Polycrystalline alumina fibers are rapidly gaining recognition for their exceptional physical and chemical properties, making them a valuable material across various industrial applications. These fibers, crafted from high-purity alumina (Al₂O₃) through specialized manufacturing processes, exhibit remarkable qualities that enable them to perform under extreme conditions. This article explores the characteristics of polycrystalline alumina fibers, their diverse applications, and their significant impact on modern industry.
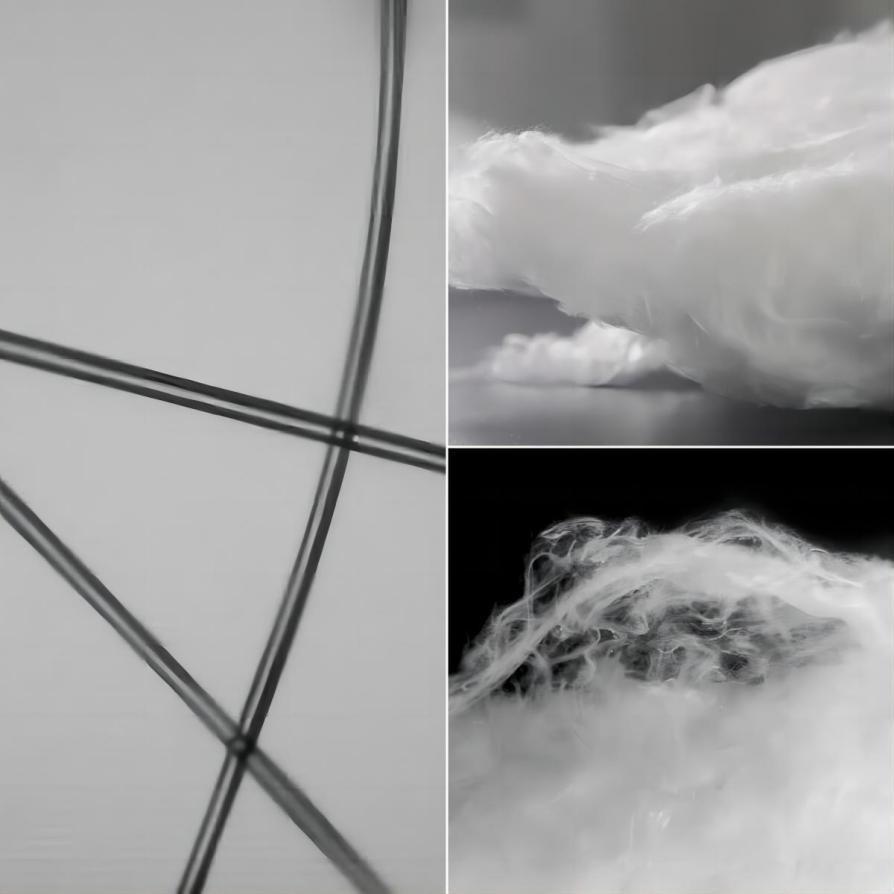
How Polycrystalline Alumina Fibers Produced
Polycrystalline alumina fibers are produced from alumina, a compound known for its stability and strength. The fibers are typically manufactured through several advanced methods, including the sol-gel process, gel-spinning method, and chemical vapor deposition (CVD).
- Sol-gel Process: This technique involves the transformation of a sol (a liquid suspension of fine particles) into a gel through chemical reactions. The gel is then processed into fibers and subjected to high-temperature treatment to achieve the desired properties.
- Gel-Spinning Method: In this method, a gel containing alumina is spun into fibers. The fibers are then heated to high temperatures to enhance their structural integrity and performance.
- Chemical Vapor Deposition (CVD): CVD involves depositing alumina from a vapor phase onto a substrate, which is then converted into fibers through subsequent heating processes.
These manufacturing techniques result in fibers with high thermal stability, chemical inertness, excellent electrical insulation, and superior mechanical strength. These attributes enable polycrystalline alumina fibers to excel in environments characterized by extreme temperatures and corrosive conditions.
Applications of Polycrystalline Alumina Fibers
Polycrystalline alumina fibers are utilized across various industries, each benefiting from their unique properties. Here is a detailed look at their applications:
1. Refractory Materials
Refractory materials are essential for industries where equipment operates under high-temperature conditions. Polycrystalline alumina fibers play a critical role in these applications, offering outstanding thermal stability and resistance to corrosion.
