The world of fibers extends far beyond the familiar realm of cotton and polyester. In industrial settings and high-temperature applications, a unique class of materials known as PCW fibers (polycrystalline wool fibers) plays a crucial role. These fibers, also referred to as ceramic fibers or polycrystalline wool, offer exceptional heat resistance and other valuable properties, making them indispensable in diverse industries. This article delves into the world of PCW fibers, exploring their composition, variations, and applications.
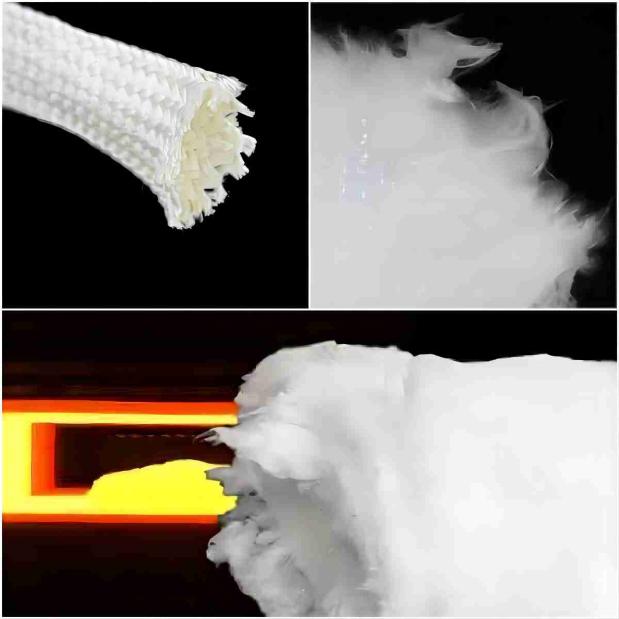
Demystifying PCW Fibers: Composition and Properties
Unlike their natural counterparts, PCW fibers are not derived from organic sources. Instead, they are manufactured from aluminosilicate materials, primarily consisting of aluminum oxide (Al2O3), also known as alumina. This composition imbues them with remarkable properties:
- High-Temperature Resistance: PCW fibers can withstand extreme temperatures, often exceeding 2,600°C (4,700°F). This exceptional thermal stability makes them ideal for applications like furnace linings, high-temperature filtration, and aerospace components.
- Low Thermal Conductivity: PCW fibers are poor conductors of heat, translating to excellent insulation properties. This characteristic helps retain heat within systems or prevent surrounding areas from becoming excessively hot.
- Chemical Resistance: These fibers exhibit high resistance to various chemicals, including acids, alkalis, and molten metals. This property makes them suitable for use in harsh environments and applications involving chemical reactions.
- Lightweight: Despite their impressive strength and heat resistance, PCW fibers are surprisingly lightweight, contributing to reduced weight in applications like aerospace and transportation.
- Mechanical Strength: PCW fibers possess good mechanical strength, allowing them to withstand moderate physical stress and maintain their structural integrity.
Exploring Variations within the PCW Fiber Family
While the core composition of PCW fibers revolves around alumina, there are several variations within this category, each offering distinct advantages:
- Alumina PCW Fiber: This is the most common type, containing a high percentage of alumina (typically over 90%). Its primary strengths lie in its high-temperature resistance and excellent chemical resistance.
- Zirconia PCW Fiber: This variant incorporates zirconium oxide (ZrO2) alongside alumina, offering even higher temperature resistance (up to 2,700°C or 4,900°F). However, it comes at the cost of slightly lower chemical resistance compared to pure alumina PCW fibers.
- Mullite PCW Fiber: This type comprises a combination of alumina and silica (SiO2), forming a mineral known as mullite. This variation offers a good balance between temperature and chemical resistance, making it suitable for various applications.
Key Differentiators
The primary distinction between these variations lies in their temperature resistance and chemical resistance. Here’s a table summarizing the key points:
Feature | Alumina PCW Fiber | Zirconia PCW Fiber | Mullite PCW Fiber |
Primary Material | Alumina (Al2O3) | Alumina (Al2O3) + Zirconia (ZrO2) | Alumina (Al2O3) + Silica (SiO2) |
Temperature Resistance | Up to 2,600°C (4,700°F) | Up to 2,700°C (4,900°F) | Up to 2,300°C (4,100°F) |
Chemical Resistance | Excellent | Good | Good |
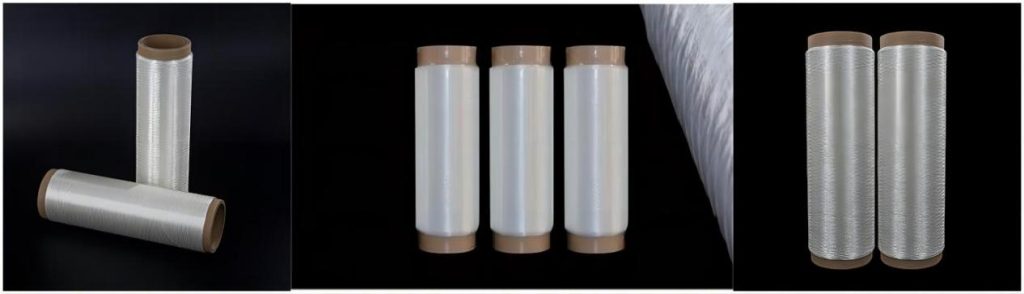
Applications of PCW Fibers: Spanning Industries
The unique combination of properties offered by PCW fibers has led to their extensive adoption in various sectors, each leveraging their specific strengths:
1. Aerospace and Defense
- Heat Shields: PCW fibers play a critical role in protecting spacecraft and re-entry vehicles during atmospheric entry by absorbing and dissipating the immense heat generated from friction with the atmosphere.
