Aluminum machining parts are used in a variety of industries, from aerospace to medical devices. These parts must be of high quality to ensure they meet industry standards and perform their intended functions effectively. Quality control is essential in the production of aluminum machining parts to ensure they meet these requirements. In this article, we will discuss the importance of quality control in aluminum machining parts, its goals and objectives, and the various techniques used to achieve it.
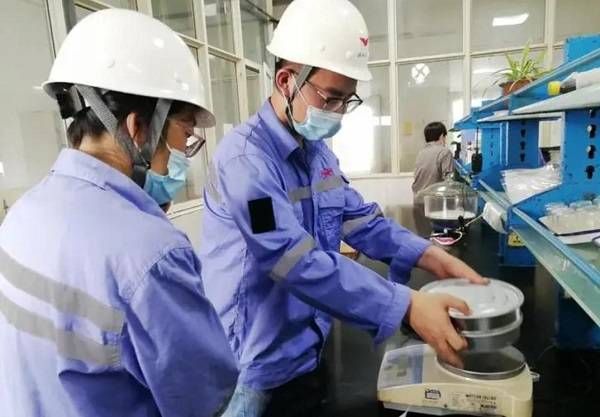
The First Step of Quality Control: Process Control
It involves monitoring and controlling the manufacturing process to ensure that the parts meet the required specifications. The process includes selecting the appropriate tools and equipment, maintaining them, and calibrating them. The process should be consistent and repeatable to ensure that the parts are of high quality.
Tool selection and maintenance are critical in the production of aluminum machining parts. The right tool for the job must be selected to ensure that the parts are of the required quality. The tools must be maintained properly to ensure that they are in good working condition and are safe to use. Maintenance should be performed regularly to prevent wear and tear, which can affect the quality of the parts.
Calibration of equipment is also essential in quality control. Equipment must be calibrated to ensure that it is accurate and reliable. Calibration should be performed regularly to ensure that the equipment is functioning correctly and producing accurate results. Calibration ensures that the parts meet the required specifications and that the manufacturing process is consistent and repeatable.
The Second Step of Quality Control: Inspection and Testing
It involves checking the parts during the manufacturing process and after they are completed. The purpose is to identify defects and ensure that the parts meet the required specifications. Inspection and testing can be done in-process, which involves checking the parts during the manufacturing process, or after the parts are completed.
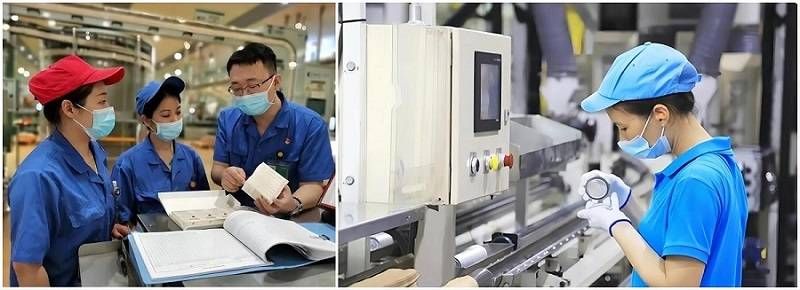
In-process inspection involves checking the parts during the manufacturing process to ensure that they meet the required specifications. It can be done using various techniques such as visual inspection, dimensional inspection, and surface finish measurement. In-process inspection ensures that any defects are identified early in the manufacturing process, which reduces waste and improves the quality of the parts.
Final inspection involves checking the parts after they are completed. It is a comprehensive inspection that ensures that the parts meet the required specifications. Final inspection involves checking the parts for dimensional accuracy, surface finish, and other quality requirements. Final inspection is essential in ensuring that the parts are of high quality and meet the required specifications.
Non-destructive testing is a technique used to test the parts without causing any damage. It is used to identify defects that are not visible to the naked eye. Non-destructive testing techniques include ultrasonic testing, radiography, and magnetic particle inspection. Non-destructive testing is an essential part of quality control and ensures that the parts are free of defects.
Surface finish measurement is critical in the production of aluminum machining parts. The surface finish of the parts can impact their performance and durability. Surface finish measurement involves measuring the roughness of the parts’ surface to ensure that it meets the required specifications.
