum powder additive manufacturing market was valued at US$410,000 in 2022 and is projected to exceed US$470,000 by 2031, growing at a compound annual growth rate (CAGR) of 32.5%. Boeing’s 3D-printed aluminum aircraft brackets reduced weight by 30%, while Tesla’s aluminum motor housings improved thermal conductivity by 30%, demonstrating how aluminum powder is redefining manufacturing paradigms.
Aluminum powder not only overcomes the limitations of traditional manufacturing for complex geometries but also unlocks unprecedented opportunities for light weighting and functional integration through material-process synergy.

The Properties and Advantages of Aluminum Powder
Aluminum, in its powdered form, retains its inherent material characteristics while gaining unique processing advantages. Its low density (approximately 2.7 g/cm³) combined with high strength-to-weight ratio makes it ideal for applications where weight reduction is critical. Additionally, aluminum’s excellent thermal conductivity facilitates efficient heat dissipation, and its natural corrosion resistance enhances durability in various environments. The ability to alloy aluminum with other elements further expands its range of mechanical properties, allowing for tailored solutions. The particle size and morphology of the powder are also critical. Spherical particles with consistent size distribution improve powder flow and packing density, which are essential for achieving high-quality prints.
These intrinsic qualities of aluminum, when transferred into powder form, set the stage for its transformative role in additive manufacturing.
How These Properties Are Beneficial in Additive Manufacturing
In additive manufacturing, these material characteristics translate into tangible benefits. The lightweight nature of aluminum allows for the creation of components that reduce fuel consumption in aerospace and automotive applications. For example, GE Aviation has utilized aluminum alloy powder to 3D-print complex heat exchangers, reducing weight by up to 40% compared to traditional manufacturing methods.
The high thermal conductivity is crucial in heat sinks and electronic enclosures, ensuring effective thermal management. The design freedom offered by 3D printing, combined with aluminum’s machinability, enables the production of intricate geometries that are impossible or cost-prohibitive to manufacture using conventional techniques. Moreover, the ability to create customized alloys through powder blending opens up a vast array of material possibilities, tailored to specific performance requirements. These advantages make aluminum powder a preferred material for high-performance AM projects.
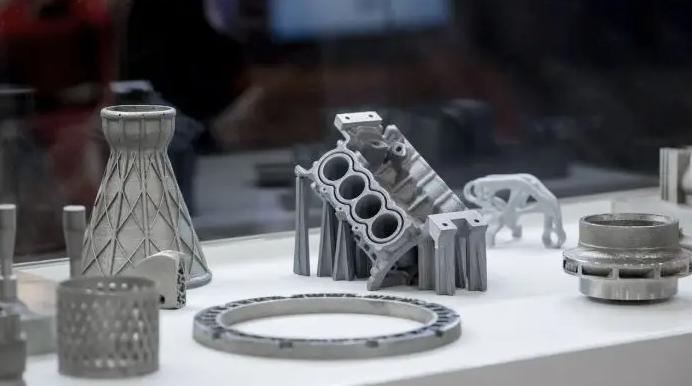
Aluminum Powder in Additive Manufacturing Processes
How Aluminum Powder is Used in Each Process
Aluminum powder is utilized in several AM techniques, each requiring specific powder characteristics to optimize performance and quality:
Selective Laser Melting (SLM):
SLM uses a high-powered laser to selectively fuse aluminum powder layer by layer. The powder must have excellent flowability, high sphericity, and uniform particle size distribution to ensure consistent layering and fusion.
Atomized aluminum powders, such as AlSi10Mg and AlSi7Mg, are commonly used. These powders are chosen for their high strength, thermal stability, and ability to produce dense, high-performance parts.
Electron Beam Melting (EBM):
Similar to SLM, EBM uses an electron beam instead of a laser to melt aluminum powder. It operates in a vacuum, reducing the risk of oxidation. The process is faster and suitable for larger parts but requires careful temperature control.
EBM often uses pre-alloyed aluminum powders, like Al-Mg alloys, which offer excellent corrosion resistance and mechanical properties. The powder must also be highly spherical to ensure smooth powder bed distribution.
Binder Jetting:
In this technique, aluminum powder is deposited in layers and bonded using a liquid binder. The green part is then sintered to fuse the particles. This method is ideal for prototyping or creating parts that don’t require high strength.
Aluminum powders with larger particle sizes (irregular or semi-spherical) are suitable for binder jetting. The powder should have low oxygen content to minimize defects during sintering.
