Drawn aluminum tubes are a vital component in various industries, thanks to their unique combination of properties and production methods. These tubes are manufactured through a cold working process, resulting in a product that is lightweight, strong, and resistant to corrosion. Made from pure aluminum or aluminum alloys, drawn aluminum tubes are used extensively in automotive, aerospace, construction, and household appliance industries due to their excellent thermal conductivity, strength, and workability.
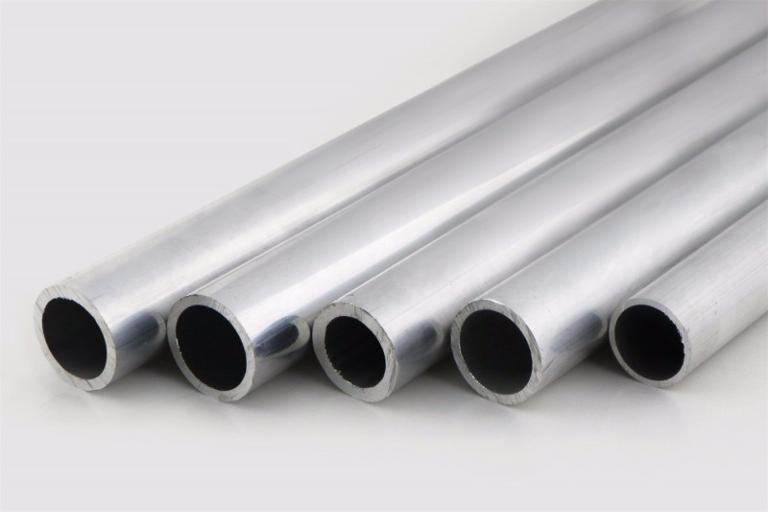
Manufacturing Processes of Drawn Aluminum Tubes
The production of drawn aluminum tubes involves several stages, each contributing to the final product’s quality and characteristics. The process begins with aluminum material, which is subjected to a drawing operation. This operation involves pulling the aluminum through a die to reduce its diameter and increase its length gradually.
Equipment and Tools in Drawn Aluminum Tube Process
Drawn aluminum tubing is produced through a cold working process that involves pulling aluminum through a die to reduce its diameter and increase its length. This process requires specialized equipment and tooling.
1. Primary Equipment
Drawing Machines: These are the workhorses of the process, pulling aluminum tubing through a series of dies to reduce its diameter and increase its length. They come in various types, including:
- Single-draw benches: For smaller diameter tubes and shorter lengths.
- Multiple-draw benches: For larger diameter tubes and longer lengths, often incorporating intermediate annealing stages.
- Continuous drawing machines: For high-volume production of consistent tube dimensions.
Annealing Furnaces: To soften the aluminum alloy between drawing passes, improving ductility and preventing cracking.
Straightening Machines: To correct any curvature or ovality introduced during the drawing process.
Cutting Machines: To cut tubes to desired lengths.
Inspection Equipment: To ensure dimensional accuracy, surface quality, and material properties meet specifications.
2. Critical Tooling
- Dies: These precision-engineered tools shape the aluminum tube as it’s drawn. They are typically made of hardened steel or carbide and have a complex geometry to achieve the desired dimensions and tolerances.
- Mandrels: These internal tools support the tube during drawing, preventing collapse and ensuring consistent wall thickness. They are often made of hardened steel or tungsten carbide.
- Lubrication Systems: Proper lubrication is essential to reduce friction, improve drawing efficiency, and enhance surface finish. Lubricants can be oil-based, water-soluble, or dry film types.
- Gripping and Feeding Systems: These components hold and advance the tube through the drawing process, ensuring accurate alignment and consistent tension.
3. Additional Equipment (Depending on Process Complexity)
- Tube Preparation Equipment: For cleaning, pickling, and surface preparation of the starting material.
- Heat Treatment Furnaces: For specific alloy properties or tempering requirements.
- Hydraulic Presses: For forming tube ends or other complex shapes.
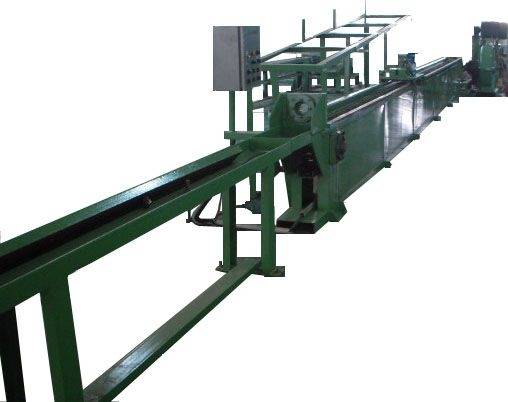
Key Steps in the Drawn Aluminum Tube Process
The drawing process for aluminum tubes involves several critical steps to ensure the desired properties and dimensions are achieved.
