Aluminum cans are an integral part of our daily lives, commonly used for packaging beverages, from soft drinks to beer and beyond. They are lightweight, easily recyclable, and possess remarkable qualities that have made them a favorite in the world of packaging. But have you ever wondered how these aluminum cans are made? What type of aluminum used in their production? In this article, we will take you on a journey through the fascinating process of creating these versatile containers.
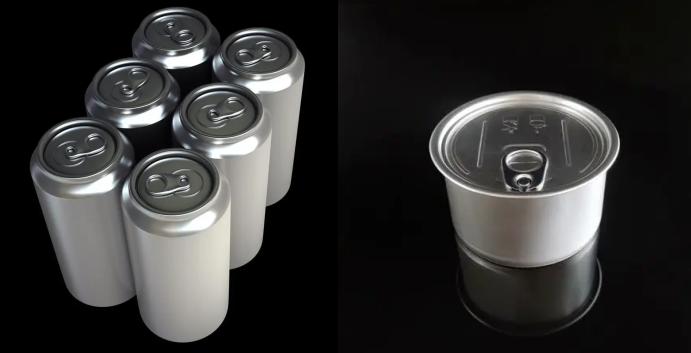
The Birth of an Aluminum Can
The manufacturing of an aluminum can begins with the primary raw material—aluminum. This remarkable material is derived from bauxite ore, a naturally occurring aluminum-rich mineral. The extraction and refining of bauxite yield aluminum oxide, which, when processed, transforms into pure aluminum metal.
Aluminum cans are typically made from a specific type of aluminum alloy. While pure aluminum is soft and lacks the strength required for manufacturing cans, an aluminum alloy called 3104 H19 is commonly used in the industry. This alloy is specially designed for can production, as it offers a balance between strength, formability, and resistance to corrosion. The “3104” denotes the specific alloy, and “H19” represents the temper, which signifies its strength and hardness.
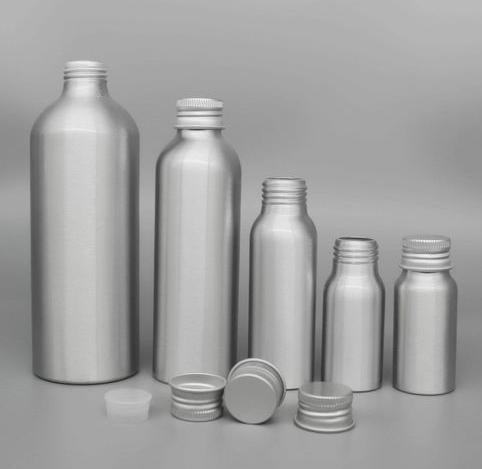
How Are Aluminum Cans Made?
1. From Ore to Metal: The Smelting Process
The first step in the journey of an aluminum can is smelting. In this process, aluminum oxide is subjected to intense heat within a furnace, causing it to melt and ultimately transform into molten aluminum. This molten aluminum is then cast into ingots or directly into thin sheets, depending on the manufacturing method in use.
Shaping and Forming
Once we have aluminum sheets ready, it’s time to shape and form them into the familiar can we know. Here’s how it’s done:
- Rolling and Coating: The aluminum sheets are passed through rolling mills, where they are progressively thinned to the desired thickness. To protect the aluminum from corrosion, a layer of protective material is applied as a coating. This coating not only guards against environmental factors but also provides a suitable surface for printing and labeling.
- Printing the Design: This is where the can’s aesthetic comes to life. The coated aluminum sheets are guided through a printing press, where graphics, logos, and information are expertly printed onto the surface, giving each can its distinctive appearance.
2. Forming the Can Body: A Delicate Dance of Machines
After the design phase, the manufacturing process transitions to shaping the can body:
- Blanking: The first step involves using a blanking press to cut out flat circles from the printed aluminum sheets. These circles will serve as the tops and bottoms of the cans.
- Cupping: The remaining flat sheet is then subjected to a cupping process using a press. This step creates the initial cup shape, forming the foundation of the can body.
- Ironing: Following cupping, the cans undergo a series of ironing steps. During ironing, the cups are gradually stretched and elongated to achieve the desired height and shape of the can. Simultaneously, the walls become thinner and taller, crafting the iconic aluminum can form we all recognize.
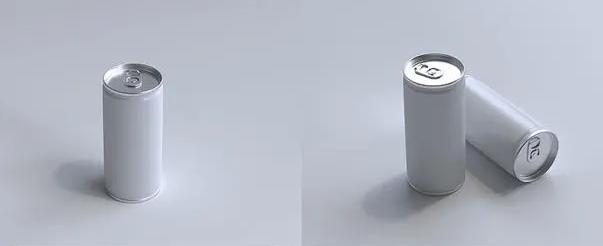
3. Finishing Touches
With the basic shape of the can established, there are a few more steps to complete before we can consider our aluminum can finished:
- Necking and Flanging: The cans are necked to shape the top opening and flanged to create a rolled rim that reinforces the can’s top, enhancing its structural integrity.
- Cleaning and Coating: The cans are meticulously cleaned to eliminate any contaminants or residues. To prevent the aluminum from coming into direct contact with the contents, a food-grade internal lining is applied, ensuring product safety and quality.
- Printing the Top and Bottom: Information such as expiration dates, manufacturing codes, and relevant details are printed onto the tops and bottoms of the cans.
4. Bringing It All Together: Assembly and Sealing
The final steps in aluminum can manufacturing involve assembling the top and bottom with the can body and sealing them together using a double-seam process. This process ensures that the can is securely closed, preventing leaks and maintaining airtightness.
5. Quality Control and Inspection
Throughout the manufacturing process, strict quality control checks are carried out. These checks ensure that each can meets the required specifications and standards for safety and performance. Any deviations are swiftly addressed to maintain the high quality and integrity of the final product.
6. Packaging and Distribution
Once the aluminum cans are successfully manufactured and inspected, they are packaged in bulk for shipment to beverage manufacturers and distributors worldwide. These cans are ready to be filled with a wide array of beverages, from carbonated drinks to energy drinks and even craft beers.
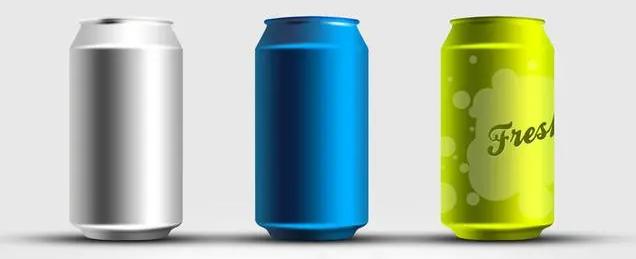
Conclusion
Aluminum cans are a true marvel of modern packaging. From their humble beginnings as bauxite ore to the efficient, sustainable containers we encounter every day, the process of creating these iconic vessels is a testament to human innovation and engineering. Understanding how aluminum cans are made not only deepens our appreciation for this ubiquitous packaging but also emphasizes the importance of recycling to maintain the sustainability of this industry. Next time you crack open a cold beverage from an aluminum can, take a moment to reflect on the journey it took to reach your hands, all while being a shining example of eco-friendly packaging in a world that increasingly values sustainability.