Hydrophilic aluminum foil is a game-changing material widely used in industries such as air conditioning, refrigeration, and packaging. Known for its unique properties and versatility, it significantly improves efficiency, durability, and environmental safety. This article delves into the definition, features, and applications of hydrophilic aluminum foil while highlighting its advantages over standard aluminum foil.
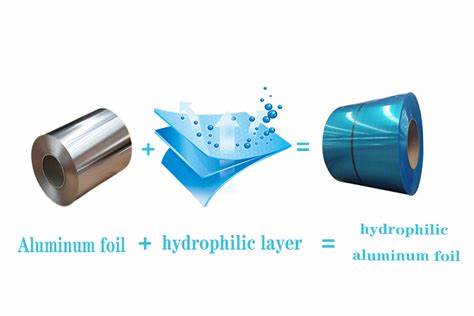
What Is Hydrophilic Aluminum Foil?
Hydrophilic aluminum foil is aluminum foil that has undergone a specialized treatment to coat its surface with a hydrophilic layer. This layer, applied using advanced technologies, allows water to spread evenly across the surface instead of forming droplets. This unique feature enhances heat exchange efficiency, accelerates cooling or heating, and minimizes noise caused by obstructed airflow.
This material plays a critical role in the heat exchangers of air conditioning systems, directly influencing their overall performance. Compared to untreated aluminum foil, hydrophilic aluminum foil can increase cooling efficiency by up to 5% while offering additional benefits such as anti-corrosion and anti-mold properties, making it indispensable in modern applications.
Key Features of Hydrophilic Aluminum Foil
Hydrophilic aluminum foil boasts an array of advanced features that set it apart from conventional aluminum foil:
- Hydrophilic and Anti-Corrosion Properties: The hydrophilic coating on the aluminum foil enables rapid dispersion of condensation water across its surface, preventing the formation of water droplets. This not only increases the heat exchange area but also ensures smooth airflow without resistance. Additionally, the coating provides excellent protection against corrosion, which is essential for maintaining the longevity of air conditioning systems operating in humid or corrosive environments.
- Superior Formability and Durability: During manufacturing, hydrophilic aluminum foil exhibits excellent formability, maintaining its shape without causing wear and tear on processing molds. This property makes it highly suitable for intricate applications, ensuring consistent quality during production.
- Resistance to Environmental Stress: Hydrophilic aluminum foil is resistant to various forms of environmental stress, including stamping oils, solvents, and high temperatures. These properties ensure that the material performs reliably in diverse conditions, maintaining its integrity and functionality across different applications.
- Enhanced Heat Exchange Efficiency: By preventing water droplet formation, the hydrophilic layer reduces airflow resistance, enabling efficient air circulation. This can improve heat exchange rates by 10% to 15%, making it a superior choice for air conditioning and refrigeration systems.
- Exceptional Barrier Properties: Hydrophilic aluminum foil is an excellent barrier against oxygen, moisture, and odors when used in packaging. These characteristics help preserve the freshness, flavor, and quality of packaged products, making them ideal for sensitive items such as food, beverages, and pharmaceuticals.
- Eco-Friendly Characteristics: Hydrophilic aluminum foil is an environmentally friendly material. In air conditioning systems, it prevents the release of harmful oxidized aluminum particles into indoor spaces, safeguarding human health and aligning with environmental standards.