- Pre-Drawing: The pre-drawing step is crucial for preparing the aluminum material before it undergoes the primary drawing process. This stage involves applying a preliminary stretch to the material to even out internal stresses and enhance its uniformity. This pre-stretch helps to prevent defects and improve the overall quality of the drawn tube.
- Rough Drawing: In the rough drawing stage, the aluminum is drawn through a die to reduce its cross-sectional area and increase its length. This step is not intended to achieve the final dimensions but to prepare the material for further drawing. It helps to reduce the diameter and create a preliminary shape.
- Intermediate Drawing: The intermediate drawing process involves a further reduction in diameter and enhancement of the tube’s uniformity. During this stage, the drawing force is carefully controlled to achieve a more precise shape. This step ensures that the material is evenly drawn and ready for the final drawing stage.
- Final Drawing: The final drawing stage is where the aluminum tube is brought to its exact dimensions. Precision in this step is critical, as it determines the final size and quality of the product. This stage involves careful control of drawing forces and conditions to achieve the desired dimensions and surface finish.
How Important Pre-Drawing is?
Pre-drawing is a critical step in the production of drawn aluminum tubes. Its primary purpose is to eliminate residual stresses that may have been introduced during earlier processing or treatment. If these stresses are not addressed, they can lead to defects such as cracks or deformations during subsequent processing steps. By redistributing internal stresses through controlled stretching, pre-drawing helps to improve the material’s uniformity, surface quality, and overall mechanical properties.
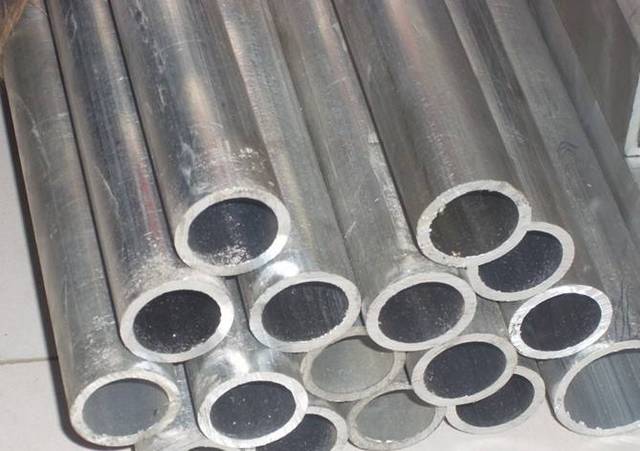
Drawn Aluminum Tubes vs. Extruded Aluminum Tubes: Differences in Manufacturing Process
Drawn and extruded aluminum tubes are produced using different methods, each with its distinct characteristics and advantages. As the following summary table shows:
Comparison Aspect | Drawn Aluminum Tubes | Extruded Aluminum Tubes |
Forming Mechanism | Pulling aluminum through a die, reducing diameter and increasing length continuously. | Pushing heated aluminum through a die, adopting the die’s cross-sectional shape. |
Equipment and Tools | Drawing machines and dies for continuous stretching. | Extrusion presses and dies for pushing heated aluminum through the die. |
Production Efficiency | Slower process with higher production costs and longer lead times. | Generally more efficient, suitable for large production runs and lower costs. |
Cost | Higher due to individual adjustments and setup required for each drawing pass. | Lower due to mass production capability and multiple products per extrusion cycle. |
Product Characteristics | Superior surface finish and dimensional accuracy, suitable for high-precision uses. | Capable of complex cross-sectional shapes, ideal for structural strength applications. |
Application Suitability | High-precision applications where surface finish and dimensional accuracy are critical. | Load-bearing applications requiring structural strength and complex shapes. |
Common Issues and Solutions in the Aluminum Tube Drawing Process
There may be a series of problems in the aluminum tube drawing process, which may affect product quality and production efficiency. Here are some common problems and solutions:
1. Surface Quality Issues
Aluminum tubes can develop surface defects such as scratches or oxidation spots during the drawing process. These issues can be mitigated by:
- Optimizing lubrication: Ensuring that high-quality lubricants are used in the correct quantities to minimize friction and wear on the material’s surface.