Cold Spray:
Aluminum powder is accelerated to supersonic speeds and sprayed onto a substrate to create dense coatings or components without melting the powder. This eliminates thermal stresses and oxidation.
Coarser aluminum powders, often with irregular shapes, are used in cold spray. The material’s ductility and purity are critical for achieving high-quality deposits.
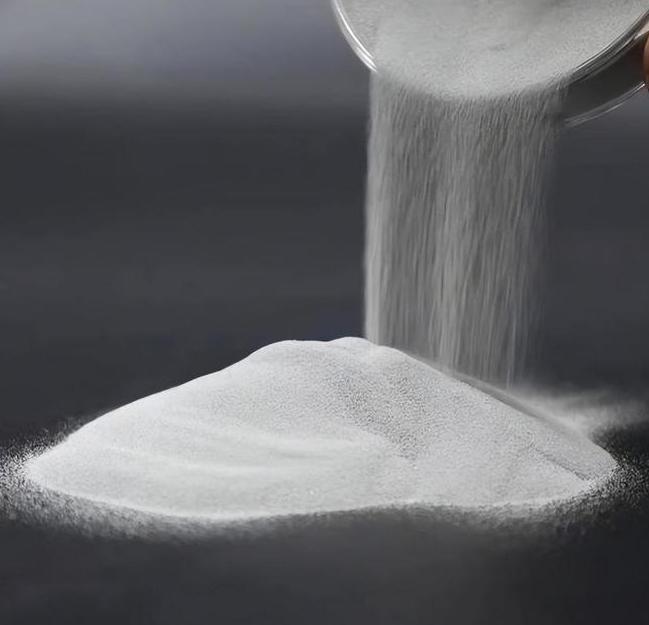
Factors Influencing the Quality of 3D-Printed Aluminum Parts
Several factors significantly influence the quality of 3D-printed aluminum parts.
- Firstly, the powder’s particle size distribution and morphology play a crucial role. Spherical particles with a narrow size distribution ensure consistent powder flow and packing density, leading to uniform melting and solidification.
- Secondly, process parameters such as laser power, scan speed, and layer thickness directly impact the microstructure and mechanical properties of the final part. Optimizing these parameters is essential to minimize defects like porosity and cracking. For instance, research shows that increasing laser power can reduce porosity but may also lead to increased residual stress.
- Thirdly, alloy selection is critical. Different aluminum alloys offer varying mechanical properties, and choosing the right alloy for a specific application is essential.
- Lastly, post-processing techniques like hot isostatic pressing (HIP) and heat treatment can further enhance the mechanical properties and surface finish of 3D-printed aluminum parts. For example, HIP can reduce internal porosity, improving fatigue resistance.
Careful control of these factors is essential to ensure the production of high-quality, reliable aluminum parts through additive manufacturing.
Main Applications Across Industries
Aerospace
In the aerospace industry, weight reduction is paramount. Aluminum powder-based additive manufacturing enables the production of lightweight structural components, fuel system parts, and heat exchangers. For instance, Airbus has implemented 3D-printed aluminum components in its A350 XWB aircraft, achieving significant weight savings and performance improvements. Additionally, the ability to create complex geometries allows for the optimization of aerodynamic designs, leading to improved fuel efficiency.
Automotive
The automotive industry is leveraging aluminum powder in additive manufacturing for prototyping, tooling, and the production of lightweight components for electric vehicles. For example, companies like Porsche are using 3D-printed aluminum parts for concept vehicles and customized components, reducing development time and costs. The ability to produce complex geometries enables the creation of optimized engine components and chassis parts, leading to improved performance and fuel efficiency. The growing adoption of electric vehicles further drives the demand for lightweight aluminum components to enhance range and efficiency.
Aluminum 3D printing is driving innovation and efficiency in automotive manufacturing, from prototyping to production.
Medical
In the medical field, aluminum powder is used to create customized implants, prosthetics, and surgical tools. The ability to tailor designs to individual patient anatomy improves implant fit and function. For instance, custom-made aluminum implants can be designed with porous structures to promote bone ingrowth, enhancing long-term stability. Additionally, 3D-printed surgical guides and tools enable precise and minimally invasive procedures.
Customization and precision are key drivers for the adoption of aluminum 3D printing in the medical industry, improving patient outcomes.
Aluminum additive manufacturing is transcending industry silos, evolving from component production to system-level functional integration with unmatched design freedom.
