In the harsh and unforgiving marine environment, where salt spray, corrosive seawater, and extreme weather conditions are the norm, the choice of materials is critical. Marine-grade aluminum has emerged as a preferred choice for boat builders, marine equipment manufacturers, and offshore construction due to its exceptional combination of strength, corrosion resistance, and workability. Here we will delve into the specifics of marine-grade aluminum, exploring the alloys, properties, common applications, and considerations for its use in the demanding marine environment.
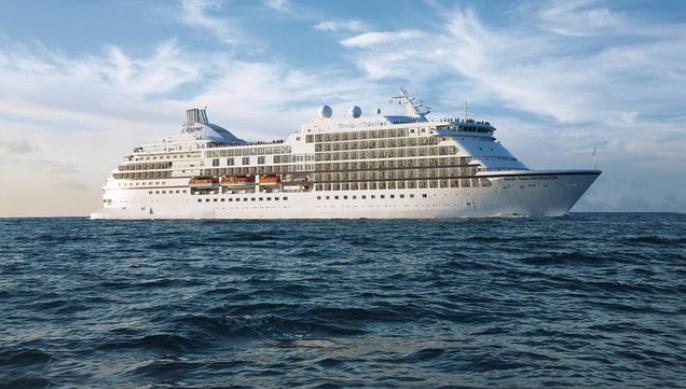
Properties of Marine-Grade Aluminum
Marine-grade aluminum has several key properties that make it a go-to material in the marine industry:
- Lightweight: Aluminum is about one-third the weight of steel, making it a preferred choice for boat hulls and structures. The reduced weight improves fuel efficiency and overall performance, especially in smaller craft like fishing boats and recreational vessels.
- Strength-to-Weight Ratio: Despite being lightweight, aluminum has a high strength-to-weight ratio, meaning it can bear significant loads without compromising on weight. This makes it ideal for marine applications that require both strength and efficiency.
- Formability: Aluminum can be easily extruded, rolled, or welded into complex shapes, giving shipbuilders flexibility in designing various marine components.
- Thermal Conductivity: Aluminum has high thermal conductivity, which can be beneficial in certain cooling systems, such as engine cooling systems in boats.
- Recyclability: Aluminum is highly recyclable without losing its structural integrity. This makes it a more environmentally friendly choice compared to other metals like steel.
How Marine-Grade Aluminum Resists Corrosion
One of the standout features of marine-grade aluminum is its ability to resist corrosion in the harsh marine environment. Unlike steel, which is highly susceptible to rust and deterioration when exposed to saltwater, aluminum forms a natural oxide layer that protects the underlying metal from corrosion. This oxide layer acts as a protective barrier, preventing further oxidation.
In addition, marine-grade aluminum alloys, like 5083, undergo specific treatments such as anodizing or applying coatings that enhance their resistance to corrosion. These treatments create a thicker oxide layer, improving the alloy’s ability to resist environmental damage over time.
Aluminum’s resistance to corrosion is crucial in marine environments where vessels and components are constantly exposed to saltwater, moisture, and varying temperatures. This makes it especially valuable for long-term performance, reducing maintenance and repair costs.
The combination of lightweight, strength, and excellent corrosion resistance makes marine-grade aluminum an ideal material for the marine industry. Its ability to withstand the harsh conditions of saltwater exposure without rusting or deteriorating significantly extends the lifespan of marine vessels and structures.
