Aluminum extrusion has become a cornerstone of modern manufacturing, offering a versatile method to shape lightweight and strong aluminum products used across multiple industries. From automotive parts to building structures, aluminum extrusions are central to many applications. However, the success of these products doesn’t rely solely on the extrusion process but largely on the quality of the extrusion mold. A well-designed aluminum extrusion mold is the blueprint for precise, high-performing, and durable products. This article explores the relationship between aluminum extrusion molds and product performance, diving into how mold design and quality directly impact the characteristics of the final extruded product.
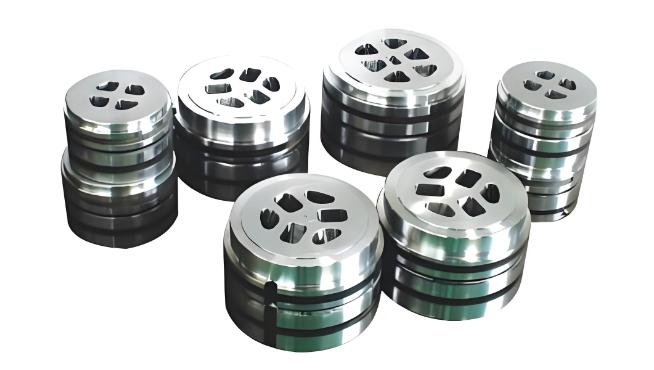
Understanding Aluminum Extrusion Molds
Aluminum extrusion molds are specialized tools that shape the heated aluminum into specific profiles during the extrusion process. These molds, or dies, are designed to allow molten aluminum to be forced through their apertures, creating products with consistent cross-sectional profiles.
There are several types of extrusion molds, including solid, hollow, and semi-hollow molds, each suited for different product profiles. The mold essentially dictates the shape, dimensions, and surface finish of the extruded product. The design of the mold, combined with its material quality and cooling system, governs the efficiency of the extrusion process and, ultimately, the performance of the end product. A poor mold design can lead to inconsistencies, surface defects, and even failure in structural performance.
Understanding the basics of aluminum extrusion molds is essential because they serve as the framework that translates raw materials into functional products. Without a well-designed mold, even the best extrusion machinery will fall short of delivering high-quality components.
How Mold Design Impacts Product Performance?
The design of an aluminum extrusion mold directly influences several key aspects of the final product’s performance. Precision, consistency, surface finish, and structural integrity all stem from how well the mold is engineered. Let’s look at these factors in detail:
Precision and Tolerances
Mold design plays a crucial role in determining the precision of the extruded product. The manufacturing accuracy of the mold must be high enough, and the geometric and dimensional tolerances need to meet the requirements of the design drawings. They are usually manufactured with negative tolerances to ensure good interchangeability between mold parts. Poor mold design can result in parts that do not fit correctly, leading to inefficiencies during assembly or requiring additional post-processing.
The design of the working belt of the mold is crucial to fixing the size of the aluminum profile. The length of the working belt needs to be optimized based on the difference in wall thickness of the profile, the distance from the center, and whether it is covered by a shunt bridge, etc.
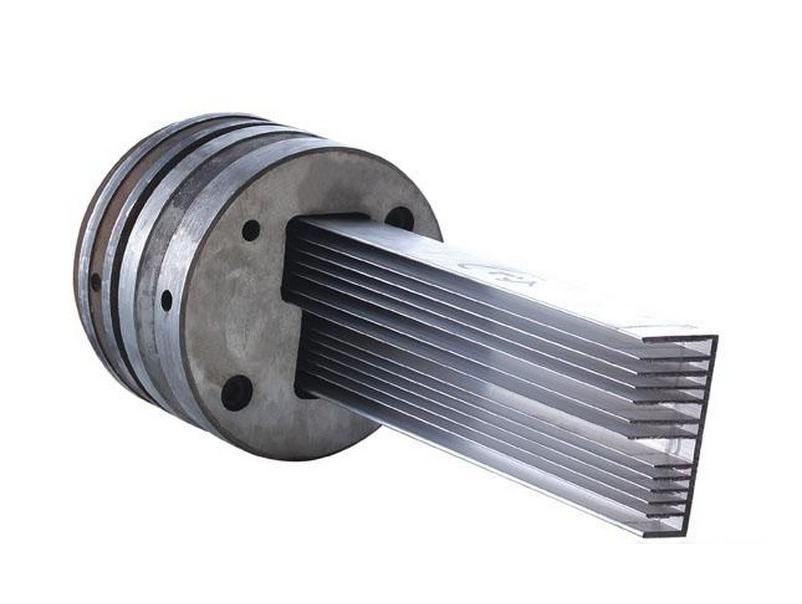
Consistency in Output
A well-engineered mold ensures that each extruded product is identical to the previous one. This consistency is vital in large-scale production, where variances in profile dimensions can lead to defective parts. Molds that wear down quickly or are poorly designed lead to fluctuations in product quality, affecting overall performance.
Surface Finish Quality
The quality of the mold’s interior surface impacts the extruded product’s surface finish. A smooth, well-crafted mold results in products with high surface quality, which is critical in applications where aesthetics and smoothness are paramount, such as in architectural or automotive parts. Rough or uneven mold surfaces can create defects, reducing product performance and lifespan.
Strength and Durability of Extruded Products
The way a mold is designed also affects the structural integrity of the product. Features such as sharp corners or complex geometries can create stress points that may weaken the final product. The metal fluidity of aluminum profiles also needs to be considered in mold design. Through reasonable mold structure design, such as symmetrical arrangement of multiple holes and unequal length sizing belts, the unevenness of metal flow can be minimized, ensuring coordinated and uniform flow of various parts of the profile, thereby improving dimensional accuracy and ensures the product’s strength.
