Now the lightweight of automobiles has become a trend in automobile manufacturing. Aluminum is a high-performance yet light metal material, so Aluminium Die Casting Parts are the best choice for car engine cylinders. This article will explain why Aluminium Die Casting Parts are the best choice for engine cylinders.
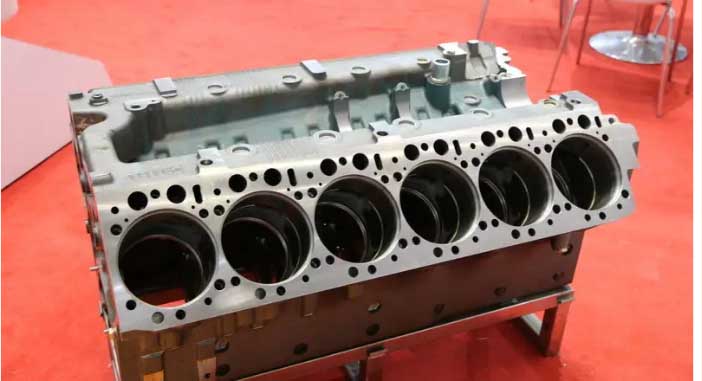
Why is aluminum so important?
Aluminum is a light metal with low density and good strength and plasticity. Aluminum alloy has good strength. The strength of super hard aluminum alloy can reach 600Mpa, and the tensile strength of ordinary hard aluminum alloy can also reach 200-450Mpa. The obtained aluminum alloy with tensile strength greater than 700Mpa has a specific strength comparable to that of high-quality alloy steel, and its specific rigidity is even much higher than that of steel. Aluminum has good thermal conductivity and can be used as a variety of heat dissipation materials. Aluminum also has good corrosion resistance and good plasticity and is suitable for various pressure processing. Therefore, aluminum alloys are widely used in various fields of machinery and automobiles.
The car engine has developed from all-iron to all-aluminum, the purpose is to reduce the weight of the car, and reducing the weight of the car means that it can save fuel consumption. Generally, the use of an aluminum cylinder engine can reduce the weight by about 20 kg. For every 10% reduction in the car’s weight, fuel consumption can be reduced by 6% to 8%. Now the cylinder heads of gasoline engines are made of aluminum alloy, and the material of the cylinder block has also been replaced by a large number of aluminum alloys.
But it is undeniable that some high-end engines have achieved real all-aluminum materials. For example, the all-aluminum cylinder block of Audi 3.1L FSI V6 does not use cast iron or steel cylinder liners but uses high Silicon aluminum alloy to overcome the reduced friction coefficient. The processing technology is very expensive, but the heat dissipation performance has been greatly improved.
Casting Structural Analysis
The solid model of the aluminum alloy die casting is shown. The overall dimensions are 445mm x 378mm x 226mm. The largest wall appears on the cylindrical wall with a thickness of 13.4mm, and the remaining walls have an average wall thickness of 4mm. The casting material is a high-silicon rare earth aluminum alloy, which is a super-eutectic AL-Si series die-casting alloy, and the silicon content is 19-21%wt.
Its Si grain size is controlled below 50 microns. The alloy has good fluidity, air tightness, thermal crack resistance, high wear resistance, and low expansion coefficient, and is suitable for the manufacture of automobile engine cylinder liners and brake blocks. , pump, and other parts materials. The product mass is 19.2kg. The overall shape of the casting is complex, the structure is changeable, and the wall thickness is uneven.
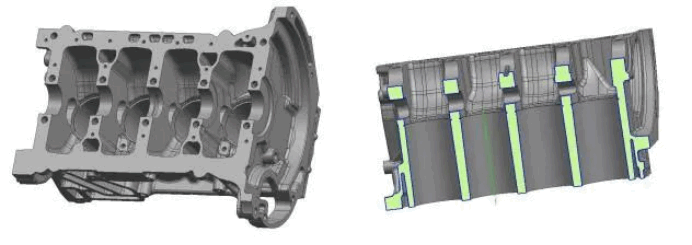
Aluminum die-casting construction of engine cylinders
The design of the gating system includes the design of the runner, the design of overflow exhaust system, the design of the cooling and heating system,
First, determine the feeding method. From the analysis of the structure of the product, the one-side feeding method is more suitable. This design is beneficial to the exhaust of the casting during the pouring process and avoids the gas being trapped in the cylinder, which will eventually lead to the appearance of large air shrinkage holes in it.
Secondly, do some necessary calculations according to the die casting process and parameters to determine the size of each part of the runner. First, determine the cross-sectional area of the gate according to the flow method and some empirical values.