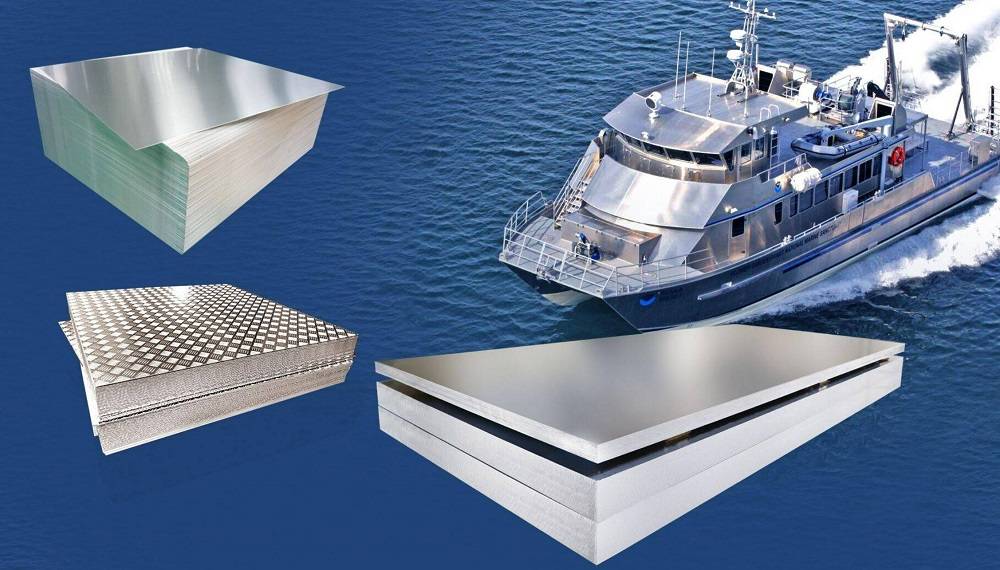
Specific Aluminum Alloys for Marine Use
Aluminum alloys are not created equal, and the marine environment demands specific grades of aluminum that can handle exposure to saltwater, UV rays, and physical stress. The most common marine-grade aluminum alloys include 5083, 6061, and 7075.
5083 Aluminum
5083 is one of the most corrosion-resistant aluminum alloys available, often used for constructing boat hulls, ship bodies, and offshore platforms. It offers excellent resistance to both seawater and aggressive chemicals, making it ideal for high-exposure environments. This alloy also maintains its strength even at low temperatures, which is why it’s frequently chosen for Arctic and sub-Arctic marine operations.
6061 Aluminum
6061 is another widely used alloy in the marine industry, particularly for structural components. It’s versatile, with a balance of strength, weldability, and corrosion resistance. This alloy is often used in the frames of smaller vessels, recreational boats, and for marine hardware like railings and ladders. While not as resistant to corrosion as 5083, 6061’s cost-effectiveness and ease of fabrication make it an attractive choice.
7075 Aluminum
7075 is a high-strength alloy often used for military and aerospace applications and in marine industries for critical components where strength is paramount. It is stronger than both 5083 and 6061, but it’s not as resistant to corrosion, which limits its use in more demanding marine environments.
Choosing the right alloy depends on the specific requirements of the marine project—whether you prioritize corrosion resistance, strength, or weldability.

Common Marine Aluminum Extrusions
Marine aluminum extrusions refer to the shapes and profiles of aluminum that are specifically fabricated for marine uses. Extrusion is the process of shaping aluminum into desired cross-sections, often used to create structural elements of marine vessels. Some of the most common aluminum extrusions found in marine applications include:
T-Slot Profiles
T-slot extrusions are frequently used in the construction of boat frames and railings. These profiles provide ease of assembly, flexibility, and adjustability, allowing designers to create robust yet lightweight structures.
C-Channels and I-Beams
C-channels and I-beams are commonly used for the construction of the frames of ships and boats. These profiles offer strength and rigidity while maintaining a lightweight design, making them ideal for hulls, superstructures, and platforms.
Round Tubes and Bars
Aluminum round tubes and bars are used extensively for creating railings, posts, and handrails on boats and ships. These extrusions are prized for their smooth surfaces and resistance to corrosion, ensuring both aesthetics and durability.
Angle Extrusions
Aluminum angles are used for supporting structural frameworks and adding stability to marine vessels. These extrusions are designed to resist bending and are often used in combination with other profiles to create strong, rigid frames.
Aluminum extrusions are vital for creating custom, lightweight, and durable components in marine structures. From frames and railings to support beams and profiles, extrusions offer flexibility in design while maintaining the essential strength and corrosion resistance needed for marine applications.
