Seamless aluminum tubes are manufactured using a process called piercing extrusion. In this process, a solid aluminum billet is heated to a high temperature and then forced through a die, which creates a hollow tube. The piercing extrusion process is a complex and precise operation, and there are a number of factors that need to be considered in order to produce a high-quality seamless aluminum tube. These factors include the material properties of the aluminum, the design of the die, and the operating parameters of the extrusion press. In this article, we will delve into the extrusion process of seamless aluminum tubes, outlining the key steps involved and the additional factors that need to be considered for successful production.
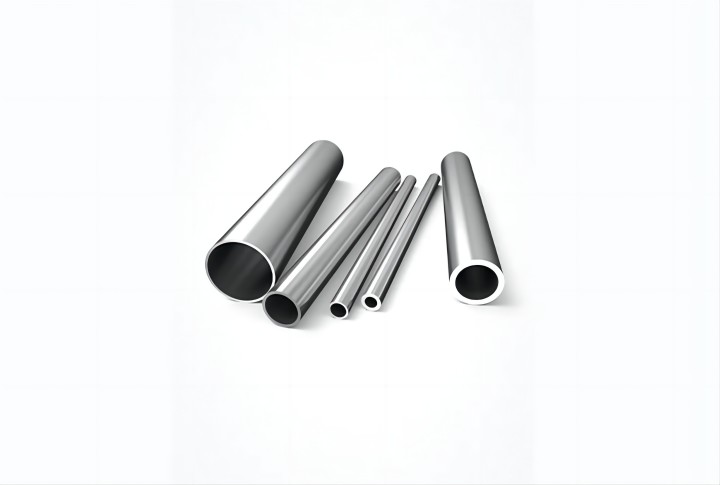
The Main Extrusion Process of Seamless Aluminum Tube
The main steps involved in the extrusion process of seamless aluminum tubes are as follows:
- Material preparation
The first step is to prepare the aluminum billet. The billet is typically made from a high-quality aluminum alloy that has been heat-treated to improve its strength and ductility. The billet is then machined to a precise size and shape to ensure that it will fit properly in the die.
- The material properties of the aluminum alloy will affect the ease of extrusion and the final properties of the tube. For example, harder alloys will require higher extrusion pressures and may be more prone to defects.
- The size and shape of the billet will also affect the extrusion process. For example, larger billets will require more time and energy to extrude.
- Heat treatment
The next step is to heat the billet to a high temperature. The temperature of the billet will vary depending on the alloy that is being used. The goal of the heat treatment is to make the aluminum soft and ductile so that it can be easily deformed during the extrusion process.
- The heat treatment temperature will need to be carefully controlled to ensure that the aluminum is not overheated. Overheating can cause the aluminum to become brittle and difficult to extrude.
- Extrusion into modeling
The billet is then placed in the die and the extrusion press is activated. The press applies a high pressure to the billet, which forces it through the die. The die is shaped to create the desired cross-section of the tube.
- The extrusion pressure will need to be carefully controlled to ensure that the aluminum is not deformed too much. Overextrusion can cause the tube to become thin and weak.
- The die design is critical to the success of the extrusion process. The die must be properly shaped to create the desired cross-section of the tube. The die must also be made from a high-quality material that can withstand the high temperatures and pressures of the extrusion process.
- Cooling
The extruded tube is then cooled to room temperature. The cooling process helps to solidify the aluminum and prevent it from becoming brittle.
The cooling rate will need to be carefully controlled to ensure that the aluminum does not become too brittle. Too rapid cooling can cause the aluminum to become brittle and crack.
