Aluminum profiles, versatile and durable, are widely used in various industries, from construction and automotive to aerospace and electronics. To ensure optimal performance and longevity of your projects, it’s crucial to identify high-quality aluminum profiles. Here we will delve into the key indicators of high-quality aluminum profiles, effective inspection techniques, common quality issues, and practical tips for ensuring quality to help you make informed decisions.
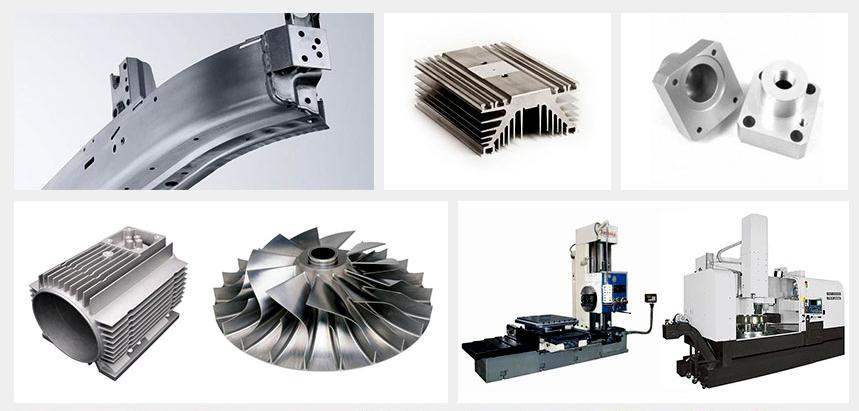
Key Indicators of High-Quality Aluminum Profiles
1. Material Composition
The alloy composition of an aluminum profile significantly impacts its strength, corrosion resistance, and workability. High-quality profiles are made from specific aluminum alloys tailored for different applications.
Common high-grade alloys, such as 6061 and 6063, are used in structural applications due to their strength and resistance to corrosion. Each alloy has specific proportions of elements like magnesium, silicon, and zinc, which give it unique properties. Ensuring the profile is made from a high-quality alloy suitable for its intended application is the first step in identifying quality. High-quality material composition ensures the aluminum profile meets industry standards for durability and performance, which translates into better product reliability.
2. Surface Finish
A high-quality surface finish enhances both the appearance and protective qualities of an aluminum profile, making it a crucial factor to consider.
Common finishes include anodizing, which improves corrosion resistance and surface hardness, and powder coating, which adds a protective, decorative layer. A uniform surface, free of blemishes or discoloration, usually indicates a high-quality finish. Poor finishing, such as uneven coating thickness or peeling, may indicate substandard production processes.
3. Dimensional Accuracy
Precise dimensions are critical for aluminum profiles, especially in applications requiring exact fitting or structural stability.
High-quality profiles are manufactured with tight tolerances to ensure dimensional accuracy, which is necessary for easy assembly and structural integrity. Profiles that deviate from standard dimensions may indicate quality control issues and could lead to misalignment or compromised safety.
4. Strength and Durability Testing
Ensuring an aluminum profile’s mechanical strength and durability is key to its performance in load-bearing and high-stress environments.
Tests such as tensile strength and hardness tests measure the profile’s ability to withstand stress without deformation. High-quality profiles undergo rigorous testing to ensure they meet the necessary strength and durability standards for their intended applications.
After we learn about the key indicators, let’s find the methods to inspect aluminum profiles.
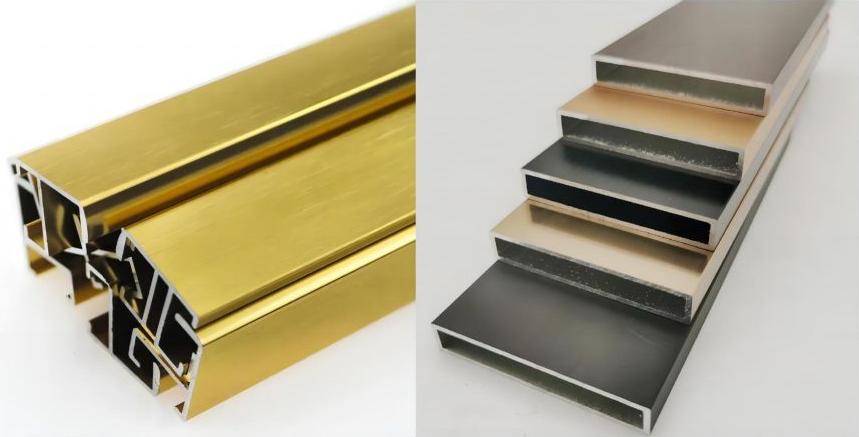
Inspection Techniques for Aluminum Profiles
Ensuring the quality of aluminum profiles involves a variety of inspection techniques that assess their structural and aesthetic properties. These techniques help identify issues with material composition, surface integrity, and internal defects. By conducting proper inspections, manufacturers and users can confirm that the profiles meet the required standards and perform well in their applications. Here are several key inspection methods:
Technique 1: Visual Inspection
Visual inspection is often the first step in evaluating an aluminum profile’s quality, as it reveals surface issues and obvious defects.
