Among the wrought aluminum alloys used today, the most widely used is the 6000 series alloys that can be strengthened by heat treatment, which are a class of Al-Mg-Si and Al-Mg-Si-Cu alloys.
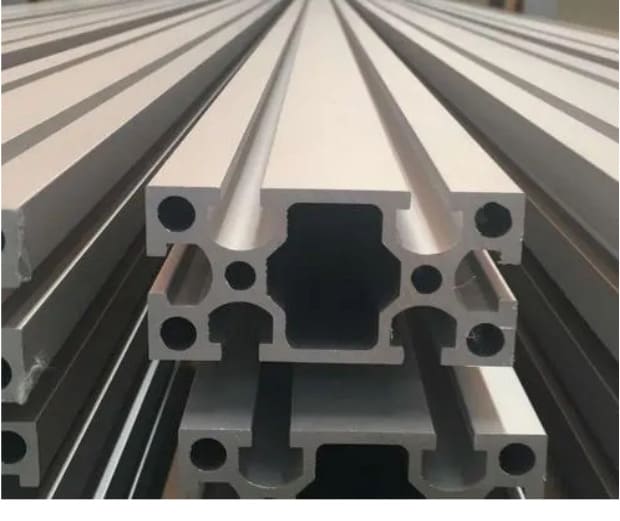
In 2018, there were 706 common and uncommon alloys registered with The Aluminum Association, Inc., of which 6000 series alloys were the most, with 126, accounting for 18%, in the construction industry, structural fields, and transportation. Equipment has been widely used because they have good formability, moderate strength, and excellent corrosion resistance.
However, if the alloy composition ratio is not appropriate, the heat treatment parameters are not properly selected, or the processing and forming are not appropriate, intergranular corrosion will occur in a chlorine-containing environment.
In most cases, intergranular corrosion occurs in alloys with a small amount of copper and high Si/Mg. Usually, the copper content of most copper-containing alloys is not more than 0.4%, and only 4 alloys such as 6013, 6113, 6056, and 6156. The copper content is as high as 1.1%, and copper is added to the Al-Mg-Si alloy to improve the mechanical properties of the alloy.
The study found that all alloys with intergranular corrosion susceptibility were often found to have copper-rich segregation layers and cathodic Q-phase precipitates when observed with high-resolution scanning transmission electron microscopy. The Q phase is a quaternary intermetallic phase with a molecular formula of Cu2Mg8Si5Al4, which precipitates along the grain boundary, causing anodic dissolution of the adjacent solid solution to form a precipitate-free zone.
Intergranular corrosion susceptibility test
There are two commonly used test methods to determine the intergranular corrosion susceptibility of aluminum alloys: field test and accelerated immersion test.
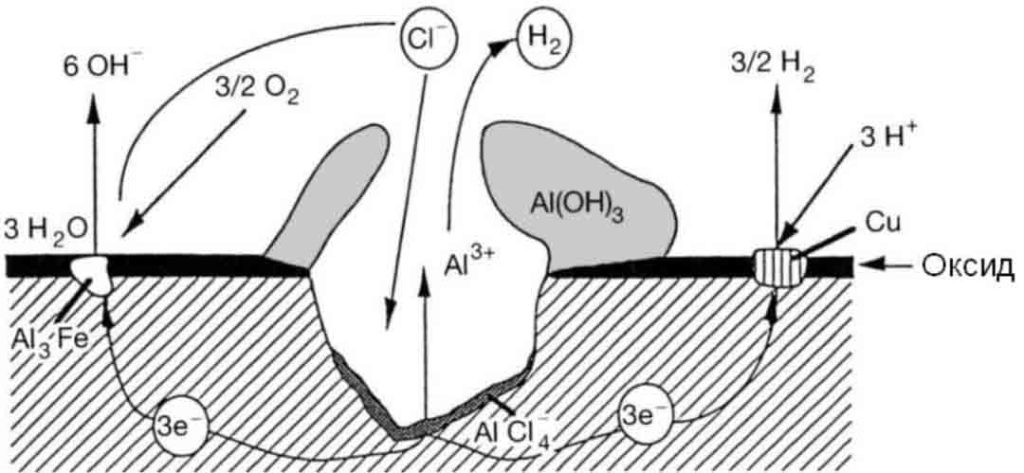
In accelerated testing, to accelerate corrosion, potassium chloride solution containing hydrochloric acid (ISO 11846 Method B) or potassium chloride solution with hydrogen peroxide (ASTM G110) are often used. After the test, the metallographic observation of the cross-section of the sample or the measurement of the loss of its mechanical properties.
The ISO 11846 accelerated test results are in high agreement with the marine atmosphere field test results, but the intergranular corrosion-susceptible aluminum exhibits severe corrosion at almost all grain boundaries near the surface of the sample during the accelerated test (uniform intergranular corrosion). ), whereas the surface of the field test specimens corroded only in limited areas (localized corrosion).
Nonetheless, accelerated testing remains the standard method for accurately determining whether a material has grain boundary corrosion.
The automotive industry often judges whether 6000 series aluminum alloys have intergranular corrosion according to the ISO 11846 Method B standard. When testing according to this standard, first fully immerse a small sample (surface area < 20cm2) in an acidic sodium chloride solution (pH=1) at room temperature for 24 hours, and then perform a metallographic examination to determine the type of corrosion (pitting or intergranular). Corrosion), in addition to determining the percentage of corrosion-damaged surfaces and the maximum corrosion depth.
Recent studies have shown that allowing some large changes in test conditions does not have a large impact on the reproducibility of test results. In particular, the standard stipulates that the ratio of the electrolyte volume to the surface area of the sample shall not be less than 5mL/cm2, otherwise the intergranular corrosion rate will be greatly affected.
The condition for corrosion on the surface of the sample is that there must be a cathodic reaction (hydrogen evolution, oxygen reduction), the pH value of the test solution increases with time, and the electrolyte corrosion decreases.
Among the 8 series deformed aluminum alloys, the 6000 series alloy is a kind of Al-Mg-Si (Cu, Zn) alloy, which is one of the alloys most prone to intergranular corrosion. Intermittent corrosion susceptibility.
To test the intergranular corrosion tendency of 6000 series alloys, one of the most effective methods is to carry out alkaline solution etching after the ISO 11846 standard test and then carry out decontamination treatment. A concentrated nitric acid solution is used for decontamination treatment. However, etching in a NaOH solution with a temperature of 50~60℃ and a mass fraction of 5%~10% for 2~5min will affect the test results.
An effective alternative to alkali etching is the use of a nitric/hydrofluoric acid solution, which effectively removes aluminum from iron-rich protoplasmic spots on the surface. It is known that aluminum particles can accelerate the corrosion of aluminum alloys in chloride solutions, because they are local microscopic cathodes, and these particles are also the origin of intergranular corrosion. Alloys corrode slower in nitric/fluoride solutions than in lye.
The above is the content of intergranular corrosion of 6000 series aluminum alloys organized by CHAL.