Due to the epidemic, the demand for aluminum foil has been rising all over the world. However, due to the shadow of the production process, some defects in aluminium foil often occur. What defects will occur in the process of rolling aluminum foil? How can we avoid these defects?
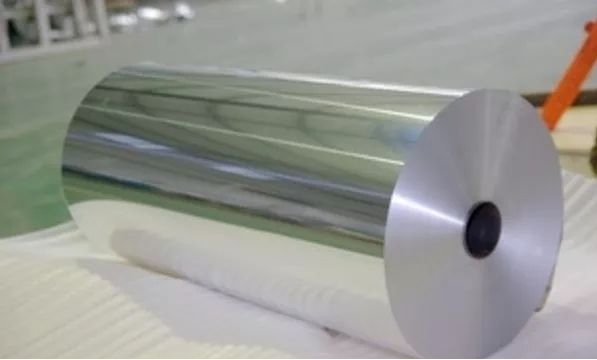
Why is aluminum foil the best food heating material?
Because of its excellent properties, aluminium foil is widely used in food, beverages, cigarettes, medicines, photographic plates, household daily necessities, etc.. And it is usually used as its packaging material, electrolytic capacitor material, thermal insulation material for buildings, vehicles, ships, houses, etc.. It can also as decorative gold and silver thread, wallpaper and various stationery prints and decoration trademarks of light industrial products, etc.
Among the above-mentioned various uses, the one that can most effectively exert the performance points of aluminum foil is as a packaging material. Aluminium foil is a soft metal film, which not only has the advantages of moisture resistance, air tightness, shading, abrasion resistance, fragrance preservation, non-toxic and tasteless, etc. but also because of its elegant silver-white luster, it is easy to process beautiful patterns and patterns of various colors. pattern, so it is more likely to be favored by people.
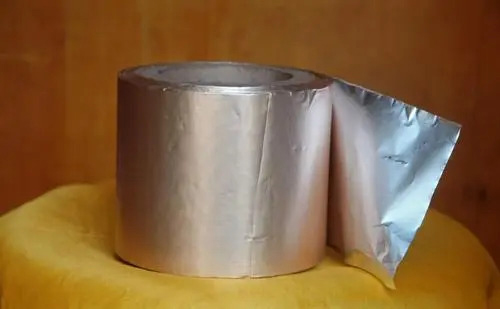
Especially after the aluminum foil is compounded with plastic and paper, the shielding properties of aluminium foil are integrated with the strength of paper and the heat sealing property of plastic, which further improves the shielding properties of moisture, air, ultraviolet rays and bacteria, which are necessary as packaging materials. , greatly broadening the application market of aluminium foil.
Since the packaged items are fully isolated from the outside light, humidity, gas, etc., the packaged items are well protected. Especially for the packaging of cooked food, the use of this composite aluminum foil material can at least ensure that the food does not deteriorate for more than one year. Moreover, heating and unpacking are very convenient, which is very popular among consumers.
With the improvement of people’s living standards and the development of tourism, the demand for beverages and canned foods such as beer and soda is increasing, which requires modern packaging and decoration to facilitate competition in the international market.
Is the aluminum foil on the market still mainstream?
To meet the market requirements, people have developed packaging materials such as plastic films and sprayed foils with good shielding properties, but their comprehensive properties are not as good as overcoating, and lamination can be compensated and improved. Therefore, it can be said that aluminium foil is a perfect packaging material with a variety of excellent properties, and it has fully shown its broad application prospects in many fields.
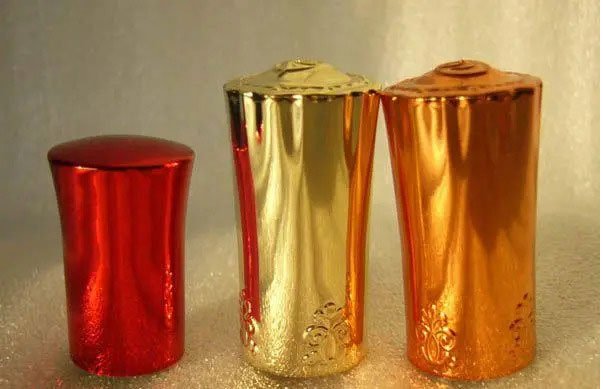
To improve the rolling efficiency and the quality of aluminum foil products, modern aluminium foil rolling mills are developing in four directions: large-roll, wide-width, high-speed, and automation. The width of the roll body of the contemporary aluminum foil rolling mill has reached more than 2200mm, the rolling speed has reached more than 2000m/min, and the coil weight has reached more than 20t. The automation level of the corresponding rolling mill has also been greatly improved, and the thickness control system (AGC) is generally installed, and most of them are installed with a shape meter (AFC). The aluminium foil industry is facing a period of rapid development.
What is the cause of coiling defects in aluminum foil?
Coiling defects mainly refer to the loose coil, channeling layer, tower shape, edge warping, etc. of the aluminum foil during the coiling process of the finished product. Since the tension of the aluminium foil is limited, sufficient tension is the condition for forming a certain tension gradient.
Therefore, the coiling quality ultimately depends on a good plate shape, reasonable process parameters, and a sleeve with suitable precision, and it is ideal to obtain a coil that is tight inside and outside.
- Unwinding
Because the winding is not tight, when the foil is extracted along the direction of the tube core, the foil is free to fall off in a cylindrical shape; or local depression occurs when the foil is pressed with fingers.
The main reasons for loose rolls are too small or uneven tension during slitting; too fast slitting speed; too low pressure on the flattening roller.
- Channeling layer
The surface layer of the aluminum foil roll is irregular between the layers, causing the end surface to be uneven.
The main reasons for staggered layers are uneven billet; improper adjustment of coiling tension; improper adjustment of flattening rollers; abnormal centering system during coiling; too fast during rolling or slitting.
- Tower shape
The channeling layer between the aluminium box end surface layer and the layer causes the tower shape offset, which is called the tower shape. The tower shape is a special case of channeling.
The main reasons for the tower shape are: the shape of the incoming material is not good; the adjustment system is abnormal during coiling; the flattening roller is improperly adjusted; the coiling tension is improperly adjusted.
- Edge warping
The phenomenon that both ends or one end of the aluminium foil roll are lifted upwards is called edge warping.
The main reasons for the generation of a navy: are excessive reduction, poor plate shape; uneven distribution of lubricating oil; improper adjustment of the cutting edge.