Aluminum plates are a versatile and popular material choice for various applications due to their unique combination of lightweight properties, strength, and formability. However, achieving optimal performance and aesthetics in aluminum plate design requires careful consideration of several key factors. This article provides a comprehensive guide to designing aluminum plates, encompassing material selection, structural considerations, surface treatments, installation details, and environmental factors.

Understanding Key Design Considerations of Aluminum Plates
When designing with aluminum plates, several crucial aspects influence the final product’s functionality, durability, and visual appeal.
1. Material Selection
Selecting the appropriate aluminum material is crucial for meeting specific application requirements. Key properties to consider include strength, rigidity, thermal conductivity, electrical conductivity, and thermal expansion coefficient.
- Strength and Rigidity: Aluminum plates must have sufficient strength and rigidity to withstand applied loads without excessive deformation. The choice of alloy and tempering process significantly affects these properties. For instance, applications requiring high strength and rigidity might benefit from alloys like 6061-T6, while those prioritizing lightweight properties could utilize 5052-H32.
- Thermal Conductivity: Aluminum’s high thermal conductivity makes it suitable for heat exchangers and thermal management applications. Understanding the thermal requirements of the application helps in selecting the right grade of aluminum.
- Electrical Conductivity: For electrical applications, the aluminum plate’s conductivity must be considered. Aluminum is commonly used in power transmission and distribution systems due to its favorable electrical properties.
- Thermal Expansion Coefficient: Aluminum expands and contracts with temperature changes. This property must be factored into the design, especially in applications involving significant temperature fluctuations.
2. Structural Design
The structural design of aluminum plates involves creating a support system and connection methods that ensure functionality and safety.
- Support Systems: Properly designed support systems are essential for maintaining the integrity of aluminum plate installations. These systems must account for factors like wind pressure, self-weight, seismic activity, and thermal effects.
- Connection Methods: The connection methods, including welding, bolting, or riveting, must be carefully chosen to ensure strong and durable joints. The design should include detailed checks on embedded parts, connection systems, keel systems, panels, and fasteners.
- Load Considerations: Structural design should account for various loads, including dead loads (self-weight), live loads (external forces), and dynamic loads (wind, seismic activity). Accurate load calculations are critical for ensuring safety and performance.
3. Surface Treatment
Surface treatment enhances the durability and appearance of aluminum plates. It is essential to specify the surface treatment color and direction in design documents.
- Color and Direction: The color of the surface treatment should be clearly indicated in the design. If the aluminum plate has a directional finish, the direction must be specified to ensure consistency.
- Weather-Resistant Treatments: For long-term outdoor use, weather-resistant treatments such as fluorocarbon coating are recommended. These treatments provide superior resistance to UV radiation, corrosion, and environmental pollutants.
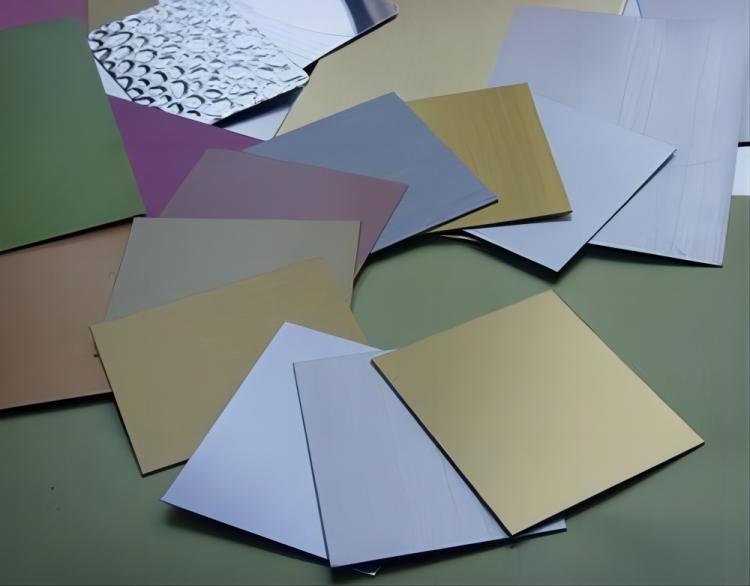
4. Installation Details
Proper installation methods are crucial for achieving the desired performance and aesthetic qualities of aluminum plates.
