Aluminum honeycomb core is a lightweight, high-strength material widely used in industries such as aerospace, construction, and transportation. This material consists of thin aluminum foil arranged in a hexagonal pattern, mimicking the structure of a natural honeycomb. Its unique design provides exceptional mechanical properties, including an excellent strength-to-weight ratio, corrosion resistance, and impact absorption. This article delves into the detailed manufacturing process of aluminum honeycomb core, from raw materials to final applications.
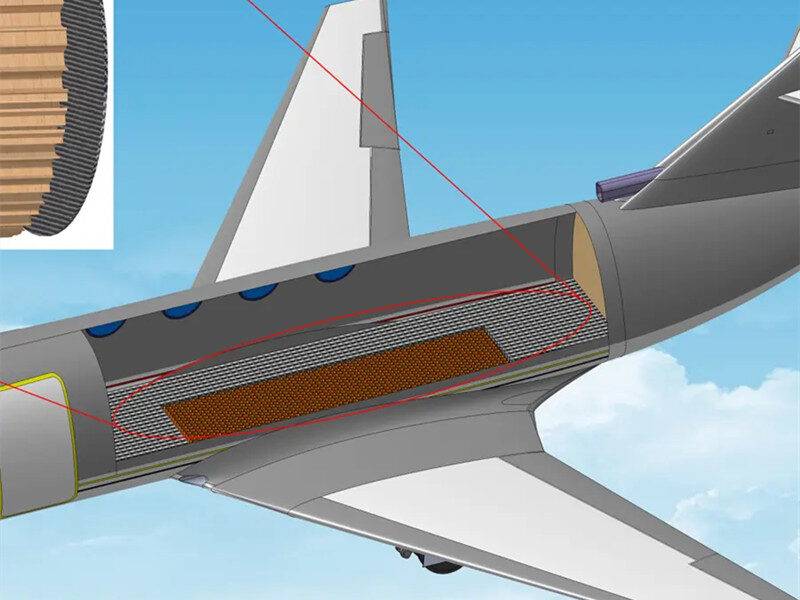
What is the Aluminum Honeycomb Core?
Aluminum honeycomb core is a structural component composed of aluminum sheets or foils bonded together in a geometric honeycomb pattern. The material’s honeycomb structure significantly enhances its rigidity while maintaining a low weight. This makes it an ideal choice for applications where weight reduction and high performance are crucial. The core can be used alone or sandwiched between other materials such as fiberglass, carbon fiber, or aluminum sheets to create composite panels with improved mechanical characteristics.
Key Properties of Aluminum Honeycomb Core
- Lightweight: The hollow structure reduces weight while maintaining strength.
- High Strength-to-Weight Ratio: Strong enough to support heavy loads with minimal weight.
- Corrosion Resistance: Resistant to oxidation and environmental degradation.
- Fire Resistance: Some variants have fireproof coatings for enhanced safety.
- Thermal and Sound Insulation: Acts as a barrier to heat and noise transmission.
- Customizable: Available in various sizes, thicknesses, and densities to meet different application needs.
What are the Aluminum Honeycomb Materials Used in Manufacturing?
The production of aluminum honeycomb core begins with selecting the right materials. The primary raw material is aluminum foil, which must meet specific strength, thickness, and corrosion resistance requirements. Commonly used aluminum foils for honeycomb cores include:
- 3000 series aluminum foils – Offers excellent corrosion resistance and moderate strength.
- 5000 series aluminum foils– Known for higher strength and good resistance to environmental factors.
Additionally, adhesives play a crucial role in bonding the aluminum sheets. These adhesives must withstand mechanical stresses, environmental exposure, and varying temperatures. And the main other materials are:
- Adhesives: High-performance adhesives are used to bond aluminum sheets together at specific points. The type of adhesive varies depending on application requirements, such as temperature resistance and structural integrity.
- Coatings: Some honeycomb cores have special coatings to improve fire resistance, enhance bonding properties, or provide additional durability.