- Surface treatment: Applying protective coatings or performing surface finishing processes to improve the material’s resistance to damage and corrosion.
2. Dimensional Accuracy
Achieving precise dimensions is a common challenge in aluminum tube drawing. Variations in tube size can be caused by equipment malfunctions or operational errors. To address this, manufacturers must:
- Regularly calibrate and maintain drawing machines to ensure their accuracy.
- Train operators to monitor and adjust the drawing process as needed.
3. Internal Defects
Internal defects, such as cracks or voids, can occur in aluminum tubes during the drawing process. These defects can be minimized by:
- Selecting high-quality aluminum alloys that are less prone to cracking.
- Controlling the drawing speed and force to prevent excessive strain on the material.
- Regularly inspecting and maintaining the dies to ensure they are free from defects.
4. Mold Wear
Mold wear is a natural consequence of the drawing process, as the aluminum repeatedly contacts the dies. To mitigate mold wear:
- Use durable materials for the dies that can withstand the high pressures and temperatures involved.
- Apply lubricants that reduce friction and heat, thereby decreasing wear.
- Regularly inspect and replace worn dies to maintain the integrity of the drawn tubes.
5. Breakage and Cracking
Breakage and cracking can occur if the aluminum tube is subjected to excessive force or if the material is too brittle. To prevent this:
- Ensure that the material properties are suitable for the drawing process.
- Use proper lubrication and control the drawing speed to avoid sudden stresses on the material.
- Regularly inspect the material for any signs of fatigue or damage.
6. High Energy Consumption
Aluminum tube drawing can be an energy-intensive process, particularly if the equipment is not efficient or if the process parameters are not optimized. To reduce energy consumption:
- Upgrade to more energy-efficient machinery.
- Optimize the drawing process by adjusting parameters such as speed and force.
- Implement regular maintenance to ensure that all components are operating at peak efficiency.
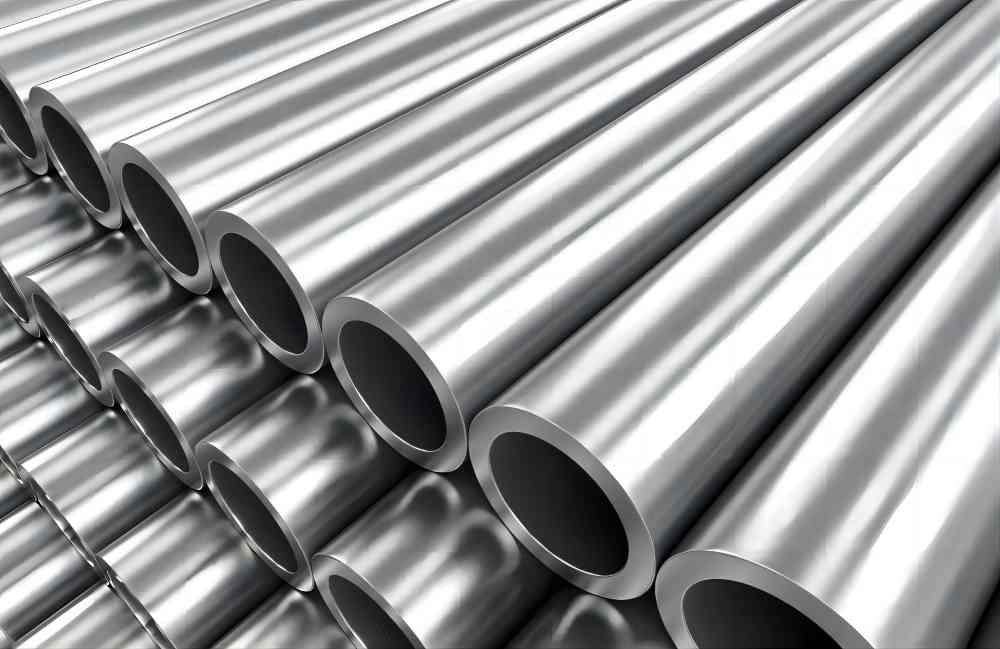
Conclusion
Drawn aluminum tubes are an essential component in various industrial applications, due to their unique properties and the advanced manufacturing processes used to produce them. Understanding the differences between drawn and extruded aluminum tubes, along with the key steps and common issues in the drawing process, is crucial for optimizing production and ensuring high-quality products. By addressing common challenges and implementing best practices, manufacturers can achieve excellent results and meet the demands of diverse applications. As technology advances, ongoing improvements in drawing techniques and equipment will continue to enhance the capabilities and performance of drawn aluminum tubes.