- Steelmaking: In steel production, the durability of equipment subjected to high temperatures and molten metal is paramount. Polycrystalline alumina fibers are used to manufacture furnace linings, insulating bricks, and refractory blankets, ensuring efficient operation and extending equipment lifespan.
- Glass Production: The production of glass involves extreme temperatures that can degrade conventional materials. By integrating polycrystalline alumina fibers, manufacturers can produce materials that withstand these conditions, leading to improved energy efficiency and lower operational costs.
- Cement Industry: The cement industry also relies on refractory materials to handle high temperatures. Polycrystalline alumina fibers are used to create insulation solutions that protect equipment from heat damage and reduce energy consumption.
2. Aerospace Industry
The aerospace sector demands materials that are lightweight yet capable of withstanding extreme temperatures. Polycrystalline alumina fibers meet these requirements effectively.
- Aircraft Engine Insulation: The fibers are used in engine components to protect against high temperatures, thereby enhancing the engine’s efficiency and durability.
- Spacecraft Thermal Protection: For spacecraft, polycrystalline alumina fibers provide essential thermal protection during re-entry and space travel, safeguarding sensitive equipment from extreme heat.
- Rocket Nozzle Insulation: In rocket engines, the fibers help insulate nozzle components from intense thermal stress, improving performance and safety.
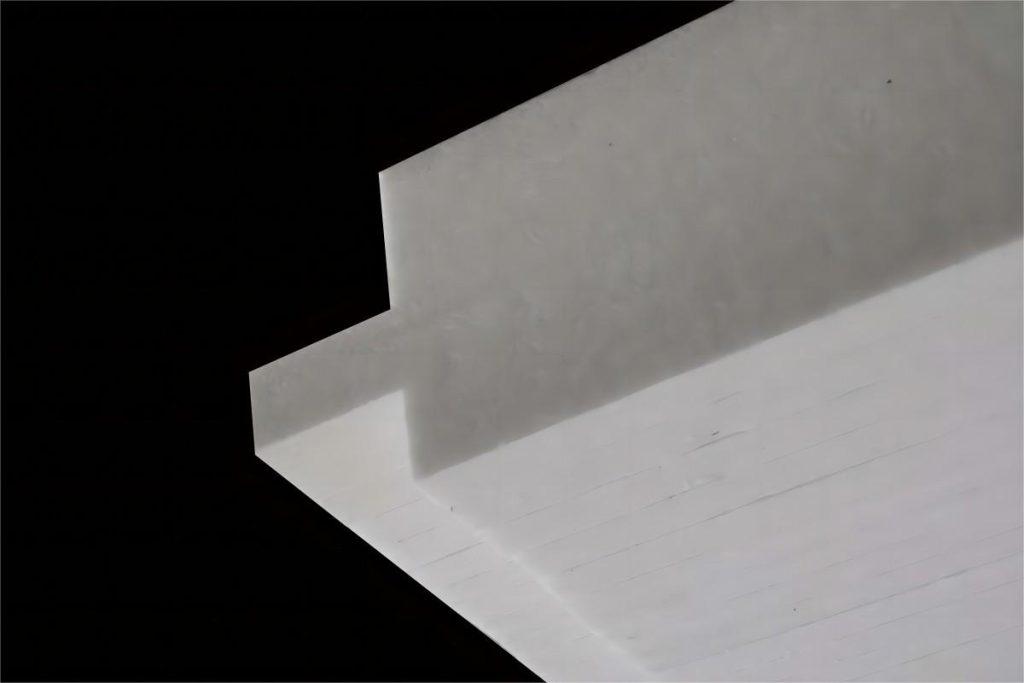
3. Automotive Industry
In the automotive industry, polycrystalline alumina fibers contribute to various components, improving vehicle performance and safety.
- Engine Heat Shields: The fibers are used in heat shields to protect engine components from excessive temperatures, leading to better fuel efficiency and reduced emissions.
- Exhaust System Insulation: The use of these fibers in exhaust systems helps manage temperatures, enhancing vehicle performance and driver comfort.
- Electrical Components: Their excellent electrical insulation properties make polycrystalline alumina fibers ideal for use in circuit boards and cable insulation, ensuring reliable operation of automotive electrical systems.
4. Chemical Industry
The chemical industry often deals with high-temperature and corrosive chemicals, requiring materials that can withstand such harsh conditions.
- Filtration and Separation: Polycrystalline alumina fibers are employed in filtering and separating corrosive chemicals, such as acids, bases, and organic solvents. Their chemical stability ensures the protection of equipment and improves overall production efficiency.
