Aluminum honeycomb panels have become the top popular choice of modern construction, aerospace, and design industries due to their unique combination of strength, lightweight properties, and versatility. These panels feature a honeycomb-shaped core sandwiched between two thin aluminum sheets, creating a structure that offers exceptional mechanical performance. From architectural facades to aircraft interiors, their applications are as diverse as their specifications. This article delves into the various aspects of aluminum honeycomb panels, addressing their types, dimensions, weight, strength-to-weight ratio, fire rating, and soundproofing capabilities.
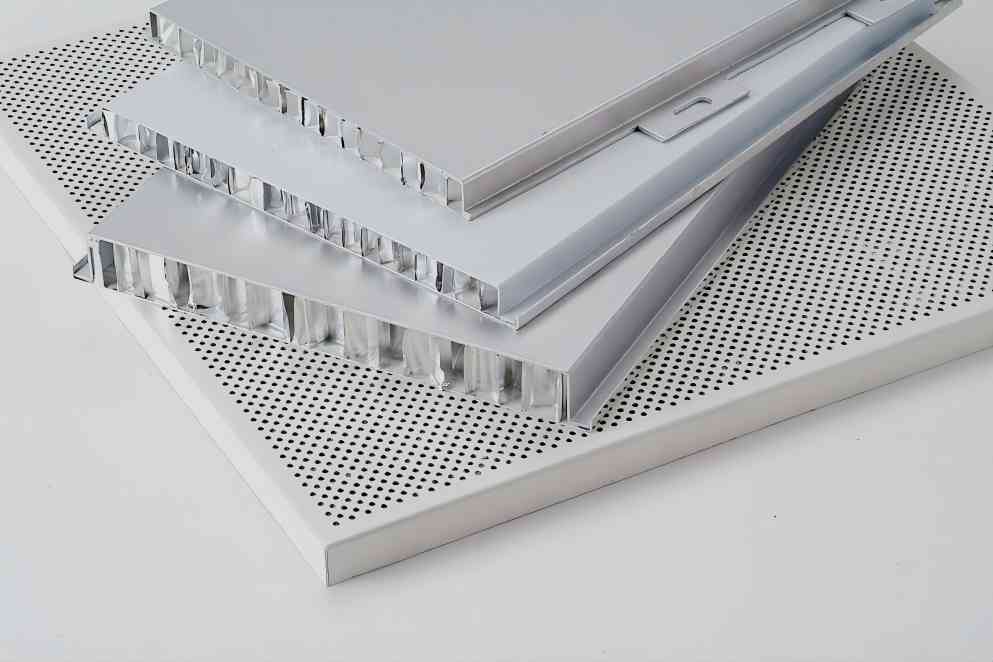
What are the Different Types of Aluminum Honeycomb Panels
Aluminum honeycomb panels are composite structures comprising two primary components: the core and the surface sheets. The combination of these elements results in a lightweight yet incredibly strong material.
Core Materials
The core of an aluminum honeycomb panel is the most crucial component, providing structural integrity and lightweight properties.
- Aluminum Honeycomb Core: This is the most common type of core material. It consists of thin aluminum foil folded into a hexagonal pattern, creating a cellular structure. This structure offers exceptional strength-to-weight ratio and excellent resistance to compressive forces.
- Non-Metallic Cores: In specific applications, non-metallic cores, such as Nomex or phenolic, may be used. These materials often offer additional properties like fire resistance, chemical resistance, or thermal insulation, making them suitable for specialized environments.
Surface Sheet Materials
Surface sheets are the outer layers of the honeycomb panel that provide protection, aesthetic appeal, and additional structural support.
- Aluminum: Aluminum sheets are the most common type due to their excellent balance of strength, weight, and cost-effectiveness. They can be customized in various thicknesses and finishes to meet specific requirements, such as anodizing for corrosion resistance or painting for aesthetic purposes.
- Carbon Fiber: Carbon fiber face sheets offer a superior strength-to-weight ratio compared to aluminum. They are often used in high-performance applications where weight reduction is critical, such as aerospace and racing. Carbon fiber panels are known for their excellent stiffness and resistance to fatigue.
