Stamping Parts
The characteristics and performance advantages of aluminum alloy make it one of the preferred materials for lightweight vehicles today. The forming characteristics of aluminum alloy sheets and their stamping process, welding process, and coating process are widely used in automotive.
Process of Aluminum Stamping Parts in Welding
The main processes of welding the aluminum alloy body include resistance welding, CMT cold transfer welding, argon tungsten arc welding, riveting, punching and grinding, and polishing.
- Aluminum alloy without riveting connection process
The riveting-free connection of aluminum stamping parts is to cold-extrude 2-layer or multi-layer metal plate parts through pressure equipment and special molds, and then form an internal inlaid connection point with certain tensile and shear strength. The thickness of the connecting plates can be the same or different, there can be an adhesive layer or other intermediate layers, and the materials can be the same or different. The connection effect is good, no auxiliary connector is required.
- Aluminum alloy parts punching riveting connection process
The punching riveting connection of aluminum plate parts, as shown in the following figure, is to use punching riveting equipment to press the punching rivet into the material to be connected to form a stable, reliable, and beautiful connection point.
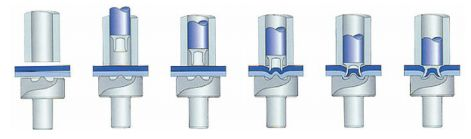
- Features of punching riveting connection process:
1) High strength, shear resistance, tensile dynamic fatigue strength, and impact resistance of riveted joints are higher than or equal to the strength of spot welded joints;
2) The connection quality can be checked visually. The rivet is completely driven into the workpiece, and at the same time a protruding joint is formed on the other side of the connecting workpiece, that is, it is considered qualified;
3) The material to be connected does not need to be drilled in advance, and the process is simple;
4) The connection point is sealed, and will not enter gas or liquid, causing material corrosion;
5) For metals and non-metals, metals of different materials, thicknesses, and strengths can be connected.
- Resistance welding
At present, the resistance welding of aluminum alloys generally adopts the medium-frequency or high-frequency resistance welding process. This welding process is only within the diameter range of the electrode of the welding tongs, and the base metal is melted in a short time to form a molten pool, and the welding point is rapid. Cooling forms a connection, and the possibility of producing aluminum-magnesium dust is extremely small. The generated welding fumes are mostly oxide particles of metal surfaces and surface impurities. The welding process is equipped with local exhaust air at the station, which can discharge these particles into the atmosphere through the air duct in time, and does not produce the deposition of aluminum and magnesium dust.
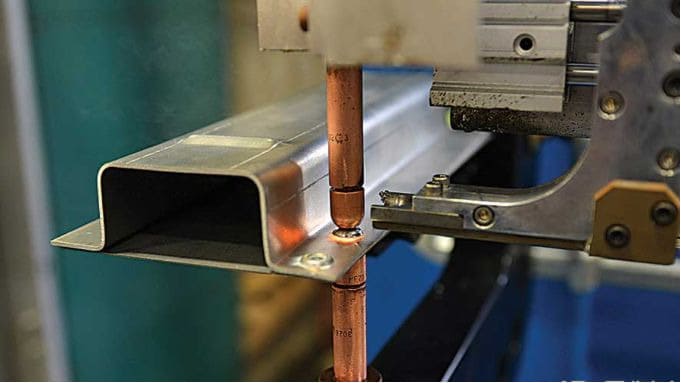
- CMT Cold Transfer Welding and TIG Welding
In these two welding processes, due to the protection of inert gas, under high temperatures, the contact between the molten metal and oxygen is insufficient, and under the action of the jet of the arc, aluminum and magnesium metal particles with small particle sizes can be generated and splashed to the In the working environment, the deposition of aluminum-magnesium dust is formed, and there is a danger of aluminum-magnesium dust explosion. It is necessary to do the prevention and treatment of dust explosions.