5. Electronics Industry
In the electronics sector, polycrystalline alumina fibers are valued for their insulating properties and high-temperature resistance.
- Circuit Boards: These fibers are used in the production of circuit boards, ensuring stable performance in various environmental conditions.
- Insulating Tubes and Cable Insulation: Their application in insulating tubes and cable layers enhances the reliability of electronic devices, protecting them from electrical interference and thermal damage.
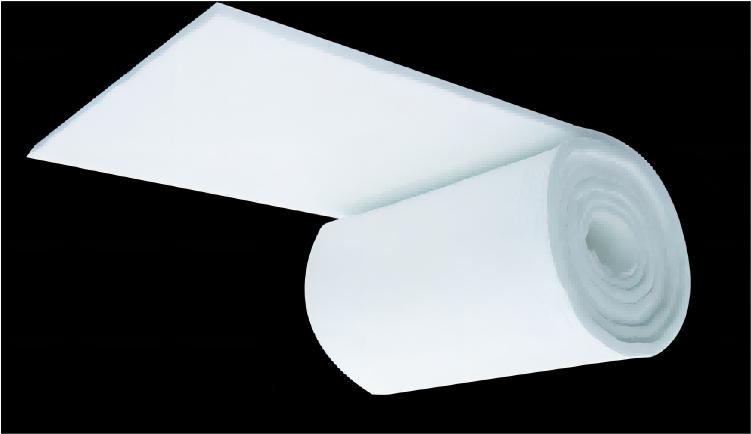
6. Energy Sector
The energy sector benefits from polycrystalline alumina fibers in several critical applications.
- Solar Collectors: The fibers are used in solar collectors to minimize heat loss, improving the efficiency of solar energy systems.
- Nuclear Reactors: In nuclear reactors, polycrystalline alumina fibers provide insulation that protects against high temperatures and radiation, contributing to the safety and stability of energy systems.
7. Medical Field
In the medical field, polycrystalline alumina fibers are employed to enhance the performance and safety of medical instruments.
- High-Temperature Medical Instruments: Fibers are used in devices such as endoscopes and surgical blades, where their high-temperature resistance and biocompatibility ensure reliable performance during sterilization and surgical procedures.
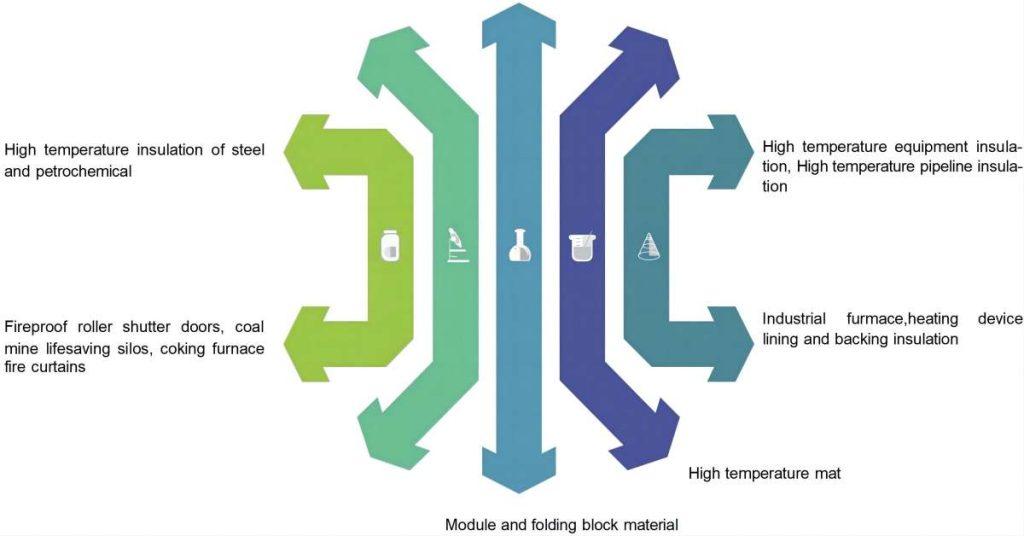
To sum up, polycrystalline alumina fibers have established themselves as a critical component in the fabric of industrial progress. From refractory materials to medical devices, their multifaceted applications underscore the versatility and significance of these fibers in modern industries. As advancements in materials science continue to unfold, the future of polycrystalline alumina fiber is poised for further expansion in performance and applications, solidifying their role as a driving force behind industrial modernization and technological innovation.