Aluminum Micro-Channel Tube
- Aluminum micro-channel tube is a kind of high-precision extruded aluminum tube, also called multi-port extrusion tube (MPE tube) and an aluminum micro-channel tube. This flat, rectangular extruded tube is made of several channels that increase heat transfer through a higher surface-per-volume ratio.
- Aluminum micro-channel tubes are available in various sizes and aluminum alloys, ensuring the best performance for the purpose required, and can be delivered with zinc or flux coating, ready for assembly and oven brazing.
PDF Download
Products Category of Aluminum Micro-channel Tube
CHAL is an excellent factory for producing aluminum micro-channel tubes, so aluminium micro-channel tubes can provide various multi-channel aluminum tubes with different sizes, shapes, and aluminum alloys. The following products are available for inquiring:
- Aluminium Micro-channel Tube
- Aluminium Multi-Port Tube
- Parallel Flow Aluminium Flat Tube
- Zinc-coated Aluminum Tube
- Pre-Flux Coated Aluminium Tube
- Si Flux Coated Aluminum Tube
- Large Multi-channel Tube(width range 50-200mm)
- Double Row Joint Multi-channel Flat Tube
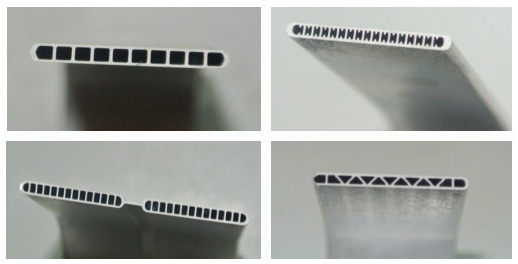
Product Dimension Control Range of Aluminum Micro-Channel Tube
Item | Range |
Fixed length | 200mm-4000mm |
Width (aluminum micro-channel tubes) | 8mm-60mm |
Width (large multi-channel) | 60-200mm |
Thickness | 1mm-5mm |
Wall thickness | 0.15mm-0.6mm |
Thickness of zinc spraying | 5g/㎡-15g/㎡ |
Thickness of flux coating | 8g/㎡-25g/㎡ |
Tolerance of Aluminum Micro-channel Tube
Width | Thickness | Wall Thicknesses | Length | Straightness (side) | Straightness (front) | Twisty |
±0. 04mm | ±0. 03mm | ±0. 05mm | ±0. 30mm | ≤L*0.2% | ≤L*0. 25% | ≤L*0.15% |
Coating Standard and Corrosion Resistance of Aluminum Micro Channel Tube
Corrosion resistance (common alloy) | Salt spray test: ≥750 hours |
Zn Coating standard | 8±2g/㎡, 10±2g/㎡, 13±2g/㎡ |
Flux Coating standard | 10-15±2g/㎡ |
Alloy Options for Aluminum Micro-channel Tube (Accept Customized Service)
At CHAL, we’re committed to manufacturing aluminum tubing products of the highest quality. To do this, quality control is according to rigorous criteria covering quality, and we work hard to drive innovation, finding and testing new alloys as we seek to develop tubing products for the engineering projects of tomorrow.
Chemical Composition of Aluminum Micro-channel Tube
No | Alloy Grades | Si | Fe | Cu | Mn | Mg | Cr | Zn | V | Ti |
1 | 1050 | ≤0.25 | ≤0.40 | ≤0.05 | ≤0.05 | ≤0.05 | — | ≤0.05 | ≤0.05 | ≤0.03 |
2 | 1100 | ≤0.95(Si+Fe) | — | 0.05~0.20 | ≤0.05 | — | — | ≤0.10 | — | — |
3 | 1197 | ≤0.15 | ≤0.20 | 0.40~0.55 | 0.10~0.20 | ≤0.03 | ≤0.05 | ≤0.05 | ≤0.05 | ≤0.05 |
4 | 3102 | ≤0.40 | ≤0.70 | ≤0.10 | 0.05~0.40 | — | — | ≤0.30 | — | ≤0.10 |
5 | 3R03 | ≤0.15 | ≤0.15 | ≤0.01 | 0.90~1.10 | ≤0.03 | ≤0.03 | ≤0.05 | ≤0.05 | ≤0.05 |
Mechanical Properties of Aluminum Micro-channel Tube
No. | Alloy Grades | Temper | Tensile Strength | Yield Strength | Elongation |
1 | 1050 | O/F/H111/H112 | ≥65 | ≥20 | ≥25 |
2 | 1100 | O/F/H111/H112 | ≥75 | ≥20 | ≥25 |
3 | 1197 | O/F/H111/H112 | ≥80 | ≥25 | ≥20 |
4 | 3102 | O/F/H111/H112 | ≥75 | ≥20 | ≥25 |
5 | 3R03 | O/F/H111/H112 | ≥80 | ≥25 | ≥20 |
3 Kinds of Coating Solutions for Aluminum Micro-channel Tube
Coating Material | Pre- Flux Coating | NOCOLOK Si Flux Coating | Zinc Coating |
SampleImages | ![]() | ![]() | ![]() |
Main Components | Flux(K1-3A1F46) | NOCLOK F1ux: 66.6%Silicon Powder: 33.3%Or according to customers requirements | Zinc powder |
Features | No need for extra brazing in brazing line but use aluminum fin material with a layer | The Si-flux to spray solder flux when brazing and the fin material can be bare foil | The tube with zinc-coated will highly enhance corrosion resistance performance |
How to start our cooperation (procedures)?