During visual inspection, look for signs of uniformity in color, absence of scratches, and dents, and a consistent surface finish. Profiles that show visible imperfections may have been improperly processed or handled, indicating potential issues with overall quality.
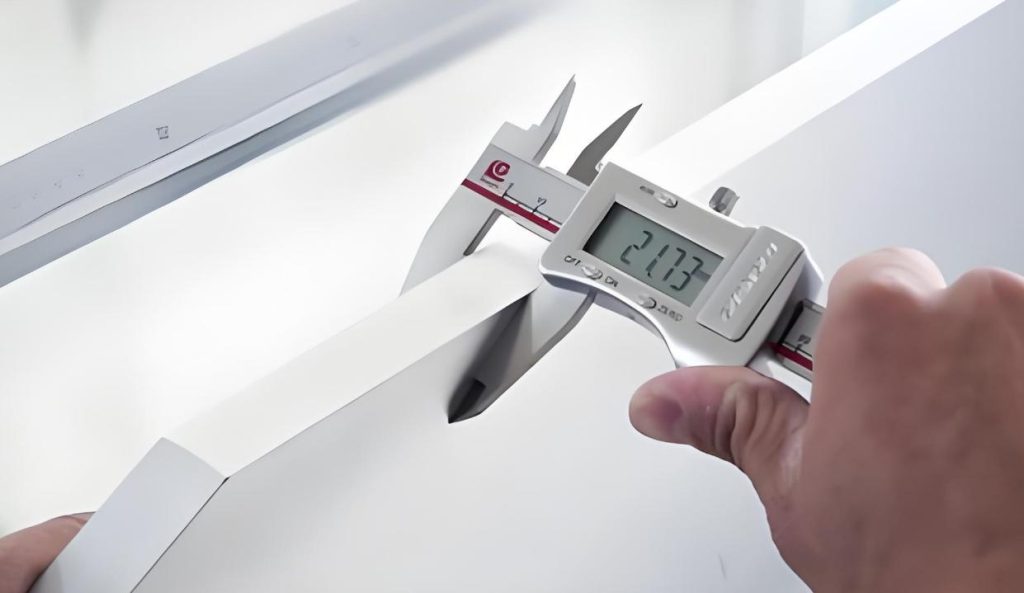
Technique 2: Chemical Analysis
Chemical analysis allows you to confirm the alloy composition, ensuring that the profile meets specified standards.
Techniques like spectroscopy can reveal the exact chemical composition of an aluminum profile, verifying that it matches the desired alloy specifications. If the composition deviates from what’s expected, it may indicate quality issues or potential performance deficiencies.
Technique 3: Mechanical Testing
Mechanical testing evaluates an aluminum profile’s physical properties to ensure it can withstand the intended application’s demands.
Common mechanical tests include tensile strength, yield strength, and hardness testing. These tests measure the profile’s ability to resist deformation, handle loads, and endure wear, which are essential for structural applications. Mechanical testing provides concrete data on an aluminum profile’s performance capabilities, verifying it meets industry standards for strength and durability.
Technique 4: Non-Destructive Testing (NDT)
Non-destructive testing (NDT) identifies internal flaws without damaging the profile, making it an essential part of quality inspection.
Techniques such as ultrasonic testing can detect internal cracks, voids, or other defects that may compromise strength. NDT ensures the profile’s structural integrity without affecting its usability, making it a valuable tool for quality assessment.
Comprehensive inspection techniques, from visual checks to advanced testing methods, play a vital role in confirming the quality of aluminum profiles. By using these approaches, manufacturers and end-users can identify and address potential issues early, ensuring profiles meet the required standards for strength, durability, and aesthetic value.