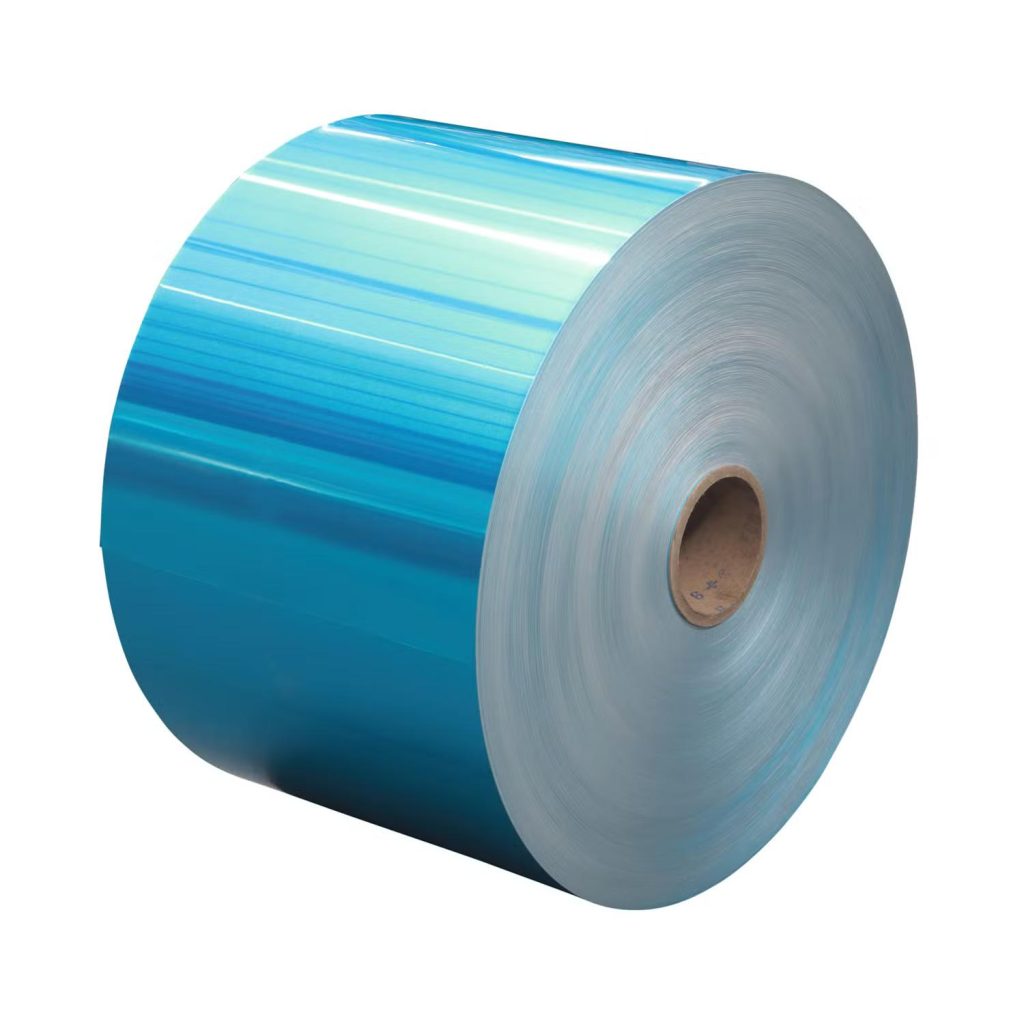
Differences in Manufacturing Processes: Hydrophilic Aluminum Foil vs. Standard Aluminum Foil
The production processes for hydrophilic aluminum foil and standard aluminum foil differ primarily in the additional surface treatment steps required for hydrophilic properties. Below is a comparison of the two processes:
Production Steps | Standard Aluminum Foil | Hydrophilic Aluminum Foil |
Raw Material Preparation | High-purity aluminum ingot | High-purity aluminum ingot |
Melting | Heating to liquid state | Heating to liquid state |
Rolling | Multiple rolls to required thickness | Multiple rolls to required thickness |
Annealing | Stress relief, improves ductility | Stress relief, improves ductility |
Surface Treatment | Chemical cleaning, mechanical polishing | Degreasing, cleaning, drying, coating with anti-corrosive and hydrophilic coatings |
Cutting and Packaging | Cut and packaged as required | Cut and packaged as required |
As shown in the table, the key difference lies in the surface treatment stage. Hydrophilic aluminum foil undergoes additional steps, including degreasing, cleaning, drying, and coating with both anti-corrosive and hydrophilic coatings. These steps are crucial for imparting unique hydrophilic and corrosion-resistant properties to the foil.
Moreover, the manufacturing process of hydrophilic aluminum foil may include specialized techniques such as the dual-coat dual-bake process, which enhances both its hydrophilicity and corrosion resistance. This extra processing ensures superior performance and durability under various conditions.
In comparison, standard aluminum foil lacks these specialized treatments, making it more susceptible to water droplet accumulation, corrosion, and reduced heat exchange efficiency.