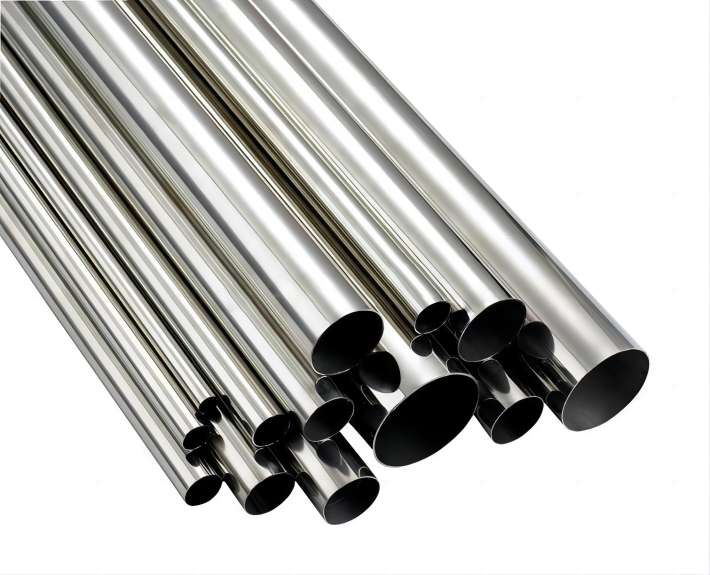
- Finishing
The cooled tube is then finished to remove any burrs or imperfections. The finishing process may involve machining, grinding, or polishing.
- The finishing process will help to improve the appearance of the tube and make it more resistant to corrosion.
- Marking
The finished tube is then marked with the manufacturer’s information and other relevant data. The marking process may involve stamping, laser engraving, or hot stamping.
- The marking process will help to identify the tube and its manufacturer.
- Other steps
There are a number of other steps that may be involved in the extrusion process of seamless aluminum tubes. These steps may include annealing, straightening, or heat treatment.
- Annealing is a heat treatment process that is used to soften the aluminum and improve its ductility.
- Straightening is a process that is used to correct any bends or distortions in the tube.
- Heat treatment is a process that is used to improve the strength and hardness of the aluminum.
Additional Factors to be Considered
In addition to the main steps listed above, there are a number of additional factors that need to be considered in the extrusion process of seamless aluminum tubes. These factors include the following:
- Mold design
The design of the die is critical to the success of the extrusion process. The die must be properly shaped to create the desired cross-section of the tube. The die must also be made from a high-quality material that can withstand the high temperatures and pressures of the extrusion process.
- Equipment precision
The accuracy and precision of the extrusion press is also important. The press must be able to apply the correct amount of pressure to the billet and the die must be properly aligned. Any errors in the press or the die can result in defects in the finished tube.
- Quality inspection standards
The quality of the finished tube must be carefully inspected to ensure that it meets the required standards. The inspection process may involve visual inspection, dimensional measurements, and mechanical testing.
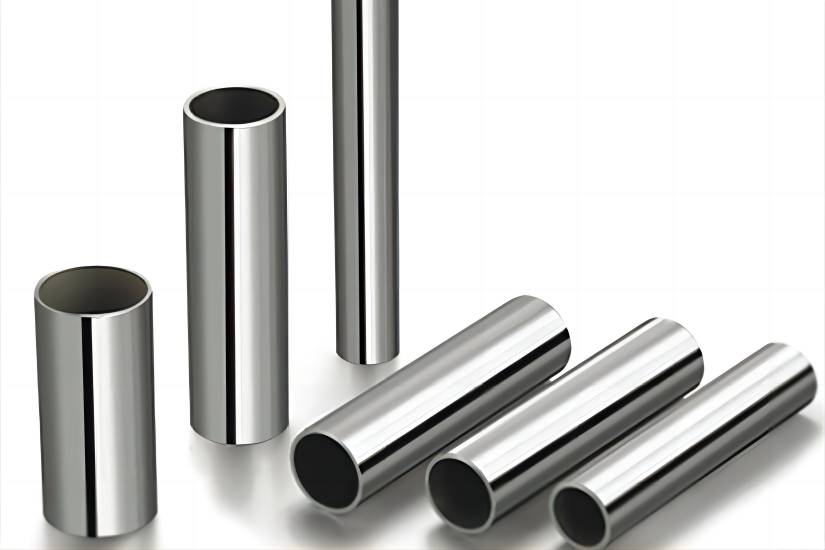
Summary
The extrusion process of seamless aluminum tubes is a complex and precise operation. There are a number of factors that need to be considered in order to produce a high-quality seamless aluminum tube. These factors include the material properties of the aluminum, the design of the die, and the operating parameters of the extrusion press.
The extrusion process of seamless aluminum tubes is a versatile process that can be used to produce a wide variety of tubes. The tubes can be used in a variety of applications, including the automotive, aerospace, and construction industries. If you are looking for seamless aluminum tube supplier in China, CHAL is a leading aluminum products manufacturer providing high-quality products and services, contact us and we will give you kindly and professional service.