The global push for sustainable energy has placed wind power at the forefront of renewable technologies. Wind turbines, towering structures harnessing the kinetic energy of wind, are pivotal in this transition. However, the efficiency and sustainability of wind energy hinge significantly on the materials used in their construction, particularly the blades. This article delves into the potential of aluminum, a versatile and abundant metal, to enhance wind turbine blade design, focusing on its strength, lightness, and environmental benefits. We will explore how aluminum, while not a direct replacement for composite blade materials, can play a crucial role in improving turbine efficiency and longevity.
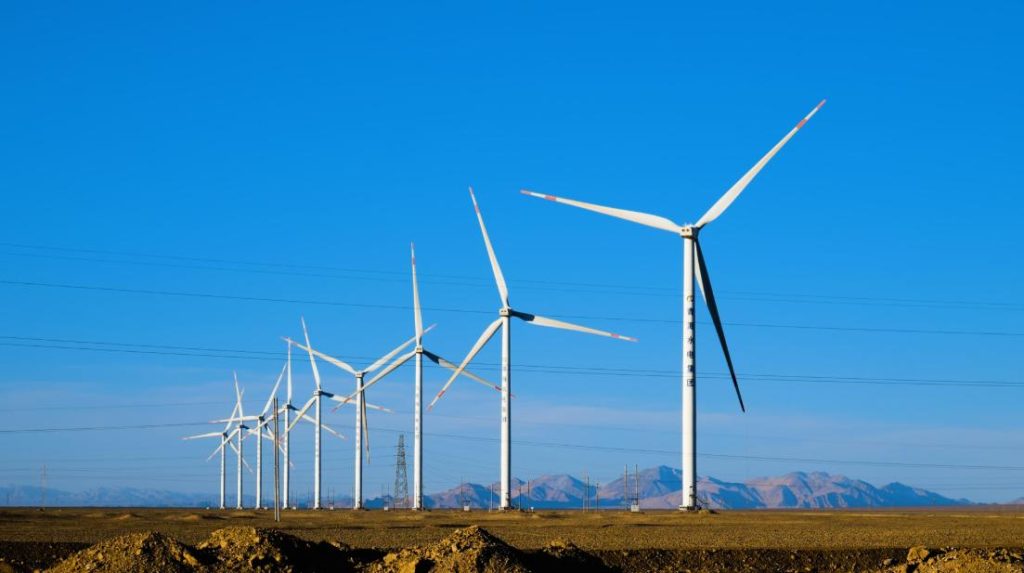
What are the Requirements for Wind Turbine Blade Materials?
Wind turbine blades operate under extreme conditions, facing constant variations in wind speed, temperature, and atmospheric conditions. Therefore, the materials used in their construction must meet stringent requirements to ensure optimal performance and longevity, including:
- High Strength-to-Weight Ratio: Blades must withstand immense aerodynamic forces without excessive weight, which reduces rotor inertia and improves energy capture.
- Fatigue Resistance: Blades endure millions of stress cycles over their lifespan, requiring materials that can resist fatigue cracking.
- Corrosion Resistance: Especially crucial for offshore turbines, materials must withstand saltwater exposure and atmospheric corrosion.
- Durability and Longevity: Blades are expected to operate for 20-25 years, demanding materials with exceptional durability.
- Manufacturability: Materials must be easily formed and shaped into complex aerodynamic profiles.
- Sustainability: Increasing emphasis is placed on recyclability and low environmental impact.
Traditional wind turbine blades primarily utilize fiberglass and carbon fiber composites. While these materials offer high strength and stiffness, they present several challenges. To address these challenges, researchers are exploring alternative materials. Aluminum, with its unique properties, presents a compelling option. While it’s not a direct replacement for the blade’s primary structural shell, it can be beneficial in various components and potentially in hybrid composite structures. Here are the comparison among aluminium blades and traditional materials:
Aspect | Aluminium Blades | Fiberglass-Reinforced Polymers (FRPs) | Carbon Fiber Composites |
Density | ~2.7 g/cm³ | ~2.5 g/cm³ | ~1.6 g/cm³ |
Tensile Strength | 200-570 MPa (depending on alloy) | ~200-400 MPa | ~600-700 MPa |
Corrosion Resistance | Excellent (with coatings or anodization) | Moderate; prone to UV degradation | High but may require additional care |
Manufacturing Cost | Moderate; reduced for recycled aluminium | Low to moderate | High |
Recyclability | Up to 95% value retained during recycling | Difficult to recycle | Limited recyclability |
Unlike composites, aluminium is cost-effective and sustainable, aligning well with the renewable energy sector’s goals. Additionally, advancements in aluminium alloys are enhancing its mechanical properties, opening new possibilities for blade design.
