In electrical and power transmission applications, aluminum wire is widely used due to its cost-effectiveness, lightweight nature, and reasonable conductivity. However, the performance of aluminum wire isn’t solely dependent on its material properties; wire size plays an equally crucial role in determining how efficiently and safely it can transmit electricity. This article delves into the intricacies of aluminum wire size, exploring its impact on factors like current carrying capacity, voltage drop, and signal integrity. By understanding these key considerations, you can make informed decisions when designing and implementing electrical systems.
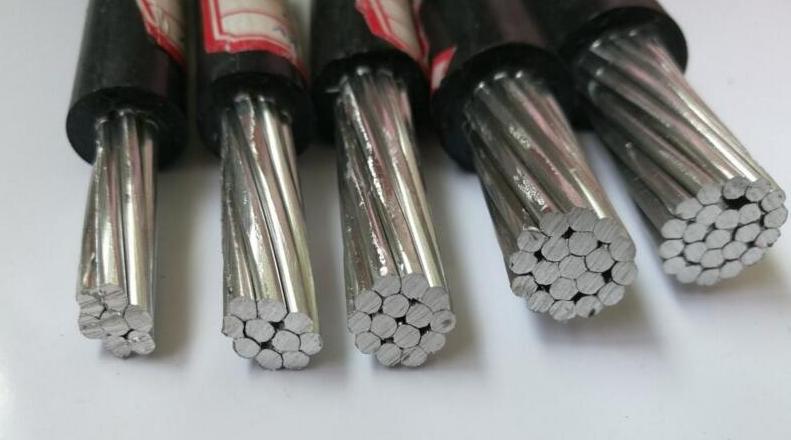
Understanding Aluminum Wire Size Basics
Wire sizing is generally measured in American Wire Gauge (AWG), where a lower gauge number indicates a thicker wire, while a higher gauge number means a thinner wire. This sizing directly impacts an aluminum wire’s ability to carry current, handle load, and maintain safety standards. Understanding these basics is the first step in selecting the optimal wire size for any electrical project.
Gauge Measurement
Aluminum wire size is most often classified by the AWG system, which numerically ranks wires based on their diameter. For instance, a 6 AWG wire is thicker than a 10 AWG wire, and this increased thickness offers different performance benefits. Diameter size is critical because it determines the amount of electrical current the wire can carry without excessive resistance or heat buildup.
Key Concepts:
- Cross-sectional Area: The larger the cross-sectional area, the greater the wire’s ability to conduct electricity without excessive heat buildup.
- Resistance: The resistance of a wire increases with its length and decreases with its cross-sectional area. Higher resistance leads to increased voltage drop and power loss.
- Skin Effect: At higher frequencies, current tends to flow primarily on the surface of the conductor, reducing the effective cross-sectional area and increasing resistance.
Aluminum wire sizing isn’t simply about fitting a wire into a system. Each gauge size impacts the wire’s resistance, conductivity, and load-bearing capacity.
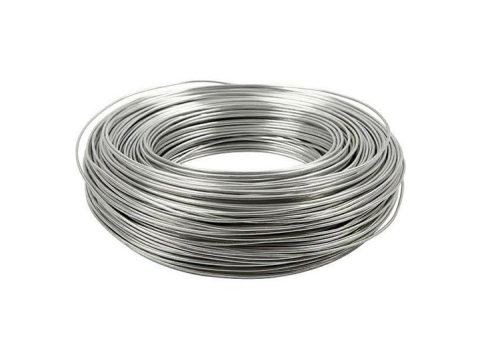
Factors Influenced by Aluminum Wire Size
The size of aluminum wire has significant effects on various aspects of electrical performance. From conductivity to heat resistance, several factors rely on proper sizing to maximize efficiency and safety. Below are the primary factors influenced by aluminum wire size.
1. Electrical Conductivity
Larger aluminum wires carry current more effectively, with reduced resistance compared to smaller wires. This increased conductivity allows electricity to flow more smoothly, enhancing efficiency and reducing energy loss. Smaller wires, due to higher resistance, may not transmit power as effectively, leading to potential performance issues.
2. Heat Generation
One major concern with smaller wires is their tendency to generate more heat. Higher resistance within thinner wires causes energy to dissipate as heat, which can raise the risk of overheating and even fire hazards. Larger wires distribute electricity with minimal heat generation, contributing to a safer operating environment, especially under high current loads.
3. Load Capacity and Current Flow
The wire size dictates the maximum load it can carry safely. For example, thicker aluminum wires can handle larger loads and carry more current without issues, making them suitable for heavy-duty applications. Using an undersized wire in high-load situations can lead to overheating, voltage drops, and potential system failures.
4. Voltage Drop
Voltage drop occurs when there’s a reduction in voltage due to resistance along the length of the wire. This is particularly critical in long-distance wiring. Thicker aluminum wires minimize this drop, ensuring the transmitted power maintains its intended strength and effectiveness over distance.
5. Durability and Longevity
Large-diameter wires are more durable in high-load situations, as they can handle greater stress without degrading. This increased durability enhances the wire’s longevity and minimizes the need for frequent replacements.
Wire size is more than just a measurement; it directly impacts essential performance factors, from conductivity to safety. Selecting the appropriate aluminum wire size optimizes these factors, ensuring safe, efficient, and long-lasting electrical performance.
