Internally threaded aluminum tubes play a crucial role in numerous applications, from fluid and gas conveyance systems to structural components and heat exchangers. Its lightweight nature, inherent corrosion resistance, and excellent machinability make it a preferred choice across industries. This article delves into the technical aspects of processing these tubes, providing a comprehensive overview of material selection, threading methodologies, and post-processing considerations.
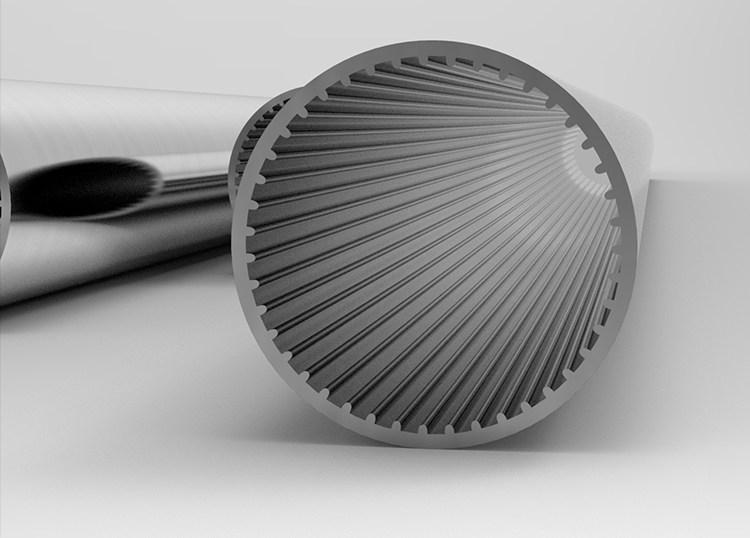
Material Selection and Considerations for Internally Threaded Aluminum Tubing
The successful fabrication of internally threaded aluminum tubing depends on meticulously selecting the optimal material based on a holistic evaluation of its mechanical properties, machinability, and compatibility with the intended application. Several high-performance aluminum alloys offer an advantageous combination of strength, corrosion resistance, and ease of machinability, making them suitable for diverse applications. Here’s a detailed examination of some commonly employed alloys and their key characteristics:
AA6061: This versatile workhorse alloy boasts exceptional tensile strength exceeding 240 MPa (35 ksi) in the T6 temper, making it ideal for demanding structural applications requiring high load-bearing capabilities. Additionally, its excellent weldability and machinability facilitate efficient fabrication and precise threading, particularly for complex thread profiles. This combination of strength, weldability, and machinability makes AA6061 a top choice for demanding applications across various industries, including aerospace, automotive, and machinery manufacturing.
AA5052: Renowned for its superior resistance to saltwater corrosion and harsh chemical environments, AA5052 finds extensive application in marine structures, food processing equipment, and chemical piping systems. Its moderate tensile strength (~180 MPa, 26 ksi) and good machinability allow for robust internal threading while maintaining adequate structural integrity. However, compared to AA6061, AA5052 exhibits slightly lower weldability, necessitating careful consideration when joining components.
AA3003: This commercially pure aluminum alloy offers impeccable formability and superior machinability, making it ideal for intricate threading patterns and complex geometries. Its moderate tensile strength (~110 MPa, 16 ksi) and good corrosion resistance make it suitable for applications requiring good machinability and formability over high load-bearing capacity. AA3003 shines in applications like decorative tubing, pressure vessels with moderate pressure ratings, and intricate heat exchanger components.
Beyond the specific alloy selection, the tube wall thickness plays a crucial role in determining the feasibility and performance of internal threading. Thicker walls enable the formation of deeper and more robust threads, capable of withstanding higher torque and axial loads. Additionally, they offer improved pressure containment capabilities, making them suitable for high-pressure applications like hydraulic systems and piping networks. Conversely, thinner walls require specialized threading techniques, such as rotary swaging, and may impose limitations on thread depth, load-bearing capacity, and pressure rating. Therefore, carefully considering the wall thickness in conjunction with the intended application and desired thread performance is essential for optimal material selection.