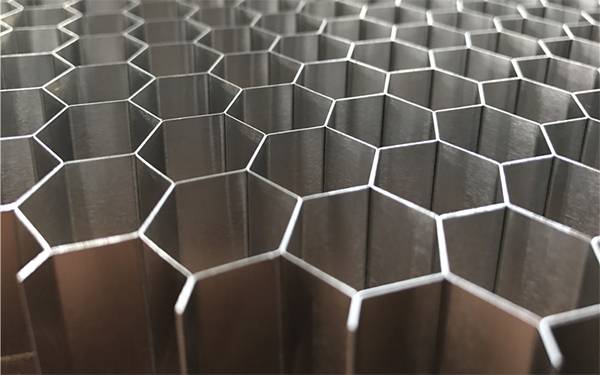
Step-by-Step Manufacturing Process of Aluminum Honeycomb Core
The production of aluminum honeycomb core is a highly precise process that involves multiple stages to ensure structural integrity, strength, and durability. Below is a detailed breakdown of the manufacturing process:
1. Aluminum Foil Preparation
The process begins with selecting high-quality aluminum foil, typically made from 3000 or 5000 series aluminum foils or sheets, known for their excellent strength-to-weight ratio and corrosion resistance. The aluminum foil is cut to the required thickness, usually ranging between 0.02 mm and 0.1 mm, depending on the desired strength and application of the final honeycomb core.
Once cut, the aluminum foil undergoes essential surface treatments to enhance its bonding capability and durability:
- Degreasing: The foil is cleaned to remove oils, grease, and other contaminants that may interfere with adhesion. This step is critical for ensuring a strong and uniform bond between layers.
- Etching: A mild chemical etching process creates a roughened surface, improving the mechanical grip of the adhesive and enhancing the bonding strength between layers.
- Coating (Optional): In applications requiring extra durability, the foil is coated with corrosion-resistant layers such as chromate or epoxy-based coatings to protect against oxidation and environmental damage.
2. Adhesive Application
After surface treatment, an industrial-grade adhesive is applied to the aluminum foil sheets. The adhesive must be carefully selected based on the strength, temperature resistance, and environmental exposure requirements of the final product. The most commonly used adhesives include:
- Phenolic Adhesives: Provide high heat resistance, making them suitable for aerospace and fire-resistant applications.
- Epoxy-Based Adhesives: Offer excellent mechanical strength and resistance to moisture and chemicals, making them ideal for automotive and marine uses.
- Polyurethane Adhesives: Known for their flexibility and impact resistance, often used in construction and transportation applications.
The adhesive is applied in a precise dot or line pattern at regular intervals across the foil. These bonding points determine the cell size and mechanical properties of the final honeycomb structure.
3. Stacking and Pressing
Once the adhesive is applied, multiple layers of aluminum foil are stacked on top of each other in a highly controlled manner. The alignment of layers is crucial to ensuring uniformity and structural consistency.
After stacking, the sheets undergo hot or cold pressing to activate the adhesive and bond the layers into a compact block. The pressing process involves:
- Controlled Pressure Application: Ensures even bonding across all layers.
- Temperature Regulation: If heat-activated adhesive is used, the pressing is done in a heated press to cure the adhesive and form a solid block.
The pressing process creates a rigid, laminated aluminum block that serves as the foundation for the honeycomb expansion stage.
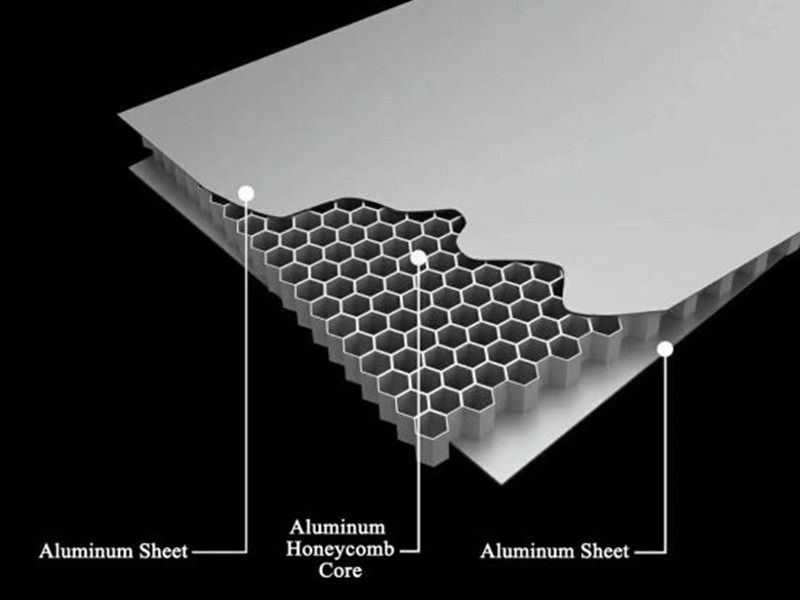
4. Expansion into Honeycomb Structure
Once the adhesive has fully cured, the bonded aluminum block is expanded to form the characteristic hexagonal cell structure of the honeycomb core. Expansion can be carried out using different methods depending on production scale and precision requirements:
- Manual Expansion: Workers physically stretch the block into its honeycomb shape, typically used for small-batch or custom-sized honeycomb cores.