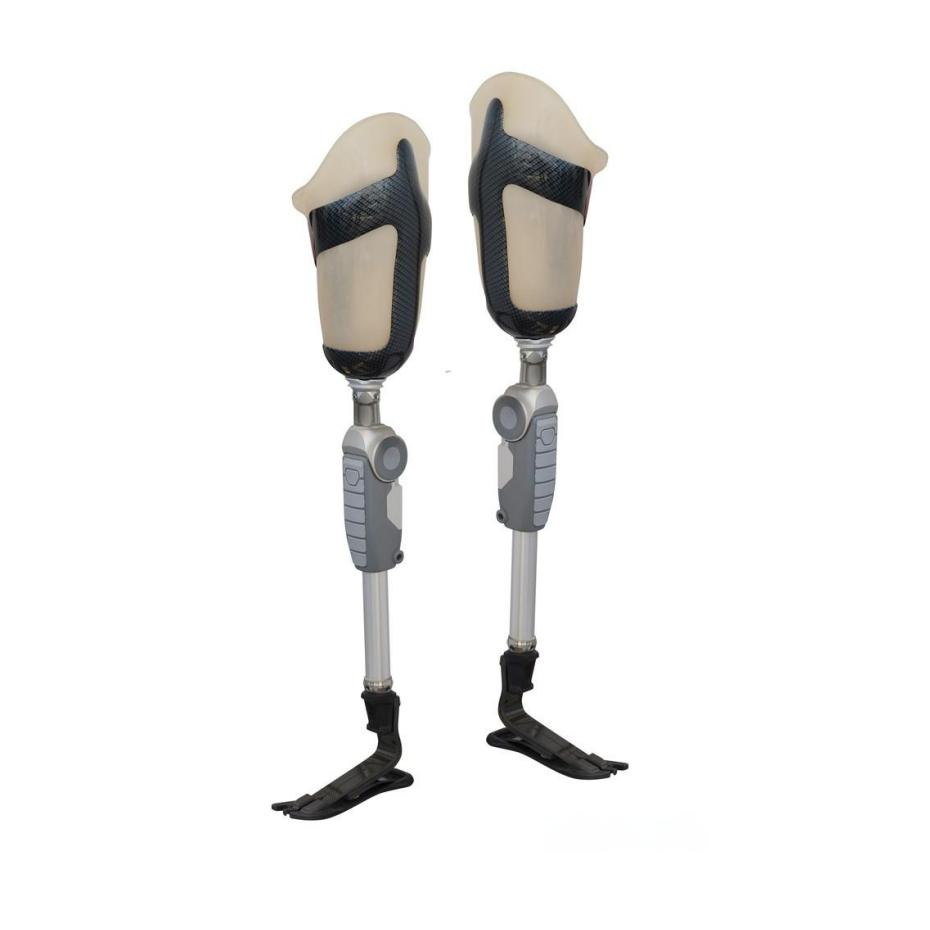
Challenges and Limitations
Despite its many advantages, the use of aluminum powder in additive manufacturing faces several challenges:
- Cost Barriers: Powder costs ($50–200/kg) account for 40–60% of part costs. EOS’s recycling system achieves 80% powder reuse, lowering expenses by 35%.
- Safety Risks: Aluminum powder is highly flammable and poses inhalation hazards. Strict safety protocols and specialized equipment are necessary for handling.
- Porosity and Defects: Achieving dense, defect-free parts can be challenging due to issues like gas entrapment and uneven powder spreading. High-strength alloys like Al7075 suffer liquation cracks in SLM. RWTH Aachen University found preheating to 200°C reduces crack density by 70%.
- Standardization Delays: Only 30% of additive aluminum parts meet AS9100D aerospace standards. NASA’s X-ray CT system detects subsurface flaws as small as 0.05 mm.
- Post-Processing Requirements: Aluminum AM parts often require extensive post-processing, such as machining and heat treatment, to achieve optimal properties.
Overcoming these challenges requires ongoing research into improving powder quality, developing safer handling techniques, and optimizing AM processes.
When Tesla’s 3D-printed aluminum battery trays extend EV range by 12%, or when the ISS’s aluminum brackets surpass 15 years of orbital service, these milestones signal aluminum powder’s transition from labs to global supply chains. Looking ahead, gradient materials (e.g., Constellium’s Al-Si-Mg alloys) and hybrid manufacturing (DMG MORI’s 5-axis milling-DED integration) will unlock next-gen applications like topology-optimized structures and functionally graded devices. McKinsey predicts that aluminum additive manufacturing could reduce global manufacturing costs by 19% by This material-driven revolution is not merely replacing traditional methods—it is scripting a new chapter in smart manufacturing.