High-frequency welding is a widely used technique for producing aluminium welded tubes and HFW pipes. This process involves heating the edges of the tube with high-frequency current, followed by pressure application to create a strong, seamless weld. While the method is efficient and cost-effective, several quality-related problems can arise, impacting the performance and longevity of the final product. This article delves into the common quality issues faced during the production of aluminium HFW pipes and provides strategies for ensuring their consistent performance.

Common Quality Issues in Aluminium HFW Pipes
Production of high-frequency welded tubes involves precise control over parameters like power, pressure, and welding speed. Any deviation can lead to defects that compromise the structural integrity of the tube. Here are the most common quality issues encountered in aluminium HFW pipes in the following table.
Issue | Manifestation | Causes | Solutions |
Welding Weakness | Weld seam detachment, cold laps | Insufficient power output and extrusion pressure | Adjust welding power, modify groove shape, fine-tune extrusion pressure |
Weld Seam Ripple | Ripples along both sides of the weld | Excessive fusion angle | Correct guide roll positions, modify forming sections, increase welding speed |
Deep Pits and Pinholes | Craters or pinholes in the weld seam | Overheating during welding | Adjust power, increase fusion angle, regulate welding speed |
Weld Burrs | Excessive burrs at the weld seam | Overly wide heat-affected zone | Enhance welding speed, adjust power output |
Inclusions (Slag) | Impurities within the weld seam | Excessive power, slow welding speed | Regulate power, optimize welding speed |
Surface Cracks | Cracks on the external weld surface | Poor base material quality, excessive extrusion pressure | Use high-quality materials, optimize extrusion pressure |
Weld Misalignment and Overlapping | Misaligned or overlapping welds | Poor forming precision | Improve forming roller accuracy, adjust machine setup |
Porosity | Gas pores in the weld | Absorption of hydrogen during molten state | Optimize welding parameters to reduce hydrogen absorption |
Weld Leakage | Leaks at the weld seam | Irregular longitudinal cuts, poor welding parameter control | Enhance longitudinal slitting process, optimize welding parameters |
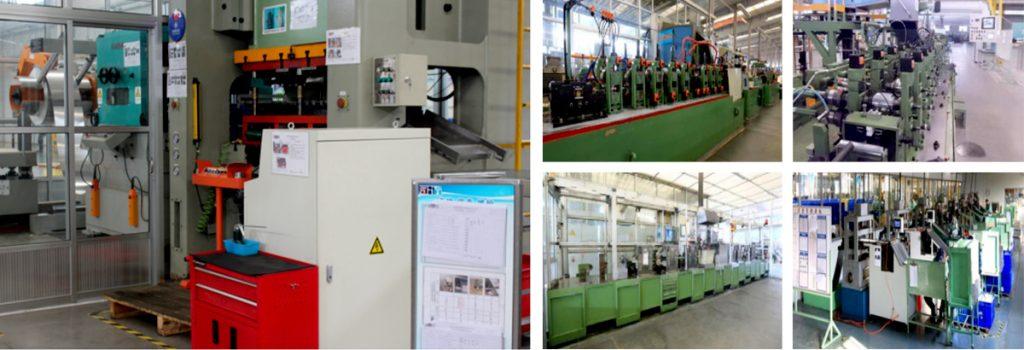
Strategies for Ensuring Welding Quality in Aluminium HFW Pipes
To produce high-quality aluminium HFW pipes, manufacturers must adopt comprehensive strategies that address every aspect of the production process.
1. Raw Material Quality Control
Quality assurance begins with selecting the right raw materials.
- Chemical Composition: Ensure that the aluminium alloy’s chemical composition meets industry standards. Different alloys may require customized welding parameters to achieve optimal results.
- Mechanical Properties: Test the raw material for properties such as tensile strength and yield strength to ensure it can withstand the welding process without deforming.
- Surface Quality: Aluminium tube blanks should be free of oil, oxidation, and other contaminants to promote strong welds.