- Mechanical Expansion: Automated machines precisely expand the aluminum block, ensuring high-speed production with consistent and uniform cell geometry.
- Stretching Techniques: Some manufacturers use specialized mechanical stretching tools to gradually pull the layers apart, preventing deformation or misalignment.
During expansion, maintaining cell integrity is crucial, as any misalignment can compromise the final product’s mechanical performance.
5. Cutting and Shaping
After expansion, the honeycomb core is cut into precise dimensions based on its intended application. Cutting is performed using advanced techniques to maintain the uniformity and structural integrity of the honeycomb cells:
- CNC Machining: Ensures high precision and customization for specialized applications.
- Waterjet Cutting: Used for high-strength cores, providing smooth and accurate edges.
- Laser Cutting: Allows for fine detailing and minimal material waste.
Depending on the application, the honeycomb core may undergo additional shaping or customization:
- Curved Forming: The core is bent or shaped to fit specific aerodynamic or architectural designs.
- Perforation: Certain applications require perforated honeycomb cores for airflow or acoustic absorption.
- Edge Trimming: Ensures uniform thickness and clean edges for easy assembly with composite materials.
6. Surface Treatment and Final Processing
Before the aluminum honeycomb core is ready for use, it undergoes final treatments to enhance its durability and suitability for different environments:
- Corrosion Protection: The core may be coated with anodized finishes, epoxy coatings, or anti-corrosion treatments to prevent oxidation and extend its lifespan.
- Fire-Resistant Coatings: For aerospace, marine, and construction applications, fire-retardant coatings are applied to improve flame resistance and compliance with safety standards.
- Lamination: In some cases, the honeycomb core is laminated with fiberglass, carbon fiber, or other composite materials to increase strength, rigidity, and impact resistance.
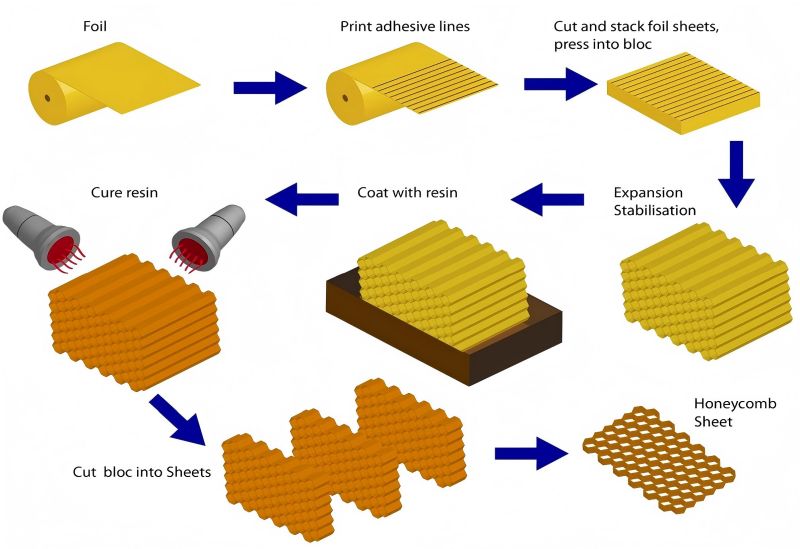
Quality Control and Testing of Aluminum Honeycomb Core
Ensuring the reliability and performance of aluminum honeycomb core requires rigorous quality control measures throughout the manufacturing process. These measures help guarantee structural integrity, durability, and safety, especially for applications in aerospace, automotive, marine, and construction industries, where material failure is not an option. Below are the critical tests performed during and after production to maintain high-quality standards:
1. Mechanical Strength Tests
Mechanical testing is crucial for evaluating the structural performance of the aluminum honeycomb core under different loading conditions. The primary mechanical tests include:
- Compression Test: This test measures the ability of the honeycomb core to withstand axial loads. A sample is subjected to a compressive force until deformation or failure occurs. The results help determine the core’s load-bearing capacity, which is particularly important for aerospace and structural applications.