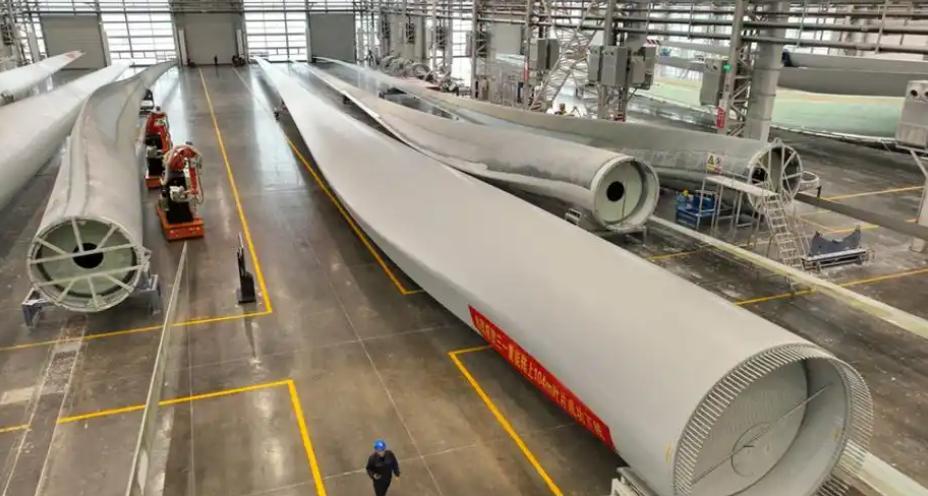
Benefits of Aluminium in Wind Turbine Blades
Aluminium stands out for its ability to address key performance and sustainability metrics. Here’s a detailed look at its advantages:
Stronger
Aluminium offers a high strength-to-weight ratio, making it an excellent choice for wind turbine blades that must endure extreme weather conditions and sustained loads. For example, aluminium alloys such as 7075-T6 have tensile strengths of up to 570 MPa, providing exceptional durability and resistance to fatigue. Unlike fiberglass-reinforced polymers (FRPs), aluminium does not suffer from gradual degradation due to prolonged UV exposure, making it more reliable in the long term. Additionally, its ability to maintain structural integrity under cyclical stress ensures that blades remain functional for decades, reducing the frequency of repairs and replacements.
Lighter
One of aluminium’s most notable benefits is its lightweight nature. At approximately 2.7 g/cm³, aluminium is significantly less dense than many traditional materials. This translates to lighter wind turbine blades, which provide multiple advantages:
- Reduced Mechanical Stress: Lighter blades exert less stress on the turbine’s supporting structures, increasing the overall lifespan of the system.
- Improved Transportation Efficiency: The reduced weight simplifies logistics and lowers transportation costs, especially for offshore wind farms where accessibility is a challenge.
- Enhanced Energy Capture: Lighter blades can operate efficiently even at lower wind speeds, optimizing energy production in areas with less consistent wind conditions. Studies have shown that aluminium blades can reduce overall blade weight by up to 30% compared to traditional fiberglass designs.
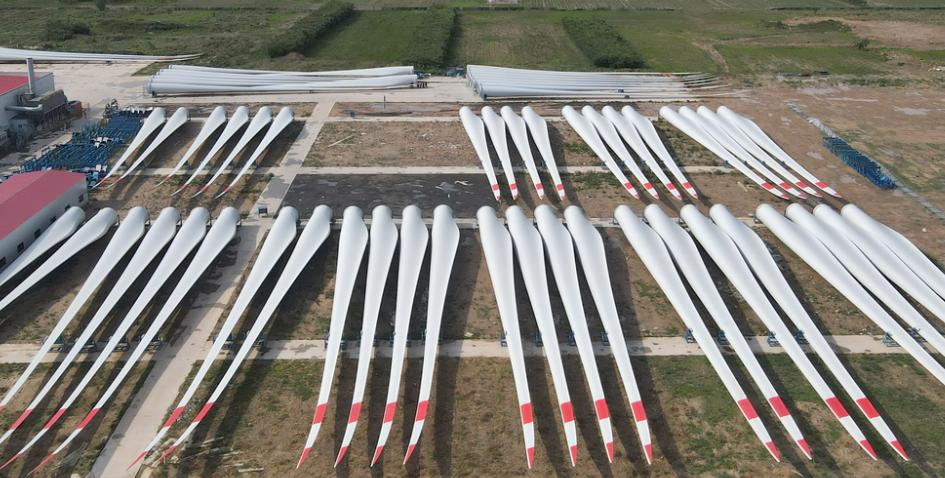
Greener
Sustainability is a cornerstone of modern wind energy, and aluminium excels in this regard. Unlike composite materials, aluminium is highly recyclable, with up to 95% of its value retained during the recycling process. Recycling aluminium requires only 5% of the energy needed to produce primary aluminium, resulting in a significantly lower carbon footprint. Moreover, aluminium’s recyclability addresses one of the wind energy sector’s critical challenges: blade waste management. By transitioning to aluminium, the industry can substantially reduce the environmental impact associated with blade disposal, contributing to a more sustainable energy ecosystem.
Applications of Aluminum in Wind Turbines
Aluminum’s applications in wind turbines extend beyond the blades themselves. It is widely used in:
- Nacelle and Hub Components: Aluminum’s lightweight and corrosion-resistant properties make it ideal for nacelle housings, hub structures, and other non-blade components.