- Fixing Method: The fixing method significantly affects the installation’s flatness. Fixed-distance compression fixing is recommended to ensure a smooth and flat surface.
- Waterproof Sealing: Effective waterproof sealing methods are essential to prevent water ingress and maintain the functionality and appearance of the aluminum plate installation. The sealing design should consider factors such as joint movement and thermal expansion.
5. Quality Control
Ensuring the quality of aluminum plates involves selecting qualified materials and implementing strict inspection methods.
- Material Quality: Choose aluminum plates that meet industry standards and specifications. Regular inspections during manufacturing and installation help detect and address any quality issues.
- Drainage Considerations: Aluminum plate design should include drainage provisions, especially for ceiling-type installations. If water ingress is allowed, drainage holes must be provided to prevent water accumulation and potential damage.
6. Maintenance and Durability
Designing for maintenance and durability ensures that aluminum plates remain functional and visually appealing over time.
- Ease of Cleaning: Choose surface treatments that are easy to clean and maintain. Smooth, non-porous surfaces are preferable for applications requiring regular cleaning.
- Environmental Resistance: Select materials and treatments that can withstand environmental factors such as UV radiation, moisture, and pollutants. This enhances the longevity of aluminum plates in various conditions.
7. Environmental Adaptability
Aluminum plates must be adaptable to their intended usage environment, including temperature, humidity, and UV exposure.
- Temperature and Humidity: Aluminum plates should be chosen and treated to resist the specific temperature and humidity conditions of the installation environment. This prevents issues such as thermal expansion and corrosion.
- UV Resistance: In outdoor applications, UV-resistant coatings are essential to prevent degradation and maintain the appearance of aluminum plates over time.
8. Cost-Effectiveness
Balancing design and performance requirements with cost considerations is key to achieving cost-effective aluminum plate designs.
- Material Selection: Choose materials that offer the best performance-to-cost ratio. While high-performance alloys and treatments may be more expensive, they can provide long-term cost savings through enhanced durability and reduced maintenance.
- Design Efficiency: Efficient design practices, such as optimizing material usage and simplifying installation processes, can help reduce overall costs without compromising performance.
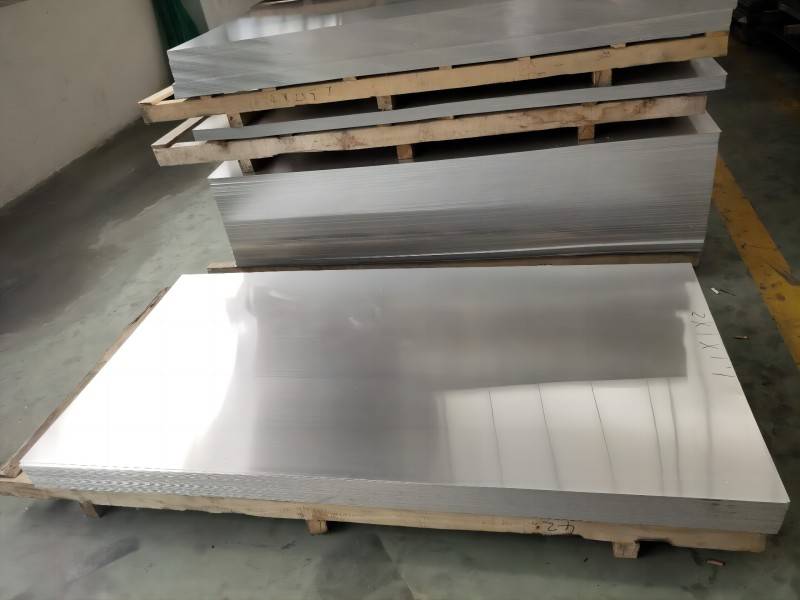
Understanding Size and Shape Considerations for Aluminum Plates
While aluminum plates offer a high degree of design flexibility, there are limitations to consider regarding their size and shape.
- Size Limitations: Aluminum plates are available in a range of standard sizes. These standard dimensions typically encompass thicknesses ranging from 0.2 mm to 200 mm, widths varying from 100 mm to 2600 mm, and lengths spanning from 500 mm to 16000 mm. However, custom sizes can be produced to accommodate specific engineering requirements. It’s important to adhere to relevant national standards for dimensional tolerances, such as the GB/T 3880.3-2012 standard for aluminum plate thickness tolerance.