In the formula: A is the cross-sectional area of the gate in mm2; G is the mass of the molten metal passing through the gate, including the mass g of the overflow slag bag; ρ is the density of the liquid metal g/cm3; V is the gate at the gate The flow rate of the molten metal m/s; t is the filling time S of the cavity.
The density of the casting is taken as 2.7g/cm3; the mass of the overflow slag bag is taken as 30% of the mass of the die casting, and G=25000g; for this cylinder, take V=60m/s, t=0.08s, and the calculation results in A=2200mm2, The casting volume is 7117cm3, and taking the gate slag bag as 45% of the casting, the total volume is 10319cm3.
The castings are used on a 2500T bedroom cold room die casting machine, and the bulging force calculated from the projection surface is 1920T, which is in the safe area. The length of the barrel is 960 mm. To prevent turbulent air entrainment in the filling of the material in the early stage, the filling rate of the barrel is best controlled within the range of 40% to 50%, and the upper limit is selected here. Therefore, the diameter of the barrel is 160 mm after calculation and rounding.
Because of the large outline and complex structure of the cylinder block casting, the conventional exhaust gas is easily entrained during casting. Moreover, the particularity of this cylinder body casting adopts the vacuum pumping method in the overflow exhaust.
Vacuum die casting can significantly reduce pores, make the structure denser, and improve the mechanical properties of castings. In addition, the filling back pressure is reduced, the forming performance is good, and the surface quality is improved. As shown in the figure below, the overflow exhaust in the second half of the casting is concentrated together, and finally converges into two exhaust plates, and then the exhaust plate on the fixed mold side is evacuated to realize the exhaust mode of the mold.
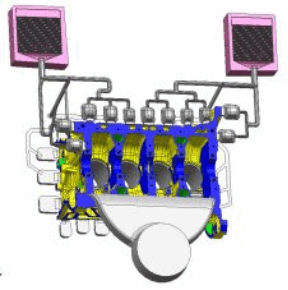
Mold temperature is an important factor affecting the quality of die castings. Most of the castings with simple shapes and good die casting technology do not require high mold temperature control. Qualified castings can still be obtained when the mold temperature changes within a large range. For complex castings, only the mold temperature can be controlled within a narrow range to produce qualified castings.
The mold temperature control is achieved by the heating and cooling system of the mold. Its main purpose is to improve the internal quality and surface quality of die-casting parts, stabilize the dimensional accuracy of die-casting parts, improve the production efficiency of die-casting parts, reduce the thermal alternating stress of the mold, and improve the service life of the mold.
From the product structure discussed above, the thick area of the cylinder is the hot spot area, and the solidification will lag behind other areas, so a reasonable cooling system needs to be set up here. The following figure shows the water cooling structure at the cylinder barrel. Thread-type cooling is arranged in the peripheral wall of the cylinder, and the thickness of the cooling wall is controlled at about 12mm. Such a design can effectively reduce the temperature here so that the molten metal in this area solidifies in advance.
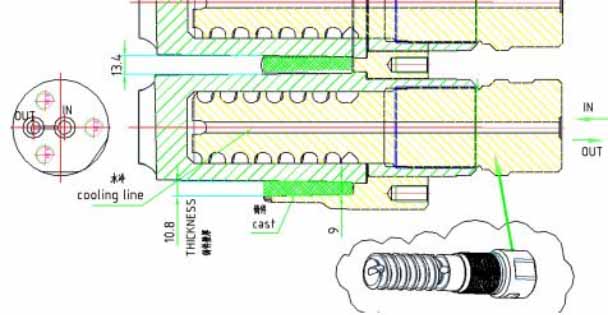
Problems existing in the engine block of aluminum die casting
To sum up, with the development of the automobile industry, the research and development and application of engine aluminum cylinder blocks are of great significance, and their development and application will become more and more extensive. Therefore, the research on the material of the cylinder, the preparation, and the research on the product forming process is particularly meaningful.
Before mass production of aluminum castings, due to the characteristics of the product structure, it is necessary to continuously improve the mold process and structure.
1. First of all, the problem of air shrinkage holes at the cylinder barrel must be solved. Vacuum die casting and an efficient cooling system greatly improve the internal quality of the casting cylinder.
2. Because the tightening force at the cylinder barrel is too large, the pulling force of the cylinder barrel insert is often too large, and the conventional insert is easily damaged, which will affect mass production in the future.
It is necessary to design a reasonable and effective cylinder liner structure and carry out surface treatment to reduce the surface friction coefficient, release the mold and reduce the damage to the mold.