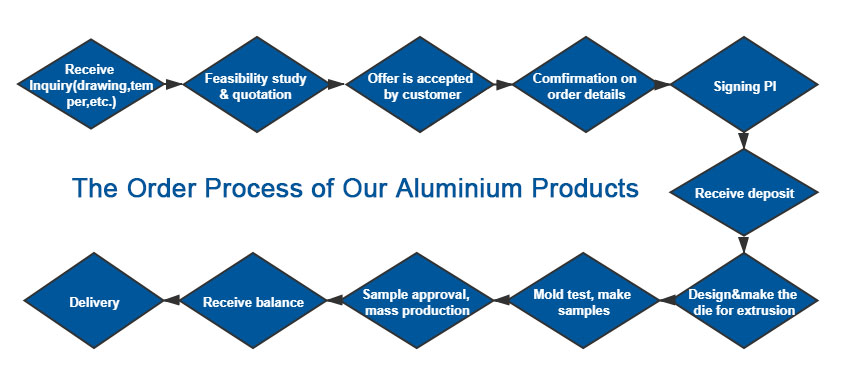
Advantages of Silicon Flux Coated Aluminium Micro-channel Tube
Compared with traditional aluminum tube, aluminum micro-channel tube with solder layer on the surface has a greater advantage:
- Improve quality, enhance brazing, guarantee 100% brazing quality anti-corrosion, and be environment-friendly.
- Reduce cost: cheaper fin material replaces composite clad fin material, the thickness can be reduced up to 30%, reduce cost greatly, lower consumption of solder, and fewer defects.
- Working condition improvement: no air flux particles, effluent reduction, and harmful gas sent out.
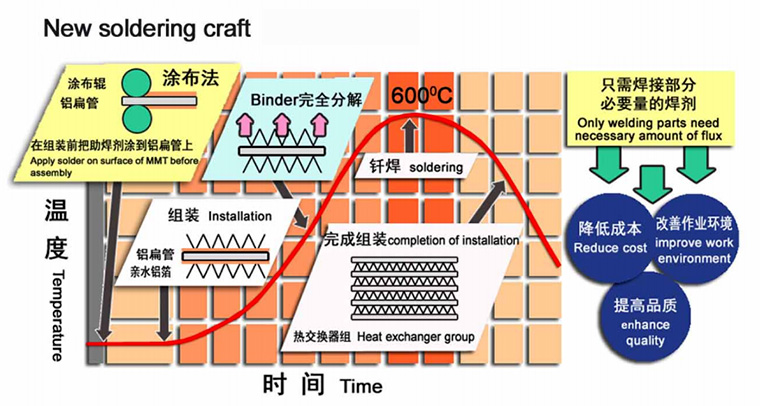
Micro-channel Technology in Heat Exchanger
Aluminium micro channel tube is the alternative solution to cooper tube and welded aluminum manifolds for increasing efficiency and reducing the overall cost.
- Reduce your system refrigerant charge by as much as 35%.
- improve your energy efficiency/coefficient of performance by up to 10%.
- Reduce your raw material consumption by more than 40%.
- Reduce your manufacturing cost compared to aluminum and copper heat exchangers.
- Easily recycle.

Applications of Aluminum Micro-channel Tubes
- Heat transfer for the automotive market
- Heat transfer for the HVAC&R (heating, ventilation, air conditioning, and refrigeration) market
- Air conditioning installation
- Industrial production
- Solar thermal
CHAL Aluminium Corporation focuses on the research and development of aluminum, we work with a famous academic institution and industrial association. Our researchers and academic partners take part in the business & technical development of the processing and producing aluminum products. We work on moving boundaries of how aluminium is used. We develop and design solutions that benefit the improvement of aluminum performance both technically and economically. CHAL Aluminium Group has 5 R/D centers across China.
Production Line and Capacity
CHAL Aluminium Corporation is one of the biggest aluminum micro-channel tube suppliers in China, comprehensive annual capacity can reach 20000T.
