Aluminum and aluminum alloys are turned into finished aluminum products and semi-finished products by melting and casting. In the process of melting and casting, various degrees of loss will occur due to oxidation, refining, slag removal, etc., resulting in irrecoverable metal loss and aluminum slag.
The general calculation formula of casting loss is: (the amount of primary aluminum – the number of finished products) ÷ the amount of primary aluminum × 100%, the higher the casting loss, the less the finished product, so how to effectively reduce the casting loss is very important.
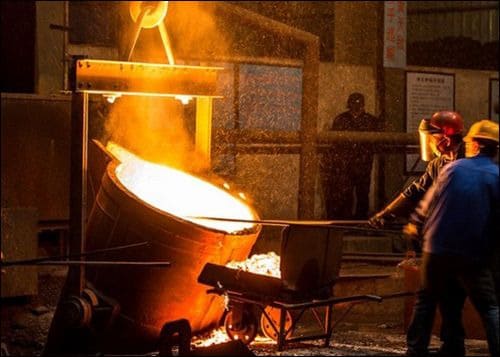
Causes of aluminum alloy casting damage
The main external manifestations of casting damage can be divided into two parts: one is in the form of pure aluminum ash, and the other is in the form of large pieces of aluminum, defective aluminum, and aluminum slag. Among them, the non-recyclable pure aluminum ash accounts for about 90% of the casting loss, and other factors account for about 10%. Other factors are mainly caused by the secondary burning loss of large pieces of aluminum alloy and defective aluminum alloy and the content of aluminum alloy in the aluminum alloy ash. Therefore, the main reasons for the internal casting damage are oxidation burning loss, secondary burning loss such as defective aluminum, and aluminum ash.
Factors affecting casting loss
① liquid aluminum temperature;
② Contact strength of molten aluminum and oxygen;
③ Aluminum content in aluminum slag;
④The molten aluminum brought out by slag skimming;
⑤ The amount of defective aluminum and bulk aluminum;
⑥Other losses.
7 ways to reduce casting loss
1. Control the temperature of liquid aluminum.
The melting point of aluminum is 660°C. Generally speaking, the casting temperature of primary aluminum is controlled at about 730°C or even lower, while the aluminum alloy has better fluidity and the corresponding casting temperature is lower than that of primary aluminum, about 710°C-730°C. The temperature of molten aluminum is effectively reduced to the corresponding casting temperature, which can reduce the huge influence of temperature on casting loss.
2. Reduce the contact strength of molten aluminum and air.
(1) Reduce the contact time between liquid aluminum and oxygen. Under the condition that the production needs are met, the liquid aluminum in the furnace should be turned into finished products as soon as possible. It is best to produce on-duty ingredients on duty, and not let the liquid aluminum stay in the furnace for too long; reasonably arrange the casting equipment and shorten the length of the laundering as much as possible. , to reduce the exposure time of liquid aluminum in the air, and at the same time, an aluminum silicate insulation board can be added to the upper part of the launder, which not only has a certain insulation effect but also reduces the oxygen content in the launder.
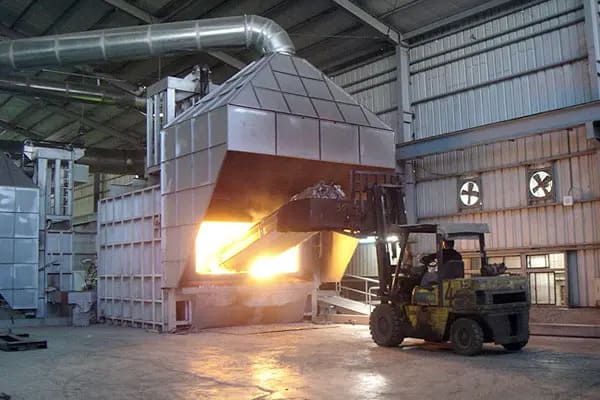
(2) Control the stirring mode of liquid aluminum.
