Aluminum blister foil is a packaging material that is commonly used in the pharmaceutical industry. It consists of a thin layer of aluminum foil that is laminated with a heat-seal coating material, such as PVC, PVDC, or cold-formable materials. This combination of materials creates a multi-layered structure that provides a high level of protection and preservation for medication. This article will explain the process of aluminum blister foil, including the raw materials used, the manufacturing process, and the importance of quality control.
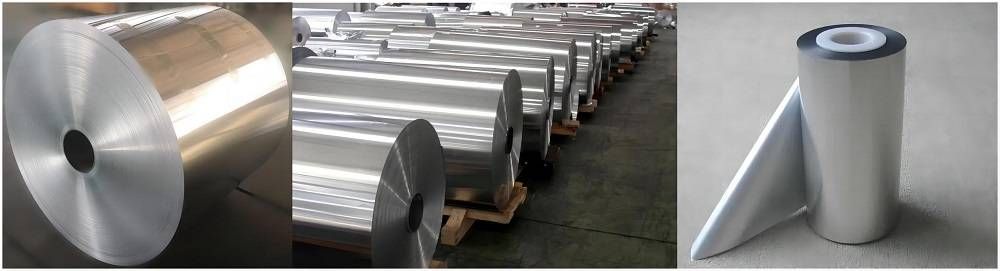
Raw Materials
The raw materials used to produce aluminum blister foil include aluminum foil and heat-seal coating materials. The aluminum foil used is typically between 20 and 30 microns thick and is made from high-quality aluminum that is free from defects. The heat-seal coating material is applied to the aluminum foil to create a multi-layered structure.
Foil Preparation
The aluminum foil and heat-seal coating material are laminated together to create a multi-layered structure. This is done by passing the materials through a series of rollers under heat and pressure. The result is a tightly bonded and uniform structure that provides a high level of protection for medication.
Printing
The printed information on the blister foil is an essential part of the packaging. It provides important details about the medication, including dosage, warnings, and expiry date. The printing process is done before the aluminum foil is cut into the required size and shape. The printing can be done using either flexographic or rotogravure printing techniques.
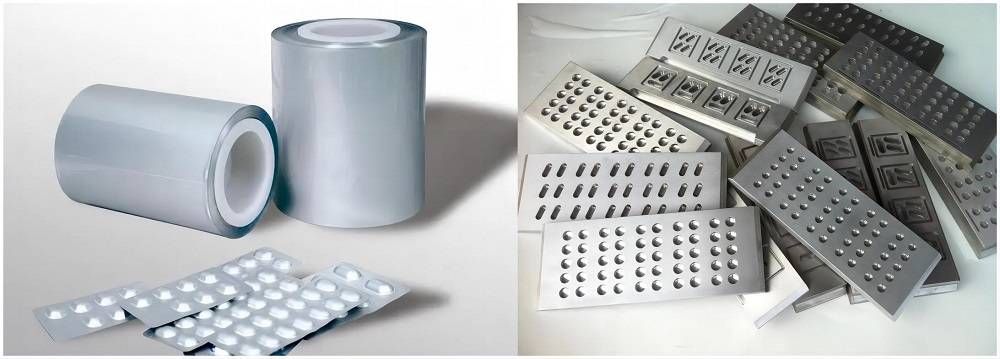
Cutting
Once the printing is complete, the aluminum foil is cut to the required size and shape using a cutting machine. The cutting machine can be either a rotary or flat-bed cutting machine, depending on the complexity of the shape required. The cutting process must be precise to ensure that each blister pack is the correct size and shape.
Forming
The cut aluminum foil is then formed into pockets or cavities using a forming machine. The forming machine creates pockets or cavities of the required size and shape. The blister packs can be formed in a variety of shapes, including round, square, or oval.
Sealing
The formed blister packs are filled with medication and then sealed with a backing material. The backing material is usually made from paper or plastic and is used to protect the medication from light and moisture. The sealing process can be done using either heat or pressure. The result is a secure and airtight seal that ensures the medication is protected until it is opened by the patient.