- Other Composite Materials: Other composite materials, such as fiberglass or Kevlar, can also be used as face sheets, depending on the specific needs of the application. These materials may offer additional properties like impact resistance, chemical resistance, or thermal insulation.
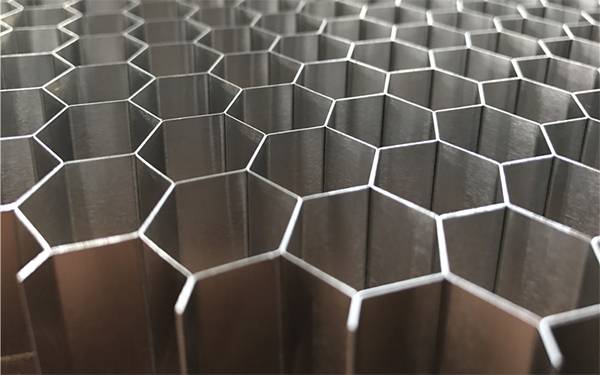
What are the Typical Dimensions of Aluminum Honeycomb Panels?
The dimensions and weight of aluminum honeycomb panels can vary widely depending on the specific application and the desired properties. However, some general trends can be observed:
- Thickness: Honeycomb core thickness typically ranges from 1/8 inch to 2 inches. Thicker cores provide greater stiffness and strength, while thinner cores offer lighter weight.
- Surface Sheet Thickness: Surface sheet thickness can range from 0.010 inches to 0.060 inches, depending on the required strength and durability.
- Weight: The weight of aluminum honeycomb panels is primarily determined by the core thickness and face sheet material. Thicker cores and heavier face sheets result in heavier panels.
What is the Strength-to-Weight Ratio of Aluminum Honeycomb Panels?
One of the most significant advantages of aluminum honeycomb panels is their exceptional strength-to-weight ratio. This means that they can withstand high loads while remaining lightweight, making them ideal for applications where weight is a critical factor.
Several factors contribute to the high strength-to-weight ratio of aluminum honeycomb panels:
- Honeycomb Core Structure: The honeycomb core structure efficiently distributes loads across the panel, maximizing its strength and stiffness.
- Material Properties: The high strength-to-weight ratio of aluminum and carbon fiber face sheets further enhances the overall performance of the panel.
- Manufacturing Process: Precise manufacturing techniques ensure that the honeycomb core and face sheets are bonded together securely, optimizing the panel’s structural integrity.
Compared to traditional materials like steel or wood, aluminum honeycomb panels offer significantly higher strength-to-weight ratios. This makes them suitable for a wide range of applications, including aerospace, automotive, and construction.
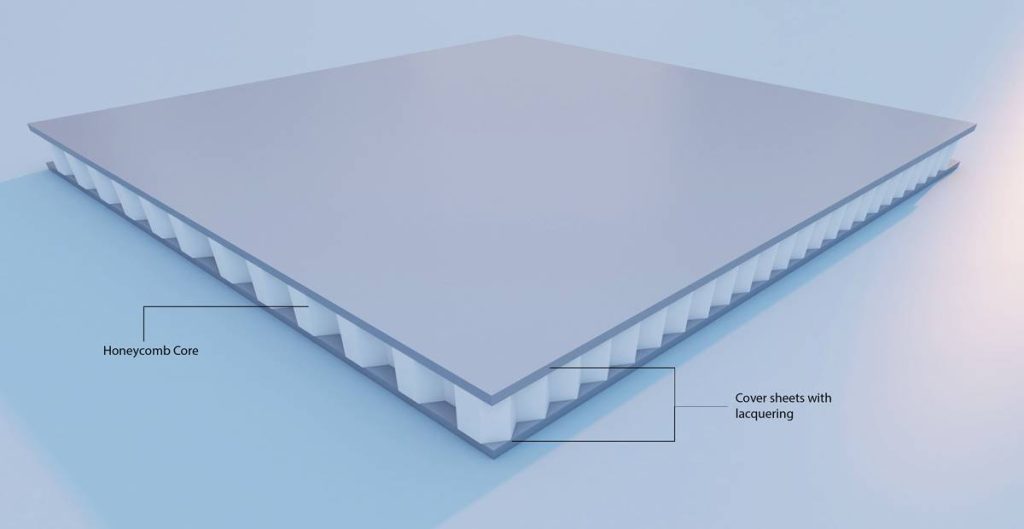
What is the Fire Rating of Aluminum Honeycomb Panels?