The Third Step of Quality Control: Statistical Process Control
Statistical process control is a technique used to monitor and control the manufacturing process. It involves using statistical tools to analyze data and identify trends in the process. Statistical process control helps to identify any variations in the process that can impact the quality of the parts. It helps to ensure that the manufacturing process is consistent and repeatable, and any variations are identified and addressed promptly.
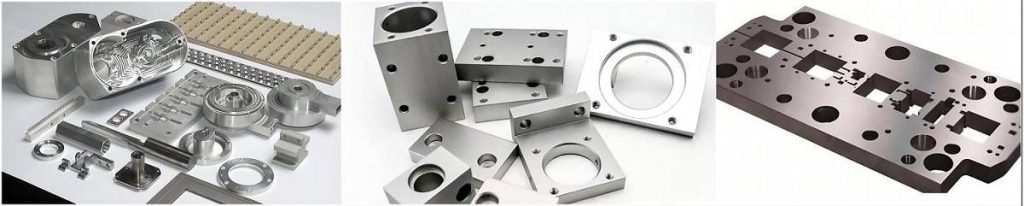
Control charts are one of the statistical process control tools used in quality control. Control charts help to identify any variations in the process and ensure that the manufacturing process is consistent and repeatable. Control charts are used to monitor critical dimensions, surface finish, and other quality requirements. The charts help to identify any trends in the process, and corrective action can be taken to address any issues.
Process capability analysis is another statistical process control tool used in quality control. Process capability analysis involves analyzing the manufacturing process to determine if it is capable of producing parts that meet the required specifications. The analysis helps to identify any variations in the process and ensures that the process is consistent and repeatable. Process capability analysis is an essential part of quality control, and it helps to improve the manufacturing process and reduce costs.
Six Sigma methodology is a statistical process control technique used in quality control. Six Sigma is a data-driven approach to quality control that aims to reduce defects and improve the manufacturing process. It involves identifying and measuring the defects in the process and developing solutions to address them. Six Sigma methodology helps to improve the quality of the parts and reduce costs by identifying and addressing the root causes of defects.
The Forth Step of Quality Control: Corrective and Preventive Action
Corrective and preventive action is an essential part of quality control. It involves identifying and addressing any issues that arise in the manufacturing process. Corrective action involves identifying the root cause of the problem and developing solutions to address it. Preventive action involves identifying potential issues before they occur and developing solutions to prevent them from happening.
Root cause analysis is a technique used to identify the root cause of defects. Root cause analysis involves identifying the cause of the defect and developing solutions to address it. Root cause analysis helps to improve the manufacturing process and reduce defects.
Corrective action plans are developed to address any issues that arise in the manufacturing process. Corrective action plans involve identifying the root cause of the problem and developing solutions to address it. Corrective action plans help to improve the quality of the parts and reduce defects.
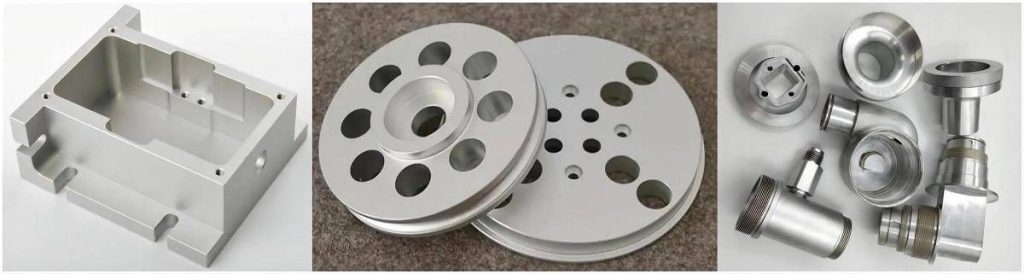
Preventive action plans are developed to prevent potential issues from occurring in the manufacturing process. Preventive action plans involve identifying potential issues and developing solutions to prevent them from happening. Preventive action plans help to improve the manufacturing process and reduce costs by preventing defects from occurring.
Conclusion
In conclusion, quality control is essential in the production of aluminum machining parts. Quality control ensures that the parts meet industry standards and are free of defects. The goals of quality control are to minimize defects, improve the manufacturing process, reduce costs, and increase customer satisfaction. The various techniques used in quality control include process control, inspection and testing, statistical process control, and corrective and preventive action. These techniques help to improve the quality of the parts, reduce defects, and improve the manufacturing process. In the future, advancements in technology will continue to improve the quality control techniques used in the production of aluminum machining parts.
Related Products
Related Articles