The automotive industry is undergoing a significant transformation, driven by the urgent need to reduce carbon emissions and reliance on fossil fuels. Electric vehicles (EVs) have emerged as a sustainable alternative to traditional internal combustion engine vehicles. However, one of the major challenges in EV development is improving energy efficiency and range. Lightweighting has become a critical strategy to address this challenge.
Aluminum alloy has become the preferred lightweight material for electric vehicles due to its light weight, high strength, good corrosion resistance and recyclability. This article explores how aluminum alloys, with their unique properties, play a pivotal role in promoting the lightweighting of electric vehicles, enhancing their performance, and contributing to a greener future.
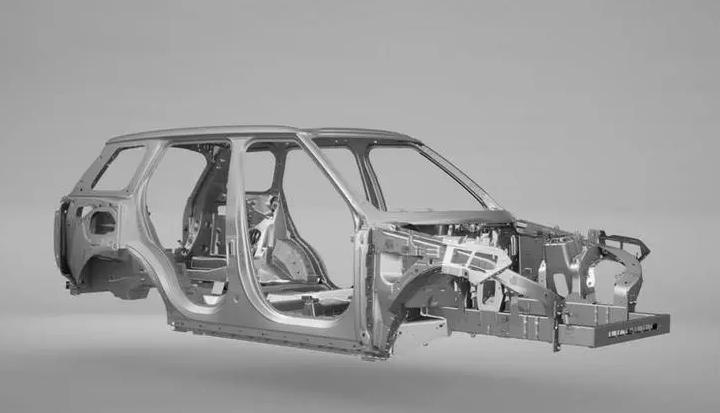
How to Realize Lightweighting in EVs?
Lightweighting is a key technology path to improve the energy efficiency, cruising range and dynamic performance of electric vehicles. By using aluminum alloys instead of traditional steel components, electric vehicles can achieve significant weight savings without sacrificing safety.
Lightweight can be achieved by optimizing structural design, using lightweight materials, and adopting efficient and reliable forming technology, connection technology, and surface treatment technology. The application of aluminum alloy materials can directly reduce the weight of components, and at the same time improve the lightweight level of the overall vehicle through structural optimization and advanced manufacturing processes.
- Design Optimization: Utilizing advanced design techniques like topology optimization and finite element analysis to minimize material usage while maintaining strength.
- Multi-material Solutions: Replacing heavier materials with lighter alternatives such as aluminum alloys. Combining different materials (e.g., aluminum, carbon fiber, high-strength steel) to exploit the best properties of each.
- Advanced Manufacturing: Employing techniques such as additive manufacturing and hydroforming to create complex, lightweight components.
Realizing lightweighting in EVs requires a holistic approach, combining material science, engineering design, and manufacturing technologies. Aluminum alloys are a key player in this strategy due to their favorable properties and versatility.
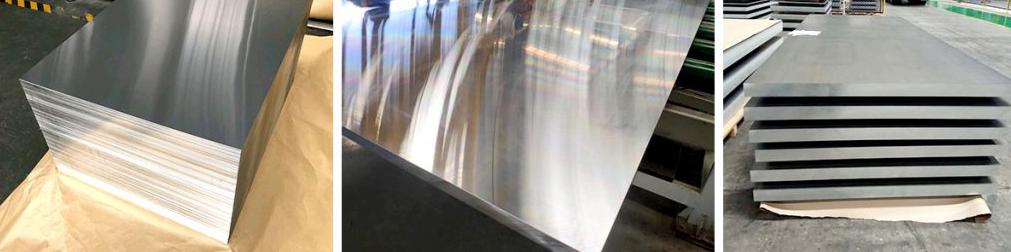
How Do Aluminum Alloys Contribute to Lightweighting?
Among the various materials considered for lightweighting, aluminum alloys have emerged as a top choice due to their unique combination of properties. The following detailed analysis explores the specific ways in which aluminum alloys contribute to lightweighting in EVs.
1. Strength-to-Weight Ratio
One of the most significant contributions of aluminum alloys to lightweighting is their high strength-to-weight ratio. This ratio is a measure of how much load a material can bear relative to its weight, making it a critical factor in vehicle design.
- High Strength: Aluminum alloys, such as 6061 and 7075, exhibit high tensile strength, which allows them to replace heavier materials like steel in various structural components. For example, AA7075 has a tensile strength of around 590 MPa, making it suitable for load-bearing applications while still being significantly lighter than steel.