2. Welding Equipment and Parameter Optimization
High-frequency welding relies on sophisticated machinery, and proper equipment calibration is critical for consistent quality.
- Welding Machine Selection: Choose high-frequency welding machines suited to the tube’s material, diameter, and thickness.
- Impedance Control: Ensure that the impedance settings align with the tube’s diameter. The impedance coil should have a 6-15 mm gap from the inner wall, with larger diameters requiring greater distances.
- Extrusion Pressure: Calculate and apply appropriate extrusion pressure based on the tube’s wall thickness. For example, thinner walls require less pressure, while thicker walls may demand increased extrusion to ensure a seamless weld.
3. Welding Process Improvements
The welding process must be fine-tuned to reduce defects and improve efficiency.
- Groove Design: Keep welding groove angles below 60° and welding gaps between 1-2 mm. Combining a small groove angle with a narrow gap can minimize stress concentration and enhance weld strength.
- Oxidation Layer Removal: Clean the oxidation layer from the weld area to ensure a defect-free joint.
- Gas Shielding: Use inert gas protection, such as argon, to create a stable welding atmosphere and prevent oxidation.
4. Real-Time Welding Process Control
Continuous monitoring during welding ensures consistent quality.
- Temperature Control: Maintain welding temperatures based on the aluminium alloy’s melting and softening points. Adjust temperature settings dynamically to avoid overheating or underheating.
- Welding Speed: Avoid extremes in welding speed. Excessively fast welding can lead to incomplete fusion, while slower speeds may cause overheating and slag formation.
5. Post-Welding Inspection and Evaluation
Comprehensive inspection after welding ensures that only defect-free tubes proceed to the next stage.
- Visual Inspection: Examine weld seams for visible defects like cracks, ripples, and burrs.
- Radiographic Testing: Use X-rays or gamma rays to identify internal flaws, such as inclusions or porosity, that are not visible externally.
- Mechanical Performance Tests: Conduct tensile, impact, and hardness tests to assess the strength and ductility of the weld seam.
- Metallographic Analysis: Analyze the microstructure of the weld and heat-affected zone to identify any abnormalities that could affect performance.
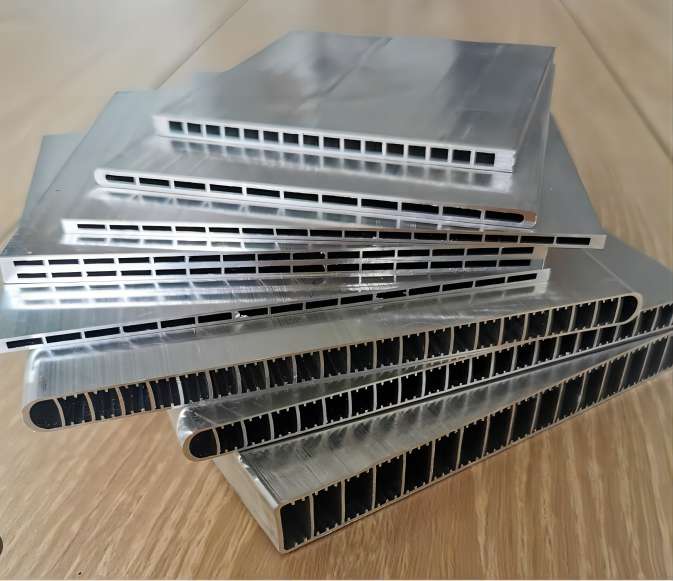
Producing high-quality aluminium HFW pipes requires meticulous attention to detail across all stages of production. By understanding and addressing common quality issues, manufacturers can enhance the structural integrity, reliability, and overall performance of their products. Strategies such as ensuring raw material quality, optimizing welding parameters, and conducting rigorous post-welding inspections are essential for achieving superior results.
High-frequency welded tubes play a critical role in modern industries, and with the right practices, their production can meet even the most demanding applications, providing long-lasting value and efficiency.
If you want to know more about high frequency welded aluminium tubes, you are welcome to feel free to contact us.