- Shape Limitations: Aluminum plates are traditionally designed as flat panels. However, with appropriate processing techniques, curved or even complex shapes can be achieved. These processing techniques can include bending, rolling, and folding. Edge treatments, such as chamfering or milling, can be implemented to meet specific design requirements and enhance safety by reducing sharp edges.
- Design Factors Influencing Size and Shape: Several design factors influence the selection of size and shape for aluminum plates.
- The application itself often dictates specific requirements. For instance, building exteriors might necessitate larger aluminum plates to cover wider areas, while interior design applications might favor lightweight or intricately shaped plates for a more decorative effect.
- Functionality is another crucial consideration. For example, laboratory equipment might require aluminum plates with specific corrosion-resistant or acid-alkali resistant treatments, potentially influencing the choice of size and shape based on available options with those properties.
- Safety should also be prioritized. The load-bearing capacity and overall stability of the aluminum plates must be carefully considered to prevent deformation or damage during use.
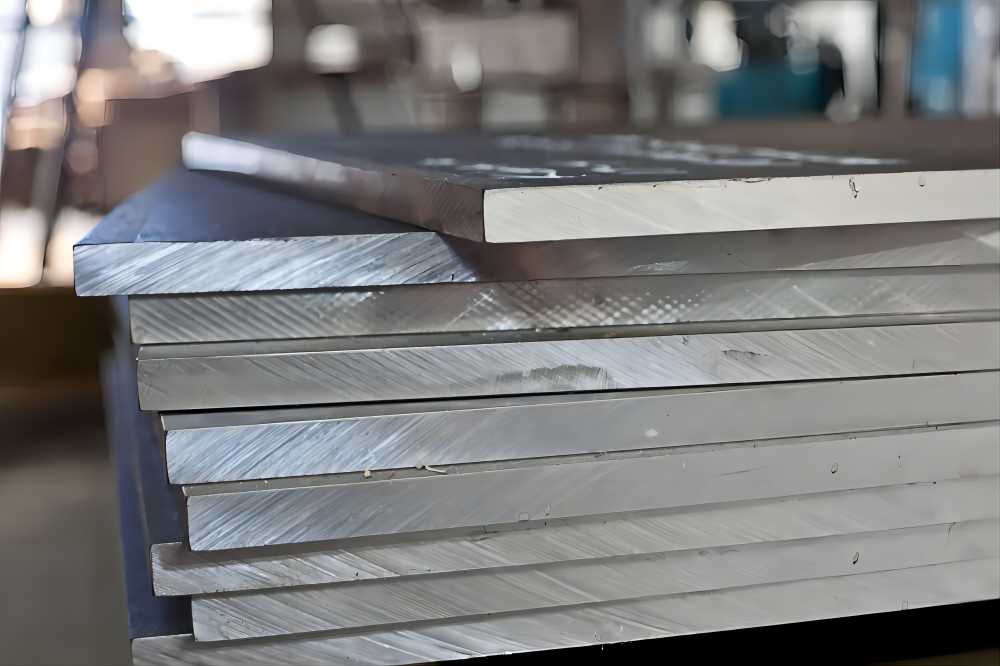
Environmental Factors to Avoid for Aluminum Plate Corrosion Prevention
Aluminum is naturally resistant to corrosion due to the formation of a thin oxide layer on its surface. However, exposure to certain environmental factors can accelerate the corrosion process. Here’s a breakdown of key environmental factors to avoid:
- Acidic Environments: Exposure to acidic chemical gases and solutions can deteriorate the aluminum plate’s surface through a process known as acid etching. Selecting aluminum alloys with higher corrosion resistance or applying protective surface treatments is crucial in such environments.
- Marine Environments: Saltwater and high humidity levels prevalent in marine environments can lead to galvanic corrosion, a process where dissimilar metals in contact with each other experience accelerated corrosion. Utilizing aluminum alloys specifically designed for marine applications or employing appropriate cathodic protection techniques can help mitigate this issue.