- Low Density: Aluminum’s density is approximately 2.7 g/cm³, which is about one-third that of steel (7.85 g/cm³). This low density means that aluminum components can weigh significantly less than steel components while maintaining similar strength levels. The reduced weight contributes to overall vehicle lightweighting, which in turn improves efficiency and range.
2. Corrosion Resistance
Aluminum alloys are inherently resistant to corrosion, which is a crucial property for long-term durability and safety in vehicles. This resistance is due to the formation of a natural oxide layer on the aluminum surface, which protects it from environmental factors such as moisture, salt, and other corrosive agents.
- Longevity: The corrosion resistance of aluminum alloys reduces the need for additional protective coatings and treatments, which can add weight and complexity to the vehicle design. By using aluminum, manufacturers can achieve lightweight without compromising on the longevity and durability of the vehicle.
- Maintenance: Corrosion-resistant materials like aluminum reduce the frequency and cost of maintenance, further enhancing the overall efficiency and lifecycle performance of the vehicle.
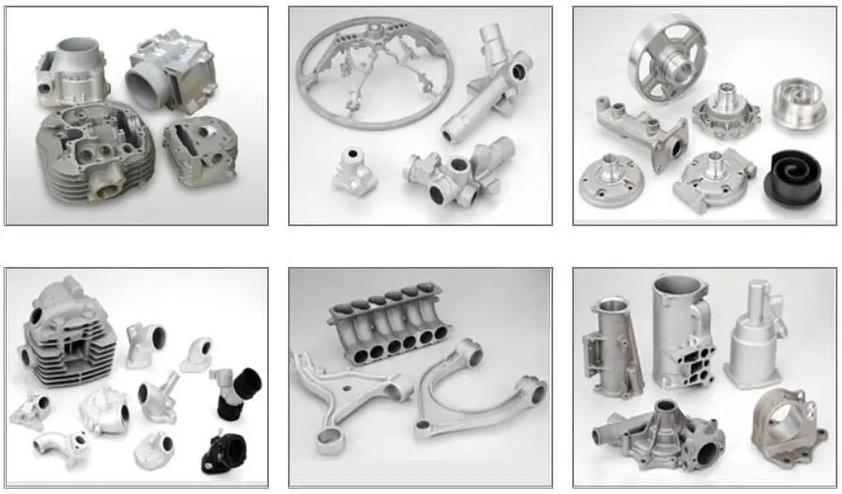
3. Thermal Conductivity
Aluminum alloys are excellent conductors of heat, which is particularly beneficial in EV applications where efficient thermal management is crucial.
- Battery Enclosures: Aluminum is widely used in battery enclosures for EVs because it effectively dissipates heat generated by the battery pack. This prevents overheating and ensures that the battery operates within the optimal temperature range, which is essential for maintaining battery efficiency and longevity.
- Cooling Systems: Aluminum’s high thermal conductivity (around 235 W/m·K for pure aluminum) is also utilized in the cooling systems of electric motors and power electronics, where lightweight, efficient heat dissipation is necessary to avoid thermal degradation and ensure consistent performance.
4. Manufacturability and Versatility
The manufacturability of aluminum alloys is another key factor that contributes to lightweighting. Aluminum alloys can be processed using various techniques, such as extrusion, casting, and sheet forming, allowing for the creation of complex, lightweight components.
- Extrusion: Aluminum can be extruded into complex shapes, which allows for the integration of multiple functions into a single component. This reduces the need for additional parts, thereby lowering the overall weight of the vehicle.
- Casting: Aluminum alloys are easily castable, enabling the production of intricate shapes that would be difficult or impossible to achieve with other materials. This flexibility allows for design optimization, which can reduce material usage and, consequently, vehicle weight.
- Sheet Forming: Aluminum sheets can be formed into body panels that are both lightweight and strong. This is particularly beneficial for EVs, where every kilogram saved can contribute to improved range and efficiency.
5. Recyclability and Sustainability
Aluminum is highly recyclable, and recycled aluminum retains virtually all the properties of the original material. This recyclability contributes to lightweighting in several ways:
- Reduced Material Costs: Recycling aluminum requires only about 5% of the energy needed to produce primary aluminum from ore. This energy efficiency reduces production costs, making it economically viable to use aluminum in more vehicle components.