Aluminum honeycomb panels exhibit excellent fire resistance properties, making them suitable for use in various fire-sensitive environments. The fire performance of these panels is influenced by several factors:
- Core Material: Aluminum honeycomb cores are inherently fire-resistant, as aluminum does not combust.
- Surface Sheet Material: The fire resistance of the surface sheet material also plays a role. Aluminum sheets are generally fire-resistant, while composite face sheets may require additional fire-retardant treatments.
- Core Density: A denser honeycomb core can provide better fire resistance, as it limits the spread of flames within the panel.
The fire rating of aluminum honeycomb panels is typically determined by industry standards such as ASTM E84 and UL 723. These standards evaluate the flammability and smoke generation of materials when exposed to fire.
What is the Soundproofing Rating of Aluminum Honeycomb Panels?
Aluminum honeycomb panels can also be effective soundproofing materials, depending on the specific design and application. The soundproofing properties of these panels are influenced by several factors:
- Core Thickness: A thicker honeycomb core can provide better sound absorption and insulation.
- Surface Sheet Material: The mass and stiffness of the surface sheet material can also affect sound transmission.
- Panel Configuration: The way the panels are installed and sealed can impact their overall soundproofing performance.
Aluminum honeycomb panels are often used in applications where noise reduction is important, such as aircraft cabins, automotive interiors, and building enclosures. By carefully selecting the core thickness, face sheet material, and installation method, it is possible to achieve high levels of soundproofing performance.
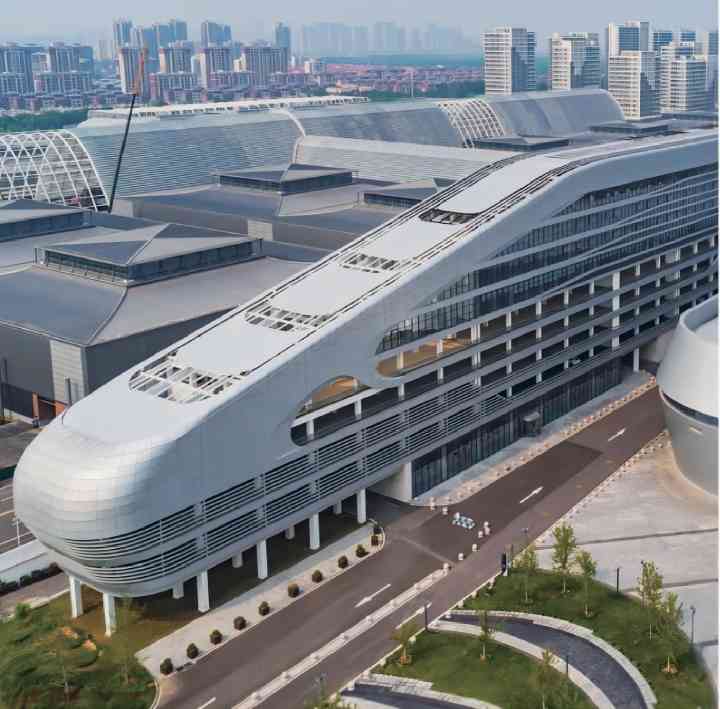
Wrap Up
Aluminum honeycomb panels offer a unique combination of strength, weight, fire resistance, and soundproofing properties, making them a versatile material with a wide range of applications. By understanding the different types, dimensions, and performance characteristics of these panels, engineers and designers can select the optimal solution for their specific needs. As technology continues to advance, we can expect to see even more innovative applications of aluminum honeycomb panels in the future.