Aluminum alloys have become irreplaceable materials in industrial manufacturing (such as automobiles, aerospace, construction, and electronics) due to their light weight, high strength, corrosion resistance, and easy processing. Extrusion is the core method of aluminum alloy forming. It uses high pressure to push heated aluminum billets through a die to form profiles with complex cross-sectional shapes.
However, the choice of aluminum alloy directly affects the feasibility of the extrusion process and the performance of the final product. For example, although high-strength aluminum alloys can improve the mechanical properties of the product, they may lead to increased extrusion difficulty and higher costs. This article explores the interaction between aluminum alloy composition and extrusion process, as well as its impact on product performance, to provide guidance for engineering material selection and process optimization.
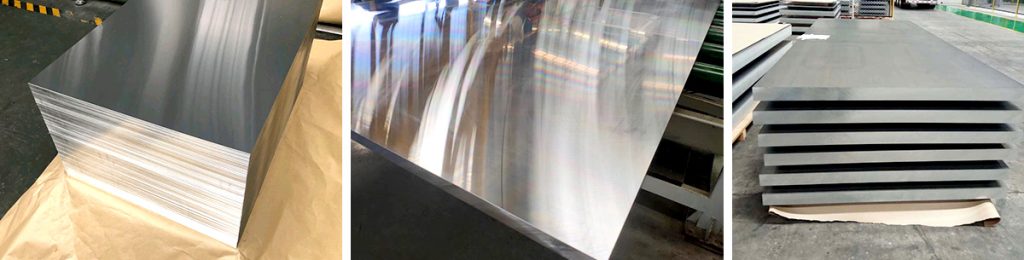
Understanding Aluminum Alloys and the Extrusion Process
Aluminum alloys are a diverse group of materials, each with unique properties tailored for specific applications. They are created by combining aluminum with other elements, such as magnesium, silicon, copper, and zinc, to enhance strength, corrosion resistance, and other characteristics.
Common Aluminum Alloys for Extrusion:
- 6xxx series (such as 6061, 6063): Contains magnesium (Mg) and silicon (Si), has good extrudability, medium strength and corrosion resistance, and is widely used in building doors and windows, and automobile frames.
- 7xxx series (such as 7075): Contains zinc (Zn) and copper (Cu), has extremely high strength but is difficult to extrude, and is suitable for aerospace structural parts.
- 5xxx series (such as 5083): Mainly magnesium, has excellent corrosion resistance, and is commonly used in ships and chemical equipment.
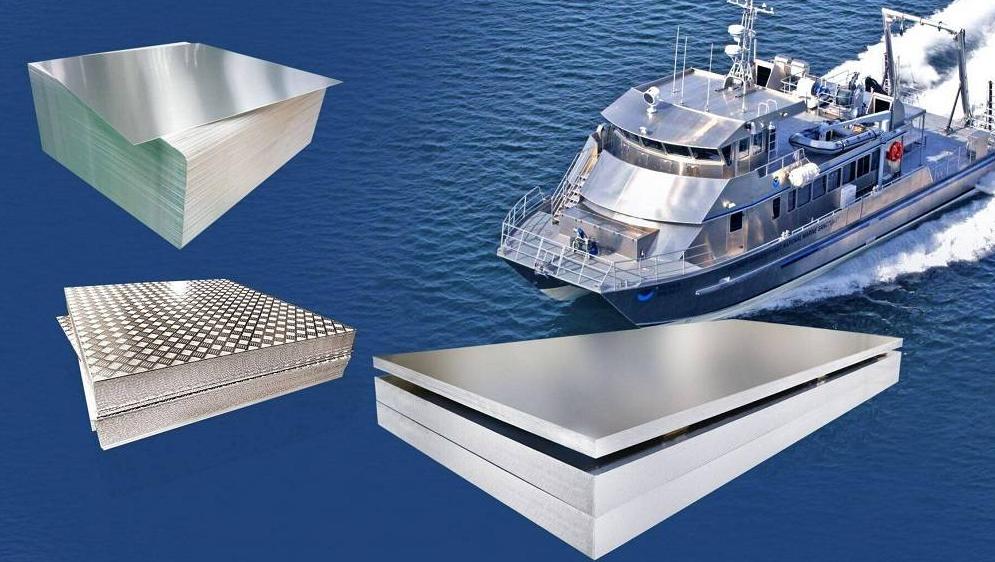
Key Parameters and Challenges of the Extrusion Process:
The extrusion process involves several critical parameters, including billet temperature, extrusion speed, die design, and cooling rate. The alloy’s properties directly influence these parameters. For instance, stronger alloys require higher pressures and may necessitate slower extrusion speeds to avoid defects. The die design must also be tailored to the specific alloy and the desired profile shape. Challenges in extrusion include managing material flow, preventing defects like cracking and tearing, and controlling the final microstructure through controlled cooling. Successfully navigating these challenges depends heavily on the appropriate alloy selection.