- Shear Test: Since aluminum honeycomb cores are often used as sandwich panel cores, shear strength is a vital property. This test assesses how well the core material resists shear forces that can cause layers to slide over one another. It is performed by applying parallel forces along the plane of the honeycomb structure.
- Tensile Test: Tensile testing evaluates the material’s resistance to being pulled apart under tension. A sample is stretched until it breaks, and the tensile strength is recorded. This test ensures the honeycomb core can withstand mechanical stress without failing.
2. Dimensional Accuracy and Uniformity Checks
The structural efficiency of aluminum honeycomb depends on the uniformity of its cell size, thickness, and overall dimensions. Some key aspects checked include:
- Cell Size Consistency: The honeycomb core must have uniformly sized and shaped cells to ensure balanced mechanical properties across the entire material. Any variation in cell size can lead to weak points, reducing overall strength.
- Panel Thickness and Flatness: The thickness of the core must remain within strict tolerances to ensure proper bonding with face sheets when used in sandwich panels. Flatness tests verify that the core does not warp or bow, which could compromise its application in high-precision industries.
- Adhesive Bonding Strength: Since adhesives are used in the fabrication of aluminum honeycomb cores, adhesion tests are conducted to ensure the bonding points between aluminum foil layers are strong enough to prevent delamination.
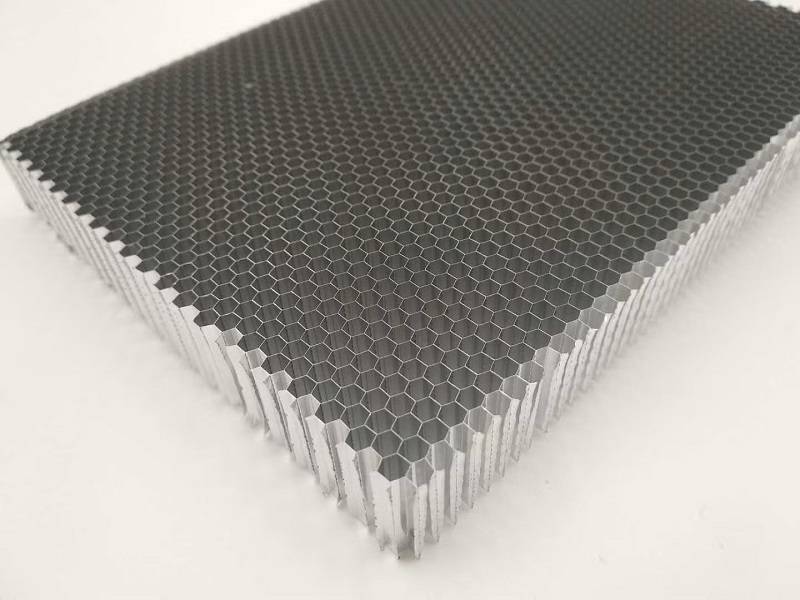
3. Fire Resistance Testing
Fire safety is a critical concern, particularly in aerospace, marine, and construction applications where materials must meet strict fire resistance standards. Fire testing includes:
- Flammability Tests: These tests assess how quickly and easily the aluminum honeycomb core ignites when exposed to open flames. Honeycomb cores often receive fire-retardant coatings to minimize combustion risks.
- Heat Resistance Testing: The core is exposed to high temperatures to determine its ability to maintain structural integrity under extreme conditions. This test is especially vital for aircraft and marine applications, where fire exposure can be catastrophic.
- Smoke and Toxicity Tests: In addition to fire resistance, testing for smoke emission and toxic gas release ensures the core material does not emit harmful fumes when subjected to heat or fire.