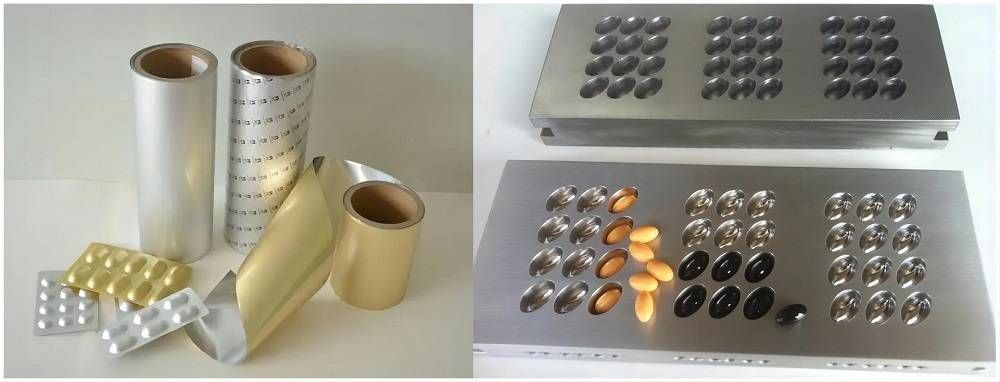
Inspection
Once the blister packs are sealed, they undergo a quality inspection. The inspection process is designed to ensure that each blister pack is of high quality and adheres to product specifications. The inspection includes checking the seal, the size and shape of the blister pack, and the printed information.
Packaging and Shipping
Once the aluminum blister packing have been inspected and approved, they are packaged and shipped to pharmaceutical companies. The blister packs are packaged in boxes that are labeled with important information such as the batch number, manufacturing date, and expiry date. The boxes are then shipped to pharmaceutical companies, where they are distributed to pharmacies and healthcare providers.
Importance of Choosing A Reliable Aluminum Blister Foil Manufacturer
Choosing a reliable aluminum blister foil manufacturer is crucial to ensure the quality and safety of the medication. When choosing a manufacturer, it is important to consider their experience, quality control processes, and adherence to product specifications. A reliable manufacturer will ensure that the aluminum blister foil is of high quality and meets all necessary safety standards.
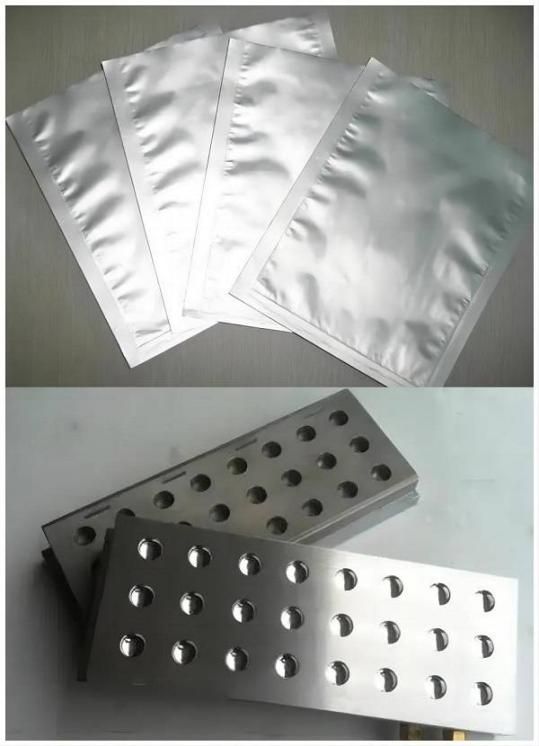
Conclusion
In conclusion, aluminum blister foil is an important part of the pharmaceutical industry, providing a high level of protection and preservation for medication. The process of aluminum blister foil involves the use of high-quality raw materials, precise manufacturing techniques, and rigorous quality control processes. Choosing a reliable aluminum blister foil manufacturer is essential to ensure the safety and efficacy of the medication. By following these steps, the pharmaceutical industry can continue to provide safe and effective medication to patients around the world.