- Thermal Insulation: Their exceptional thermal insulation capabilities make them ideal for spacecraft insulation, maintaining optimal temperature control for sensitive electronics and crew comfort within the spacecraft.
- High-Temperature Seals: PCW fibers are employed in high-temperature seals due to their ability to withstand extreme temperatures and prevent leaks in critical engine components and other high-pressure systems.
2. Chemical Processing
- Reactor Linings: The outstanding chemical resistance of PCW fibers makes them suitable for lining reactors used in various chemical processes. This lining protects the reactor walls from corrosion caused by aggressive chemicals and ensures the integrity of the reaction vessel.
- Filtration Media: PCW filters are utilized in high-temperature filtration applications within the chemical processing industry. These filters effectively remove pollutants and contaminants from hot exhaust gases or molten materials without degradation due to the exceptional thermal stability of the fibers.
3. Fire Protection
- Fire Blankets: PCW fibers are incorporated into fire blankets due to their exceptional thermal stability and non-flammable nature. These blankets provide a vital layer of protection for firefighters and civilians during fire emergencies, offering valuable time for evacuation and firefighting efforts.
- High-Temperature Gaskets: Gaskets made from PCW fibers are employed in applications involving extreme temperatures, such as high-pressure boilers and furnaces. These gaskets effectively create a tight seal, preventing leaks and ensuring the safe operation of equipment.
- Fire Protection Fabrics: Fabrics woven from PCW fibers are used in fire protection clothing and equipment due to their ability to withstand high temperatures and resist flames. This protective gear safeguards firefighters and other professionals working in hazardous environments.
Considerations for Using PCW Fibers
While PCW fibers offer significant advantages, it’s crucial to acknowledge specific considerations before implementation:
1. Cost: Compared to some conventional materials, PCW fibers can be more expensive upfront. However, their extended lifespan and unique performance characteristics often outweigh the initial investment due to:
- Reduced maintenance costs: Their durability minimizes the need for frequent replacements compared to other materials susceptible to degradation under high temperatures or harsh chemicals.
- Improved energy efficiency: The excellent thermal insulation properties of PCW fibers can lead to significant energy savings in applications like furnace linings and high-temperature filtration.
2. Abrasion Resistance: While PCW fibers possess good mechanical strength, they are not as resistant to abrasion as certain other materials. This necessitates:
- Careful handling: Implementing proper handling procedures during transportation, installation, and maintenance is essential to prevent damage and ensure optimal performance.
- Application-specific selection: Choosing the appropriate PCW fiber type with suitable abrasion resistance based on the specific application’s requirements is crucial. For instance, applications involving frequent contact or movement might benefit from additional protective measures or alternative materials with superior abrasion resistance.
3. Environmental Impact: Manufacturing PCW fibers can be energy-intensive, requiring significant resources and potentially contributing to greenhouse gas emissions. However, there are efforts to mitigate this impact:
- Sustainable manufacturing practices: Implementing sustainable practices throughout the production process, such as using recycled materials or adopting energy-efficient technologies, can significantly reduce the environmental footprint associated with PCW fiber production.
- Life cycle analysis: Conducting life cycle assessments to evaluate the environmental impact throughout the entire life cycle of PCW fibers, including production, use, and potential end-of-life options, can inform decision-making and encourage sustainable practices.

Conclusion
PCW fibers, with their remarkable combination of high-temperature resistance, chemical stability, and lightweight nature, have become a cornerstone material across various industries. From industrial furnaces to aerospace applications, these versatile fibers play a vital role in diverse applications requiring exceptional thermal management and chemical resistance. Understanding the different variations and their unique properties empowers engineers and designers to select the most suitable PCW fiber for their specific needs. As research and development in this field continue, we can expect even more advancements in PCW fiber technology, potentially leading to even higher performance and broader applications in the future.