4. Environmental Durability Tests
Aluminum honeycomb core is often used in harsh environments, so it must resist degradation from various environmental factors. Key durability tests include:
- Moisture and Humidity Resistance: Exposure to high humidity or direct water contact can lead to corrosion or material degradation over time. This test involves subjecting the honeycomb core to accelerated humidity conditions to evaluate its resistance to moisture absorption and corrosion.
- Chemical Resistance Testing: The aluminum honeycomb core may be exposed to chemicals such as cleaning agents, fuels, lubricants, and solvents in industrial applications. Chemical resistance testing determines whether prolonged exposure weakens the material or causes surface damage.
- UV and Weathering Tests: Outdoor applications require the honeycomb core to withstand prolonged UV radiation and weathering. Accelerated aging tests simulate years of exposure to sunlight, wind, and rain to determine how well the material holds up over time.
Importance of Quality Control in High-Stakes Industries
These rigorous testing procedures are essential for maintaining high-quality standards, especially in industries where failure is not an option. Aerospace manufacturers demand flawless honeycomb cores to ensure aircraft structural components remain lightweight yet incredibly strong. In the automotive and marine industries, these cores contribute to fuel efficiency and safety by providing durable yet lightweight solutions.
By implementing stringent quality control measures, manufacturers can ensure that aluminum honeycomb cores meet or exceed industry standards, offering long-term reliability and optimal performance in even the most demanding applications.
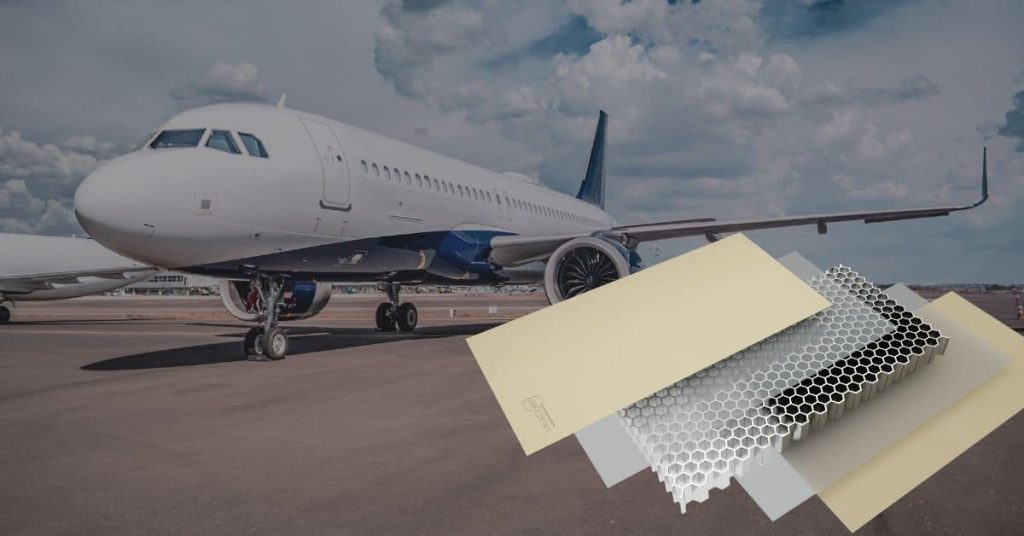
Applications of Aluminum Honeycomb Core
Aluminum honeycomb core is used in a wide range of industries due to its exceptional properties. Some of the key applications include:
Industry | Applications |
Aerospace and Aviation | – Aircraft flooring and interior panels |
– Structural reinforcements in fuselage and wings | |
– Lightweight cargo containers | |
Construction and Architecture | – Facade cladding and curtain walls |
– Lightweight partitions and ceilings | |
– Fire-resistant doors and panels | |
Automotive and Marine | – Lightweight panels for electric vehicles |
– Hull structures and bulkheads in ships | |
– Energy-absorbing crash components | |
Industrial Equipment & Packaging | – Protective enclosures for sensitive equipment |
– Energy-absorbing structures for impact protection | |
– Custom packaging for fragile goods |
In conclusion, aluminum honeycomb core is a versatile material with applications across multiple industries due to its lightweight yet strong structure. The manufacturing process, from aluminum foil preparation to final quality testing, ensures the production of high-performance honeycomb cores. With ongoing advancements in material science and manufacturing techniques, aluminum honeycomb core technology is expected to evolve, offering even better performance, durability, and sustainability in the future.