The diversity of aluminum alloys is closely related to the complexity of the extrusion process. Only by deeply understanding the interaction between material properties and process parameters can we effectively avoid production risks and improve product quality.
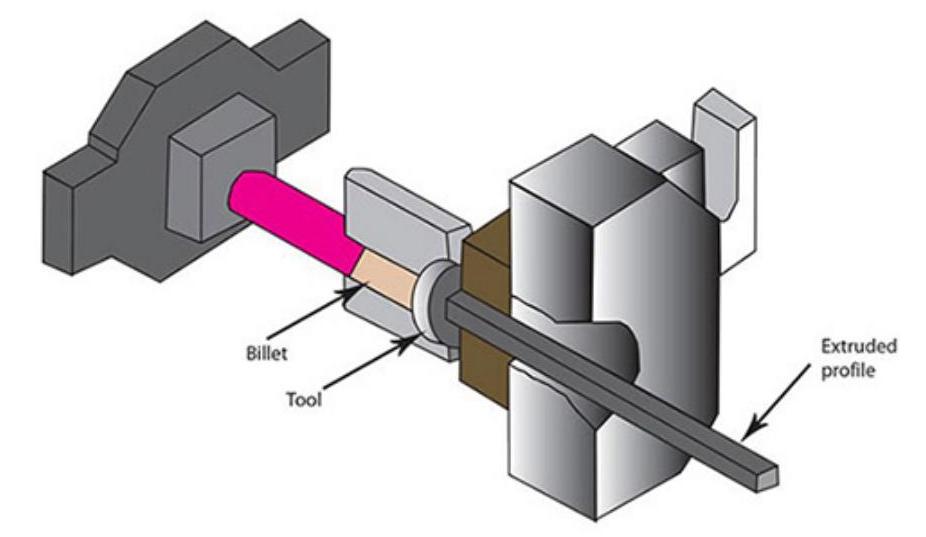
Effects of Aluminum Alloy Selection on Extrusion Process
The selection of aluminum alloy plays a pivotal role in the intricacies of the extrusion process, influencing both the material behavior during deformation and the parameters required for successful extrusion.
Alloy Properties Impacting Extrusion:
Strength and Malleability: These properties at elevated temperatures dictate the force required to push the billet through the die. Stronger alloys demand higher pressures, potentially requiring specialized equipment. Malleability affects how easily the material flows and fills the die cavity, influencing the complexity of extrudable shapes.
Extrudability: This refers to the ease with which a specific alloy can be extruded. Extrudability Determined by the deformation resistance and fluidity of the alloy. For example, 6xxx alloys have better fluidity than high-zinc 7xxx alloys due to the lubrication of the Mg₂Si precipitate phase. Alloys with higher extrudability require less force and can be extruded at higher speeds, leading to increased productivity.
Thermal Conductivity: The alloy’s ability to conduct heat influences the cooling rate of the extruded profile. Rapid cooling can affect the microstructure and, consequently, the final properties.
Process Parameters Influenced by Alloy:
Extrusion Speed: The maximum speed at which extrusion can occur is often limited by the alloy’s properties. Extruding too quickly can lead to defects. For example, 6061 alloy allows speeds of 20~30 m/min, while 7075 alloys need to be reduced to 5~10 m/min to prevent cracking.
Die Design: The complexity of the desired profile and the characteristics of the chosen alloy dictate the die design. More complex profiles and less malleable alloys demand more intricate die designs to ensure uniform material flow.
Billet Temperature: The temperature of the aluminum billet before extrusion significantly affects the material’s flow stress and the forces involved. Different alloys require different billet temperatures for optimal extrusion. 6xxx alloys can be extruded at 450-480°C, while 7xxx alloys require higher temperatures (480-520°C) to reduce deformation resistance.
The chemical composition of aluminum alloy directly determines the feasibility and economy of extrusion process. So selecting an alloy with properties compatible with the desired profile and extrusion equipment is essential for a smooth and efficient extrusion process.