Main Production Line | Qty | Products | Annual Capacity |
Extrusion Line | 6 | MPE Tube in Coil | 20000T |
Cutting Line | 15 | Fixed Straight Length | 15000T |
Tooling R&D Manufacturing Center | 1 | Extrusion Die | 5000PCS |
Zinc Coating | 6 | Zinc Coated Tube | 20000T |
Si-Flux Coating | 1 | Si-Flux Coated Tube | 2000T |
Patents
35 Invention Patents and 198 Utility Model Patents are certified.
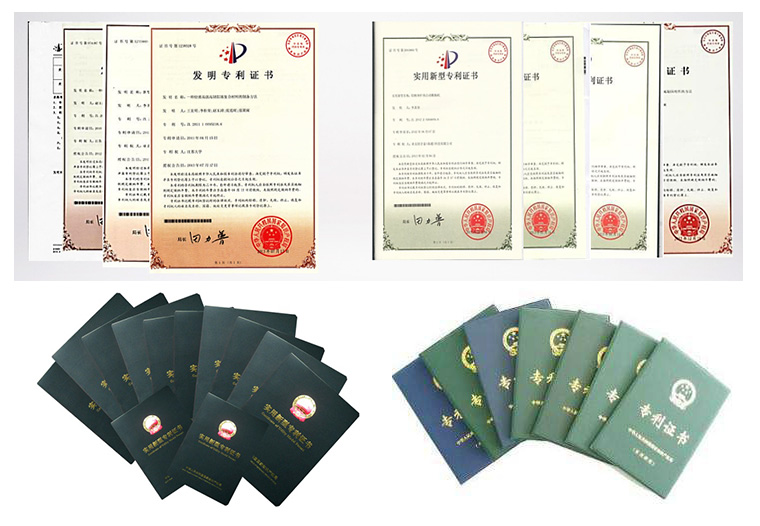
Production Process
The manufacturing processes consist of heat molds and aluminum billet, extrusion, zinc spraying, cooling(flux coating), rolling and cutting.