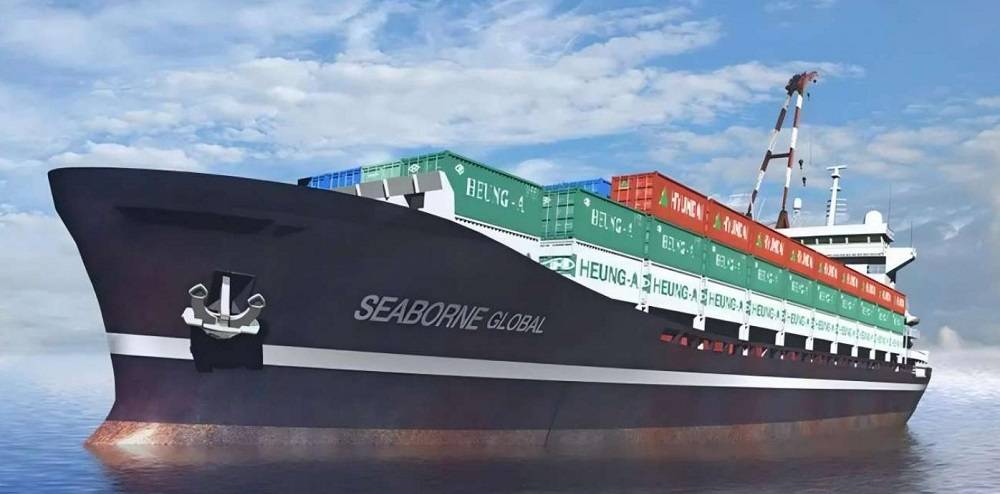
Considerations for Using Marine-Grade Aluminum
While marine-grade aluminum offers numerous advantages, there are several important considerations to keep in mind before incorporating it into your marine projects. These factors can affect the material’s performance, cost-effectiveness, and durability over time.
1. Initial Cost
Marine-grade aluminum, particularly high-quality alloys like 5083, tends to be more expensive than other materials like steel or standard aluminum. The cost of the material can be a significant factor when deciding whether to use aluminum for your project. However, it’s important to consider the long-term benefits, including reduced maintenance costs, fuel savings due to its lightweight properties, and the longevity of the material, which may offset the higher initial investment.
2. Strength Limitations
While aluminum offers an excellent strength-to-weight ratio, it is not as strong as steel in terms of tensile strength. For applications that require extreme strength, such as certain heavy-duty marine structures, steel or other stronger materials might still be the better option. Aluminum is suitable for most marine applications but may not always be appropriate for areas that undergo heavy stress or impact.
3. Welding and Fabrication
Welding aluminum requires specialized knowledge and equipment. Unlike steel, aluminum has a lower melting point and can be prone to distortion during welding. Special care must be taken to ensure proper weld integrity, as poor welds can lead to structural weakness or corrosion over time. Additionally, aluminum’s tendency to form oxide layers on its surface may complicate the welding process, so surface preparation is essential.
4. Galvanic Corrosion
One of the most important factors to consider when using marine-grade aluminum is its potential for galvanic corrosion when in contact with dissimilar metals, such as steel or copper. In a marine environment, where seawater acts as an electrolyte, aluminum and other metals can form a galvanic cell, leading to accelerated corrosion. To prevent this, careful material selection, the use of isolating coatings, and proper maintenance are crucial to ensure that aluminum doesn’t come into direct contact with more cathodic materials.
5. Fatigue Resistance
While aluminum offers excellent resistance to corrosion, it can be more susceptible to fatigue over time, particularly when subjected to cyclic stresses or vibration. In high-stress applications, such as for engines, propellers, or areas prone to vibration, additional reinforcement may be necessary. Alloy selection and design modifications, such as using thicker sections or additional supports, may be required to prevent premature failure.
6. Environmental Considerations
Marine-grade aluminum is highly recyclable, which adds an environmental benefit to its use. However, the production of aluminum is energy-intensive, which means that its carbon footprint is higher compared to materials like steel, especially in the early stages of production. That said, aluminum’s recyclability and long service life mitigate this environmental concern over time, making it a sustainable choice in the long run.
Marine-grade aluminum has proven to be an invaluable material in the marine industry, offering a compelling blend of strength, corrosion resistance, and workability.
Whether you’re designing small boats, large vessels, or offshore platforms, marine-grade aluminum offers numerous advantages that ensure performance and longevity. By taking the time to understand its properties and applications, you can harness the full potential of this versatile material in your next marine project.