Stirring with the furnace door open will not only bring about huge fluctuations in the liquid level and increase the contact area with oxygen, but also increase the oxygen content in the furnace, accelerate the chemical reaction, and increase the burning loss. Electromagnetic stirring can be carried out in a closed state and the liquid level fluctuation is small, which effectively avoids the corresponding disadvantages. At the same time, it can also reduce the moisture in the air entering the furnace and reduce the absorption probability of liquid aluminum to hydrogen.
3. Control the height of the bubble blowing.
The general refining method is to manually sprinkle the refining agent into the furnace, and then perform stirring and refining. However, for some alloy production, nitrogen-blowing refining is required (the refining time is longer, up to about 30 minutes), and there must be a certain blowing height. , which drives the huge fluctuation of liquid aluminum, so it is best to adjust the nitrogen pressure and control the blowing height to 10-15mm.
4. Correctly select and use the refining agent to fully separate the slag and aluminum.
In the smelting process of aluminum and aluminum alloys, in addition to their inclusions, aluminum can easily form alumina or sub-alumina with oxygen, resulting in a layer of scum on the surface of the molten aluminum.
In addition to using the flux produced by the flux factory, it is best to adjust the proportion of the flux components according to the composition of the aluminum alloy being smelted. At the same time, the refining process conditions are strictly controlled, such as the amount of flux, the contact time between the flux and the melt, the contact area, the stirring situation, and the temperature.
5. Effectively deal with the aluminum slag produced.
Aluminum slag is an inevitable part of the melting and casting process. Although relevant measures are taken, a certain proportion of metal aluminum will be taken out, which needs to be effectively treated. Screening is carried out to effectively recover part of the aluminum beans.
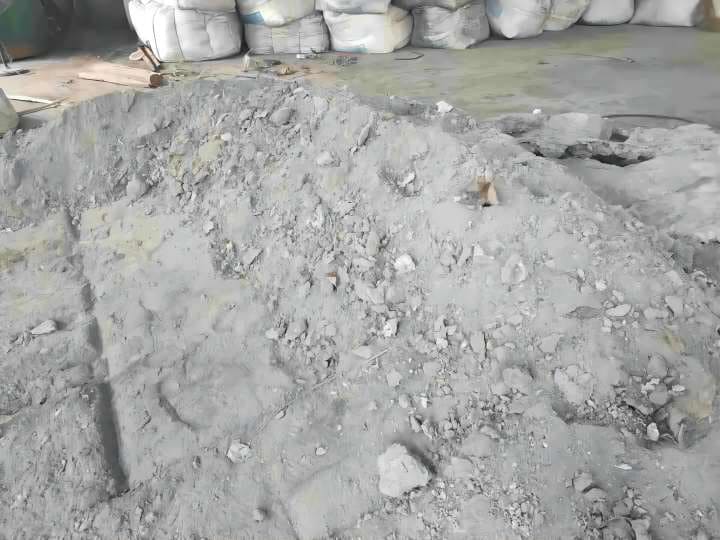
6. Strictly control the quality of slag removal to prevent liquid aluminum from being brought out.
The existing slag scraping operation uses a large rake to scrape the aluminum slag out of the door of the furnace. During this operation, in addition to requiring personnel to operate carefully, try not to bring out the molten aluminum. At the same time, the design of the large rake also needs to be carefully considered. Several rows of small round holes are opened on the surface of the rake so that the liquid aluminum contained in the aluminum slag can flow into the furnace, otherwise, too much liquid aluminum will be brought out and returned to the furnace again, which will cause burning damage.
7. Reduce the amount of defective aluminum and bulk aluminum.
In the production process, operate in strict accordance with the process requirements to ensure that one furnace is produced and one furnace is qualified. Especially in the process of producing ordinary aluminum, try to avoid the generation of defective aluminum such as flash, burr, corrugation, and weight inconsistency. Before the end, push the liquid aluminum in the launder as much as possible into the mold to form a qualified product to reduce the amount of large aluminum.
Summary
Although casting loss is inevitable in the melting and casting process, controlling the temperature of the molten aluminum, reducing the contact strength between the molten aluminum and the air, controlling the aluminum content in the aluminum ash, and reducing the amount of defective aluminum, the casting loss in the melting and casting process can be effectively reduced. , will produce significant effects, and will certainly bring considerable economic benefits to the enterprise.