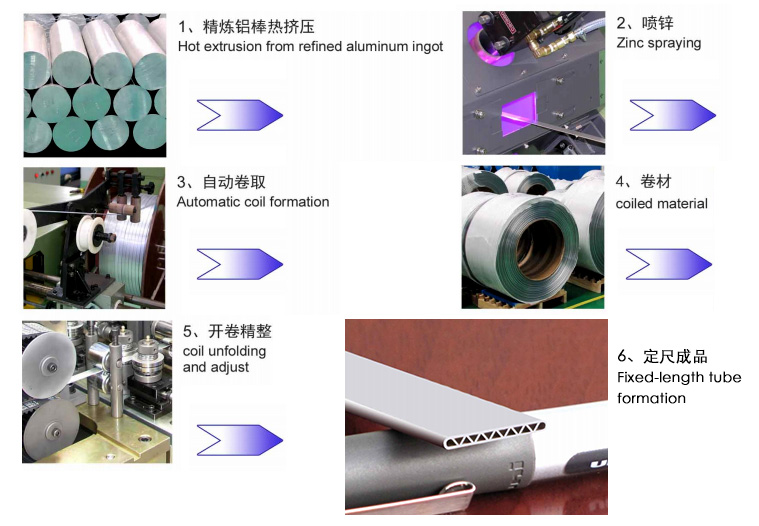
Production Equipment
Aluminum Billet Cast Equipment (Germany)

Extruder: 1650T/1800T/2000T/2600T/3600T
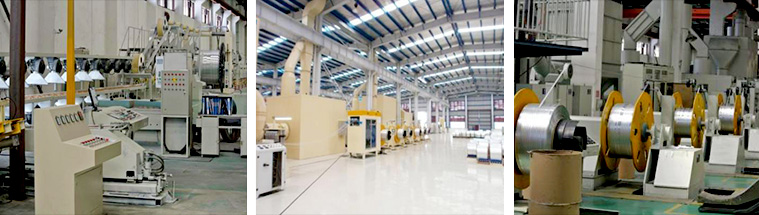
Metallisation Zinc Spray System (UK)
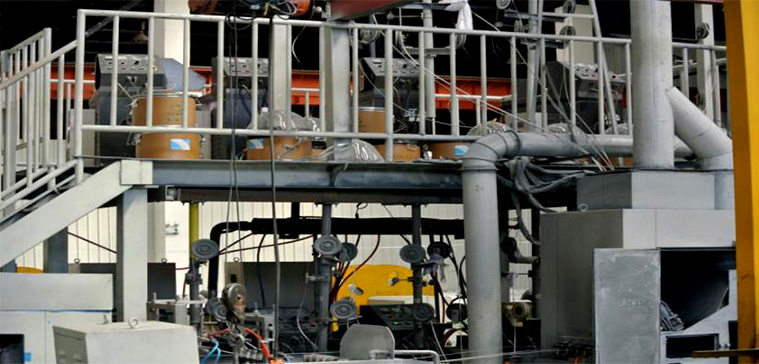
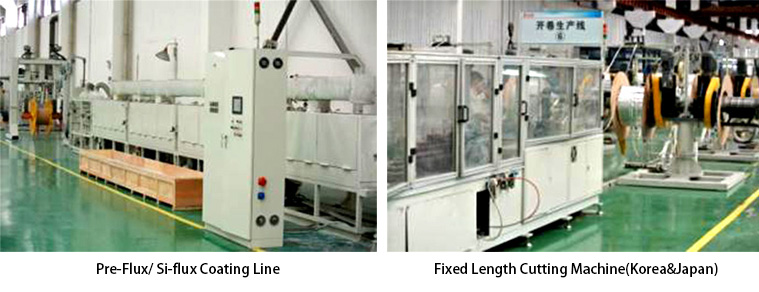
Certificates
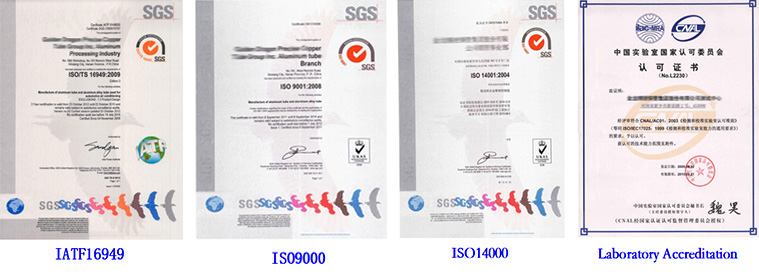
Testing Instruments
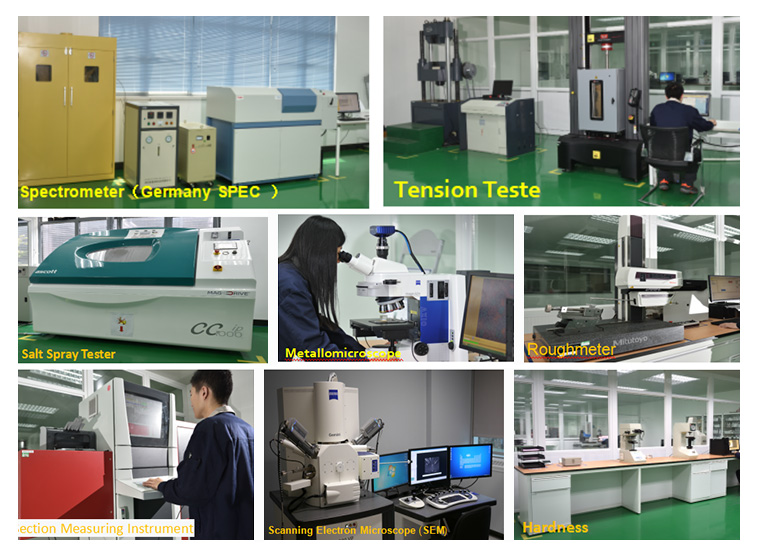
Burst Pressure Test
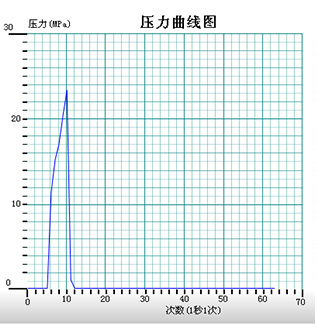
Cooperation Partners
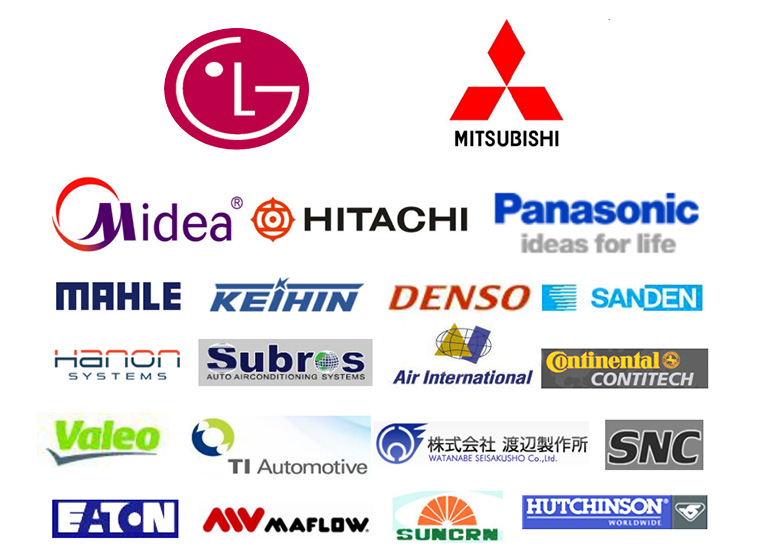