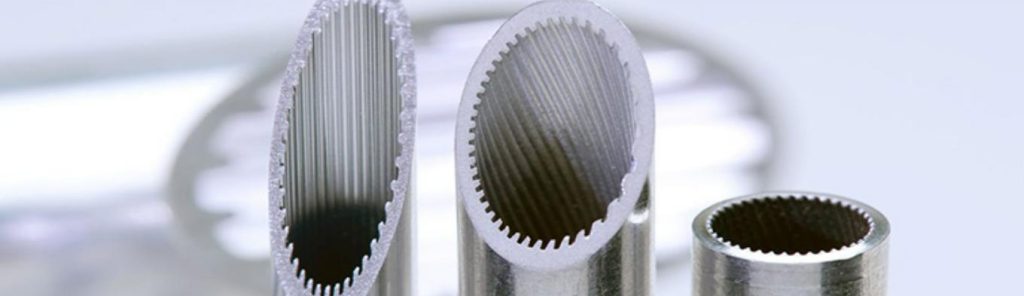
Threading Techniques for Internally Threaded Aluminum Tubing
Achieving precise and robust internal threads on aluminum tubing necessitates meticulous execution and the judicious selection of the appropriate technique. Several distinct methods are employed in industry, each offering unique advantages and inherent limitations:
1. CNC Machining: This computer-controlled machining process reigns supreme in terms of precision and flexibility. Utilizing numerically controlled tools, CNC machining allows for the creation of complex thread profiles with intricate geometries, ideal for applications requiring high dimensional accuracy and custom thread designs. Furthermore, its inherent programmability enables consistent quality and repeatability, making it particularly well-suited for high-volume production runs. However, CNC machining often necessitates significant capital investment and specialized expertise, which can be cost-prohibitive for smaller batches or simpler designs.
2. Tapping: This traditional method, often considered the workhorse of threading, utilizes a dedicated tap to progressively form threads within a pre-drilled bore. Tapping offers cost-effectiveness and simplicity, making it the preferred choice for standardized thread sizes and straightforward designs, particularly for smaller production runs. Its ease of use and minimal equipment requirements make it readily accessible to various workshops and manufacturing facilities. However, tapping is limited in its ability to handle complex thread profiles and may exhibit lower dimensional accuracy compared to CNC machining.
3. Rotary Swaging: This specialized technique, primarily used for thin-walled tubing, employs a rotating mandrel to progressively deform the inner surface of the tube, cold-forming the desired thread profile. Rotary swaging offers several advantages, including minimal material waste, improved thread strength due to cold work hardening, and the ability to create threads on extremely thin walls where conventional methods might be impractical or impossible. However, rotary swaging requires specialized equipment and careful control of process parameters to achieve optimal results. Additionally, it may not be suitable for all thread profiles or applications requiring high dimensional accuracy.
4. Combination Techniques: In some instances, a combination of threading techniques may be employed to leverage the strengths of each method. For example, pre-drilling and tapping might be used for the initial thread formation, followed by CNC machining for finishing and customization of complex profiles. Choosing the optimal combination requires careful consideration of the desired thread characteristics, wall thickness, production volume, and cost constraints.
By understanding the unique advantages and limitations of each threading technique, engineers and manufacturers can select the most appropriate method for their specific needs. This ensures the creation of internally threaded aluminum tubing with the desired performance characteristics, dimensional accuracy, and cost-effectiveness, ultimately contributing to the successful completion of diverse engineering projects.
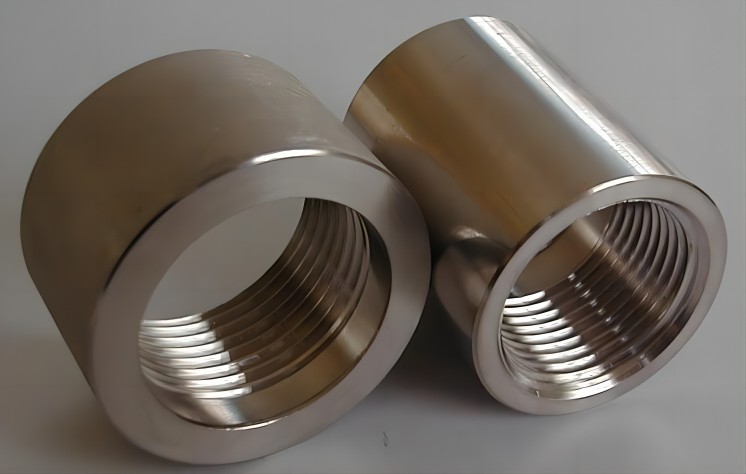
Additional Processing for Internally Threaded Aluminum Tubing
Following the successful formation of internal threads, various post-processing steps may be necessary depending on the intended application and desired performance characteristics of the tubing. These steps aim to enhance functionality, durability, and aesthetics while minimizing potential operational issues.
