Aluminum alloy plate is a kind of industrial building material. It is used in various industries according to different materials. According to the surface treatment method, it can be divided into two categories: non-painted products and painted products.
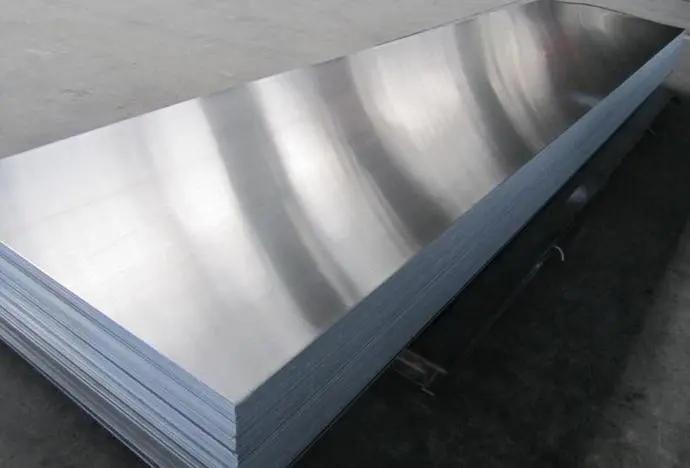
In the process of aluminum plate manufacturing, the problem of uneven aluminum plates often appears. This is because the plane Angle of the aluminum sheet has not been corrected. In this paper, the factors affecting the flatness problem are summarized and based on this, the solution to the flatness problem is formulated.
The plane angle of the aluminum sheet was improved by modifying the model
Mold repair is the most common solution to the poor flatness of extruded materials. The advantage of this method is a wide range of applications, basically, all extrusion materials can use this treatment method. Its disadvantage is that the production needs to be terminated. After the mold is handled well, the machine will try the mold again, which is time-consuming and laborious and is not conducive to energy saving and consumption reduction.
The poor plane clearance of the aluminum plate is mainly related to the uneven flow rate of the die. By changing the size or Angle of the diversion pit, or the working belt’s length, the metal flow rate can be effectively adjusted to a uniform flow rate and eliminate the defects of poor plane clearance.
This kind of plate is generally used in the early stage of production. Some molds can be repaired once to solve the flatness problem, and some molds need three or even more times to completely solve the flatness problem. This is not only related to the mold itself but also has a greater relationship with the technical level of the mold workers.
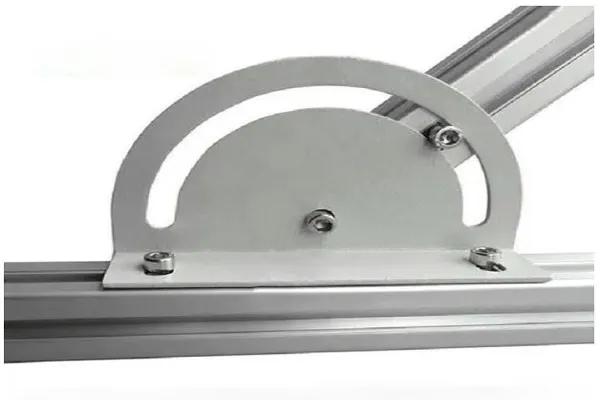
Use offline finishing to correct the flatness of the product
First of all, according to the characteristics of the specific flatness of the plate, the roller of the off-line finishing machine is reasonably configured. Then a product with flatness is selected for the fixed roll.
By constantly adjusting the height and position of the roller, when the flatness of the product qualified, fixed the height and position of the roller, and then the batch of products off-line finishing. Off-line finishing is generally time-consuming and laborious, but also easy to bring a certain impact on the appearance of products.
On-line finishing is used to correct the flatness of the product
If the order quantity is relatively large, if the off-line finishing is adopted, it will greatly reduce production efficiency and waste a lot of manpower. So after a period of discussion and exploration and combining the principle of offline finishing, the engineers put forward the concept of online finishing and decided to make an online finishing device.
If successful, it will not affect production efficiency and will save a lot of manpower. This method is based on the principle of finishing offline, in the original extruder exit guide device is mounted on the basis of bearing and roller, by adjusting the height and position of the roll sheet to change the size of the pressure on products a certain amount of deformation in the products, to make products of flatness control in a reasonable range, so as to achieve the purpose of finishing online.