Aluminum billets are cylindrical blocks of aluminum that are used as a starting material for a variety of manufacturing processes. They are typically produced by melting and casting scrap aluminum or bauxite ore. Aluminum billets are available in a wide range of sizes and shapes, and they can be made from a variety of aluminum alloys. However, these billets require further processing and machining to transform them into the desired shapes and dimensions. This article delves into the methods employed to shape aluminum billets, including extrusion, forging, CNC machining, and other techniques, highlighting the importance of quality control throughout the process.

Preparation of Aluminum Billets
Before initiating the shaping process, it is essential to inspect and ensure the quality of incoming aluminum billets. Once verified, the billets are cut into manageable lengths. To facilitate subsequent processing, billets may undergo heating or preheating, optimizing their malleability and reducing the likelihood of defects during shaping.
Extrusion Process
Extrusion stands as one of the most widely used methods for shaping aluminum billets. It involves forcing the heated billets through a die to create profiles with specific cross-sectional shapes. Prior to extrusion, billets are loaded onto handling equipment, and homogenization heat treatment ensures uniform properties. The extrusion press exerts immense pressure to shape the aluminum billet, with the die design being a crucial factor in determining the final product’s dimensions. Once extrusion is complete, the profiles are cooled, stretched, cut to specified lengths, and may undergo surface treatments and finishes to meet the desired requirements.
Forging Process
Forging is another popular method for shaping aluminum billets. It involves subjecting the billets to compression forces to change their shape while maintaining their integrity. Billets are heated to the appropriate temperature, and carefully controlled to prevent overheating or inadequate shaping. The forging press, equipped with appropriately designed dies, applies pressure to mold the billet into the desired shape. The process may involve open-die, closed-die, or impression forging. Heat treatment and annealing processes follow, ensuring optimal material properties. After forging, the products may undergo machining and finishing operations like trimming and deburring to achieve the desired final shape.
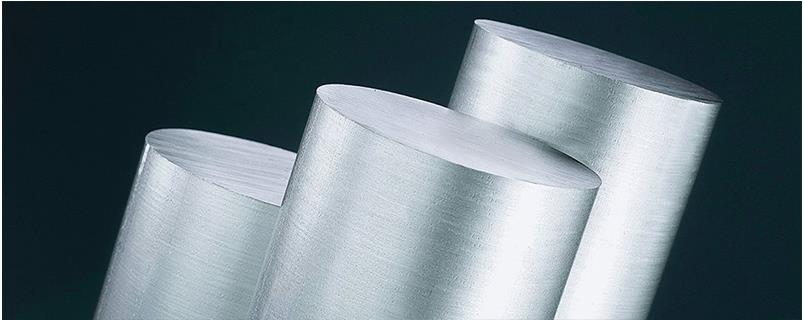
CNC Machining
Computer Numerical Control (CNC) machining is a precise and efficient method used to shape aluminum billets into intricate and custom designs. Before machining, the billets are prepared by fixing them securely and aligning them accurately for precise cutting. Cutting tools are carefully selected and set up for operations like milling, turning, and drilling. CNC machines are programmed to follow the desired dimensions, and the machining process begins. Quality control measures and inspections are implemented during and after machining to ensure the dimensional accuracy and surface finish of the final product.
Other Processing Methods
In addition to extrusion, forging, and CNC machining, there are alternative techniques for shaping aluminum billets. Rolling and drawing are commonly used for specific applications. Rolling involves passing the billet through a set of rollers to reduce its thickness and shape it accordingly. Drawing involves pulling the billet through a die to elongate and shape it into a desired form. These additional methods cater to various manufacturing requirements, offering flexibility in shaping aluminum billets.
Quality Control and Inspection
Throughout the entire process of shaping aluminum billets, quality control and inspection play a vital role. Non-destructive testing methods, such as ultrasonic inspections and visual inspections, are employed to detect any potential defects. Dimensional checks and metrology techniques ensure that the final products meet the specified tolerances. Material testing for mechanical properties, such as hardness and tensile strength, verifies the billets’ integrity and suitability for the intended application.
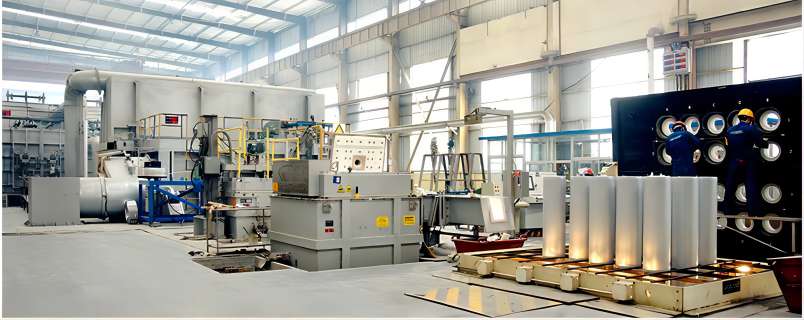
Surface Treatment and Finishing
To enhance the performance, aesthetics, and durability of the final products, surface treatment, and finishing processes are often employed. Surface treatments like anodizing, painting, or powder coating provide an added layer of protection against corrosion and enhance the appearance of aluminum products. The billets undergo cleaning and preparation before the application of surface treatments. Surface finishes, such as polishing or brushing, are also employed to achieve the desired visual appeal and texture. Quality control and inspection are conducted after surface treatment to ensure the desired outcome and adherence to specifications.
Conclusion
The processing and machining of aluminum billets is a complex and diverse field. There are a variety of methods that can be used to shape aluminum billets, and the choice of method will depend on the specific application. The importance of proper techniques and quality control in achieving desired products cannot be overstated.
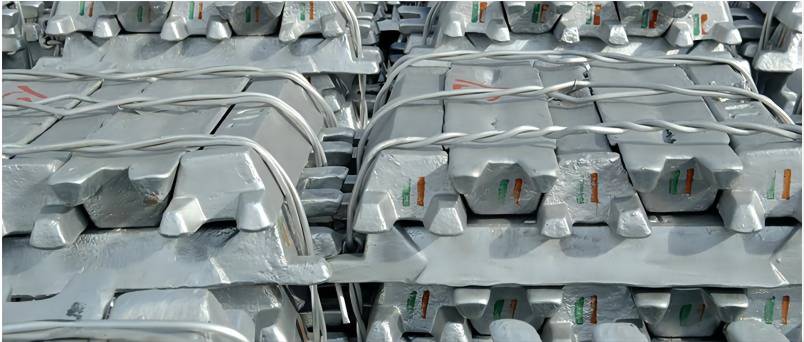
The future of aluminum billet processing is bright. With the development of new technologies, such as additive manufacturing, the possibilities for shaping aluminum billets are endless. As the demand for aluminum products continues to grow, the need for efficient and cost-effective methods of processing aluminum billets will only increase.