1. Deburring: This critical step involves the meticulous removal of sharp edges and burrs left behind from the threading process. These residual protrusions can compromise smooth operation, create leak paths, and damage mating components. Two primary methods are employed for deburring:
- Mechanical deburring: This method utilizes specialized tools such as rotary brushes, files, or deburring blades to physically remove burrs and chamfer thread edges. Different tools and techniques are employed based on the specific thread profile, tube diameter, and material characteristics.
- Chemical deburring: This approach involves immersing the tubes in a chemical bath that dissolves or weakens the burrs, allowing for their subsequent removal via rinsing or ultrasonic cleaning. Chemical deburring is often preferred for complex thread geometries or situations where mechanical tools may be difficult to access.
2. Cleaning: Thoroughly cleaning the tubes ensures the removal of any residual contaminants, such as machining lubricants, coolants, or metallic particles, that could negatively impact performance or promote corrosion. Common cleaning methods include:
- Ultrasonic cleaning: This technique utilizes high-frequency sound waves to create microscopic bubbles that vibrate and dislodge contaminants from the tube’s surface and internal threads. Ultrasonic cleaning is particularly effective for intricate geometries and hard-to-reach areas.
- Chemical cleaning: Immersion in specialized cleaning solutions can remove specific types of contaminants, such as oils, greases, or oxides. Chemical cleaning often requires subsequent rinsing and neutralization steps to ensure complete removal of the cleaning agents and prevent potential corrosion.
3. Coating: Depending on the specific application requirements, internally threaded aluminum tubing may be coated with various finishes to enhance functionality, aesthetics, or environmental resistance. Some common coating options include:
- Anodization: This electrochemical process creates a thin, hard oxide layer on the aluminum surface, significantly enhancing its corrosion resistance and wear properties. Anodization can also be applied in decorative colors for aesthetic purposes.
- Powder coating: This dry finishing technique involves applying a layer of pigmented powder that is electrostatically charged and then cured to form a durable and chip-resistant coating. Powder coating offers excellent protection against corrosion, wear, and UV degradation, and is available in a wide range of colors and textures.
- Thermal coatings: For applications involving heat transfer or thermal insulation, specialized coatings with specific thermal properties can be applied. These coatings can improve thermal efficiency, prevent overheating, and protect against thermal degradation.
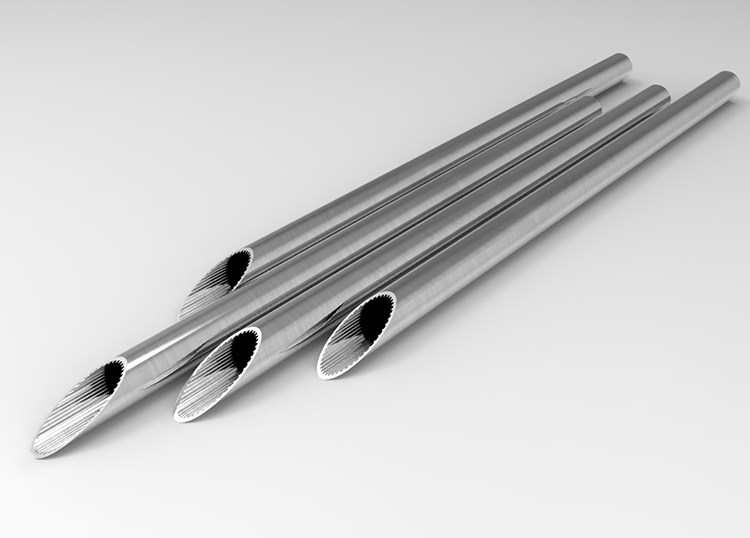
Quality Control for Internally Threaded Aluminum Tubing
Maintaining stringent quality control protocols is imperative for ensuring the structural integrity, functional performance, and long-term reliability of internally threaded aluminum tubing. These protocols encompass a comprehensive set of inspection and testing procedures designed to verify conformance to specified requirements across various critical parameters.
