Aluminum profiles are new products formed from aluminum billets. Aluminum profiles meet the material needs of various fields through different forms. Aluminium profile is different from steel, it is a lighter, more durable and more environmentally friendly material. This article summarizes the characteristics of aluminum profiles and knowledge points that people do not often mention, so that you can know more about aluminum profiles when purchasing aluminum profiles.
Basic properties of aluminum
Silver white can form a layer of the oxide film to prevent metal corrosion in humid air, relative density of 2.7g/cm3, melting point of 660℃, boiling point of 2327℃, high specific strength, good electrical and thermal conductivity, high reflection properties, and oxidation resistance.
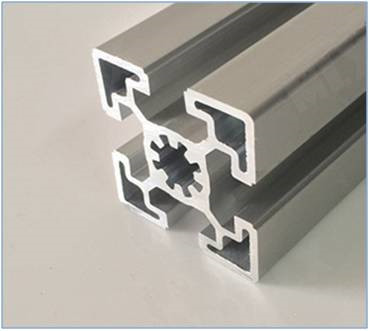
Commonly used aluminum profile grades
The first digit of the grade represents the aluminum alloy series, the second digit represents the modification of the original aluminum alloy, and the last two digits represent the purity of the aluminum alloy in the same group.
1100: For processing parts that require good formability and high corrosion resistance, but do not require high strength. Such as storage containers, sheet metal workpieces, deep-drawn concave vessels, heat exchangers, printing plates, nameplates, reflectors, etc.
2011: Free-cutting alloy, good machinability, and high strength, but poor corrosion resistance, suitable for volume shafts, optical components, screw heads, screws, and machining products that require good cutting performance.
3003: The performance of 1xxx series alloys is higher than that of 1xxx series alloys, such as kitchen utensils, food, and chemical products processing and storage devices, tanks and tanks for transporting liquid products, and various pressure vessels and pipes for sheet processing.
4A01: High silicon content, heat-resistant, and wear-resistant, it belongs to building materials, mechanical parts, forging materials, and welding materials.
5052: The most representative alloy of medium strength (5083 is the highest), with good corrosion resistance, weldability, and formability, especially high fatigue strength, and good seawater resistance, used in the manufacture of aircraft fuel tanks, oil pipes, and vehicles, Sheet metal parts of ships, instruments, street lamp brackets and rivets, hardware products, etc.
6061: Heat-treated corrosion-resistant alloy. Treated with T6, it can have a very high endurance value, but the strength of the welded joint is low, so it is suitable for screws, ships, vehicles, and land structures.
6N01: A medium-strength extrusion alloy, which can be used for large-scale thin meat profiles with complex shapes, with good corrosion resistance and weldability. Suitable for vehicles, land structures, and ships.
6063: a representative alloy for extrusion, with lower strength than 6061, good extrudability, can be used as profiles with complex cross-sectional shapes, good corrosion resistance and surface treatment, suitable for building highway guardrails, vehicles, furniture, home appliances Products, and decorations.
7072: Low electrode potential, mainly used for anti-corrosion covering leather, also suitable for heat exchanger fins, air conditioner aluminum foil, and ultra-thin strips.
7075: One of the alloys with the highest strength among the aluminum alloys, but the corrosion resistance is not good. The covering with 7072 can improve its corrosion resistance, but the cost increases. Suitable for aircraft, ski poles, and thick plate forgings.
Reasonable selection of aluminum profiles according to the application field:
If the product is required to be hard, and the surface treatment is coarse wire drawing or coarse sand surface, choose 5000 series aluminum alloy, commonly used: 5052
If the surface treatment requirements of the product are high, there should be no sand holes or traces of profiles, and 6000 series aluminum alloy should be used. Commonly used: 6063/6061
If the product requires a low price and needs to be stretched and re-examined, choose 2000 series pure aluminum, commonly used: 2011
If the product requires high strength and high hardness and needs to be used for load-bearing structure, choose 7000 series aluminum alloy, commonly used: 7075
Types of aluminum profiles
The types of aluminum profiles can be divided into three categories according to the state of the profiles
- Profiles: aluminum profiles, aluminum pipes, aluminum bars, etc.
- Sheets: aluminum sheet, aluminum foil, aluminum strip (coil)
- Casting: aluminum castings, aluminum pellets
Among them, aluminum sheet is the most widely used product in aluminum profiles. Among them, the aluminum sheet is the most widely used product in aluminum profiles. Aluminum sheets can be divided into single-layer aluminum sheets, conforming-layer aluminum sheets, honeycomb aluminum sheets, and other different varieties.
Single layer aluminum plate
It can be used for electronic product casings, home appliance product casings or internal thermal conductors, etc. The finished aluminum shell is completed by three processes: metal stamping die drawing, surface pretreatment, and coloring.
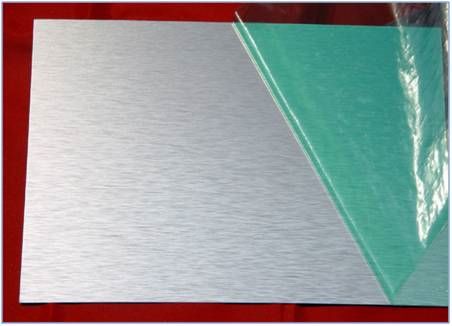
Aluminum-plastic composite panel
It is a new type of material that is made of surface-treated aluminum plate with coating and baking paint as the surface, polyethylene and polypropylene plastic mixed as the core layer, and processed through a series of processes.
It can be used in the decoration of curtain walls, inner and outer walls, halls, restaurants, shops, conference rooms, etc., and can also be used in the reconstruction of old buildings, as counters, furniture surfaces, vehicle inner and outer walls, etc.
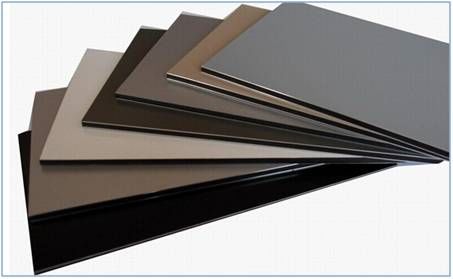
Honeycomb aluminum plate
The composite honeycomb structure is adopted, and the preformed box-shaped panel and back panel are hot-pressed and composited with the aluminum alloy honeycomb core material. It is suitable for building curtain wall decorations, ceilings, buses, trains, subways and rail transit vehicles, commercial transport vehicles and container car bodies, shipbuilding, billboards, and interior decoration projects.
In general, aluminum parts are used to decorate the shell of the product, with a high tensile surface. The material is generally 0.4-0.8mm thick, and the grade is 6063/6061 or pure aluminum.
The functional shell is made of aluminum parts, with a bottom stretching and bending structure. The material is generally 0.8-1.2 thick, and the harder grades 5052/7075, or special grades are selected.
If aluminum parts are used on the shell of electronic products, a laser engraving oxide layer is required for conductive grounding, because the oxide layer is not conductive after anodization.