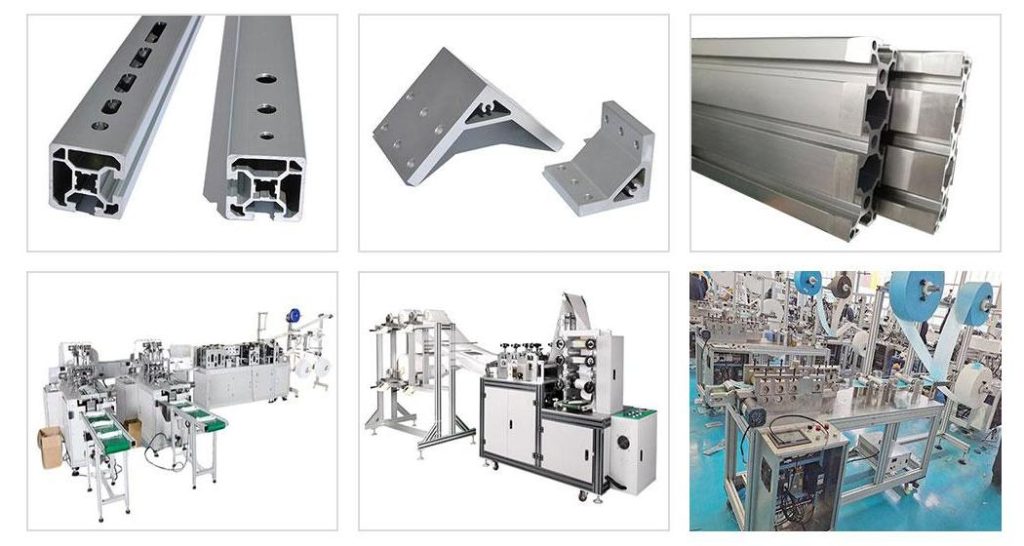
Effects of Aluminum Alloy Selection on the Performance of the Final Product
The choice of aluminum alloy profoundly impacts the performance characteristics of the final extruded product, dictating its suitability for specific applications. Careful consideration of the desired properties is crucial for selecting the optimal alloy.
Mechanical Properties:
Strength: Different alloys offer a wide range of tensile and yield strengths, directly influencing the load-bearing capacity of the extruded profile. For example, 6061 alloy, with its moderate to high strength, is commonly used in structural applications like bicycle frames and aircraft components. In contrast, 6063, while offering good strength, is often chosen for applications where aesthetics and extrudability are paramount, such as window frames. Higher strength alloys like 7075 (often used in aerospace) would require significantly more force to extrude and might not be suitable for complex profiles.
Hardness: Resistance to indentation and wear is crucial for applications where surface durability is essential. For instance, components exposed to abrasive environments, like gears or sliding parts, might benefit from alloys with higher hardness, such as some 7xxx series alloys. However, increased hardness can sometimes come at the cost of reduced ductility.
Ductility: This property describes the material’s ability to deform without fracturing. Ductile alloys are essential for applications requiring bending, forming, or impact resistance. 6063, for example, exhibits good ductility, making it suitable for complex shapes and applications where some deformation might be required. Conversely, some higher-strength alloys might have lower ductility, making them more brittle.
Fatigue Resistance: Essential for components subjected to cyclic loading, such as those in machinery or vehicles. Alloys with good fatigue resistance, like certain 6xxx series alloys, can withstand repeated stress cycles without failure. For example, 6061 is often used in automotive parts due to its good fatigue properties. The specific alloy and its processing significantly influence fatigue life.