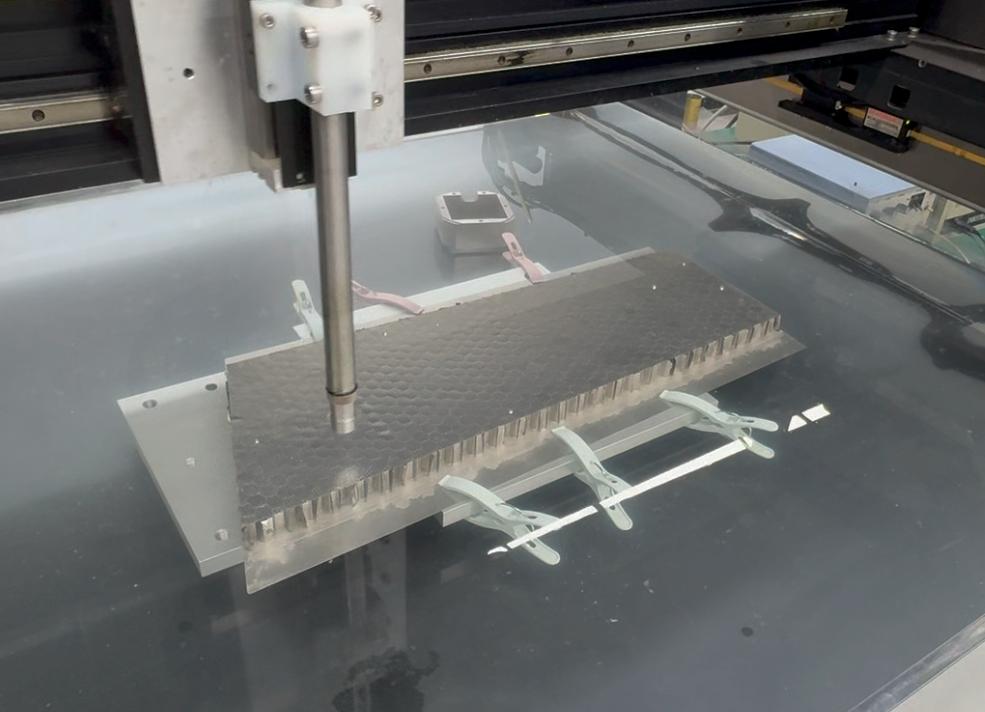
Common Quality Issues and How to Spot Them
Even with high manufacturing standards, aluminum profiles can sometimes exhibit quality issues that may affect their performance, appearance, or durability. Being aware of common defects, such as corrosion susceptibility, warping, and poor surface finishes, allows users to recognize and address these problems before they impact the project. Typical quality issues are:
Issue 1: Corrosion Susceptibility
Corrosion can compromise the performance and appearance of aluminum profiles, especially in environments with high moisture or chemical exposure. Detecting early signs of corrosion can prevent long-term issues.
How to Spot: Low-quality aluminum or inadequate surface finishing may increase the profile’s susceptibility to corrosion. Inspect for signs of discoloration, pitting, or early signs of rust, especially in profiles used outdoors or in challenging environments.
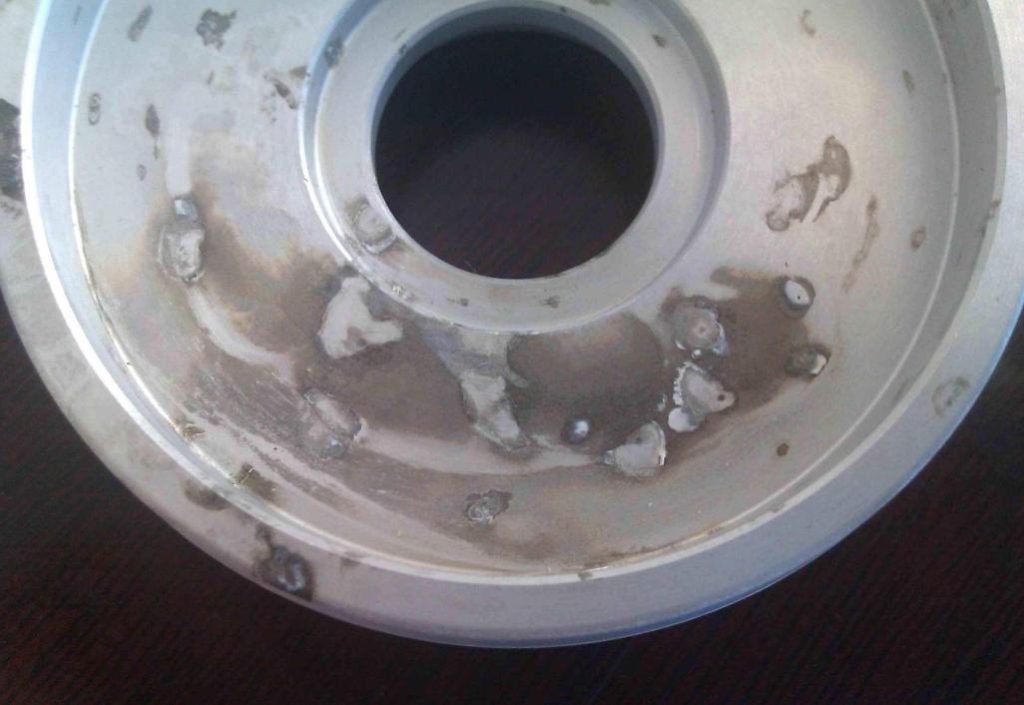
Issue 2: Warping and Inconsistency
Warping and dimensional inconsistencies can impact an aluminum profile’s fit and functionality, particularly in applications that require precision and uniformity.