- Environmental Impact: The use of recycled aluminum in vehicle manufacturing reduces the carbon footprint associated with material production. Given that aluminum can be recycled indefinitely without losing its properties, it aligns with the broader goals of sustainability in the automotive industry.
6. Data-Driven Insights
Weight Reduction Potential: According to the Aluminum Association, replacing traditional steel components with aluminum can reduce a vehicle’s weight by up to 50%. For example, an aluminum-intensive vehicle can weigh around 500 kg less than a comparable steel-intensive vehicle, leading to a significant improvement in energy efficiency.
Range Improvement: A study by the International Council on Clean Transportation (ICCT) found that for every 10% reduction in vehicle weight, the range of an EV can be increased by approximately 6-8%. This means that a 100 kg reduction in weight could result in a range increase of around 10%, highlighting the direct impact of aluminum alloys on vehicle performance.
Aluminum alloys provide an optimal balance of properties, cost-effectiveness, and recyclability, making them the preferred choice for lightweight in EVs.
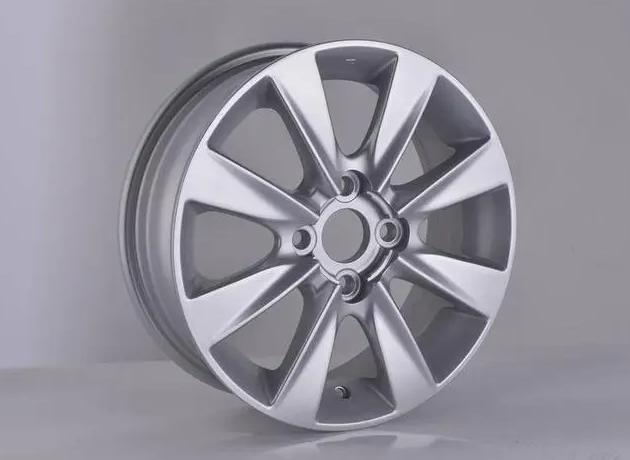
Applications of Aluminum Alloys in EVs
The application of aluminum alloy in the body structure of electric vehicles is mainly reflected in the following aspects:
- Body covering parts: Aluminum alloy is often used to make body covering parts of electric vehicles, such as doors, hoods, trunk lids, etc., due to its light weight and high strength, which helps to reduce the weight of the whole vehicle and improve energy efficiency and driving performance.
- Body frame: The application of aluminum alloy in the body frame includes the use of high-strength aluminum alloy materials to manufacture the supporting structure of the body, such as front longitudinal beams, side beams, and cross beams. These structures can provide good strength and rigidity when subjected to impact while maintaining low weight.
- Chassis and suspension system: The application of aluminum alloy in the chassis and suspension system can improve the dynamic performance and ride comfort of the vehicle. For example, control arms and steering knuckles made of aluminum alloy can reduce non-suspension mass and improve handling response.
- Wheel: Aluminum alloy wheels are lighter than traditional steel wheels, which can reduce rotational inertia, thereby improving acceleration performance and fuel economy. In addition, aluminum alloy has good heat dissipation performance, which helps to cool the braking system and improve safety.
- Battery packs and other structural components: Aluminum alloys are also used to manufacture battery pack housings and other structural components of electric vehicles, which need to protect the battery from external impact and provide sufficient structural strength.
The use of aluminum alloys can not only improve the performance of electric vehicles but also help to achieve lightweight design, thereby extending the range of electric vehicles, which is in line with the current development trend of the electric vehicle industry for energy conservation, emission reduction, and energy efficiency.
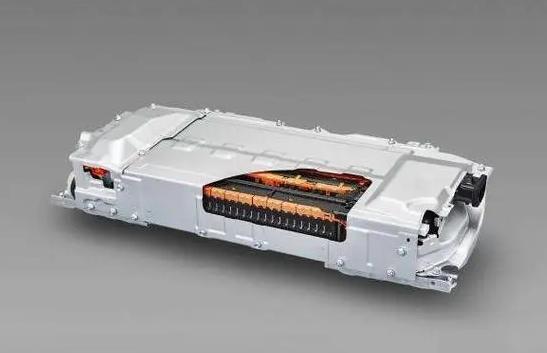
If you are interested in our aluminum products for your projects, please contact our sales department, and we will reply to you within 24H.