1. Dimensional Accuracy
- Thread dimensions: Meticulous verification of thread parameters such as pitch, major and minor diameters, and thread depth is crucial for ensuring proper mating with other components and optimal performance. This may involve employing specialized measuring tools like thread gauges, calipers, or coordinate measuring machines (CMMs).
- Wall thickness: Accurate measurement of the tube wall thickness ensures it meets the specified requirements for strength, pressure rating, and thread depth limitations. Non-destructive ultrasonic thickness gauges are often utilized for this purpose.
- Overall geometry: Verification of the tube’s overall geometry, including straightness, roundness, and concentricity, is essential for ensuring proper fitment and functionality in the intended application. Specialized inspection tools or CMMs may be employed depending on the required precision level.
2. Surface Finish
- Thread profile: Thorough assessment of the thread profile for smoothness, absence of burrs, and adherence to the desired surface texture specifications is crucial for minimizing friction, improving wear resistance, and preventing leaks. Visual inspection alongside tactile evaluation and surface roughness measurements are typically employed.
- Internal and external surfaces: Examination of the internal and external surfaces for scratches, pitting, or other imperfections that could compromise performance or aesthetics is essential. Visual inspection and non-destructive eddy current or magnetic particle testing techniques may be utilized depending on the material and application requirements.
3. Pressure Testing
- For high-pressure applications: For tubes intended to handle significant pressure loads, rigorous pressure testing is mandatory to ensure they can withstand the specified operating pressures without failure or leakage. This involves subjecting the tubes to controlled pressure exceeding the expected service pressure and monitoring for any signs of deformation, leaks, or ruptures.
- Leak testing: For applications where leak prevention is paramount, specialized leak detection methods such as helium leak testing or bubble emission testing may be employed to identify even minute imperfections or potential leakage paths.
4. Additional Quality Control Measures
- Material certification: Verification of the aluminum alloy used in the tubing through material certificates or chemical analysis ensures adherence to the specified grade and its suitability for the intended application.
- Coating adhesion testing: For coated tubes, adhesion testing ensures the coating adheres properly to the substrate and will not peel or flake under normal operating conditions.
- Documentation and traceability: Maintaining detailed records of all inspection and testing procedures, including results and any corrective actions taken, is crucial for ensuring traceability and quality assurance throughout the production process.
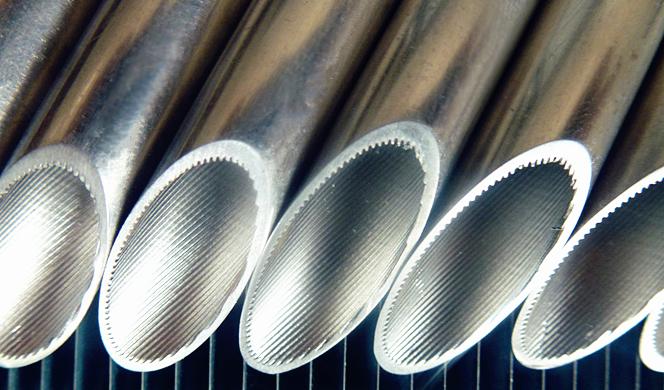
Conclusion
The successful fabrication and processing of internally threaded aluminum tubing requires a comprehensive understanding of material properties, threading techniques, and post-processing considerations. By carefully selecting the appropriate material, employing the optimal threading method, and implementing stringent quality control measures, engineers and manufacturers can create high-performance tubes for diverse applications across various industries. The versatility, strength, and corrosion resistance of internally threaded aluminum tubing, coupled with its amenability to various processing techniques, make it a valuable material for a wide range of engineering challenges.