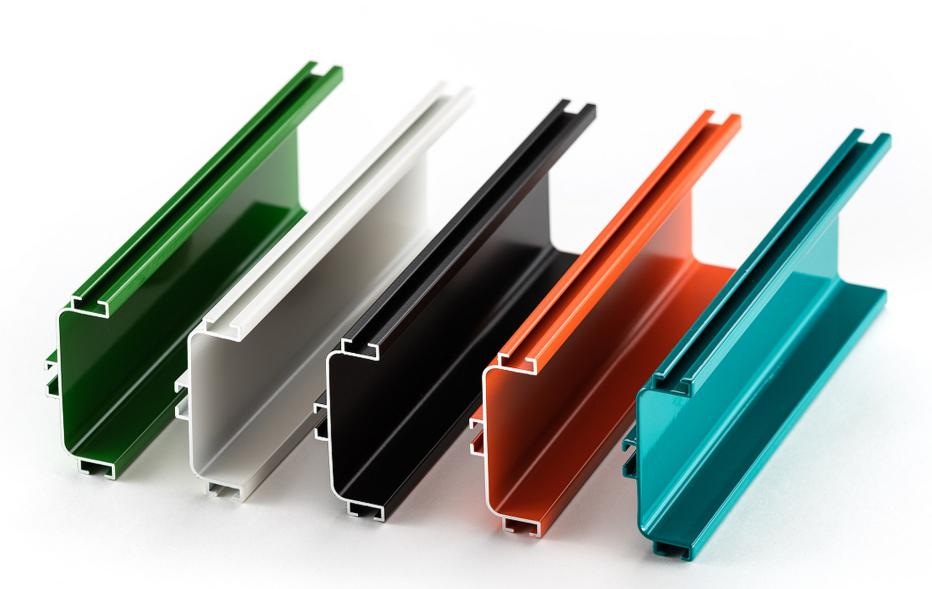
Surface Quality and Corrosion Resistance:
Surface Finish: Some alloys naturally produce a smoother surface finish after extrusion, reducing the need for additional processing. 6063 is known for its excellent surface finish, making it a popular choice for architectural applications where aesthetics are important. Other alloys might require additional finishing processes, such as anodizing or painting, to achieve the desired appearance.
Corrosion Resistance: The ability to withstand environmental degradation varies significantly between alloys. 6063 and 6061 offer good corrosion resistance, making them suitable for outdoor applications. For more demanding environments, like marine applications, alloys with superior corrosion resistance, such as 5xxx series alloys (although less common for complex extrusion), might be considered. It’s crucial to select an alloy that can withstand the specific environmental conditions it will be exposed to. For example, using a non-corrosion-resistant alloy in a marine environment would lead to premature failure.
Functional Properties:
Beyond mechanical and surface properties, other functional characteristics might be critical depending on the application.
- Electrical Conductivity: For electrical applications, alloys with high electrical conductivity are necessary. While aluminum itself is a good conductor, certain alloys are optimized for electrical conductivity.
- Thermal Conductivity: In heat sinks and other thermal management applications, alloys with high thermal conductivity are essential. For example, 6063 is often used in heat sinks due to its good thermal conductivity.
- Weldability: If welding is required for fabrication, the alloy’s weldability is a crucial factor. Some alloys are easier to weld than others, and the welding process can affect the properties of the material. 6061, for example, is known for its good weldability.
The choice of aluminum alloy not only determines the mechanical performance of the product, but also profoundly affects its durability and functional adaptability. Through precise material selection, the overall performance of the product can be maximized.
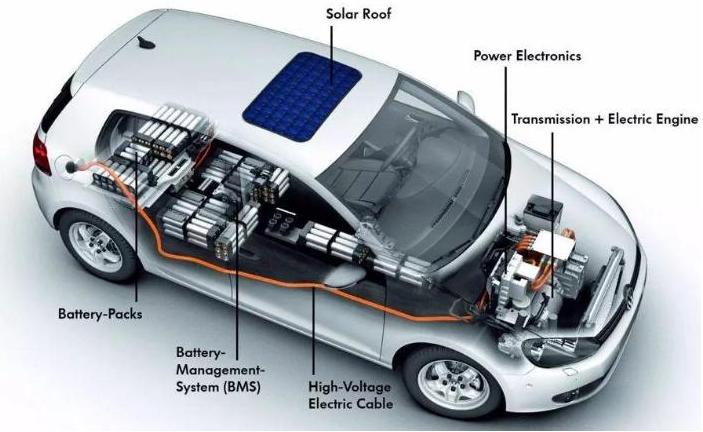
Application-Specific Alloy Selection
Choosing the right aluminum alloy is a balancing act. It requires a thorough understanding of the specific application requirements, including the necessary mechanical properties, environmental conditions, and manufacturing constraints. For example, architectural applications often prioritize aesthetics and corrosion resistance, while structural components may require high strength and fatigue resistance. Some common alloy selections for applications are:
- Construction: Alloys like 6063 are chosen for window frames, railings, and curtain walls due to their aesthetic appeal and corrosion resistance.
- Automotive: High-strength alloys such as 6061 and 7075 are used for structural components and crash-resistant parts.
- Aerospace: Lightweight, high-strength alloys like 7075 are essential for aircraft structures.
- Consumer Goods: Alloys with excellent surface finishes and machinability, such as 6063, are used for furniture and electronic housings.
Consulting with material scientists and extrusion experts to ensure the optimal alloy selection for a given application when necessary.