- Sandstorms and Air Pollution: Airborne pollutants and sand particles can adhere to the aluminum plate’s surface and form corrosive substances. Regular cleaning and maintenance practices are essential in such environments to minimize the risk of corrosion.
- Electrochemical Corrosion: Specific combinations of metals and electrolytes can create an electrochemical environment that accelerates aluminum corrosion. A thorough understanding of the intended use environment and the potential for such interactions is necessary to select appropriate materials and mitigate this risk.
- Humidity: High humidity levels can promote the formation of condensation on the aluminum plate’s surface, leading to corrosion. Maintaining a dry storage and use environment is crucial, and employing moisture-resistant surface treatments can offer additional protection.
- Temperature: Extreme temperatures, particularly high temperatures, can cause moisture to accumulate inside packaging materials during storage or transportation. This trapped moisture can initiate corrosion upon unpacking. Proper storage practices and the use of moisture-proof packaging materials are essential to prevent such issues.
- Improper Packaging and Transportation: Direct contact with moisture during transportation or storage can significantly accelerate aluminum plate corrosion. Employing appropriate packaging materials and implementing protective measures like waterproof wrapping or desiccant packs can help prevent moisture buildup and subsequent corrosion.
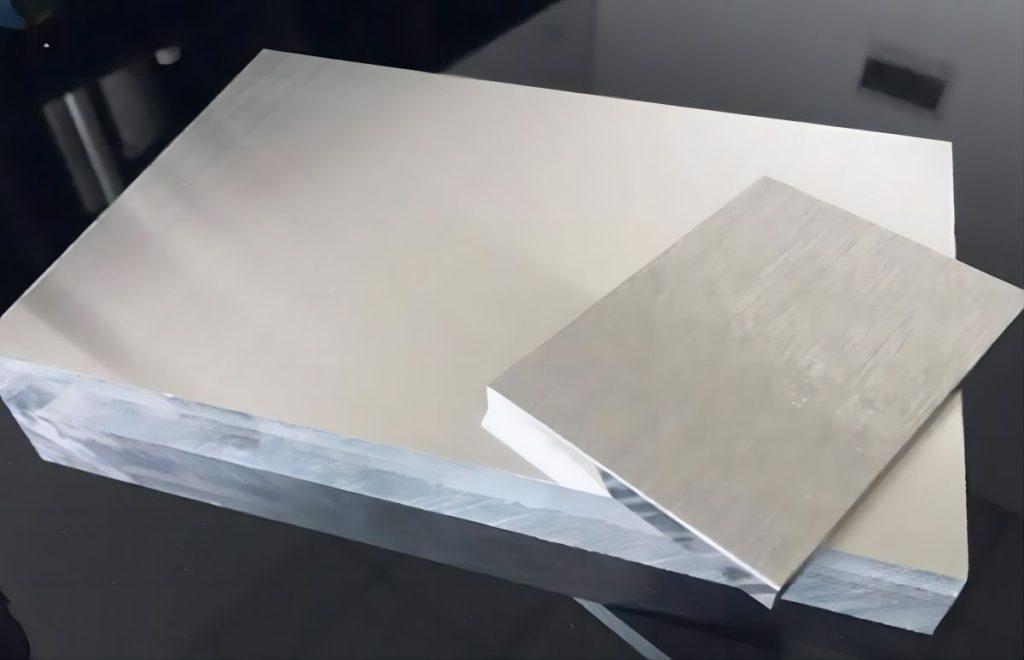
Conclusion
By carefully considering the design factors outlined in this comprehensive guide, you can optimize the performance and aesthetics of aluminum plates in your project. Selecting the appropriate material, and surface treatment, and implementing measures to mitigate environmental factors will ensure the longevity and functionality of your aluminum plate application. Remember to prioritize quality control throughout the process, from material selection to installation. With proper planning and execution, aluminum plates can serve as a durable, versatile, and visually appealing solution for a wide range of applications.
For high-quality aluminum plates that meet stringent design and performance standards, consider CHAL. CHAL offers a wide range of aluminum plate products tailored to various applications, ensuring optimal material selection, structural integrity, and surface treatments. With their commitment to quality and customer satisfaction, CHAL is a reliable supplier for your aluminum plate needs. Visit CHAL’s website to explore their product offerings and find the perfect solution for your project.