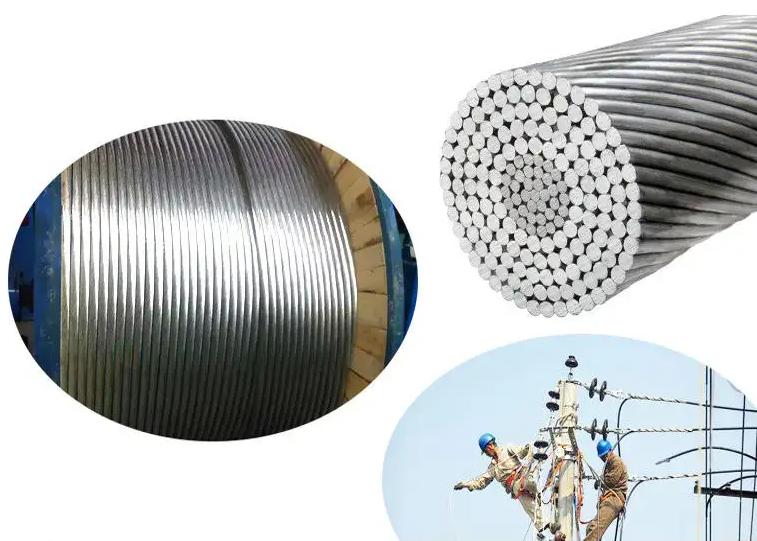
Choosing the Right Aluminum Wire Size for Different Applications
Selecting the correct aluminum wire size depends on the specific requirements of each application. Factors such as power needs, environment, and distance all influence wire size selection. This section explores how to approach wire size selection for various applications.
- Low vs. High-Power Applications: For low-power applications, such as lighting circuits, smaller aluminum wires are often sufficient due to the lower current demand. High-power applications like air conditioning units, industrial motors, or large appliances require thicker wires to manage higher loads without risking overheating or excessive voltage drop.
- Household Wiring: In residential settings, aluminum wiring is commonly used for certain circuits, like those for large appliances. Standard gauge recommendations exist to ensure safety, such as using 10 AWG for dryer circuits or 6 AWG for electric ranges. Choosing a wire size that aligns with these standards helps ensure that household electrical systems run efficiently and safely.
- Industrial and Commercial Uses: Heavy-duty industrial or commercial applications often demand aluminum wires that can handle substantial currents. In these settings, selecting an undersized wire can lead to frequent overheating and costly repairs. Wire gauge calculators, often specific to these environments, provide a helpful resource for choosing the correct size.
- Long Distance vs. Short Distance Wiring: Long-distance wiring setups, such as those seen in power distribution or solar panel installations, face significant voltage drops. Thicker aluminum wires help mitigate this, allowing for reliable power transmission without efficiency losses over distance. Short-distance wiring doesn’t face these challenges as intensely, often allowing for a smaller gauge size.
Different applications have unique requirements, and matching the right aluminum wire size to each ensures maximum efficiency, safety, and durability. Considering factors like power demand, distance, and setting enables informed decisions, especially for complex or high-stakes applications.
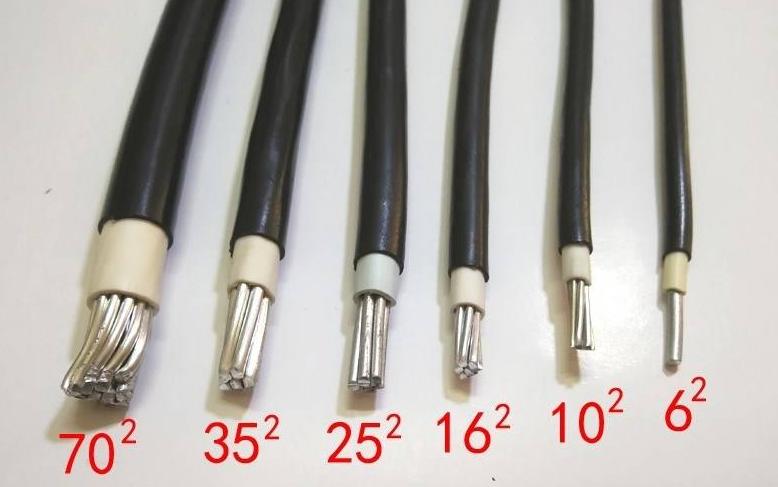
Common Challenges and Mistakes in Selecting Aluminum Wire Size
Selecting the right aluminum wire size can be challenging, especially given the various factors to consider. Errors in this process can lead to serious performance and safety issues. Here, we’ll look at common mistakes and challenges and how to avoid them.
- Underestimating Load Requirements: One common mistake is choosing a wire that is too small to handle the load. This often occurs when users try to save costs by selecting a smaller gauge. However, underestimating the required load capacity can lead to overheating, voltage drops, and even wire failure.
- Cost vs. Safety Trade-offs: While larger wires cost more, cutting costs by opting for smaller sizes can compromise safety. Thin wires can’t handle high currents and may degrade quickly under heavy loads, increasing the risk of fires and accidents. Always prioritize the correct wire size over cost-saving.
- Compatibility with Other Materials: When using aluminum wires in systems that also contain copper, compatibility issues can arise. Mixing metals can lead to corrosion, increasing resistance and creating hotspots in the wiring. Using connectors rated for aluminum-copper compatibility, or considering aluminum-only systems, helps mitigate these issues.
Avoiding these common mistakes can prevent costly errors and ensure that aluminum wire performs as intended.
Selecting the appropriate aluminum wire size is a critical decision that can significantly impact the performance and safety of electrical systems. By understanding the factors influenced by wire size, such as current carrying capacity, voltage drop, and signal integrity, you can make informed choices that optimize system efficiency and minimize potential problems. Remember to consider the specific requirements of your application, adhere to relevant electrical codes, and consult with qualified professionals when necessary.