- Tower Construction: Aluminum alloys can be used in tower sections, particularly in hybrid designs, to enhance stability and reduce weight.
- Internal Components: Aluminum is used in various internal components, such as gearboxes, generators, and control systems, due to its thermal conductivity and machinability.
- Potential Hybrid blade designs: Researchers are investigating aluminum matrix composites and hybrid structures that combine aluminum with other materials to improve blade performance.

Challenges and Innovations of Using Aluminium
Challenges
Despite its advantages, the use of aluminium in wind turbine blades presents several challenges:
- Cost of High-Performance Alloys: Advanced aluminium alloys, such as 7075-T6, offer exceptional strength but can be expensive. The initial investment in these alloys can impact the overall cost-effectiveness of turbine production.
- Corrosion Risks: While aluminium is naturally resistant to corrosion due to its protective oxide layer, specific environments—especially marine settings—can accelerate corrosion. Salt spray and prolonged exposure to moisture require the application of protective coatings, anodization, or periodic maintenance to prevent material degradation.
- Adaptation of Manufacturing Processes: The transition from composites to aluminium demands significant changes in manufacturing techniques, including the adoption of advanced joining, forming, and machining technologies. These adaptations often require upfront investments in equipment and workforce training.
- Thermal Conductivity: Aluminium’s high thermal conductivity, while beneficial in many applications, can complicate the manufacturing process. Processes like welding may introduce challenges, such as thermal distortion, that require precision engineering solutions.
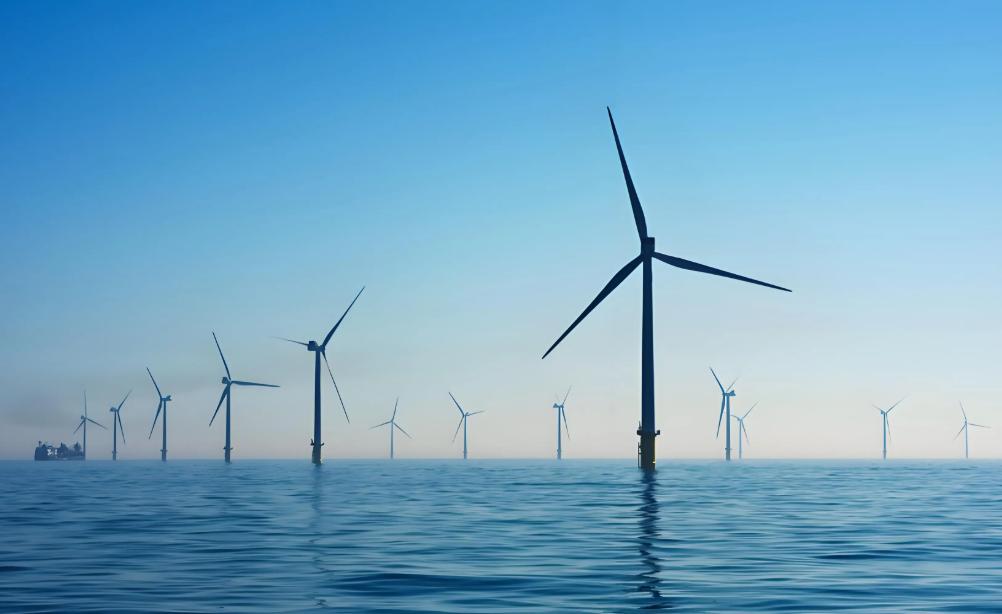
Innovations
Innovative solutions are addressing these challenges and unlocking aluminium’s potential for wind energy:
- Corrosion-Resistant Alloys: New aluminium alloys with enhanced corrosion resistance, such as 5xxx and 6xxx series alloys, are being developed specifically for offshore wind applications. These alloys minimize the need for additional coatings, reducing long-term maintenance costs.
- Protective Coatings and Treatments: Advanced surface treatments, including nanocoatings and plasma electrolytic oxidation, offer superior protection against harsh environmental conditions while preserving aluminium’s lightweight properties.
- Hybrid Material Designs: Combining aluminium with other materials, such as composites or reinforced polymers, leverages the strengths of each. These hybrid designs improve overall blade performance while maintaining manageable costs.
- Additive Manufacturing (3D Printing): Additive manufacturing technologies are enabling the precise and efficient production of complex aluminium components. This approach reduces material waste and offers new possibilities for optimizing blade designs.
- Cold Spray Technology: This innovative deposition process allows for the application of aluminium coatings without melting the material. It enhances surface properties, including wear and corrosion resistance, making it suitable for demanding environments.
Looking Forward
Aluminium’s unique properties make it a strong candidate for the future of wind turbine blades. Its combination of strength, lightness, and sustainability aligns perfectly with the renewable energy sector’s goals. While challenges remain, ongoing innovations in material science and manufacturing are paving the way for broader adoption of aluminium in wind energy.