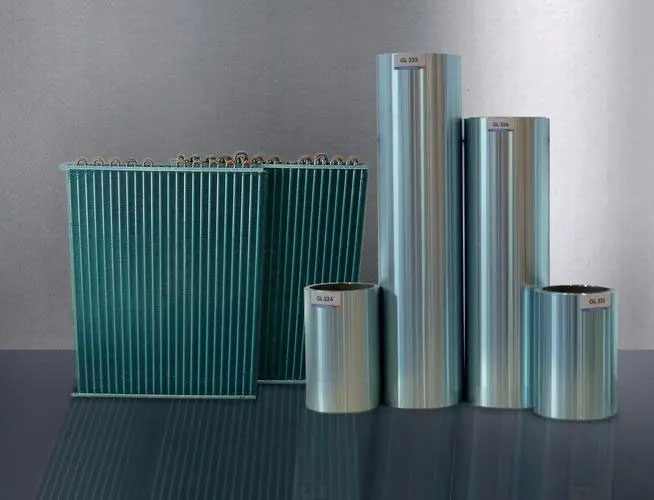
Applications of Hydrophilic Aluminum Foil
The versatility of hydrophilic aluminum foil makes it an essential material across various industries:
1. Air Conditioning Systems
Hydrophilic aluminum foil is a primary material for heat exchanger fins in air conditioning units, refrigeration systems, and automotive air conditioners. Its unique properties provide numerous advantages over standard aluminum foil:
- Increased Cooling Efficiency: The material can enhance the cooling performance of air conditioners by 5%.
- Mold and Odor Prevention: The anti-mold and odor-resistant properties ensure cleaner, fresher air.
- Noise Reduction: By preventing water droplet accumulation, it reduces vibration-induced noise.
- Environmental Compliance: It eliminates the risk of oxidized aluminum particles entering indoor environments.
2. Packaging Industry
The packaging sector benefits greatly from the superior barrier properties of hydrophilic aluminum foil. Its applications include:
- Food and Beverage Packaging: The foil preserves the freshness and taste of food and beverages by blocking oxygen and moisture. It also serves as an insulator for hot and cold drinks, maintaining their temperature for longer periods.
- Pharmaceutical Packaging: Hydrophilic aluminum foil is used to protect medications from environmental factors, ensuring their efficacy and safety.
- Electronics Packaging: The material provides moisture resistance and thermal stability, making it suitable for electronic components.
3. Specialized Applications
Beyond air conditioning and packaging, hydrophilic aluminum foil is used in scenarios requiring high resistance to moisture and corrosion, such as in industrial heat exchangers and advanced insulation systems.
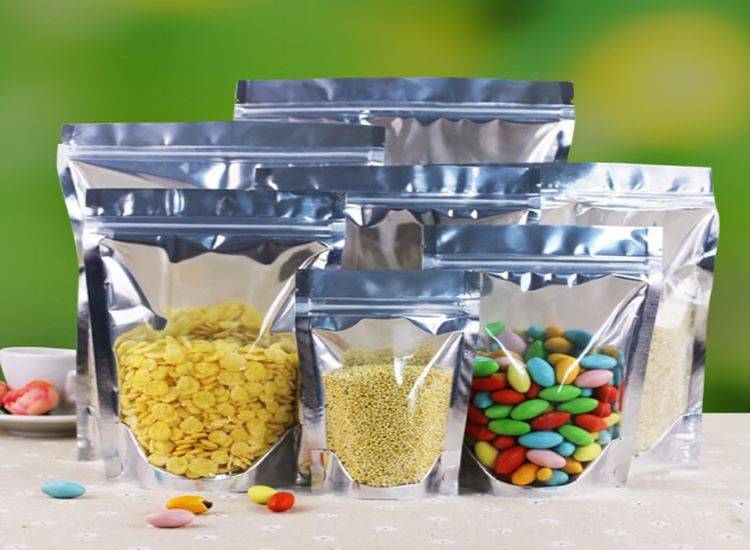
Where to Find Hydrophilic Aluminum Foil
When sourcing hydrophilic aluminum foil, quality and reliability are essential to ensure optimal performance. One of the leading suppliers in this domain is CHAL, a trusted provider of aluminum products known for their superior manufacturing processes and commitment to excellence.
CHAL offers a wide range of hydrophilic aluminum foil options tailored to meet diverse industrial and commercial needs. Their products are designed to meet the highest standards of efficiency, durability, and environmental safety. Customers can benefit from:
- Customized Solutions: CHAL provides tailored specifications to meet unique requirements for heat exchangers, packaging, and more.
- Exceptional Quality: With state-of-the-art technology, CHAL ensures consistent quality and performance.
- Global Distribution: CHAL’s extensive network allows it to supply hydrophilic aluminum foil to clients worldwide.
For industries seeking reliable materials to enhance efficiency and sustainability, CHAL is an excellent choice. Their expertise and dedication to innovation make them a leader in the aluminum foil market. Welcome to feel free to contact us.