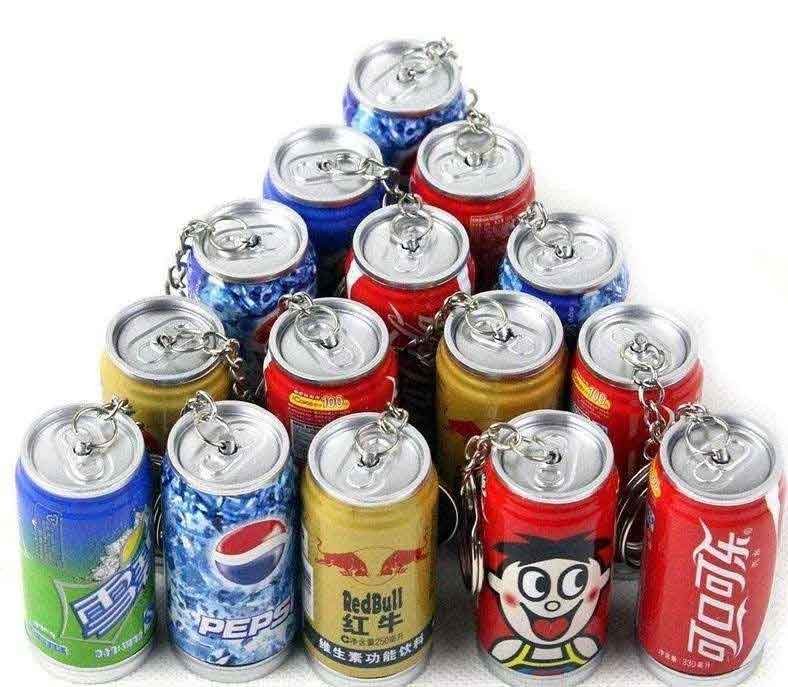
In summer, beverages in cans such as Coke and Sprite must be the most popular drinks. But, did you know that cans are made from aluminum circles? If you were to ask what was inside the bulging circle on the edge of the can, you probably wouldn’t be able to answer.
The first rules out an option for you – this layer of circles is not hollow.
The process of making cans from aluminum wafers
I guess I can’t even think of it. This layer of circles is surrounded by liquid. What kind of liquid is that? The things wrapped in this layer of circles have a lot to do with the manufacturing process of the cans themselves. The cans of cans are punched out of aluminum sheets. This aluminum sheet is about 0.3 mm thick. The punch is placed on a tool called a drawing die.
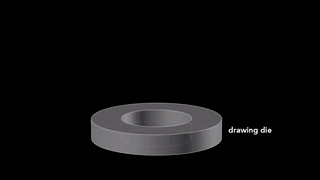
Next, a cylindrical object (a punch) is slammed into the aluminum sheet from top to bottom, forming a short cylindrical object like an ashtray. This process is called stamping.
However, after punching only once, the aluminum circle is still very wide and thick, and it has not yet reached the shape of the final can. Therefore, it is necessary to continue stamping.
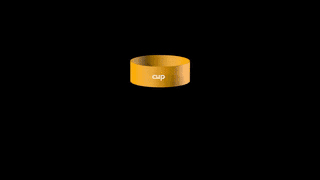
Each punch makes the short cylinders formed from the aluminum sheets thinner, with smaller radii, and at the same time, taller.
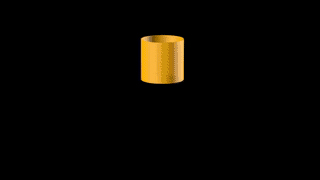
After a few punches, the round aluminum sheet at the beginning has the shape of a pop-top can.
Now there are only 2 steps left, and a can is made.
The remaining 2 steps, one is to make the sunken bottom of the can, and the other is to seal it.
Making the dented butt of a can requires a dome-shaped tool. The manufacturing process is similar to stamping, which is to press the can on the half dome to punch out a concave shape.
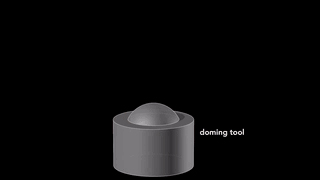
But why do soda cans need a sunken butt?
Because the sunken butt is like an arch bridge and can withstand more pressure.
All of the above processes take only one-seventh of a second.
After trimming the top of the can, you can spray the can with the outer packaging.
The inside of the aluminum can should also be sprayed with a coating, otherwise the acidic beverage will react with the aluminum, you will drink a lot of aluminum, and the nervous system will become demented. (Otherwise, don’t eat fritters made of alum (potassium aluminum sulfate dodecahydrate), the reason is the same.)
Next, pull out a thinner neck for the can to prevent the thin aluminum can from wrinkling.
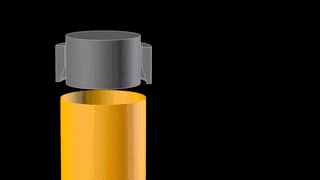
Now, on to the most crucial part – sealing the can.
First, the edge of the neck is bent to create a flanged edge.
Then, there is the wonderful double-seaming drama.
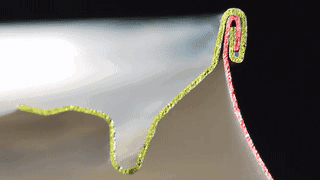
In 1810, tinplate cans were invented. In the beginning, the top and bottom of the can were welded directly to the round can, so the food inside was often contaminated with welding materials such as lead.
The double roll seal that is common in cans now does not have this problem. The double roll seal is a relatively new invention. In 1894, the AMS machine company began producing double-seal double-seal cans.
What is double wrapping?
Take a look at the picture below. The roll edge and lid (top) form such a spring roll shape.
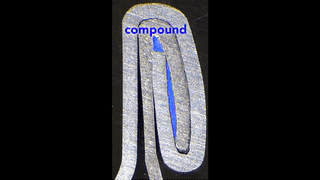
The double roll seal looks nothing special, but it requires a lot of precision. A 1mm difference will cause the capping and sealing process to fail.
However, the double roll seal itself cannot completely isolate the inside and outside of the can. See the gap in the double roll seal?
These gaps are filled with a liquid sealing compound to prevent gas from can escaping through the gaps in the bead and prevent external contaminants from entering the can.
So, what’s in the sealant?
Sealants typically contain a mixture of latex, rubber or resins. These substances are dissolved in an oily solvent and then poured onto the rim of the can top to form a film that solidifies into a film that fills the gap during the double-seal process.
So, the round-rolled edge of the cans we usually drink is wrapped in a greasy liquid. Totally did not think of it.