The heat treatment of the mold is also an important factor. Proper preheating can reduce the thermal stress of the mold during the extrusion process, extend the life of the mold, and indirectly affect the dimensional stability.
Mold design plays a pivotal role in how well an aluminum extrusion performs in its intended application. From tight tolerances to enhanced strength, every aspect of product performance is tied to the care and precision applied in mold creation.
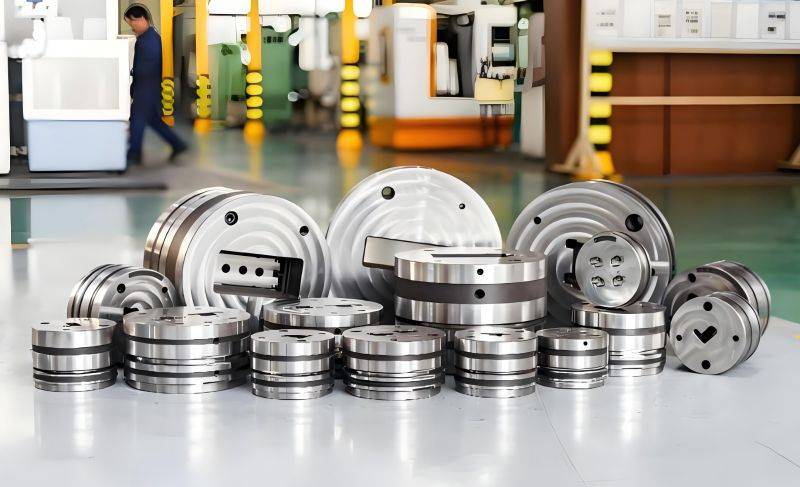
Key Factors in Mold Design for Optimized Product Performance
Several key factors influence how effective an aluminum extrusion mold will be in optimizing product performance. Such as the material used for the mold, the cooling systems in place, the complexity of the geometry, and the maintenance practices followed.
Material Choice for the Mold
The material from which the mold is made directly affects its durability and longevity. Harder materials, such as high-grade tool steel, resist wear and tear, allowing for longer production runs without compromising product quality. Softer materials may degrade quickly, leading to frequent repairs and inconsistent product performance. Choosing the right mold material ensures prolonged use without sacrificing precision.
Mold Cooling Systems
Proper cooling is essential for maintaining the dimensional stability of the extruded aluminum. A well-designed cooling system prevents overheating, which can lead to defects like warping or cracking. This, in turn, preserves the product’s structural integrity and ensures high performance, especially in industries where heat resistance is crucial.
Geometry and Profile Complexity
The more complex a product’s geometry, the more challenging it is to design a mold that will produce it accurately. Complex profiles require intricate mold designs that balance the need for detail with the structural limitations of the aluminum. Mold design must consider the product’s intended use to ensure that complex geometries do not compromise the product’s strength or durability.
Mold Wear and Maintenance
Mold wear is inevitable over time, but regular maintenance can extend the life of the mold and ensure consistent product performance. Worn molds can introduce variations in product dimensions, leading to performance degradation. Implementing a maintenance schedule and monitoring mold wear are essential for maintaining product quality and avoiding costly downtime.
Paying attention to these key factors during the design and maintenance of aluminum extrusion molds ensures that product performance is optimized. The right choices in mold material, cooling systems, and geometry can make the difference between a high-performing product and one that fails to meet expectations.
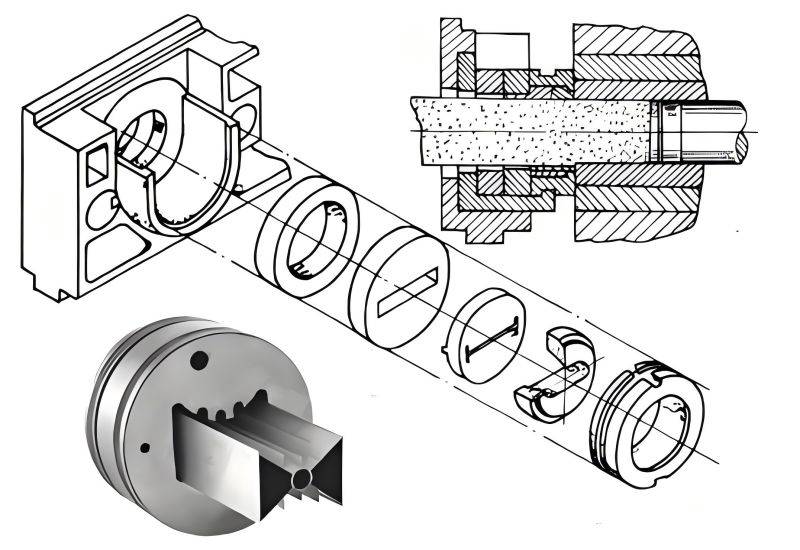
In summary, the relationship between aluminum extrusion molds and product performance is undeniable. Molds serve as the foundation for creating high-precision, consistent, and durable aluminum products. A well-designed mold ensures that each product meets the necessary specifications, from tight tolerances to surface finish and structural integrity. Moreover, factors like mold material, cooling systems, and proper maintenance are critical in ensuring that the mold performs optimally throughout its lifespan.
Investing in quality mold design and considering all the elements that impact performance not only results in superior products but also improves manufacturing efficiency and reduces long-term costs. For any manufacturer involved in aluminum extrusion, understanding and prioritizing mold design is essential for delivering high-performing products that meet the needs of modern industry. If you are looking for a aluminum extrusion mold provider, please feel free to contact CHAL.