Process of Aluminum Stamping Parts in Coating
- The principle and function of washing passivation of aluminum alloy stamping parts
Washing passivation refers to removing the oxide film and oil stains naturally formed on the surface of aluminum parts, and wrapping a dense oxide film on the surface of the workpiece through the chemical reaction between the aluminum alloy and the acid solution. The oxide film on the surface of the aluminum parts after stamping, oily welding, and gluing will all have an impact. To improve the adhesion between the glue and the weld, it is necessary to use chemical processes to maintain the long-term adhesive connection and resistance stability of the surface to achieve better welding. . Therefore, all parts that require weldings such as laser brazing and cold metal transfer welding (CMT) need to be washed and passivated.
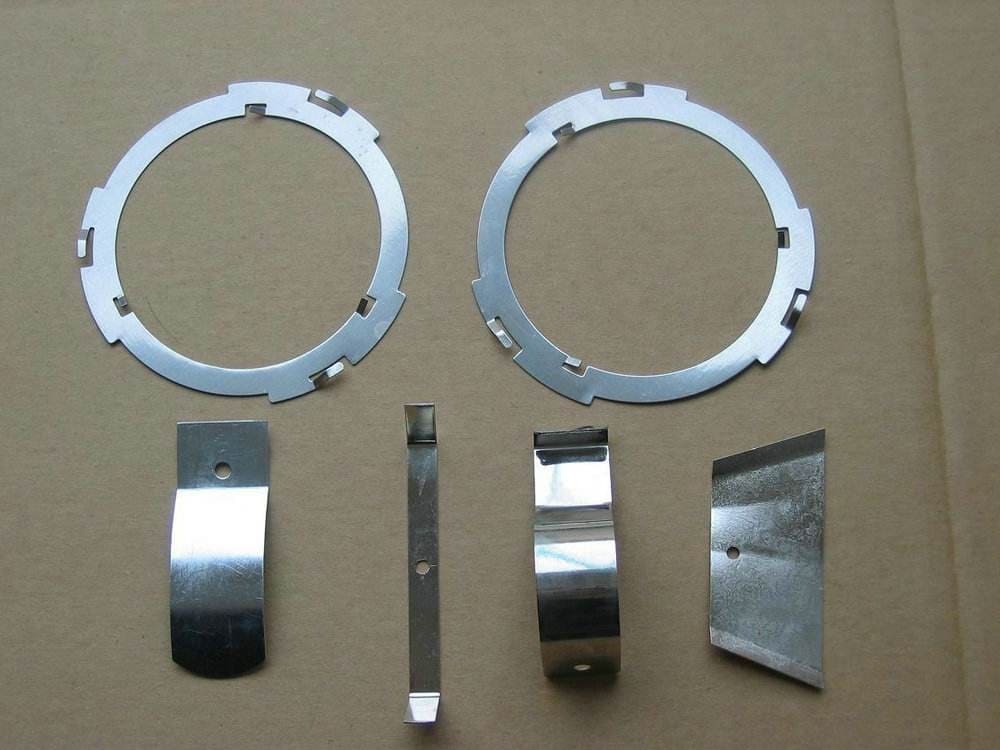
- Process flow of washing and passivation of aluminum alloy stamping parts
The water washing passivation equipment consists of a degreasing area, an industrial water washing area, a passivation area, a clean water cleaning area, a drying area, and an intake and exhaust system. The aluminum parts to be treated are loaded into the cleaning basket, fixed, and lowered into the water tank. In tanks filled with different solvents, it is usually used for long-side pressing. Inside, the parts are repeatedly washed with all the working solutions in the tank. All tanks are equipped with circulating pumps and nozzles to ensure that the tank fluid can flush all parts evenly. The water washing passivation process is: degreasing 1→degreasing 2→water washing 2→water washing 3→passivation→water washing 4→water washing 5→water washing 6→drying, aluminum castings can be omitted from water washing.
- Aluminum alloy stamping parts washing passivation drying process
1) The time for the temperature of the part to rise from room temperature to 140 is about 7 minutes, and the shortest time for the glue to harden is 20 minutes.
2) The aluminum parts are raised from room temperature to the holding temperature for about 10 minutes, the aluminum holding time is about 20 minutes, and the cooling time for the aluminum parts from the holding temperature to part temperature 100 is about 7 minutes. The overall drying process of the piece was 37 min.