How to Spot: Warping may result from improper manufacturing or handling. Visually inspect for irregular shapes or deviations from standard dimensions, as these can compromise the structural integrity and assembly of the profile.
Spotting warping early can prevent misalignment issues and ensure compatibility with other components in construction or assembly, making it easier to maintain quality and functionality.
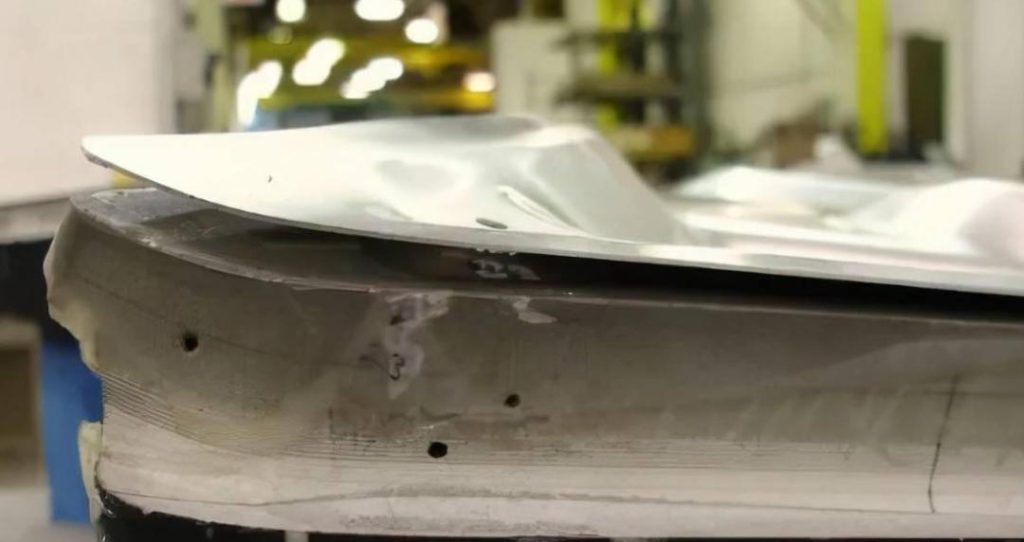
Issue 3: Poor Finish and Coating
A poor finish not only affects the profile’s appearance but may also reduce its resistance to wear and environmental factors. Identifying coating defects is crucial for applications that require visual appeal and durability.
How to Spot: Look for signs such as peeling, bubbling, or inconsistent coating thickness. These issues indicate inadequate finishing processes, which can lead to reduced durability and poor protection against corrosion.
Recognizing common quality issues such as corrosion, warping, and poor finishing helps prevent performance and aesthetic concerns in aluminum profiles. By identifying these problems early, users can make informed decisions and maintain quality standards, ensuring profiles meet the demands of their specific applications.
Practical Tips for Quality Assurance
Consistently ensuring the quality of aluminum profiles requires proactive quality assurance practices. By adopting reliable sourcing, regular inspections, and advanced testing methods, businesses can avoid the risks associated with low-quality materials and defective profiles.
- Source Reputable Suppliers: Working with reputable suppliers is one of the most important steps in maintaining quality standards for aluminum profiles. High-quality suppliers follow strict production and quality control protocols, reducing the risk of defects.
- Conduct Regular Inspections: Regular inspections, whether visual or more detailed, help catch inconsistencies or flaws before profiles are used in projects. Establishing a systematic inspection process is key to maintaining high-quality standards over time.
- Utilize Laboratory Testing: Laboratory testing adds a layer of precision to quality assurance by verifying an aluminum profile’s composition and performance attributes under controlled conditions. Tests such as chemical analysis, mechanical testing, and corrosion resistance assessments provide detailed insights into the profile’s quality. Laboratory testing is particularly beneficial for applications requiring strict adherence to material and strength standards.
Identifying the quality of aluminum profiles involves evaluating several factors, from material composition and surface finish to structural integrity and inspection practices. By understanding these key indicators, utilizing effective inspection techniques, spotting common quality issues, and following practical quality assurance tips, you can ensure that the aluminum profiles you use are reliable, durable, and fit for purpose. Investing in high-quality aluminum profiles ultimately leads to safer, longer-lasting applications, ensuring both the project’s and end users’ satisfaction.